Pruebas efectivas de dureza móvil para el aseguramiento de la calidad en la industria aeronáutica
Los requisitos de seguridad para los materiales utilizados en la construcción y revisión aeroespacial están en constante evolución.
La industria aeroespacial exige estándares muy estrictos para los materiales utilizados, lo que incluye el uso de compuestos avanzados y aleaciones metálicas que son más livianas y resistentes que los materiales tradicionales, así como procesos extensos de prueba y certificación.
Además, la impresión 3D está ganando cada vez más popularidad, ya que permite la producción de piezas complejas con formas y geometrías especiales que son difíciles de lograr con métodos de fabricación tradicionales.
Materiales como las fibras de carbono, las aleaciones de aluminio y titanio forman un pilar importante en la construcción de metal ligero para aeronaves. Reducen el peso de los componentes de la aeronave, al tiempo que garantizan su resistencia y durabilidad.
Riesgos de componentes livianos para la construcción de aeronaves
En la aviación, los componentes están expuestos a las cargas más extremas. El principal riesgo asociado con los componentes livianos de aeronaves es que pueden no ser tan fuertes y duraderos como los materiales tradicionales. Esto podría provocar fallos en vuelo, lo que tendría consecuencias catastróficas. Además, los componentes livianos pueden ser más susceptibles a daños por temperaturas extremas y fuerzas elevadas.
Los componentes livianos pueden ser más costosos de fabricar, lo que podría aumentar el costo de la producción de aeronaves. Se exigen altas demandas en los procesos de producción, que minimicen los rechazos incluso para pequeñas series de componentes.
¿Cómo se puede limitar el riesgo de fallo de los componentes mediante métodos de pruebas no destructivas?
Para mitigar estos riesgos, es importante que los componentes sean sometidos a pruebas exhaustivas antes de ser utilizados en una aeronave.
Los métodos de pruebas no destructivas se pueden utilizar para limitar el riesgo de fallo de los componentes en aeronaves con pruebas del 100%. Estos métodos incluyen la inspección visual, radiografía, pruebas de corrientes inducidas, pruebas ultrasónicas, pruebas de partículas magnéticas y pruebas de dureza no destructivas.
Estas pruebas se utilizan para detectar fallas y defectos en materiales y componentes que no son visibles a simple vista y que pueden haber surgido, por ejemplo, en el proceso de fabricación. Además, las pruebas no destructivas pueden utilizarse para monitorear la condición de los componentes con el tiempo. Esto significa que se detectan signos de desgaste que podrían conducir a fallos en una etapa temprana.
Campos comunes de aplicación para la medición de dureza móvil en la aviación
Los medidores portátiles de dureza se utilizan ampliamente en la aviación para probar la dureza de los materiales utilizados en componentes de aeronaves como el tren de aterrizaje, el motor y el fuselaje. Por ejemplo, el tren de aterrizaje debe cumplir o superar los requisitos de diseño y los estándares de seguridad especificados antes de ser aprobado para su uso en una aeronave. Esto garantiza que los componentes sean lo suficientemente fuertes para soportar las exigencias del vuelo. La prueba se utiliza tanto en la producción como más tarde en el mantenimiento. Los componentes para probar también pueden variar considerablemente en tamaño: desde los elementos más pequeños de bisagras hasta llantas de ruedas o elementos de las alas.
Los medidores de dureza móvil también pueden utilizarse para probar la dureza de elementos de fijación, como tornillos y pernos utilizados para sujetar componentes a la aeronave, en combinación con pruebas de conductividad para verificar el estado del tratamiento térmico en piezas de aluminio y aleaciones especiales de acero de alta resistencia para asegurarse de que sean adecuadas para su uso en componentes de aeronaves. Los componentes con una amplia variedad de propiedades elásticas a menudo deben medirse rápidamente en sucesión. Además, es ventajoso si los ajustes del dispositivo ya están almacenados en la memoria con anticipación para poder utilizarlos fácilmente durante la prueba. El diseño móvil también permite un uso flexible y versátil en la recepción de mercancías.
Esto muestra que el compromiso se extiende desde la fabricación de componentes hasta el mantenimiento técnico.
La medición móvil de dureza en la aviación debe cumplir con estándares estrictos
Los altos estándares exigidos a la medición móvil de dureza en la aviación incluyen la necesidad de precisión, repetibilidad y confiabilidad que deben mantenerse a lo largo de un largo período. El personal operativo conoce los materiales y la tarea de prueba tan bien como todas las funciones del dispositivo de prueba para una calibración y aplicación óptimas con resultados verificables. La medición móvil de dureza se utiliza para probar la dureza de los componentes de aeronaves que deben cumplir ciertos estándares para ser aprobados para su uso en aeronaves. Las especificaciones de prueba se describen en detalle en las respectivas especificaciones de prueba.
