Rissprüfung: Wie funktioniert ein Wirbelstromprüfgerät?
Die Wirbelstromprüfung ist ein zerstörungsfreies Verfahren zur Überprüfung leitender, d.h. metallischer Oberflächen auf Fehler wie Risse oder Einschlüsse.
Zur Rissprüfung wird das Prüfteil mechanisch in Rotation versetzt und von einer feststehenden Sonde mit zwei eingegossenen Spulen abgetastet. Alternativ tastet eine rotierende Sonde das ruhende Prüfteil ab. Während die eine Spule als Sendewicklung dient, wird die andere als Empfängerspule eingesetzt. Die Sendewicklung wird mit einem definierten Wechselstrom beaufschlagt. Der durch die Spule fließende Wechselstrom erzeugt ein Magnetfeld, welches wiederum einen Wirbelstrom in dem leitenden Prüfteil induziert. Analog dieser Technik kann auch umgekehrt die vom Wirbelstrom erzeugte Spannung mit einer Empfängerspule gemessen werden.
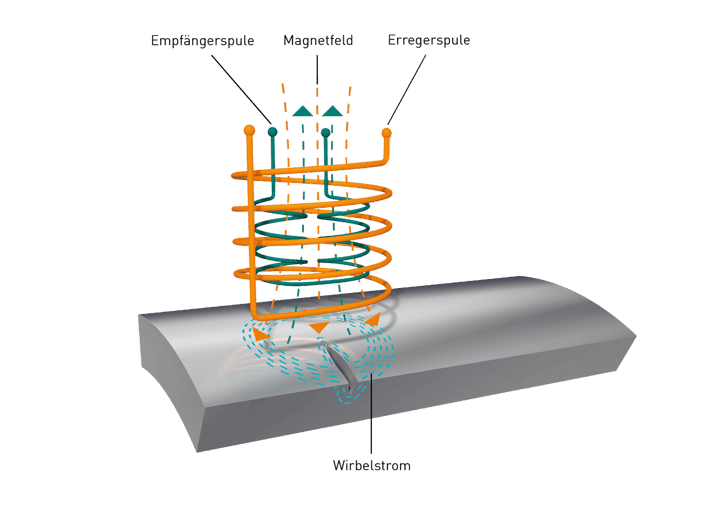
Diese hochfrequenten elektromagnetischen Wechselwirkungen werden für die Rissprüfung genutzt. Ein Wirbelstromprüfgerät vergleicht das gesendete mit dem empfangenen Signal, um somit Rückschlüsse auf die Oberfläche des Prüfobjektes zu ziehen. Befindet sich beispielsweise ein Riss auf der Oberfläche des Prüfteils, so breiten sich die Wirbelströme anders aus. Dies führt zu einer Veränderung der Phasenlage und Amplitude. Genau diese Veränderung stellt das Prüfgerät dann graphisch als sogenanntes Wirbelstromsignal dar.
Hier erfahren Sie mehr über die Vorteile der Wirbelstromgeräte zur Fehlererkennung.
Mit diesem Verfahren können vor allem oberflächennahe Risse oder Poren detektiert werden. Die Eindringtiefe des Wirbelstroms ist dabei abhängig von der
- Elektrischen Leitfähigkeit
- Magnetischen Permeabilität
- Prüffrequenz
Die elektrische Leitfähigkeit, sowie die magnetische Permeabilität werden vom Prüfobjekt vorgegeben. Die Prüffrequenz jedoch kann aktiv beeinflusst werden.
Je tiefer die Prüffrequenz, desto höher ist die Eindringtiefe. Daher werden hohe Frequenzen für die Detektion oberflächennaher Fehler und geringe Frequenzen für tieferliegende Fehlstellen eingesetzt. Mit der Verringerung der Frequenz nimmt die Sensitivität ab, d.h. die Fehlerauflösung wird bei tieferliegenden Fehlern deutlich geringer. Daher gibt es für jede Prüfung eine optimale Prüffrequenz, um die Balance zwischen Eindringtiefe und Sensitivität zu finden.
