The rotor shaft is the core of the electric drive. It converts electrical energy into kinetic energy. As the central component of the electric motor, it acts as a carrier shaft for the laminated core of the rotor. The rotor shaft transmits the electrically induced torque to the drive train via a form-fitting connection.
Due to e-mobility, the shaft is becoming increasingly important and the quality requirements for the shaft are increasing. Owing to the different performance classes of electric motors, different rotor shafts are used, which differ not only in size and length but also in the manufacturing processes. For example, there are solid shafts, hollow shafts or assembled shafts. In addition to the cooling concept, lightweight construction also has a significant influence on the design of the rotor shaft. This involves meeting requirements for speeds of up to 25,000 rpm and torque that are often significantly higher than those of a conventional combustion engine. For this reason, high-strength materials are used for production, which are adapted to the corresponding requirements of the respective application.
Eddy current and magneto-inductive testing on rotor shafts
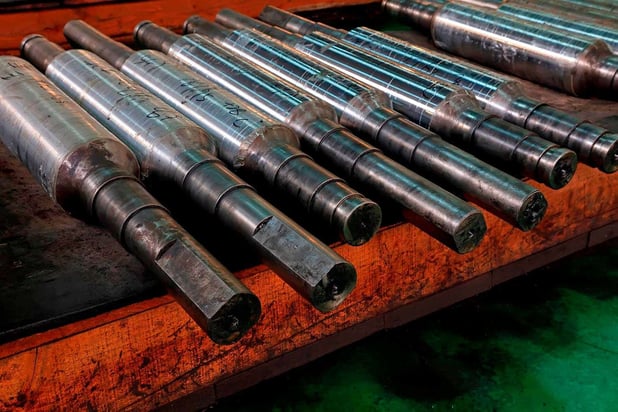
In order to meet these enormous demands on the rotor shaft, it is of great importance that the manufacturing processes are carried out and monitored correctly. Eddy current testing, or magneto-inductive testing, can provide ideal support here. This is because, in addition to checking for material mix-ups, the microstructure can also be inspected fully automatically, i.e. 100% end-of-line (EoL). This ensures that the heat treatment process on the rotor shafts was successful. The MAGNATEST product family from FOERSTER in combination with specially manufactured encircling coils is ideal for inline testing. The coils can be adapted to any requirement. Major advantages of microstructure testing are that the component is not damaged and the test is contactless. Furthermore, no coupling medium is necessary, the inspection is easy to automate and a high throughput can be achieved.
Why cracks on rotor shafts need to be detected
During the manufacturing and/or hardening process, cracks can occur in addition to problems in the microstructure. Likewise, cracks or flaws may already be present in the base material. These - as well as an incorrect heat treatment process - can lead to the function of the rotor shaft being restricted or to failure and thus to a standstill of the vehicle.
FOERSTER offers the eddy current test instrument of the STATOGRAPH product family for crack detection on rotor shafts. With the eddy current crack detection, it is possible to scan the entire surface of the rotor shaft. As a result, surface-open defects can be detected, and the quality of the components can be continuously monitored. For this purpose, the rotor shaft is set in rotation and scanned without contact using an eddy current sensor. Thanks to specially developed eddy current probes it is even possible to detect cracks on both the base and the tooth. Likewise, complex rotor shafts with bores and grooves can be completely scanned thanks to the STATOVISION evaluation software. Interfering signals such as bores or grooves can be selectively filtered and suppressed using intelligent filter algorithms. STATOVISION enables the visualization of the eddy current signals in a C-scan. On the one hand, this C-Scan provides information about the quality of the surface, on the other hand, a comprehensive product documentation can be generated. Crack and microstructure inspection by means of eddy current on rotor shafts enables defective parts to be detected at an early stage and subsequent damage to be avoided. Ultimately, this leads to an optimization of the production process.