The Importance of Density Verification with Sintered Metal Parts
Introduction to Sintered Parts
Sintered parts are components manufactured through a process known as sintering, which involves compacting powdered materials into a die and heating them below their melting points to form a solid mass. This method is renowned for producing parts with intricate shapes and precise dimensions. Industries such as automotive, aerospace, and medical sectors widely use sintered parts due to their distinct advantages, which include:
- High Precision: Sintering enables the creation of complex shapes and tight tolerances without the need for extensive machining.
- Material and Production Efficiency: Utilizing powder metallurgy significantly reduces material waste compared to traditional manufacturing methods. The near-finished state of molded parts also eliminates costly secondary operations.
- Mechanical Properties: Sintered parts achieve a balance of strength, hardness, and ductility tailored to specific applications.
Understanding the significance of density verification in sintered metal parts is crucial, as it directly impacts these properties and the overall performance of the parts.
Mechanical Properties of Sintered Parts
Strength
Strength refers to the material's ability to withstand an applied force without breaking or deforming. This includes different types of strength:
- Tensile Strength: Resistance to being pulled apart.
- Compressive Strength: Resistance to being compressed.
- Shear Strength: Resistance to sliding forces.
Ductility
Ductility measures a material's ability to deform under tensile stress. Ductile materials can undergo significant plastic deformation before rupture, making them more pliable and less likely to crack under stress.
Hardness
Hardness is the measure of a material's resistance to deformation, particularly permanent deformation, scratching, or indentation. Harder materials are more resistant to wear and abrasion but may be more brittle and less ductile.
In summary, strength measures the ability to withstand forces, ductility indicates the material's ability to stretch or bend before breaking, and hardness assesses resistance to surface deformation and wear.
Factors Influencing Density in Sintered Parts
Powder Mixing and Blending
Inconsistent mixing of the powder can lead to uneven distribution of particle sizes and types, resulting in density variations. Ensuring a homogenous mixture is essential for uniform density.
Compaction Speed and Pressure
Variations in the pressure applied during the compaction process can cause differences in green density (density before sintering) and uniformity, translating to variations in the final sintered density.
Powder Particle Size and Shape
The size and shape of the powder particles influence how well they pack together. Irregularly shaped particles or a wide range of particle sizes can cause non-uniform densities.
Sintering Temperature and Time
Inconsistent sintering temperatures can lead to uneven densification. Higher temperatures generally increase density, so variations in temperature can cause density differences within the part. Additionally, insufficient sintering time can result in lower density, while excessive time can cause grain growth and other issues.
Cooling Rate
The rate at which sintered parts cool can affect the microstructure and density. Rapid cooling might trap residual stresses, while slow cooling can lead to different microstructural features.
Controlling these factors is essential to achieving uniform density and consistent mechanical properties in sintered components.
The Necessity of Density Verification
Given the challenges of maintaining correct mechanical and atmospheric conditions to produce homogeneous sintered components, validating density has become highly important. Current industry standards typically involve batch testing or weighing each part on a sensitive scale. However, these processes can be time-consuming and tedious, requiring special metallurgical tools and a lab for destructive analysis.
Low-Frequency Eddy Current Testing
Low-frequency eddy current testing (magneto-inductive testing) offers a solution for in-line testing of every part produced on a production line, both in the green state and after sintering. Parts do not need to be handled individually but pass through an encircling test coil via a non-conductive conveyor. This method allows even fragile green parts to benefit from the test.
The advantage of green part testing is that if the part fails the test, it can be easily recycled back into the powder since the sintering process has not occurred, and bonding has not taken place.
FOERSTER MAGNATEST D
The test setup consists of a FOERSTER MAGNATEST D device connected to an encircling test coil. A conveyor belt carries the pressed part through an appropriately sized coil, triggering the test device. An alternating magnetic field is induced into the powder part, where variations in the material’s conductivity and/or permeability affect the induced field. The test device then calculates these variations, allowing for a simple pass/fail approach, with the test completed in less than one second.
Benefits of Post-Sintering Testing
In the post-sintering stage, the benefits of the MAGNATEST D are further enhanced, as it can check for:
- Heat treatment range
- Interior porosity
- Fields of micro-cracking
- Delamination
All these checks can be done without marking or altering the component in any way.