Wichtiger Einflussfaktor zur Rissprüfung: die Oberflächengüte
Auch andere Eigenschaften spielen eine wichtige Rolle. Allen voran die Oberflächengüte des Prüfobjektes. Die Wirbelstromprüfung ist eine berührungslose Art der Prüfung, d.h. die Sonde muss das zu prüfende Bauteil nicht berühren, sondern lediglich in einem geringen Abstand reproduzierbar positioniert werden. Je feiner die Oberfläche (z.B. poliert), desto näher kann die Sonde herangeführt werden, um eine höhere Fehlerauflösung zu erzielen. Bei rauen Oberflächen kann das Sondenelement beschädigt werden, wenn der Sensor zu nah an die Oberfläche des Prüfteils kommt und durch Unebenheiten touchiert wird.
Grundsätzlich ist zu beachten, dass jede Oberfläche ein sogenanntes Grundrauschen erzeugt. Für die sichere und reproduzierbare Detektion von Fehlstellen sollte das generierte Fehlersignal 3x höher sein als das Grundrauschen. Dieses Verhältnis nennt man Signal-Rausch-Verhältnis oder auf Englisch Signal-to-Noise Ratio (kurz: SNR). Aus oben genannten Gründen ist es bei feinen Oberflächen einfacher ein SNR von 3:1 oder höher zu erzielen.
Abstandskompensation und weitere wichtige Parameter für eine optimale Rissprüfung
Doch nicht nur die Oberflächenbeschaffenheit beeinflusst den Abstand der Sonde zum Bauteil, auch die symmetrische Rotation ist ein entscheidender Faktor. Bei einer unsauberen Rotation kann es passieren, dass der Abstand über eine 360° Rotation nicht immer konstant ist, sondern variiert. Das wird durch die sogenannte Abstandskompensation ausgeglichen. Hier misst ein zusätzlicher Abstandskanal permanent die Signalstärke und kann somit Rückschlüsse auf den Abstand der Sonde zum Prüfteil schließen. Diese Information wird durch einen Algorithmus in das Risssignal eingearbeitet, um für gleiche Risse identische Amplituden zu erzeugen, unabhängig vom Abstand der Sonde zum Prüfobjekt.
Bei modernen Wirbelstromprüfgeräten wie z.B. dem STATOGRAPH CM / CM+ von FOERSTER kann man jedoch nicht nur die Frequenz und die Abstandskompensation einstellen, sondern zusätzlich noch die Parameter:
- Sensitivität
- Bandpass
- Phasenlage
Mit der Sensitivität (Prüfempfindlichkeit) kann die Amplitude des Fehlersignals manuell erhöht werden, um ein Fehlersignal sicher über den Schwellenwert zu bringen. Der Schwellenwert definiert, ab wann ein aufgenommenes Wirbelstromsignal zu hoch ist und die Komponente als n.i.O. deklariert wird. Die Sensitivität wird anhand von künstlichen oder natürlichen Referenzfehlern vor der Prüfung eingestellt und überprüft. Mittels geeigneter Schnittstellen, z.B. PROFINET, kann dieser Wert an eine SPS übergeben werden, welche dann wiederum die Bauteile in Gut- und Schlechtteile sortiert. Durch andere Schnittstellen, wie beispielsweise digitale Ein- und Ausgänge, wird dem Prüfgerät zudem mitgeteilt, wann eine Prüfung beginnt (externer Trigger) oder wie lange geprüft werden muss.
Mit dem Bandpass können störende Nebenfrequenzen herausgefiltert werden, so dass es nicht zu Falschanzeigen beim Fehlersignal und damit Pseudoausschuss kommt.
