Induktionsthermographie für die Komponentenprüfung - Die neue Lösung zur automatisierten Prüfung komplexer Oberflächen
Risse in metallenen Bauteilen können mit einer Vielzahl von Prüfmethoden ermittelt werden, darunter Wirbelstromprüfung, Eindringprüfung (PT) und Magnetpulverprüfung (MPT). Komponenten mit komplexer Geometrie stellen jedoch eine besondere Herausforderung für die Qualitätskontrolle dar. Das Abtasten der Oberfläche eines Bauteils mit einer Wirbelstromsonde ist unter Umständen ineffizient, sodass die PT- und MPT-Prüfungen von geschultem Personal durchgeführt und ausgewertet werden müssen. Eine Automatisierung ist dabei oft unmöglich.
Die Induktionsthermographie stellt nun eine neue Lösung zur Erkennung von Rissen in der Oberfläche von metallischen Komponenten dar. Das Verfahren arbeitet berührungslos und zerstörungsfrei. Außerdem liefert es kontrastreiche Bilder der Fehlstellen und bietet eine hohe Reproduzierbarkeit. Durch kurze Prüfzyklen von unter einer Sekunde je Prüfbereich kann eine automatisierte Prüfung, integriert in einer Produktionslinie, stattfinden.
Zudem ergänzt die Induktionsthermographie ideal die Wirbelstromprüfung. Da beide Methoden induzierte Wirbelströme verwenden, um ein Fehlersignal zu erzeugen, entsprechen die erforderlichen Materialeigenschaften der einen Methode häufig auch denen der anderen. Auch die zu untersuchenden Fehler sind meist die gleichen.
Die Wirbelstrom-Rissprüfung ist einfach, stabil und hocheffizient bei linearen und zylindrischen Oberflächen, bei denen die Sonde mit einer einfachen Bewegung entlang des Prüfbereichs verfahren werden kann. Jede aufwendige Bewegung, die zum Abtasten der Oberfläche erforderlich ist, erhöht die Komplexität, wodurch die Wirbelstromprüfung ihren Vorteil verliert. Dann werden Roboterprogramme oder eine manuelle Bedienung benötigt. In solchen Bereichen kann die Induktionsthermographie eingesetzt werden, um eine vollständige Prüfung des Teils zu ermöglichen.
Physikalische Grundlagen und Erfassungsmethode
Unter Thermographie versteht man im Allgemeinen die bildliche Darstellung von Wärmestrahlung. Im Gegensatz zur Lichtbildfotografie benötigt sie keine Lichtquelle, die eine Szene beleuchtet. Vielmehr geht von allen Objekten Wärmestrahlung aus, die durch die Bewegung der atomaren und subatomaren Teilchen in der gesamten Materie entsteht. Die Intensität und das Spektrum hängen dabei von der Temperatur der Materie ab, wie sie von Max Planck in seinem Gesetz von 1900 beschrieben wurde. Bei hohen Temperaturen ist die Wärmestrahlung sichtbar und zeigt sich als bekannte Lichtquellen wie das Glühen von heißem Metall, Öfen, Glühbirnen oder insbesondere das Strahlen der Sonne. Bei niedrigeren Temperaturen verschiebt sich die Wärmestrahlung in das Infrarotspektrum. Sie ist für das menschliche Auge nicht mehr sichtbar, kann aber mit speziellen Infrarotkameras aufgezeichnet werden.
Die Induktionsthermografie stellt eine Form der aktiven Thermografie dar, bei der das Objekt im Verlauf der Untersuchung absichtlich erwärmt wird. Das bedeutet, dass ein Impuls auf das Prüfobjekt einwirkt und die thermische Reaktion der Oberfläche, wie Erwärmung, Abkühlung und Wärmediffusion, in Form von Wärmebildern oder Videos aufgezeichnet wird. Diese Effekte geben einen wichtigen Einblick in die Materialeigenschaften und die Beschaffenheit des Prüfobjekts.
Das Induktionsverfahren weist einige Ähnlichkeiten mit der Wirbelstromprüfung auf, erfordert jedoch eine eigene Ausstattung. Wie bei der Wirbelstromprüfung legt eine Induktionsspule ein oszillierendes Magnetfeld an, das im Prüfteil Wirbelströme induziert. Es gibt jedoch keine Empfängerspule, die die sekundären Magnetfelder erfasst. Vielmehr verursacht der spezifische Widerstand des Materials eine Joulesche Erwärmung, die mit der Infrarotkamera gemessen wird. Dabei können Fehlstellen in der Oberfläche, wie etwa Risse, einen lokalen Erwärmungseffekt verursachen. Ein nennenswerter Effekt kann für eine Kamera bereits bei einer Erwärmung des Objekts um nur wenige Grad Celsius sichtbar werden. Das bedeutet, dass die Materialeigenschaften des Werkstücks in der Regel nicht beeinflusst werden. Um eine signifikante Reaktion zu bewirken, müssen jedoch schnelle Prozesse stattfinden. Das Induktionssystem muss kurze und intensive Magnetfeldimpulse abgeben und diese mit der Infrarotkamera synchronisieren, die mit einer hohen Bildrate läuft. Dadurch lassen sich lokale Wärmequellen und Wärmesenken erkennen, die gute Indikatoren für Fehlstellen an einem Prüfteil sind.
