Eddy Current Component Testing: A Crucial Gear Inspection Technique
In the fast-paced world of automotive engineering, where precision and reliability are paramount, quality testing gears emerge as a crucial component ensuring both performance and safety on the roads. From the humble gear mechanisms in manual transmissions to the sophisticated systems driving electric vehicles, the integrity of gears directly impacts vehicle functionality and, more importantly, the safety of drivers, passengers, and pedestrians alike.
Why Quality Testing Matters
- Reliability Under Stress: Gears are subjected to intense mechanical stress during operation. From high-speed acceleration to abrupt stops, these components must endure varying conditions without compromising performance. Quality testing simulates these scenarios, identifying weaknesses before they lead to catastrophic failures on the road.
- Mitigating Failure Risks: A single gear malfunction can have devastating consequences, ranging from accidents to costly repairs. Rigorous quality testing helps identify potential failure points, allowing engineers to address issues proactively, reducing the risk of unexpected breakdowns.
- Optimizing Performance: In addition to safety concerns, well-tested gears contribute to overall vehicle performance. By ensuring precise engagement and smooth operation, quality-tested gears help optimize efficiency, enhance fuel economy, and extend the lifespan of drivetrain components.
- Meeting Regulatory Standards: Automotive manufacturers are bound by stringent safety regulations and industry standards. Quality testing serves as a vital step in compliance, verifying that gears meet or exceed these requirements before vehicles hit the market. This not only safeguards consumers but also protects manufacturers from costly recalls and legal liabilities.
Understanding Eddy Current Testing
Eddy current testing is a non-destructive testing (NDT) technique widely utilized in the aerospace, automotive, and manufacturing industries. It relies on the principle of electromagnetic induction to detect surface and subsurface defects in conductive materials without causing damage to the tested components.
What is Eddy Current, and how does it work?
Eddy currents are circular electrical currents induced in a conductive material when subjected to a changing magnetic field. These currents generate their own magnetic fields, which interact with the primary magnetic field, producing measurable effects.
In ECT, a probe containing a coil is placed near the surface of the gear to be inspected. An alternating current is passed through the coil, creating a changing magnetic field. Any surface defects or variations in material properties alter the eddy currents' flow, causing disturbances in the magnetic field, which are detected by the probe.
The Eddy Current Testing Process for Gears
- Surface Inspection: Eddy current testing excels at detecting surface irregularities such as cracks, pits, and corrosion. By passing an alternating current through a coil probe positioned near the surface of the gear, eddy currents are induced in the material. Any disruptions caused by defects alter the electrical impedance, which is measured and analyzed to identify anomalies.
- Subsurface Detection: Beyond surface defects, eddy current testing can penetrate the material to detect variances hidden beneath the surface. This capability is particularly valuable for assessing the integrity of gear teeth and detecting internal defects such as inclusions and heat treatment irregularities. Advanced signal processing techniques enhance the sensitivity of the method, allowing for precise detection of subsurface anomalies.
- High-Speed Inspection: In automotive manufacturing, efficiency is paramount. Eddy current testing offers rapid inspection capabilities, making it well-suited for high-speed production lines. With automated systems and real-time data analysis, manufacturers can conduct thorough inspections without compromising production throughput.
Advantages of Eddy Current Testing
- Non-Destructive: Unlike traditional destructive testing methods, eddy current testing preserves the integrity of gears, minimizing waste and reducing production costs.
- High Sensitivity: Eddy current testing can detect minute defects, ensuring the reliability and safety of automotive gears even under demanding operating conditions.
- Versatility: The technique is applicable to a wide range of materials, including ferrous and non-ferrous alloys, making it suitable for diverse automotive gear applications.
In the pursuit of automotive excellence, ensuring the quality and safety of gears is paramount. Eddy current testing stands at the forefront of quality assurance methodologies, offering unparalleled sensitivity and efficiency in defect detection. By leveraging this advanced NDT technique, automotive manufacturers can uphold their commitment to delivering vehicles that not only meet but exceed stringent safety and performance standards. As technology continues to evolve, eddy current testing remains a cornerstone of automotive innovation—a testament to the industry's unwavering dedication to driving safety forward, one gear at a time.