Ähnlich funktioniert die Phasenlage, hier können Signale in ihrer Phasenlage gedreht werden, um lediglich das relevante Fehlersignal mittels Schwellenwert auszuwerten und andere irrelevante Signale zu vernachlässigen.
Wichtig ist dabei immer, dass ein Wirbelstromprüfgerät gegen Referenzfehler prüft. Es findet also ein Abgleich statt. Je nachdem ob der zuvor definierte Schwellenwert bei diesem Abgleich überschritten wird, werden die Prüfteile in i.O. und n.i.O. gruppiert. Bei hochwertigen Geräten wie dem STATOGRAPH CM / CM+ von FOERSTER können verschiedene Schwellenwerte und Auswertemethoden gewählt werden. So kann beispielsweise frühzeitig eine Meldung erstellt werden, wenn die Bauteile eine Tendenz Richtung der n.i.O.-Schwelle entwickeln. Mit Hilfe dieser Informationen können frühzeitig Rückschlüsse auf den gesamten Fertigungsprozess gezogen und eingegriffen werden – ganz im Sinne der Industrie 4.0.
Damit die Rissprüfung noch einfacher und intuitiver erfolgen kann, hat FOERSTER das Wirbelstromprüfgerät STATOGRAPH umfassend weiterentwickelt.
Kontaktieren Sie unsere Experten und besprechen Sie Ihre Prüfaufgabe. Fordern Sie eine personalisierte Demo an. Wir helfen Ihnen gerne weiter!
Share this
Vielleicht gefällt Ihnen auch
Verwandte Artikel
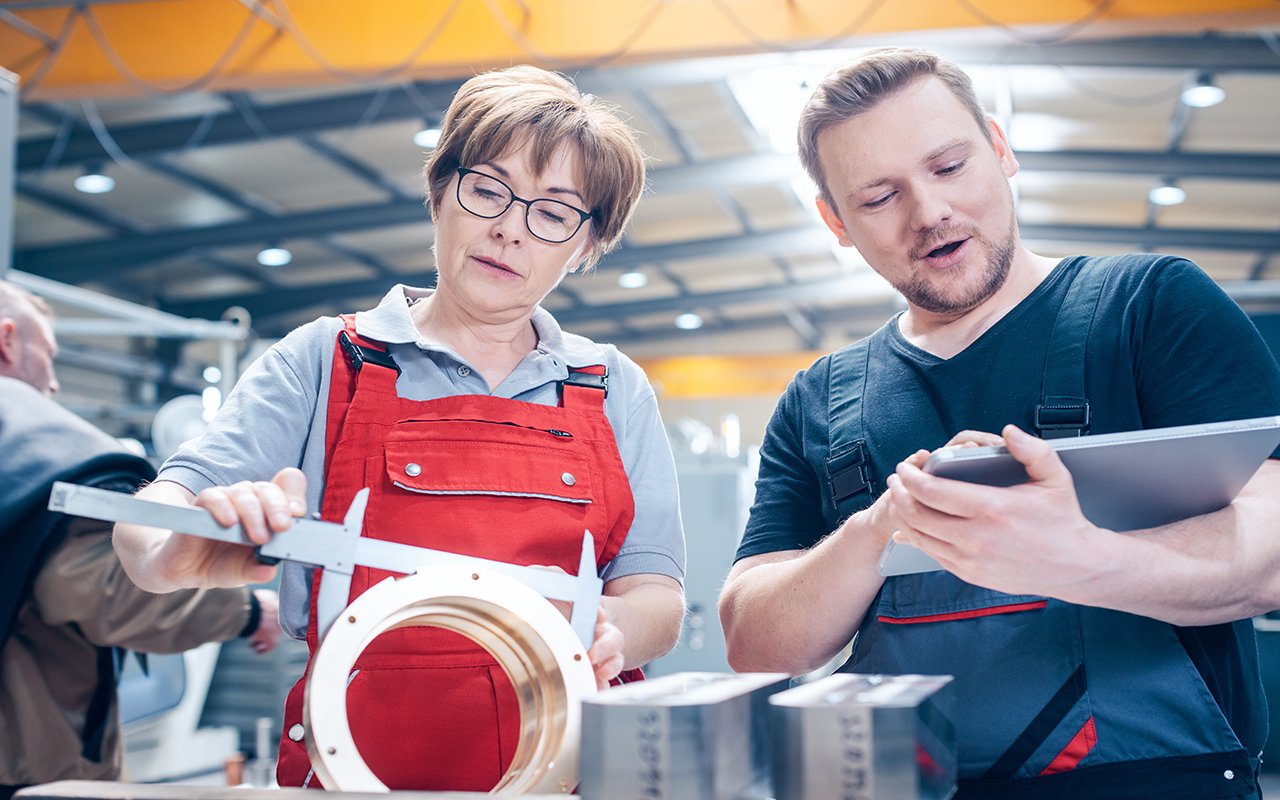
Wirbelstromgeräte: Vorteile, Anwendungen und Funktionen zur Fehlererkennung
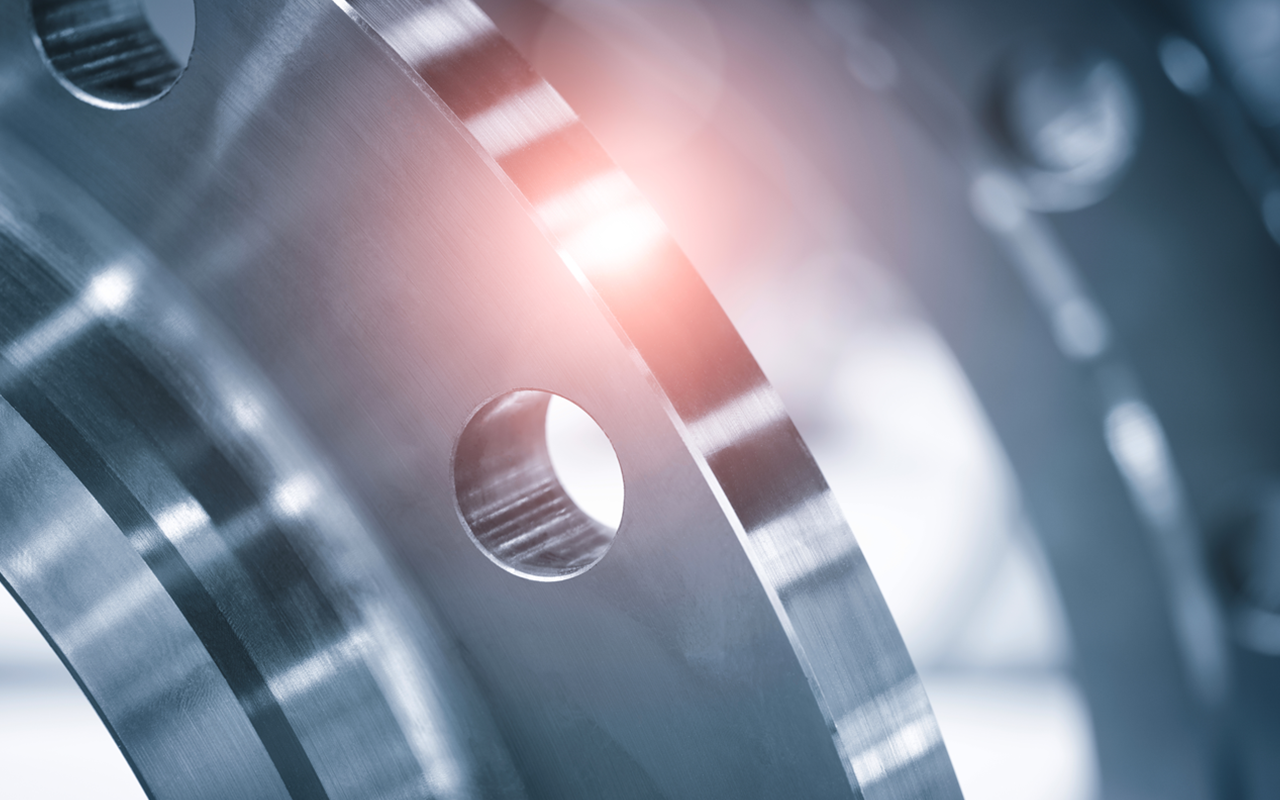
Was ist eine Wirbelstromprüfung?