Bild 1 - (links) Ein typischer Induktionsaufbau mit Infrarotkamera, Induktor und Prüfteil. Generatoren und Zeitgeber sind nicht abgebildet. (Mitte) Passive Thermografie eines Lenkritzels Risse sind nicht sichtbar. (rechts) Aktive Induktionsthermografie zeigt Wärmequellen während des Induktionsimpulses und ein deutliches Defektmuster.
Bild 2 - (von links nach rechts) Schematische Risserkennung: Induzierte Ströme umfahren einen Riss. Bereiche mit hoher Stromdichte werden zu Hotspots. Die Hotspots sind als Muster von Wärmequellen in einer Induktionsthermografie-Aufnahme sichtbar. Im Vergleich dazu zeigt eine lichtmikroskopische Aufnahme keinen Hinweis auf einen Riss.
Der Schwerpunkt der Induktionsthermographie liegt auf der Rissprüfung. Diese Art von Fehler führt häufig zu charakteristischen Mustern bei der thermischen Erwärmung. Wenn ein Material durch Induktion erwärmt wird, bilden sich in der Nähe der Oberfläche des Objekts Wirbelströme, die das Objekt gleichmäßig erhitzen. Wenn ein Riss im Material vorhanden ist, wird der Strom gezwungen, diesen zu umgehen, indem er entweder unter ihm hindurch oder an den Seiten vorbei fließt oder durch Kontaktpunkte an den Risswänden geleitet wird. Während die Erwärmung in der Nähe des Risses im Allgemeinen geringer ist, treten an diesen besonderen Stellen außergewöhnlich hohe Stromdichten auf und bilden sogenannte Hotspots. Diese sind auf der Oberfläche des Objekts für die Kamera sichtbar. Wärme, die in geringer Tiefe unter der Oberfläche erzeugt wird, kann auch an die Oberfläche diffundieren und sich als unscharfe Hotspots auf einem Wärmebild zeigen. Auf einer Wärmebildaufnahme erscheint ein Riss daher oft als kühlerer Bereich mit deutlichen Hotspots an den Enden. Manchmal entsteht sogar ein perlenartiges Muster von Hotspots entlang des Rissverlaufs.
Bild 3 - Beispiele für geeignete Teile und Prüfbereiche für die Induktionsthermografie (türkis). Einige Teile mit zylindrischen Oberflächen können für die Hybridprüfung zusammen mit der Wirbelstromprüfung (orange) geeignet sein.
Automatisierte Lösungen mit DEFECTOVISION CT
Die Vorteile der Induktionsthermographie im Vergleich zu anderen visuellen Prüfverfahren wie der Eindringprüfung oder der Magnetpulverprüfung sind die hohen Signalstärken und die hohe Reproduzierbarkeit der Fehlerbilder. Auf diese Weise können Bildverarbeitungsalgorithmen trainiert werden, um Fehlermuster genau zu erkennen und sie von natürlich vorkommenden Mustern auf Gutteilen zu unterscheiden.
DEFECTOVSISION CT ist die neue automatisierte Induktionsthermografie von FOERSTER für die Komponentenprüfung. Die Anwendung der Grundlagen der Wärmebilderfassung und Bildverarbeitung ermöglicht einen zuverlässigen Sortierprozess.
Zusammen mit der Wirbelstromprüfung ermöglicht DEFECTOVISION CT die Prüfung komplizierter Teile in automatisierten Hybridprüfzellen. Es können aller bzw. die meisten kritischen Prüfbereiche untersucht werden. Dies ohne den Einsatz teurer Magnetpulver- und Eindringprüfungen.
