A single automobile is composed of about 20,000 to 30,000 parts. The reliability of all these parts, including the engine, transmission, steering system, suspension and braking systems, and body, must be ensured in order to guarantee the dynamic performance and comfort of the car, and to ensure safe driving. Many of the components are subjected to high loads all the time, so they need to be strong enough to withstand these forces. If even one of the components has a quality or performance problem, the safety of passengers cannot be ensured.
Parts that need to be particularly strong are manufactured by forging. After hot forging or cold forging, the parts undergo a heat treatment process to obtain specified hardness and tensile strength. In case of hot forging of non-tempered steel, prescribed hardness is obtained through the cooling process, and in case of cold forging, through work hardening during processing. However, in heat treatment process, parts may not gain the desired hardness or tensile strength due to defects in the heat treatment equipment or uneven temperatures in the heat treatment furnace. In addition, it is possible that unintentional factors may cause untreated parts to be mixed in. It is impossible to measure the hardness of all mass-produced parts, and destructive testing would result in the loss of the value of the part as a product itself. In addition, various types of parts are manufactured in forging factories, and different grades of steel are used for different types of parts for automobiles. If these defective products were to be incorporated into automobiles, they could cause serious accidents.
Therefore, at the final stage of the production line, a non-destructive, complete inspection is conducted to sort out defective products. This method uses electromagnetic induction to detect hardness, tensile strength, and foreign material contamination by passing the part through an encircling coil.
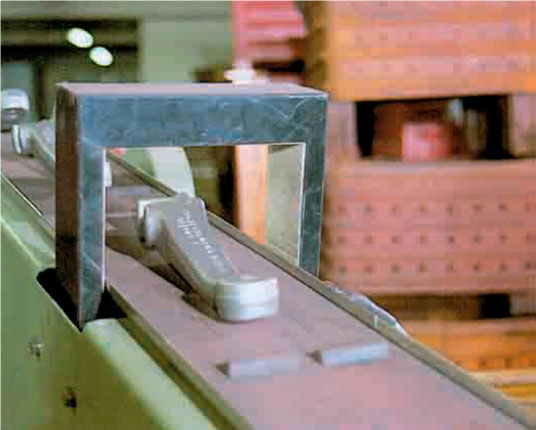
Fig.1: Example of forging parts inspection
By applying a low-frequency magnetic field to a part by passing a current of a specific frequency through an encircling coil, eddy currents are generated in the part by electromagnetic induction, and the change in impedance, which is affected by magnetic permeability and electrical conductivity, is measured. Differences in hardness and tensile strength caused by changes in the crystal structure and microstructure of metals can be determined by magnetic permeability, and different materials can be discriminated by measuring the electrical conductivity. By applying these principles, it is possible to automatically sort out defective parts in a short time.
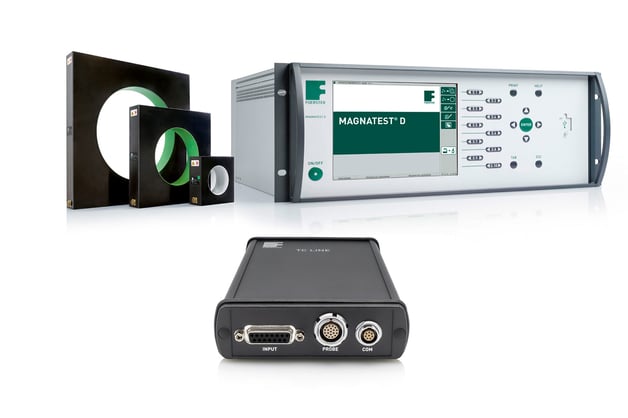
Fig. 2: MAGNATEST product family
For this test, FOERSTER‘s MAGNATEST test instrument and a special coil can be used for the best performance.