Además, la medición móvil de dureza debe utilizarse en lugares que son inaccesibles para aplicaciones clásicas. De esta manera, se pueden gestionar puntos de medición difíciles de alcanzar, o componentes muy grandes o que no pueden ser removidos, que se prueban en una amplia variedad de direcciones. Además, se debe poder medir un amplio rango de valores de dureza, desde materiales blandos hasta materiales duros. Las mediciones clásicas en el laboratorio generalmente se realizan en piezas de referencia, cuyos resultados luego se utilizan para las pruebas móviles para validar el proceso de prueba.
Después de todo, la medición móvil de dureza debe poder llevarse a cabo de manera rápida y eficiente para que los componentes puedan ser verificados a tiempo para los tiempos de mantenimiento más cortos posibles.
Métodos útiles de medición móvil de dureza para la aviación
El método de prueba UCI (del inglés Ultrasonic Contact Impedance) se destaca como un método. Evalúa electrónicamente una impresión de prueba de dureza Vickers durante la carga en fracciones de segundo y la muestra digitalmente. Debido al pequeño tamaño y profundidad de la indentación, el proceso se considera a menudo no destructivo.
La gran ventaja de la medición UCI en comparación con la medición Vickers óptica en piezas de trabajo es el contacto completo con el material al determinar la dureza Vickers. Medir las longitudes diagonales con el método óptico se vuelve cada vez más difícil, especialmente con indentaciones de medición más pequeñas (baja fuerza de medición, alta dureza).
La medición de dureza UCI se puede ajustar con precisión al trabajo de medición en comparación con la medición clásica de dureza Vickers. Se convierte en el "brazo extendido" de la tecnología de medición de laboratorio clásica en producción o en el área de mantenimiento. Un ajuste del dispositivo para materiales con un módulo de elasticidad diferente (cobre, aluminio, cromo, etc.) es fácilmente posible mediante una medición de comparación con una máquina de medición de dureza clásica (HV, HRC, HB).
¿Dónde se pueden encontrar soluciones UCI para medición móvil de dureza?
Con el SONODUR 3, FOERSTER ofrece un medidor de dureza UCI móvil que cumple con los diversos requisitos de uso flexible con un alto grado de precisión, repetibilidad y confiabilidad al mismo tiempo. El dispositivo se puede usar con la más amplia gama de sondas con fuerzas de prueba estándar de 10 N, 30 N, 49 N y 98 N (sondas de medición manuales) y 1 N, 3 N y 8.6 N (sondas de medición motorizadas). Las sondas manuales clásicas están disponibles con diferentes diseños de punta para alcanzar puntos de medición más profundos, como en perforaciones o en la base de dientes de una rueda dentada. Incluso con altos niveles de dureza, las sondas motorizadas proporcionan máxima reproducibilidad de los valores medidos gracias a su aplicación uniforme de fuerza y uso sencillo con pies de sonda especiales en superficies niveladas y curvas. Utilizando un tubo de soporte de acero, también se pueden medir de manera confiable las superficies de los dientes de engranajes con pequeñas fuerzas de prueba. Las sondas de trípode complementan las soluciones con su guía sin juego de sondas de medición manuales, lo que permite minimizar la dependencia del operador debido a su operación guiada.