Bild 4 - DEFECTOVISION CT
Share this
Vielleicht gefällt Ihnen auch
Verwandte Artikel
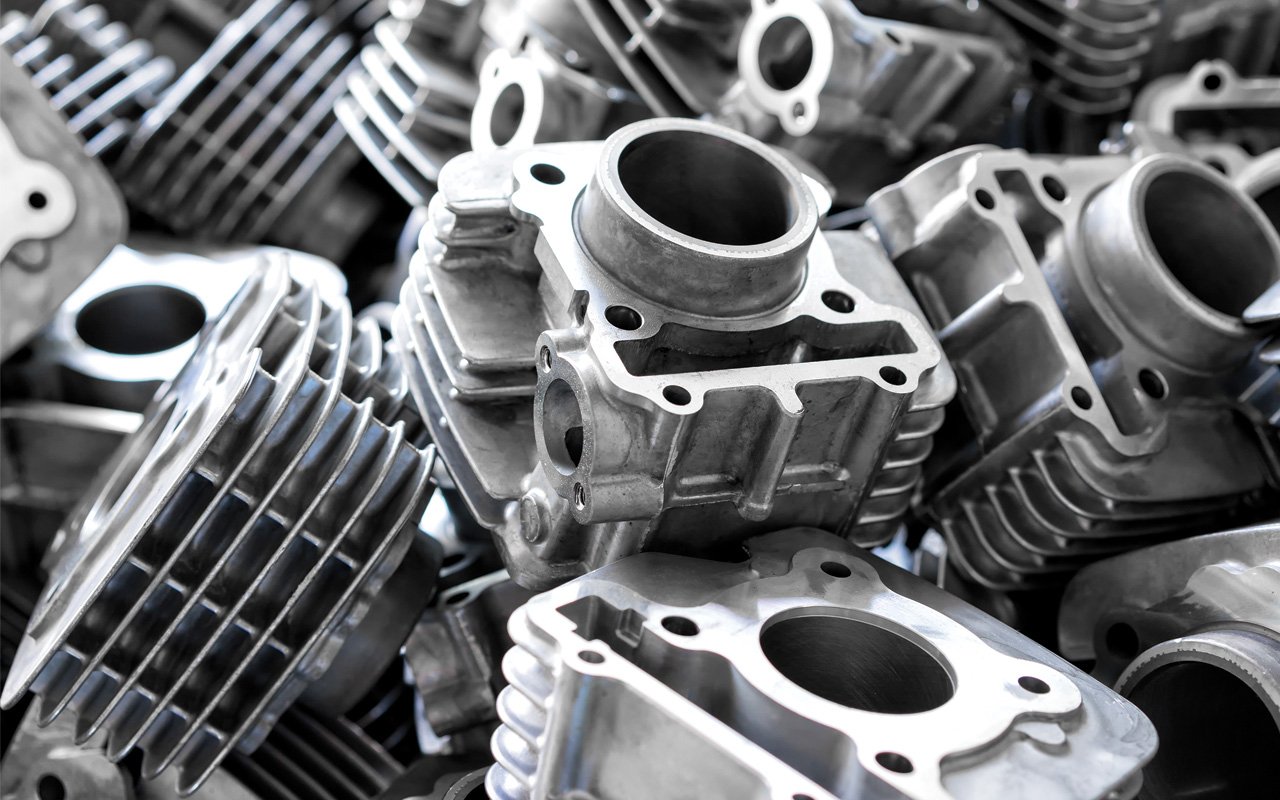
