Härteprüfung - Verbindungsmittel & Schrauben, damit sie halten, was sie versprechen
Warum Schrauben und Verbindungsmittel auf Härte prüfen?
Schrauben und Verbindungselemente wie Bolzen müssen Bauelemente bei unterschiedlichsten mechanischen Belastungen sicher zusammenhalten. Dabei stellen die Umweltbedingungen nochmals zusätzliche Forderungen an die Materialbeschaffenheit, Konstruktion und den Oberflächenzustand. Dazu gibt es Normen und Vorschriften, denen die Schraubenhersteller mit Ihren Produkten Rechnung tragen müssen. Neben Materialverwechslung beim Wareneingang des Vormaterials spielt die Oberflächenfehlerprüfung auf Risse eine wichtige Rolle. Am Endprodukt wird dann meist die Festigkeit geprüft, die üblicherweise an einer Auswahl von Teilen zerstörend in einer Zerreißprüfmaschine festgestellt wird. Die Schrauben werden in Eigenschafts- bzw. Sicherheitsklassen mit entsprechender Kennzeichnung nach Norm sortiert. Diese Kennzeichnungen sind sehr umfangreich, wie die vielen unterschiedlichen Ausprägungen von Schrauben nahelegen. Baustahlschrauben sind beispielsweise in Festigkeitsklassen eingeteilt nach Zugfestigkeit und Streckgrenze mit einheitlicher Bezeichnung auf dem Schraubenkopf bzw. am Schraubenschaft. „M8.8“ bezeichnet hierbei M = Sechskantschraube metrisches Maß, 8 x 100 = 800 MPa Zugfestigkeit und 8 x 8 x 100 = 640 MPa Streckgrenze oder bei „M12.9“ würde stehen: 12 x 100 = 1200 MPa und 12 x 9 x 100 = 1080 MPa. Dies sind zwei der Mindestanforderungen, die erfüllt werden müssen und sind in sogenannten Schraubenfibeln zu finden.
Da die Zugfestigkeit mit der Härte des Werkstoffs positiv korreliert (≥HV 10) und empirische Umwertungsregeln existieren z.B. nach EN ISO 18265, wird aus praktischen Gründen immer wieder auch die Härtemessung zur Qualitätsbeurteilung herangezogen. Dies ist insbesondere dann wichtig, wenn eine größere Zahl an Schrauben, Bolzen usw. überprüft werden muss und/oder die geometrischen Abmessungen einer Zerreißprobe entgegenstehen. Dabei ist die klassische Härteprüfung nach Vickers, Brinell und Rockwell zwar flexibler, jedoch muss i.d.R. eine aufwendige Oberflächenbearbeitung ausgeführt werden bzw. die Schraube muss für den Prüfprozess zerteilt und häufig eingebettet werden. Diese zusätzlichen Arbeiten versucht man zu umgehen, indem mobile Härteprüfverfahren wie z.B. die UCI-Methode (Ultrasonic Contact Impedance) zum Einsatz kommen. Allerdings gibt es auch hier keine pauschale Aussage zur Anwendbarkeit. Aufgrund der hohen Variabilität in den Ausprägungen von Schrauben und Bolzen sind Versuche an Mustern vorab sehr zu empfehlen. Besonders brisant wird die Situation, wenn trotz aller Vorsichtsmaßnahmen sicherheitsrelevante Schrauben beispielsweise schon im Fahrzeug oder auf der Baustelle verbaut sind und eine nachträgliche Entnahme sehr beschwerlich ist. Dann kommt auch dort die Härtemessung mit UCI zur Verwechslungsprüfung ins Spiel, da die Messung einfach direkt am eingebauten Teil in jeder Richtung schnell und sicher ausgeführt werden kann.
Für weitere Informationen zum Thema „UCI Härtemessung“ klicken Sie bitte hier.
Härteprüfung bei Verbindungsmitteln & Schrauben: Wie wird's gemacht?
- Was sind heutige Lösungsansätze?
- Wo greifen diese zu kurz?
- Welche Herausforderungen gibt es beim Härteprüfen von Schrauben und Verbindungsmitteln?
- Was sind einschränkende Faktoren?