Key Features of MAGNATEST D
- Up to 4 amps coil current
- Single coil testing (no need for a comparison coil)
- Multi-channel operation (can run up to 16 separate coils)
- Higher harmonic evaluation up to 8kHz
- Frequency ranges from 2Hz to 128kHz
- User-friendly interface
Conclusion
In conclusion, the importance of density verification in sintered metal parts is clear. The mechanical properties of strength, ductility, and hardness are all directly influenced by the density of the material. Variations in the sintering process can lead to density inconsistencies, which in turn affect the performance and reliability of the parts.
Implementing advanced testing methods like low-frequency eddy current testing with devices such as the FOERSTER MAGNATEST D can significantly improve the efficiency and accuracy of density verification. These methods provide a non-destructive, in-line solution that ensures each part meets the required standards, ultimately leading to higher quality and more reliable sintered components.
By understanding and controlling the factors that influence density, manufacturers can produce sintered parts that meet stringent industry requirements, thereby enhancing the performance and longevity of the final products.
Share this
You May Also Like
These Related Stories
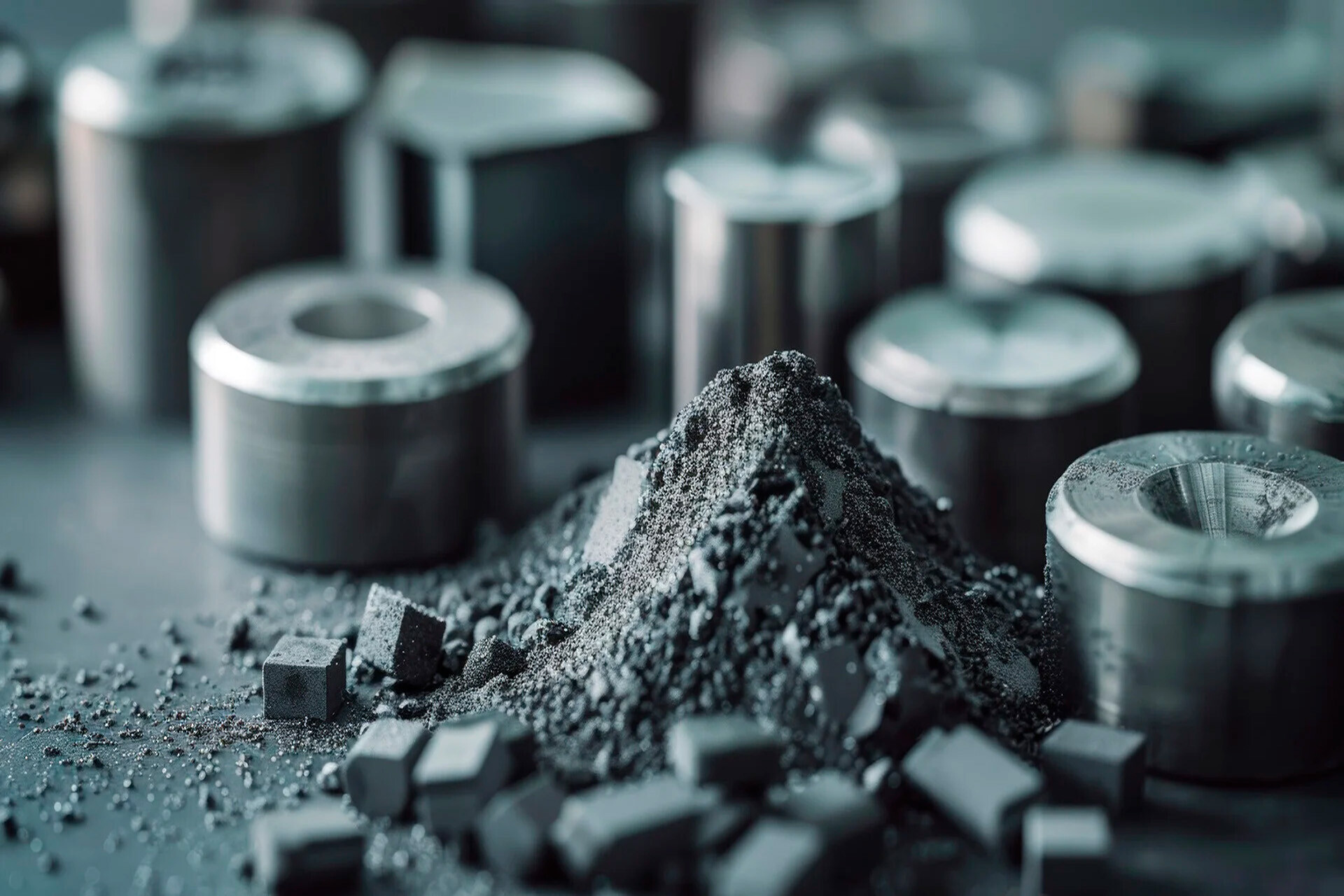
Die Bedeutung der Dichtheitsprüfung bei Sintermetallteilen
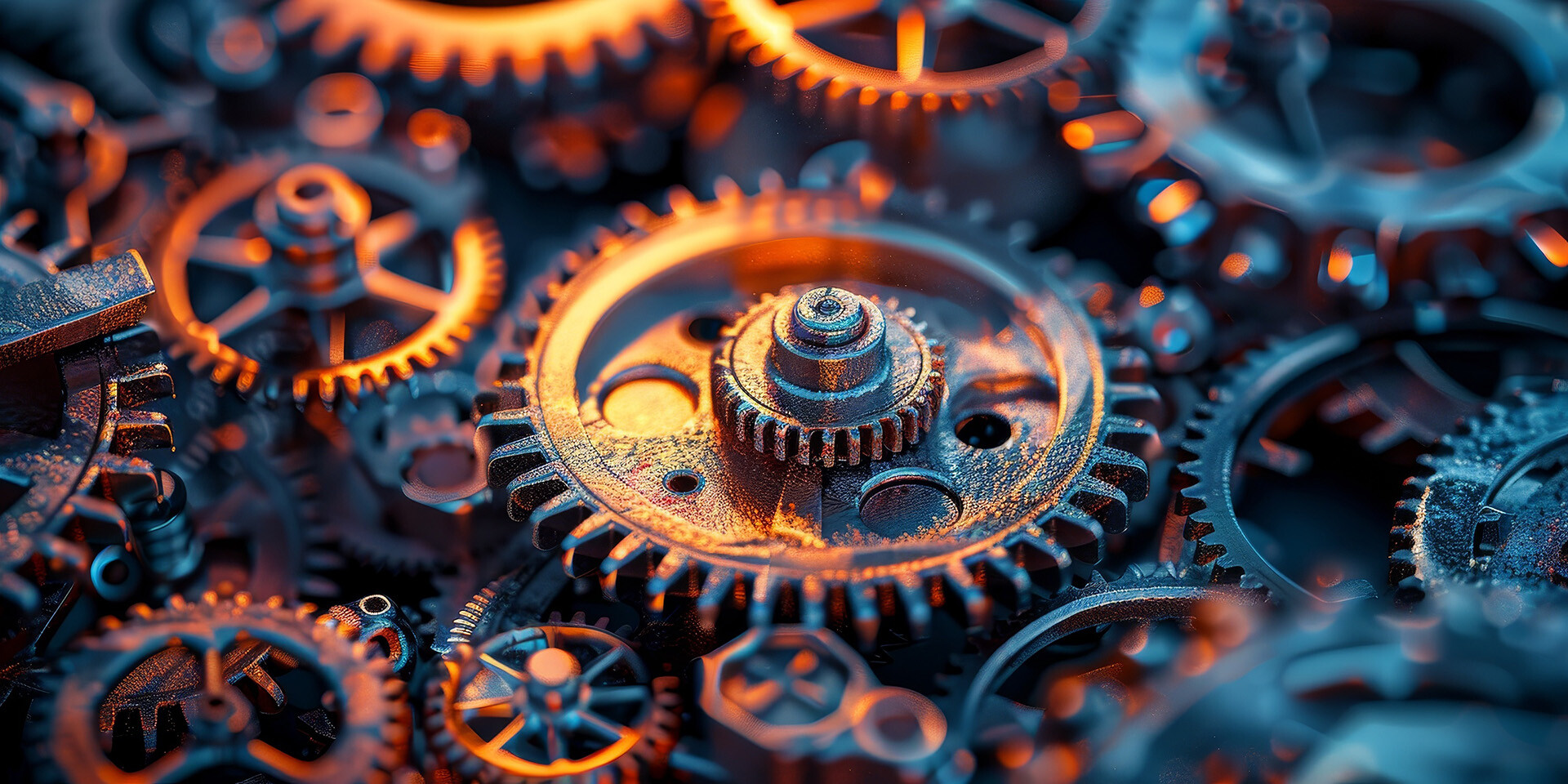
Revolutionizing Gear Manufacturing with Eddy Current Testing
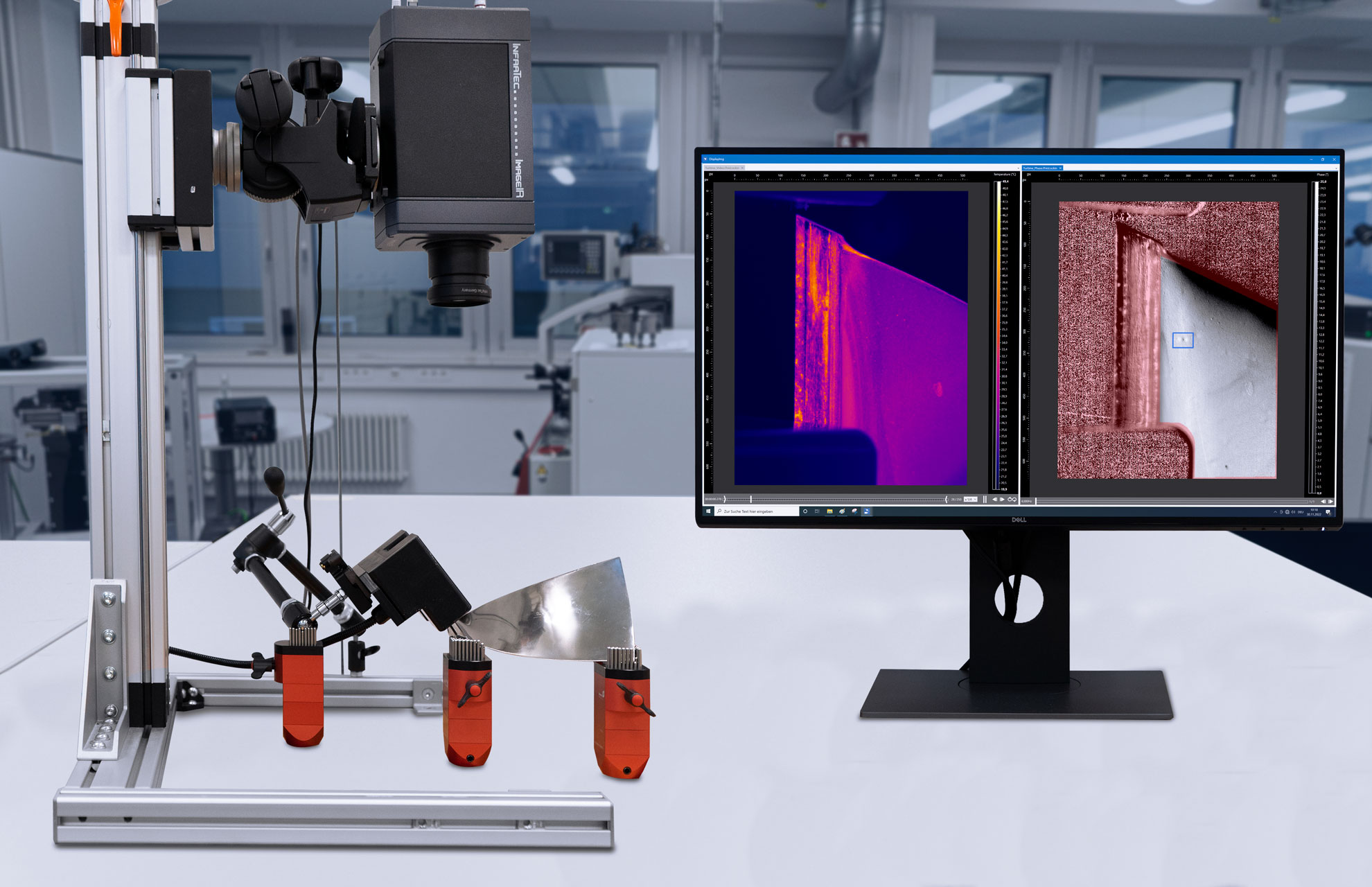