Oberflächenhärte bei Komponenten
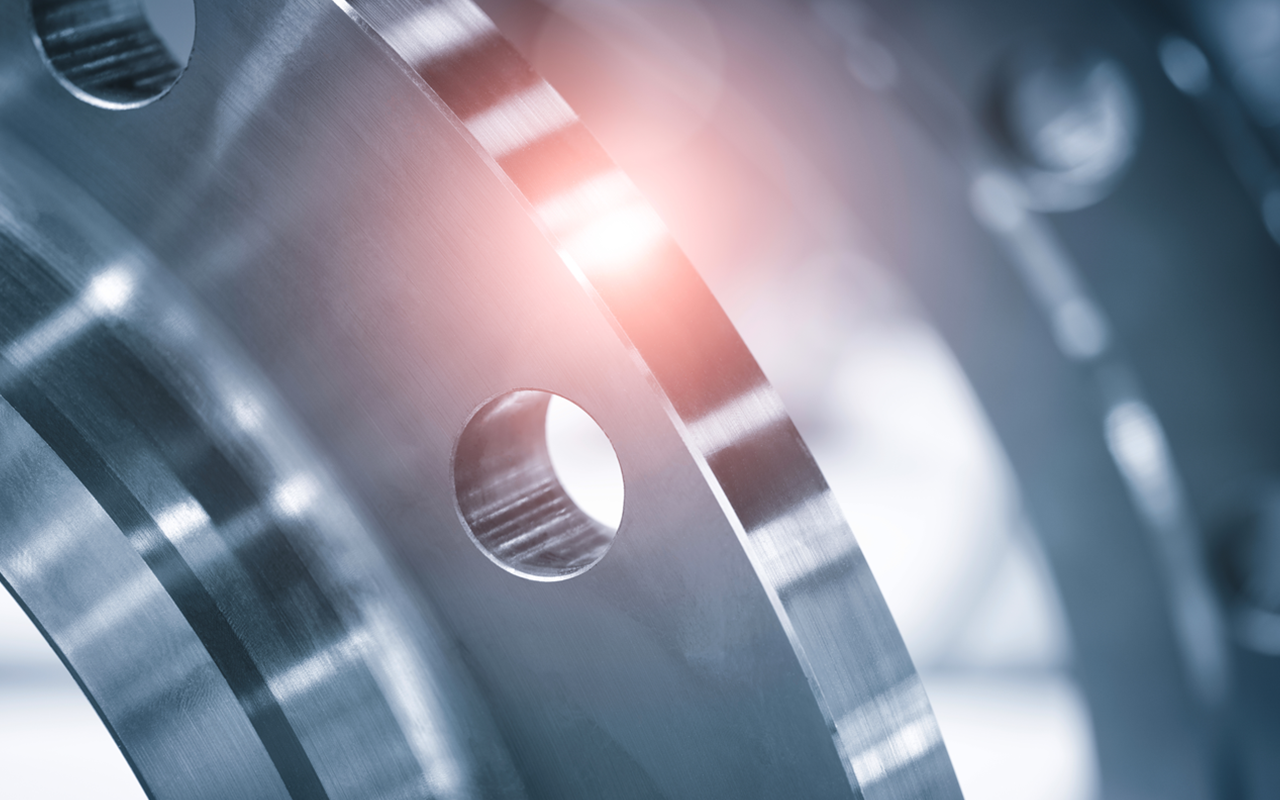
Was ist eine Wirbelstromprüfung?
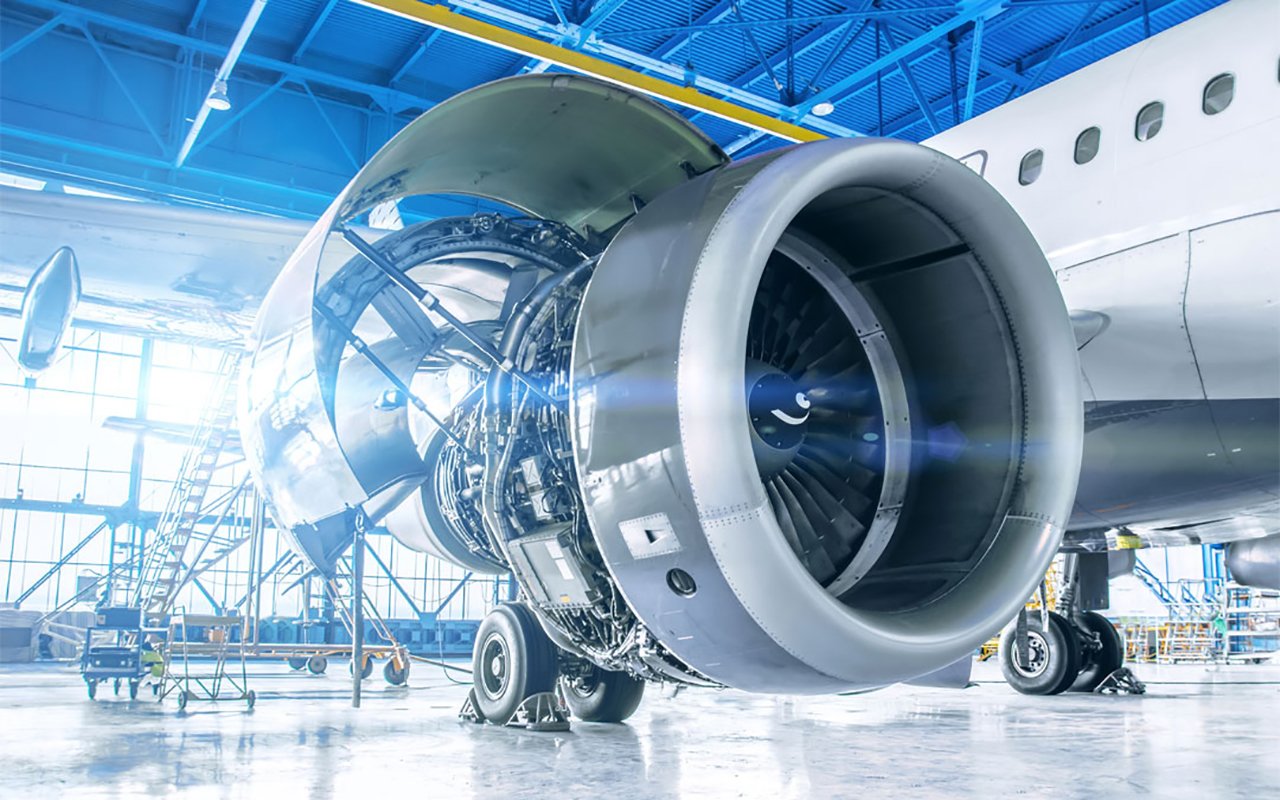