Die Rotorwelle ist das Kernstück des Elektroantriebs und wandelt elektrische in kinetische Energie um. Als zentrales Bauteil des Elektromotors fungiert sie als Trägerwelle für das Blechpaket des Rotors. Über eine formschlüssige Anbindung überträgt die Rotorwelle dabei das elektrisch induzierte Drehmoment an den Antriebsstrang.
Durch die E-Mobilität gewinnt die Rotorwelle immer mehr an Bedeutung. Dadurch steigen die Qualitätsanforderungen an die Welle. Auf Grund der unterschiedlichen Leistungsklassen von Elektromotoren kommen verschiedene Rotorwellen zum Einsatz, die sich neben Größe und Länge auch in den Fertigungsprozessen unterscheiden. So gibt es z.B. Vollwellen, Hohlwellen oder gebaute Wellen. Neben dem Kühlkonzept, hat auch das Thema Leichtbau einen wesentlichen Einfluss auf das Design der Rotorwelle. Dabei gilt es Anforderungen an Drehzahlen von bis zu 25.000 U/min und einem Drehmoment standzuhalten, die oft deutlich über denen eines herkömmlichen Verbrennungsmotors liegen. Aus diesem Grund werden für die Fertigung hoch feste Werkstoffe eingesetzt, die an die entsprechenden Anforderungen der jeweiligen Applikation angepasst werden.
Wirbelstrom- und magnetinduktive Prüfung an Rotorwellen
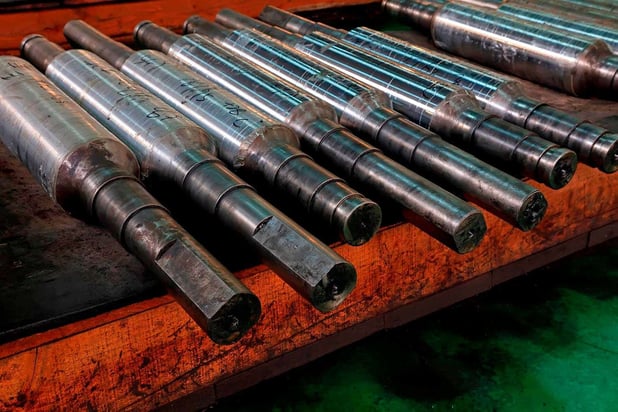
Um diesen enormen Anforderungen an die Rotorwelle gerecht zu werden, ist es von großer Bedeutung, dass die Fertigungsprozesse korrekt durchgeführt und überwacht werden. Die Wirbelstromprüfung bzw. magnetinduktive Prüfung kann hier ideal unterstützen. Denn neben dem Prüfen auf Materialverwechslung, kann auch das Gefüge vollautomatisiert, d.h. 100 % End-of-Line (EoL), geprüft werden. Somit kann sichergestellt werden, dass der Wärmebehandlungsprozess an den Rotorwellen erfolgreich war. Die MAGNATEST Produktfamilie von FOERSTER in Kombination mit speziell gefertigten Durchlaufspulen ist optimal für eine Inlineprüfung. Die Spulen können an jede Anforderung angepasst werden. Große Vorteile der Gefügeprüfung liegen darin, dass das Bauteil nicht beschädigt wird und die Prüfung berührungslos geschieht. Des Weiteren sind keine Kontaktmittel notwendig, die Prüfung ist leicht zu automatisieren und es kann eine hohe Durchsatzleistung erzielt werden.
Warum Risse an Rotorwellen erkannt werden müssen
Beim Fertigungs- und/oder Härteprozess können neben Problemen im Gefüge auch Risse entstehen. Ebenso können bereits im Grundmaterial Risse oder Fehlstellen vorhanden sein. Diese - wie auch ein nicht korrekter Wärmebehandlungsprozess - können dazu führen, dass die Funktion der Rotorwelle eingeschränkt ist bzw. es zum Ausfall und damit zum Stillstand des Fahrzeuges kommt.
Zur Rissprüfung an Rotorwellen bietet FOERSTER das Wirbelstromprüfgerät der STATOGRAPH Produktfamilie an. Mit der Wirbelstromrissprüfung kann die komplette Oberfläche der Rotorwelle abgescannt werden. So werden oberflächenoffene Defekte detektiert und die Qualität der Bauteile kontinuierlich überwacht. Dazu wird die Rotorwelle in Rotation versetzt und mit einem Wirbelstromsensor kontaktlos abgescannt. Dank speziell entwickelter Wirbelstromsonden ist es sogar möglich, Risse im Verzahnungsbereich sowohl im Tal als auch auf dem Zahn zu detektieren. Ebenso können komplexe Rotorwellen mit Bohrungen und Nuten dank der Auswertesoftware STATOVISION vollständig abgetastet werden. Durch intelligente Filteralgorithmen können Störsignale wie Bohrungen oder Nuten gezielt gefiltert und ausgeblendet werden. STATOVISION ermöglicht dabei die Visualisierung der Wirbelstromsignale in einem C-Scan. Dieser C-Scan gibt zum einen Aufschluss über die Qualität der Oberfläche, zum anderen kann eine umfassende Produktdokumentation erstellt werden. Durch die Riss- und Gefügeprüfung mittels Wirbelstrom an Rotorwellen werden frühzeitig fehlerhafte Teile erkannt und spätere Schäden vermieden. Schlussendlich führt dies zu einer Optimierung des Produktionsprozesses.