Brake discs are one of the safety-relevant components of a vehicle. Therefore, the highest demands are placed on the material used. The material must withstand both high mechanical and thermal loads during braking. For this reason, it must be ensured that only defect-free material is installed.
Figure 1: Brake disc
In order to test the material surface of brake discs for longitudinal, point and transverse defects, FOERSTER offers a fully automated 100 % crack testing system in the production line. For this, the STATOGRAPH eddy current test instrument is used in combination with highly sensitive probes. The non-destructive eddy current testing method is based on a comparison with reference defects.
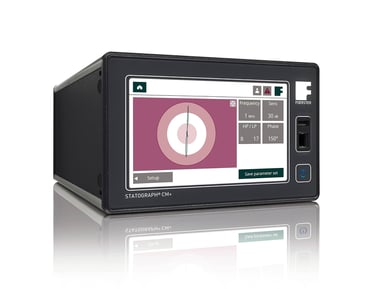
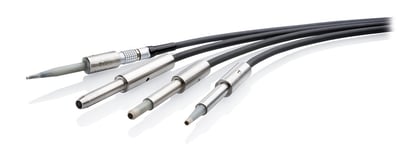
Figure 2: STATOGRAPH CM+ with various probes
During testing, defined, fault-prone zones of the the braking surface and bolting surface are examined both on the outside and inside of the brake disc. The automatic testing allows a high throughput speed of about 240 parts per hour.
Figure 3 shows a schematic drawing of a brake disc being tested. In this case, the testing concept has been adapted to the requirements of the testing job so that four separate probes scan the relevant testing zones of the brake disc. These probes can be adapted per customer specifications to the respective material in order to enable a sensitive and reproducible test. The use of several test modules results in a multi-channel solution working at a high clock speed.
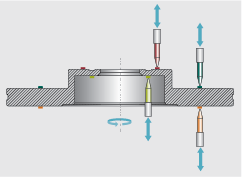
Figure 3: Testing principle
Following the test, automatic sorting takes place in two groups „OK“ and „NOK“. Detailed documentation functions of the testing results support the continuous quality assurance.
For the crack detection of brake discs we recommend the STATOGRAPH test instrument with appropriate probes. This combination allows early detection of surface defects and supports continuous monitoring of product quality. For further information, please visit our website at: foerstergroup.com