Share this
You May Also Like
These Related Stories
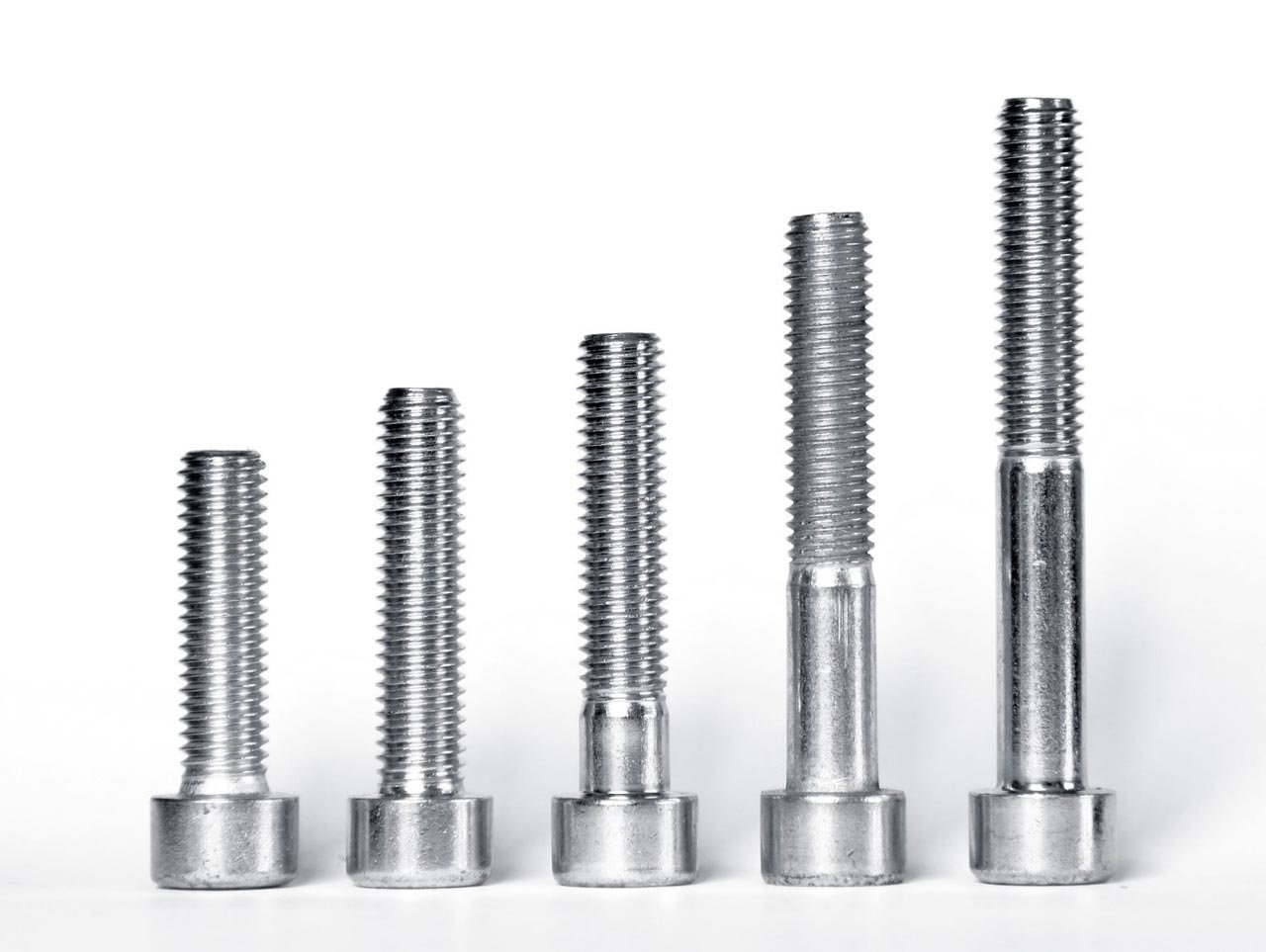
Pruebas de dureza: para que las fijaciones y los tornillos cumplan lo que prometen