Share this
You May Also Like
These Related Stories
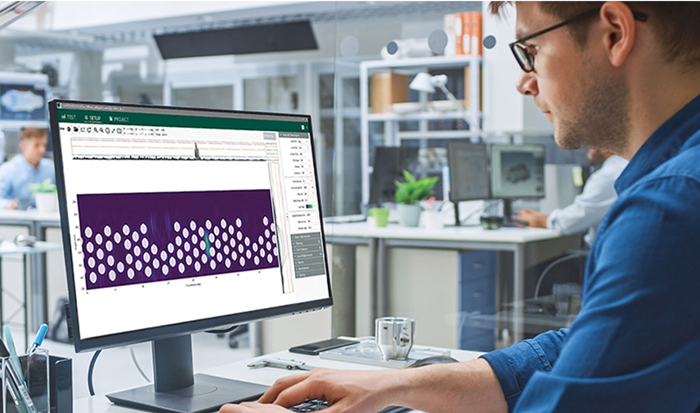
Software for visualization of surface quality
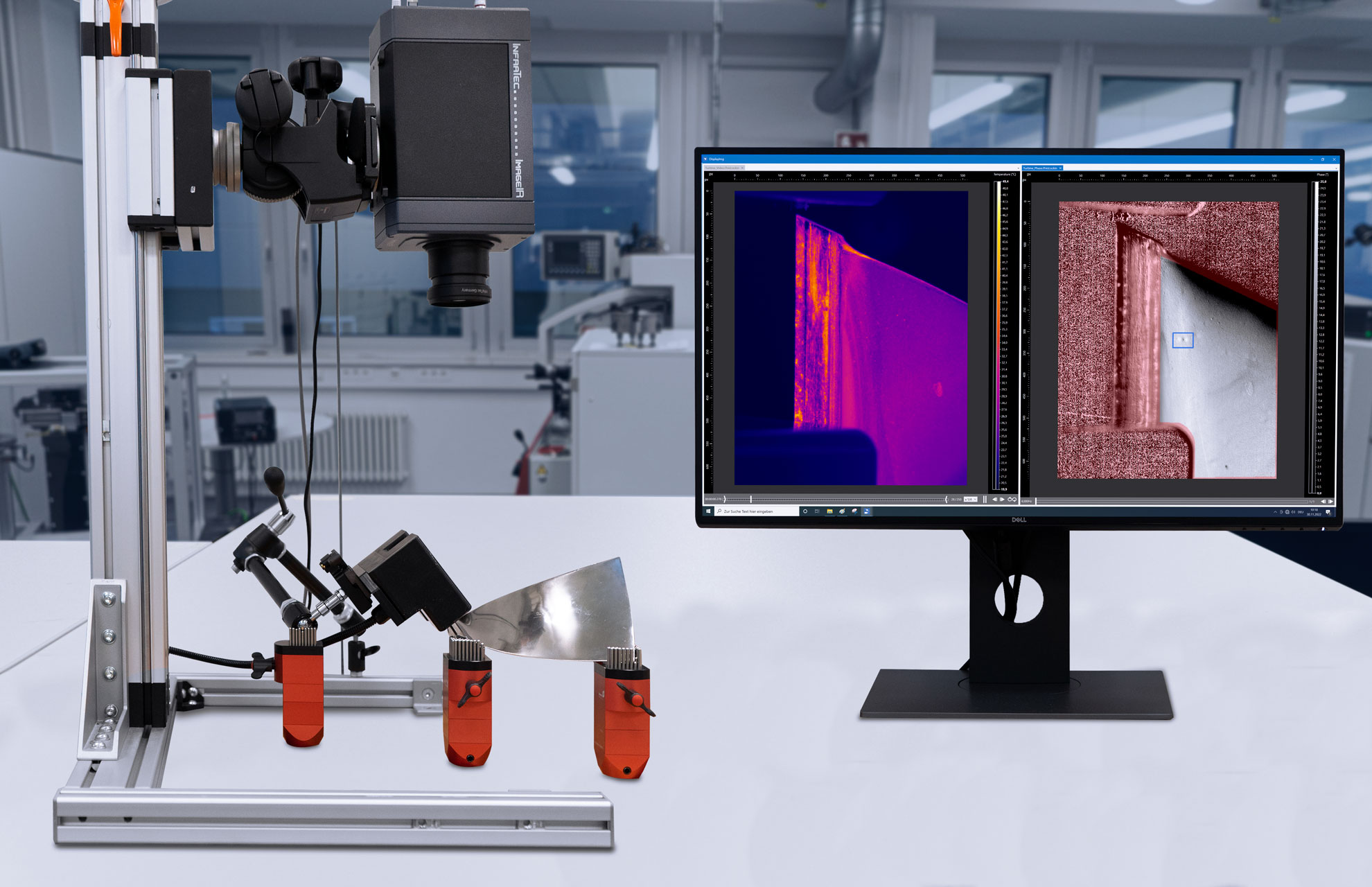