Schrauben und Bolzen werden für den Anwendungsfall optimiert hergestellt. Dazu gehören Oberflächenbeschichtungen gegen Korrosion oder für optimale Gleiteigenschaften und sogar lokale Härte- bzw. Festigkeitseigenschaften durch thermische Behandlung. Somit müssen an vorbestimmten Stellen wie Schraubenkopf, -schaft und -ende die Kernhärte und Oberflächenhärte mit definierten Prüfkräften zwischen HV 0,3 und HV 10 abgenommen werden. Dementsprechend müssen die Härteprüfverfahren auf diese Aufgaben eingestellt werden. Vor der Messung des Werkstoffs müssen Oberflächenbelegungen entfernt werden. Messungen am Schaft sind für die Vickers-Härteprüfung schwierig, da die Oberfläche üblicherweise flach angeschliffen werden muss, um die Diagonalen des Eindrucks richtig zu erfassen. Der Prüf-Ort auf der Schraube muss gut erreichbar sein, was aufgrund des aufwendigen Aufbaus einer Prüfmaschine häufig ein Zerlegen der Schraube erfordert. Schließlich muss die Schraube dann auch noch bei konischem Körper richtig ausgerichtet (eingebettet und poliert) werden, weil sonst je nach Steigung die Optik zur Auswertung des Prüfeindrucks nicht gut genug fokussiert werden kann.
Welche Härteprüfverfahren gibt es?
Je nach Anforderung stehen verschiedene Prüfverfahren zur Verfügung. Gängig sind hierbei vor allem die folgenden:
- Martens (Universalhärte)
- Vickers (HV)
- Rockwell (HR)
- Brinell
- Knoop
- Shore
- Barcol
- Buchholz
Mit der UCI Härteprüfung einen Schritt voraus bei Verbindungsmitteln & Schrauben?
Weshalb bzw. wann und wo ist das UCI-Verfahren besser geeignet für die Härteprüfung von Schrauben und Verbindungsmitteln?
Das Wesen der UCI-Härteprüfung ist die Messung der akustischen Impedanz eines Körpers über die Frequenzverschiebung eines in Resonanz schwingenden Stabes mit Vickers-Diamanten. Aus der Frequenzverschiebung Δf bei einer bestimmten vordefinierten Prüfkraft wird die Härte des Werkstoffs bestimmt. Dabei bildet die Vickers-Härteskala die Referenz für jeden Werkstoff. Die UCI-Geräte sind auf Werkstoffe mit ca. 210 GPa E-Modul justiert und lassen sich über eine Vergleichsmessung mit einer Vickers-Härteprüfmaschine genau auf die neue Aufgabe einstellen. Dies ist nur einmal nötig, weil die Einstelldaten immer wieder reproduzierbar aus dem Speicher abgerufen werden können.
SONODUR 3 mit UCI-Messsonden
Somit ist die Schraubenprüfung mit UCI sehr einfach und schnell durch einmaligen Vergleich mit der Vickers-Skala möglich. Da die UCI-Sonden stiftförmig mit dünnen Prüfspitzen (Φ 2,5 mm bzw. speziell Φ 1,7 mm) sind, können auch schwierige Prüfpositionen getroffen werden.
Gleichwohl sind hier die Randbedingungen aus der Anwendung der UCI-Methode zu beachten. Die Oberfläche muss sauber bzw. angeschliffen sein, jedoch nicht unbedingt blank. Zudem muss der Mess-Ort für die Sonden-Spitze zugänglich sein. Das Bauteil muss fest und von möglichen Bauteil-Resonanzen entkoppelt sein. Resonanzen lassen sich i.d.R. sehr gut über stark streuende und überhöhte bzw. viel zu niedrige Messwerte erkennen, die weit außerhalb des Erwartungsbereichs liegen.
Schäfte können nach Norm DIN 50159-1 noch bis zu Φ 3 mm ohne besondere Maßnahmen gemessen werden. Mit Prüfkräften zwischen HV 0,1 UCI (Motor-Mess-Sonden) und HV 10 UCI (Hand-Mess-Sonden) können Schrauben als Ganzes oder auch eingebettet sowohl manuell als auch im Stativ gemessen werden. Aufgrund der Schnelligkeit der UCI-Messung bei gleichzeitig hoher Präzision ist eine Vielzahl von Messungen gegenüber klassischen Methoden möglich. Dadurch können ganze Messreihen durch Abscannen des Schafts ein detailliertes Bild über das erreichte Behandlungsergebnis liefern.
Ein geeignetes Werkzeug zur Härteprüfung bei Schrauben und Verbindungsmitteln
SONODUR 3: Portable Härtemessung für höchste Flexibilität und präzise Ergebnisse
Das SONODUR 3 ist unter den UCI-Härte-Prüfgeräten prädestiniert für schwierige Prüfaufgaben. Es verfügt derzeit im Markt über das breiteste Sonden- und Zubehörprogramm. Über Touchscreen lassen sich beliebig umfangreiche Messreihen schnell auf fehlerhafte Messungen durchsuchen und bewerten – dazu müssen Sie nur „Extremwerte“ antippen und SONODUR 3 sucht den verdächtigen Messwert auf. Darüber hinaus bilden sowohl die Versuchsführung (Umwertungstabellen, Justierfunktion CAL und Eindringzeit), als auch die Dokumentationsmöglichkeiten (Datenformate CSV, .txt, HTML, wireless, USB, Foto) ein starkes Argument für den Einsatz von SONODUR 3.