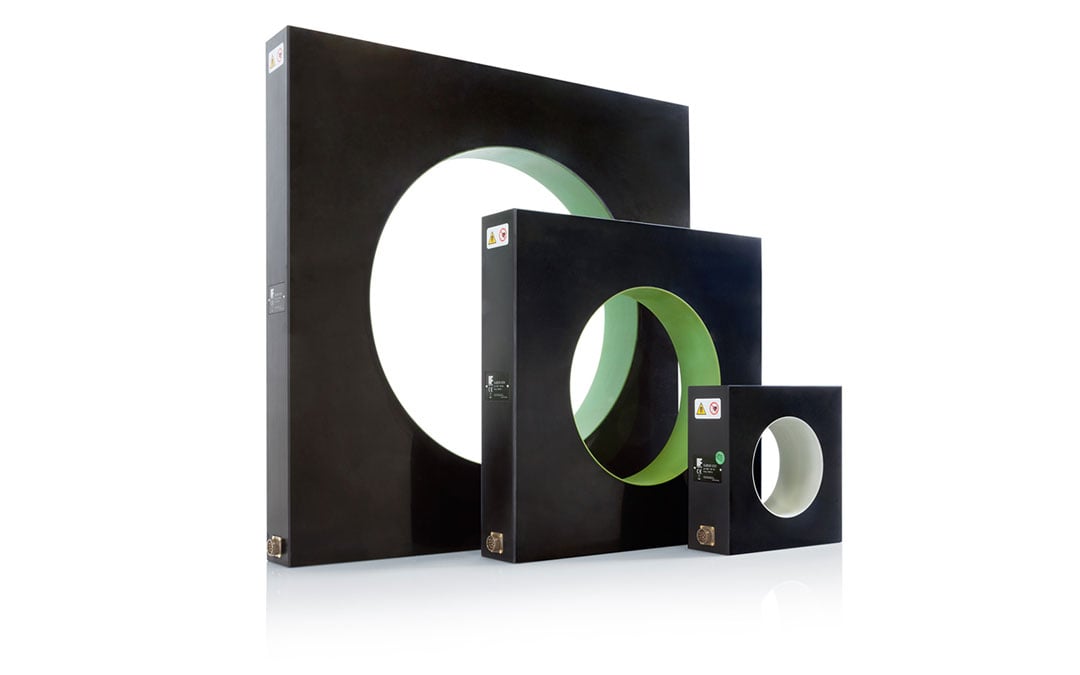
Tipos de bobinas para ensayos de dureza con corrientes inducidas
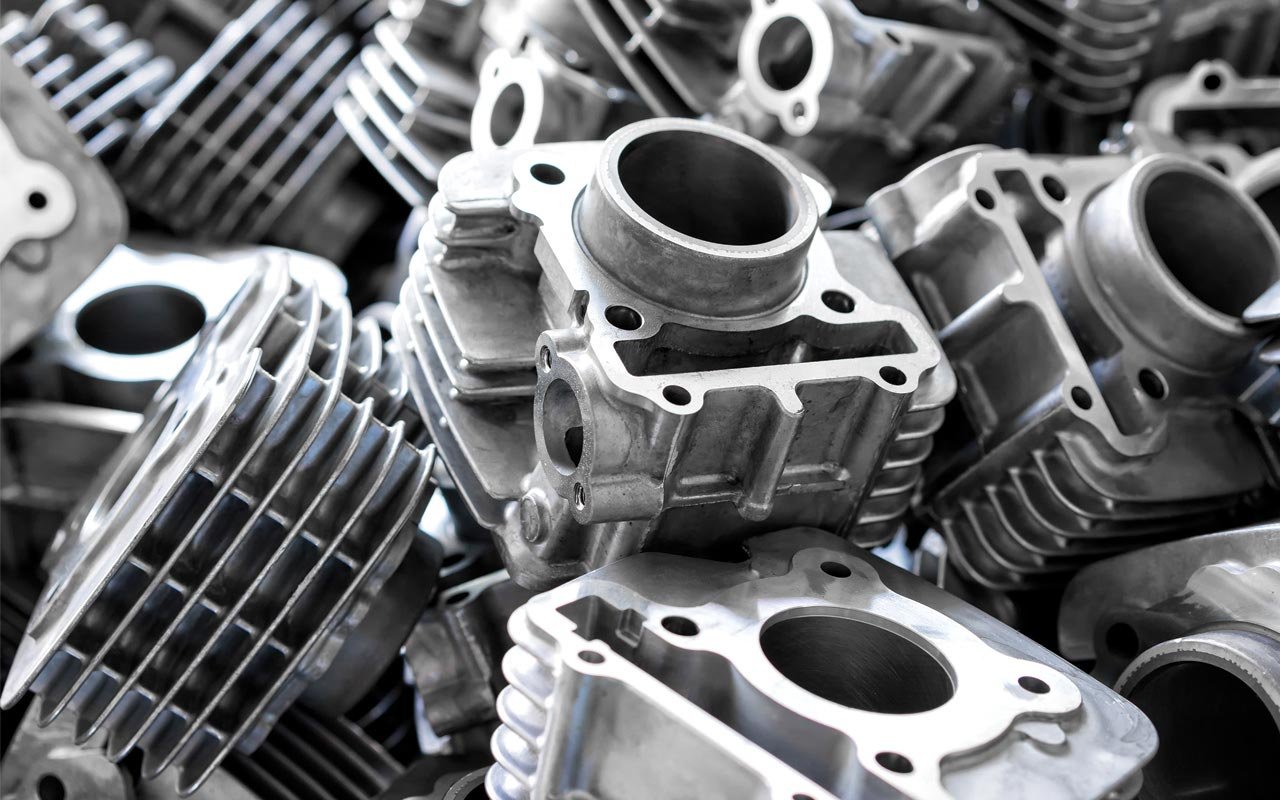