Induction thermography for component testing - A new solution for the automated inspection of complex surfaces
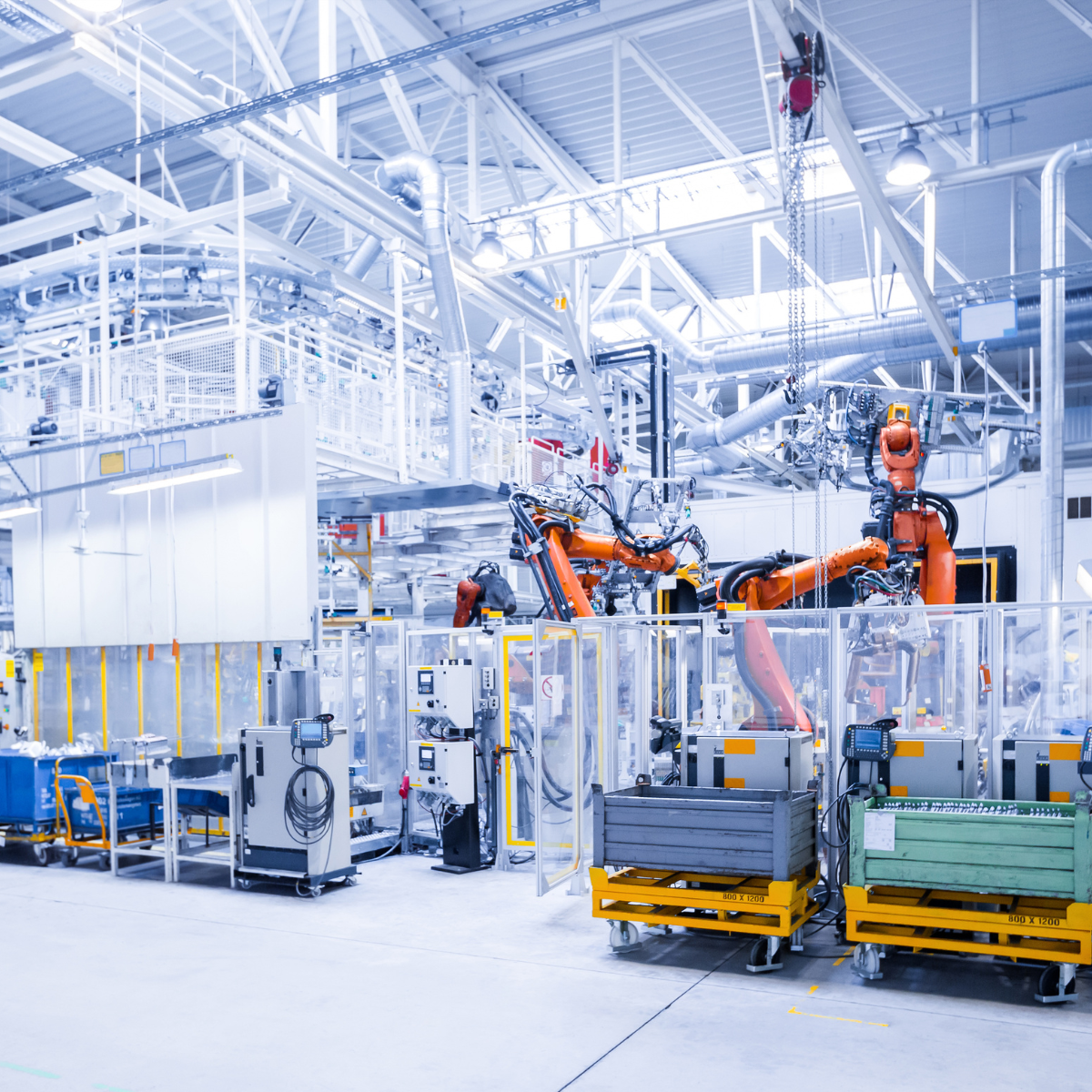