Erfahren Sie weitere Vorteile vom SONODUR 3!
Share this
Vielleicht gefällt Ihnen auch
Verwandte Artikel
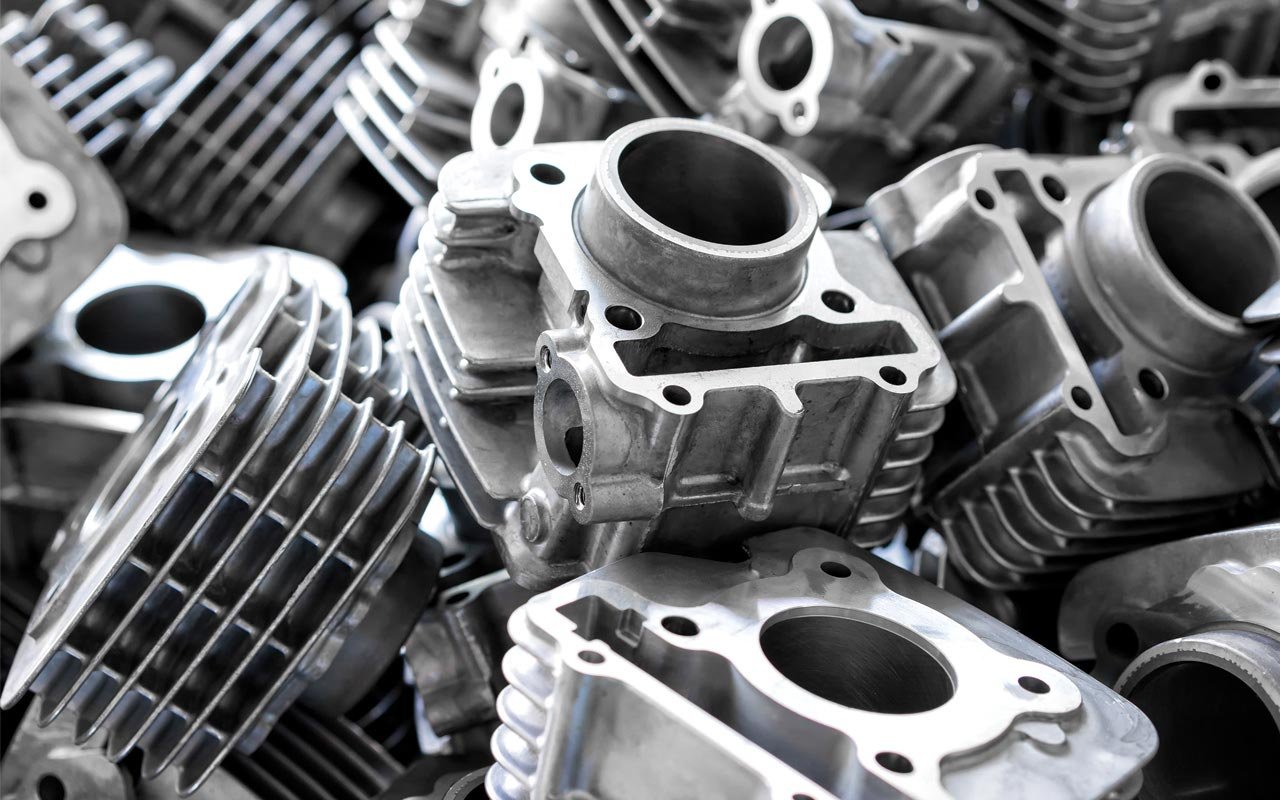
Mobile Vickers-Härtemessung mit UCI zur Entlastung des Prüfpersonals