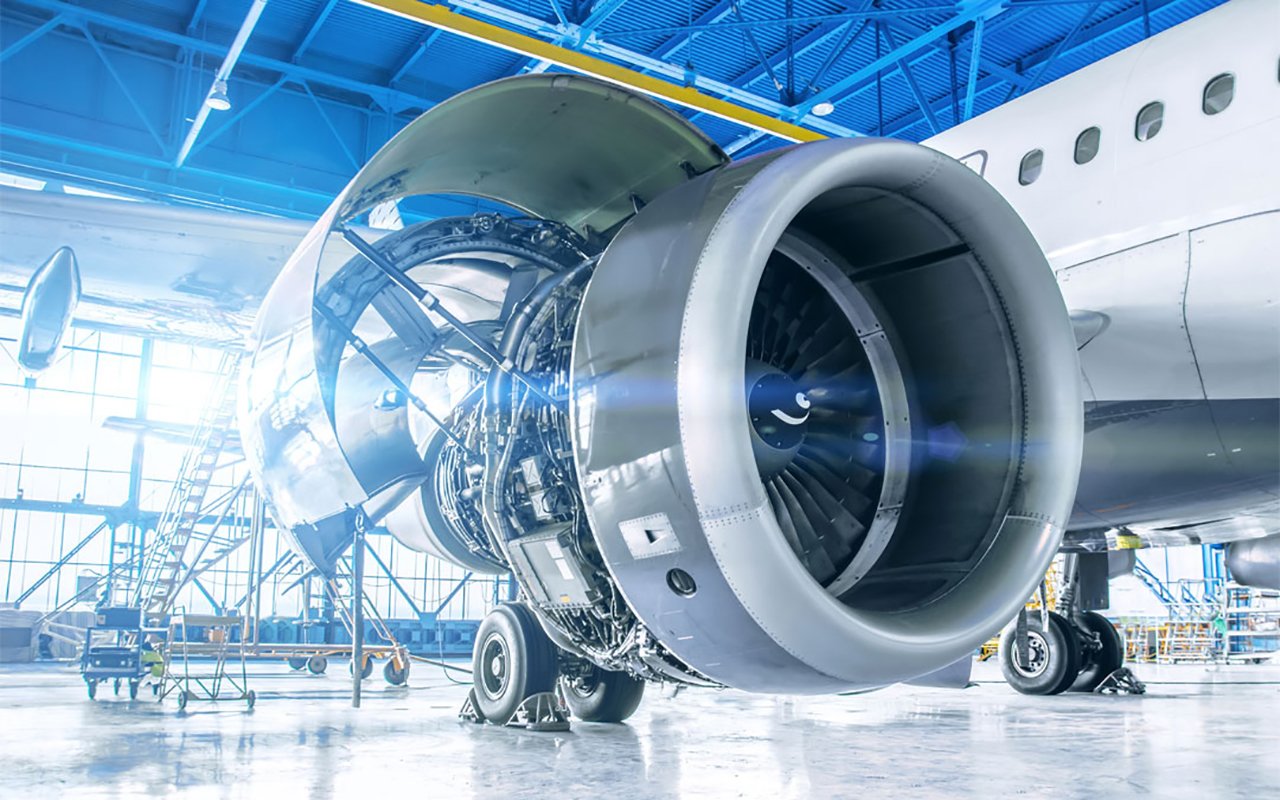