Conductivity measurement of metallic materials
Electrical conductivity is a physical quantity that describes the ability of substances to conduct an electrical current. In electrical engineering, electrical conductivity is represented by the Greek symbol sigma. The derived SI unit for electrical conductivity is represented in Siemens per meter (S / m).
The ability to conduct electricity depends on various factors. For instance, the mobile electrons present in the material or the geometry of the component. Basically, the electrical conductivity increases with the number of freely moving electrons in the material. Solid or granular substances, therefore, have different conductivities.
In electrical engineering, electrical conductivity plays an important role. Reason for this is that most of the materials used have very good electrical conductivity. Some applications include connecting various electronic components on a printed circuit board made of materials with high conductivity or using non-electrically conductive materials as isolation or resistance insulation.
In which areas does electrical conductivity play an important role?
Electrical conductivity is used in various industrial sectors and range of branches. Typical application examples where materials used are tested for their electrical conductivity are:
- Manufacturing of printed circuit boards (PCBs): Measurement of the electrical conductivity of galvanized copper
- Testing the discharge capacity of components: commonly performed in aircraft construction to ensure functionality in the event of material stress, such as a lightning strike
- Testing the electrical conductivity of insulators: for example when used for power lines
Electrical conductivity can also be used for quality assurance, as it allows conclusions to be drawn about the properties of materials. This makes it possible to determine whether a material is suitable for its intended use.
Each material has a specific electrical conductivity, which can vary within a certain range. By combining different materials in metallic alloys, a specific electrical conductivity is created for this group of elements.
Measurement of the electrical conductivity allows the present material to be determined. This measurement is used in various industries for material identification. Possible applications are among others:
- Incoming goods inspection in production plants to check the delivered material quality
- Coin mint to ensure the use of the correct material alloy
- Jewelers and jewelry manufacturers, to distinguish the material quality of the gold used
- Recycling yards, to separate materials such as copper, brass, aluminum or titanium
How to measure electrical conductivity?
Conductivity measurement by the van der Pauw method
The Van der Pauw measuring method is a technique to easily measure the electrical conductivity. Here, the voltage drop of a defined impressed current is recorded. Furthermore, the measurement setup determines the electrical resistance, which can be converted into the electrical conductivity with known layer thicknesses.
Van der Pauw Method
The material is contacted via four pins. This step is the most error-prone one, since the contact quality is decisive for the measurement. Achieving this depends on various factors: on the one hand, on possible soiling or unevenness on the surface, on the other hand, on the wear of the contact tips.
In serial applications it is therefore difficult to measure the electrical conductivity with this method.
Eddy Current Measurement of the Electrical Conductivity
The eddy currents generate alternating magnetic fields in conductive materials, which act in the opposite direction to the primary field introduced. This interaction can be measured by secondary inductors. Conductive materials have an effect on the amplitude and phase of the secondary field due to the formation of eddy currents.
The phase shift between the primary and secondary field can be used as a measure of electrical conductivity. By calibrating the phase shift in relation to the conductivity, an eddy current meter can be used to measure the electrical conductivity.
One of the great advantages of eddy current measurement is that it is contactless. Thus, non- destructive. In other words, the surface quality remains unaffected.
The distance of the eddy current probe to the measuring surface has a great influence on the measuring accuracy. On this note, the eddy current measuring instruments available on the market usually have the function of measuring the distance from the probe to the measuring object.
The conductivity is strongly dependent on the temperature. If the temperature of the test object differs from that of the measuring probe, the calibration curve for determining the electrical conductivity is no longer accurate. Thus, the sensor head must be thermally coupled with the component to be tested in order to obtain a uniform temperature level, and an exact measurement.
Another challenge is the measurement of conductivity on a curved surface, e.g. a wave. If the diameter of the probe head is significantly larger than the radius of the surface to be examined, it is difficult to carry out the measurement. To make this possible, an eddy current measuring instrument can be additionally calibrated to different radii. On the same note, it is important to use the required radius.