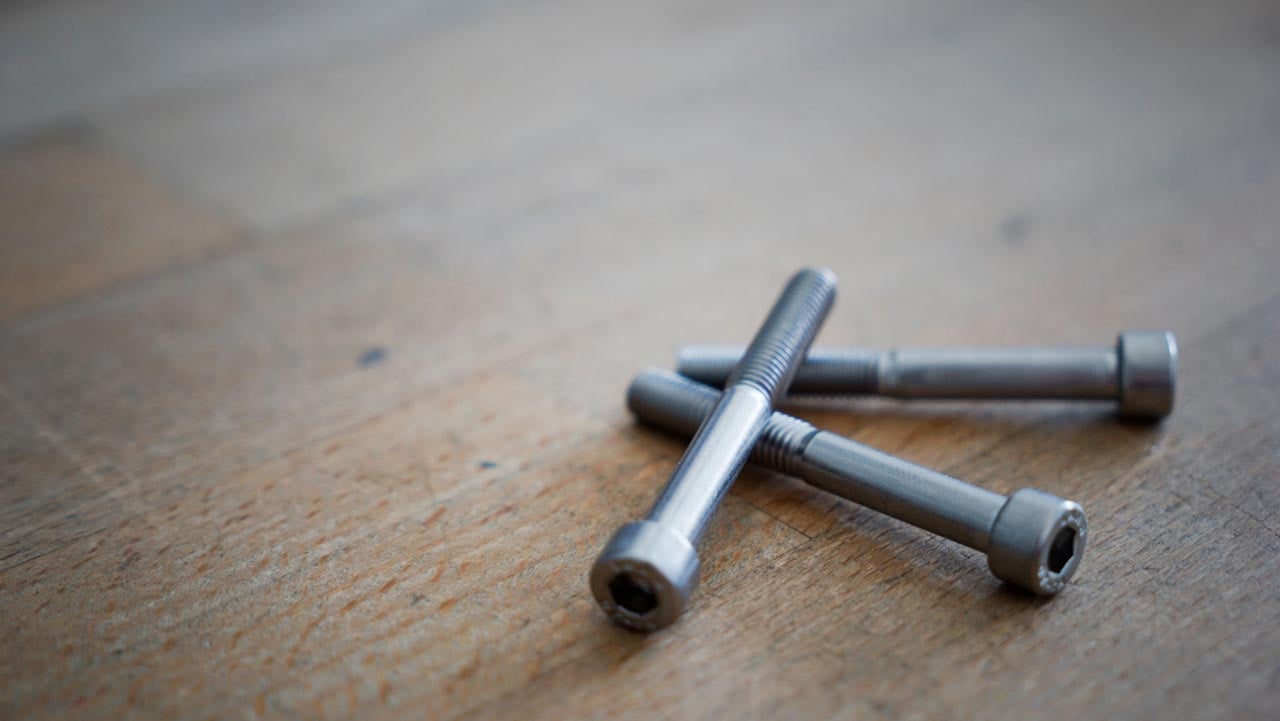
Schnelle UCI-Härtemessung an Schrauben und Bolzen: Anwendungsfälle aus der Praxis
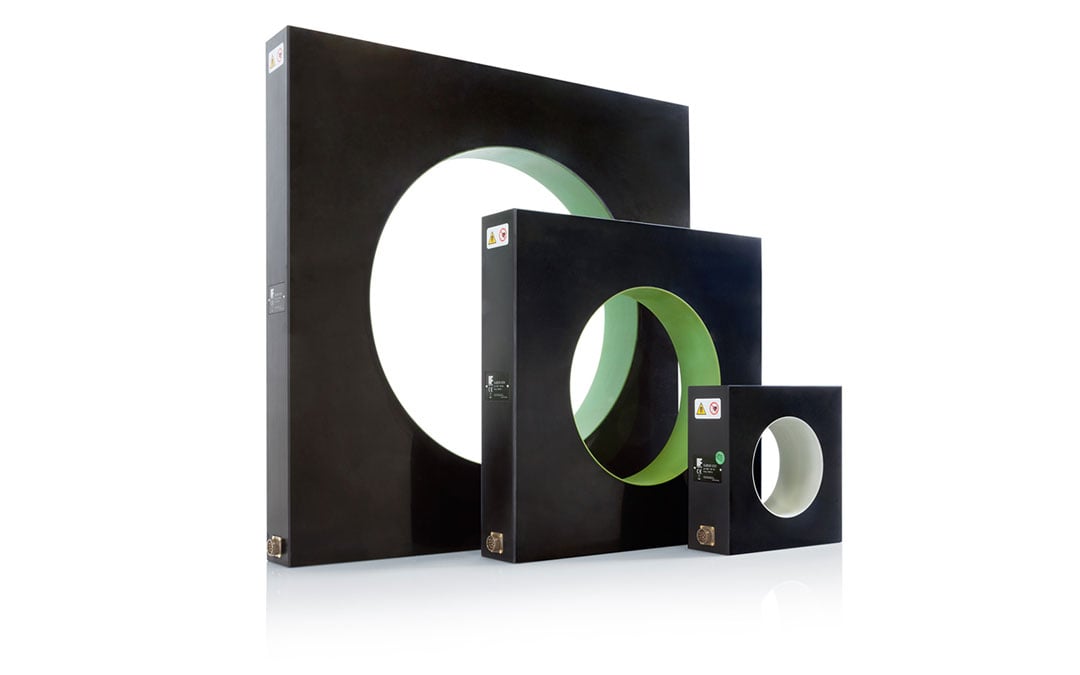