There are two types of DC motors: brushed and brushless motors. Brushless motors have a permanent magnet on the rotor side and an electromagnet on the stator side, which is the opposite of the brushless motor structure, but it has many advantages. Since the motor is controlled by a position sensor instead of a brush, there is no electrical noise and less vibration, and the rotor is small, thin, and light because it uses a permanent magnet. With no secondary losses, high output is possible while saving energy, and the speed can be easily controlled and stable torque can be obtained from low to high speed ranges. With these advantages, they are used in a wide range of applications such as robots, automobiles, home appliances, control equipment, and air conditioning equipment.
The permanent magnet on the rotor side is cylindrical and the number of magnetic poles can be changed by changing the magnetization pattern, which provides a high degree of freedom in motor design, but at the same time, the performance of the motor is determined by the quality of the ring magnet. Since ring magnets are manufactured by forming and sintering magnetic powders into a ring shape, the magnetic flux density is affected by the magnetic powder material composition, crystal grain size and density after sintering. Since this is a so-called pottery, defects are caused by various factors such as the state of the magnetic powder, temperature during sintering, and the degree of heat rotation in the furnace. For example, in the case of a four-pole motor, the motor is magnetized in the order of (1) S-pole, (1) N-pole, (2) S-pole, and (2) N-pole, but if a longitudinal crack occurs in the center of the (1) S-pole, a new S-pole and N-pole are generated in the (1) S-pole. A magnet has the physical characteristic of forming new magnetic poles at the cracked end, and as a result, a ring magnet with complex magnetic poles is formed instead of the four poles it should have, and the rotor does not rotate normally even if it is assembled in this state in a motor. Even if the crack is small and the rotor rotates, the imbalance in magnetic flux density makes precise control impossible. Furthermore, cracks so small that they are overlooked by visual inspection can cause defects that are difficult to identify.
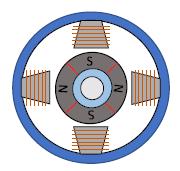
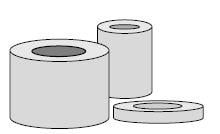
Fig.1: Structure of brushless motors and ring magnets
Therefore, it is essential to inspect the inner and outer surfaces of the ring for cracks prior to magnetization. Eddy current inspection is contactless and does not require any couple medium such as a liquid to perform the inspection. The depth and size of the cracks can be captured as electrical signals, and traceability can be established by storing the inspection data simultaneously, making it the most suitable method for efficient inspection of sintered materials.
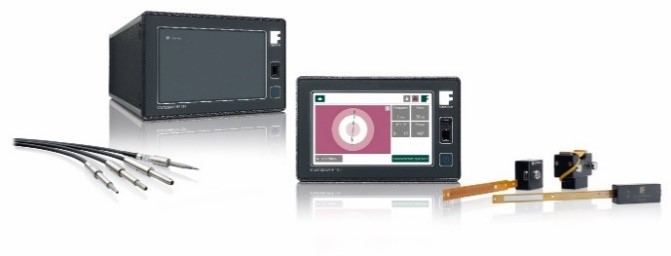
Fig. 2: STATOGRAPH CM / CM+ and different probes
The best performance is achieved by using FOERSTER‘s STATOGRAPH and special probes for this test.