The formation of the eddy currents and the secondary alternating field generated by them also depends on the frequency used. Eddy currents only form from a few hundred hearts up to several kilohertz. The higher the frequency used, the larger the eddy currents become. Very high frequencies of up to one megaherz are therefore required for very thin layers to be measured. For this reason, the calibration of the eddy current measuring instrument must be carried out at different frequencies. At very high frequencies and electrical conductivities, the demands on the measurement hardware increase strongly, since the sensitivity, i.e. the skin effect, is very small due to the conductivity.
A great advantage of eddy current instruments is the possibility of automated series testing directly in the production line: Thanks to fast measuring sequences and this contactless method, measurements can be performed with high reproducibility.
FOERSTER’s product solution for measuring electrical conductivity
With the SIGMATEST, FOERSTER has an established and reliable measuring instrument in its portfolio designed for measuring electrical conductivity. As a case in point, the SIGMATEST is approved for many maintenance applications in aviation. In industry, it is used in the quality control of manufacturing products, the testing of material combinations and the sorting of metals, alloys or recyclable materials. The determination of heat damage and in-process inspection in manufacturing and processing in metallurgy are additional fields of application.
Five different test frequencies and a very high measuring accuracy characterize the portable measuring device. Even at a high frequency of 960 kHz the device achieves a very high measuring accuracy. Thus, even very thin materials can be measured exactly. In addition, the measuring device can automatically normalize the measured value of the electrical conductivity to 20°C due to the built-in temperature compensation.
Share this
You May Also Like
These Related Stories
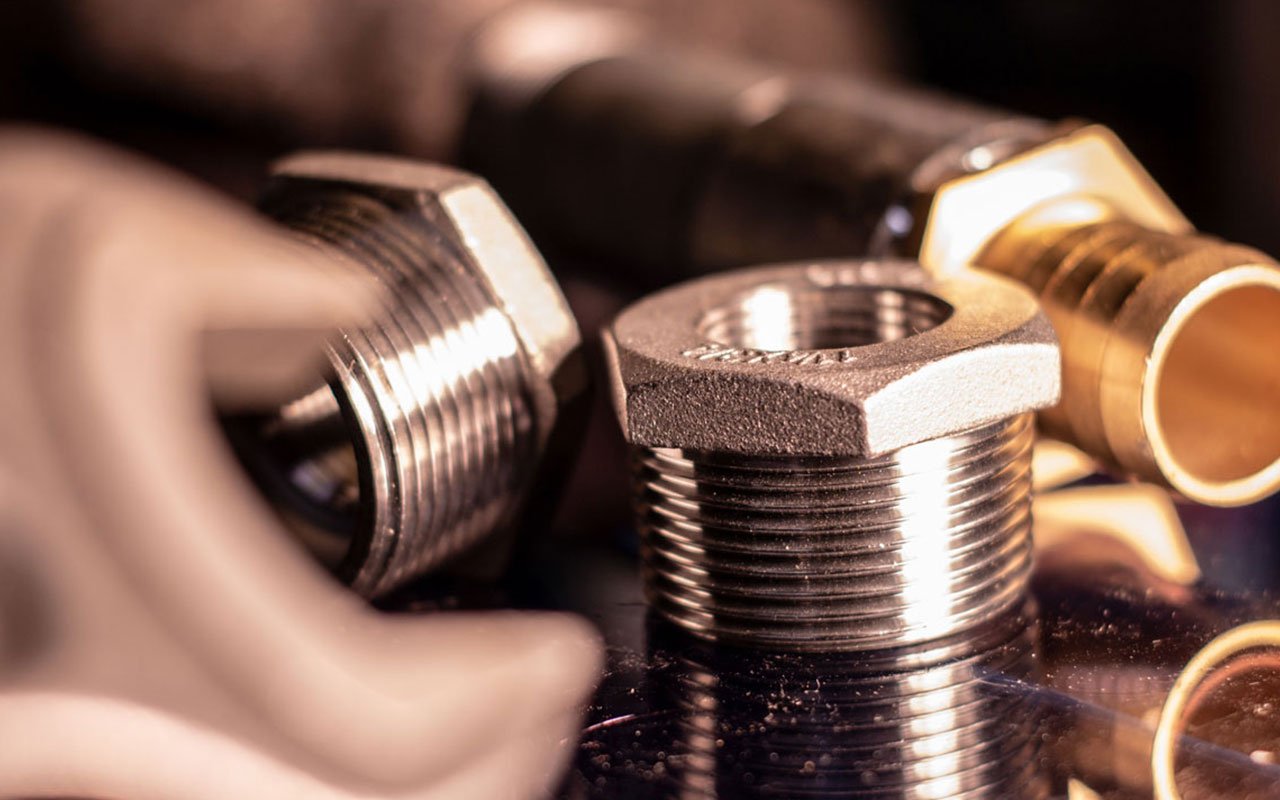
Electrical conductivity measurement with eddy current - 6 factors you should pay attention to
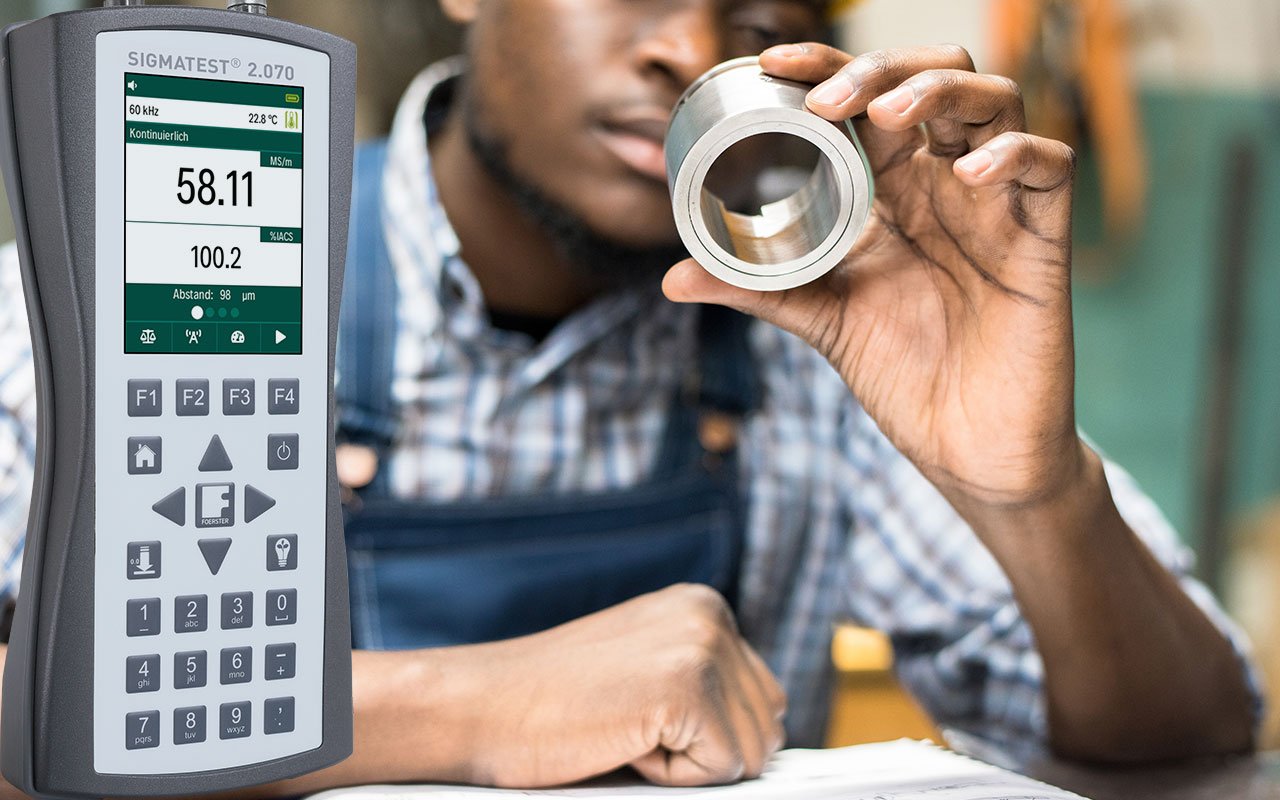
The different types of calibration standards for measuring electrical conductivity
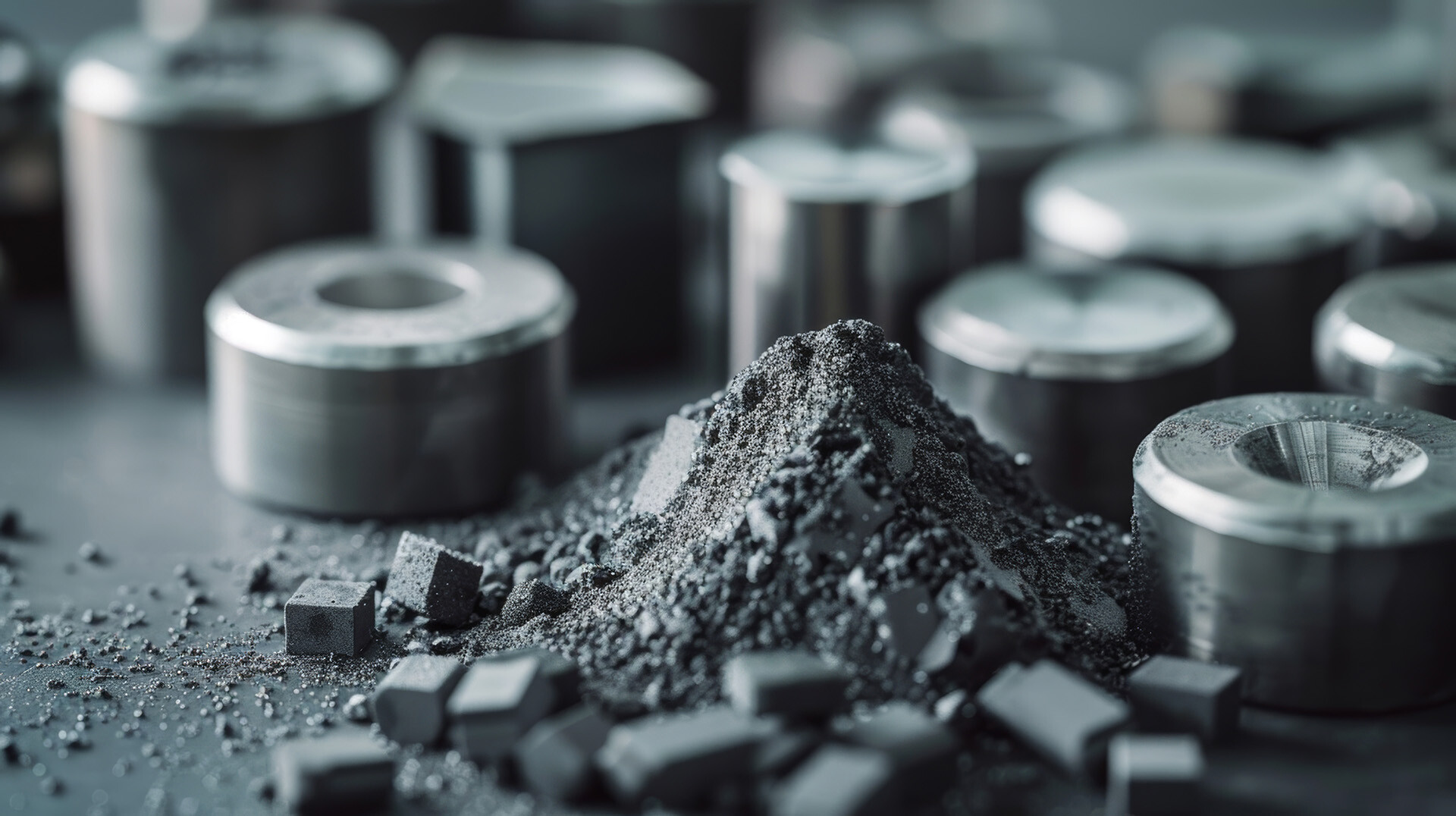