Existen dos tipos de motores de corriente continua: los motores con escobillas y los motores sin escobillas. Los motores sin escobillas tienen un imán permanente en el lado del rotor y un electroimán en el lado del estator, lo cual es lo opuesto a la estructura del motor con escobillas, pero tiene muchas ventajas. Dado que el motor es controlado por un sensor de posición en lugar de una escobilla, no hay ruido eléctrico y hay menos vibración, y el rotor es pequeño, delgado y ligero debido al uso de un imán permanente. Sin pérdidas secundarias, es posible obtener una alta potencia mientras se ahorra energía, y la velocidad se puede controlar fácilmente y se puede obtener un par estable desde bajas hasta altas velocidades. Con estas ventajas, se utilizan en una amplia gama de aplicaciones, como robots, automóviles, electrodomésticos, equipos de control y equipos de aire acondicionado.
El imán permanente en el lado del rotor es cilíndrico y el número de polos magnéticos puede cambiarse cambiando el patrón de magnetización, lo que proporciona un alto grado de libertad en el diseño del motor, pero al mismo tiempo, el rendimiento del motor está determinado por la calidad del imán anular. Dado que los imanes anulares se fabrican mediante la formación y sinterización de polvos magnéticos en forma de anillo, la densidad del flujo magnético se ve afectada por la composición del material del polvo magnético, el tamaño de grano cristalino y la densidad después de la sinterización. Dado que esto es lo que se denomina cerámica, los defectos son causados por diversos factores como el estado del polvo magnético, la temperatura durante la sinterización y el grado de rotación térmica en el horno. Por ejemplo, en el caso de un motor de cuatro polos, el motor se magnetiza en el orden de (1) polo Sur, (1) polo Norte, (2) polo Sur y (2) polo Norte, pero si se produce una grieta longitudinal en el centro del (1) polo Sur, se generan nuevos polos Sur y Norte en el (1) polo Sur. Un imán tiene la característica física de formar nuevos polos magnéticos en el extremo agrietado, y como resultado, se forma un imán anular con polos magnéticos complejos en lugar de los cuatro polos que debería tener, y el rotor no gira normalmente incluso si se ensambla en este estado en un motor. Incluso si la grieta es pequeña y el rotor gira, el desequilibrio en la densidad del flujo magnético hace imposible un control preciso. Además, las grietas tan pequeñas que pasan desapercibidas en la inspección visual pueden causar defectos difíciles de identificar.
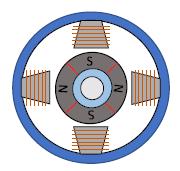
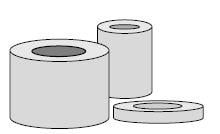
Fig.1: Estructura de los motores sin escobillas y los imanes anulares
Por lo tanto, es esencial inspeccionar las superficies internas y externas del anillo en busca de grietas antes de la magnetización. La inspección por corrientes inducidas es sin contacto y no requiere ningún medio acoplado, como un líquido, para realizar la inspección. La profundidad y el tamaño de las grietas se pueden capturar como señales eléctricas, y la trazabilidad se puede establecer almacenando los datos de inspección al mismo tiempo, lo que la convierte en el método más adecuado para la inspección eficiente de materiales sinterizados.
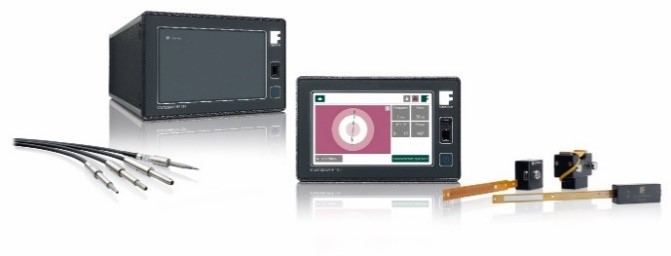
Fig. 2: STATOGRAPH CM / CM+ and different probes
Se logra el mejor rendimiento utilizando el sistema de prueba STATOGRAPH de FOERSTER y sondas especiales para esta prueba.