Hardness testing - so that fasteners & screws deliver what they promise
Why should bolts and fasteners be tested for hardness?
Screws and fasteners such as bolts must hold components together securely under a wide range of mechanical loads. The environmental conditions place additional demands on the material properties, structure and surface condition. In addition, there are standards and regulations that screw manufacturers must take into account with their products. In addition to material mix-ups when the raw material is received, surface defect inspection for cracks plays an important role. The final product is then tested for strength, which is usually determined destructively on a selection of parts in a tensile testing machine. The bolts are sorted into property or safety classes with corresponding markings according to the standard. These markings are very extensive, as the many different types of bolts suggest. Structural steel screws, for example, are divided into strength classes according to tensile strength and yield strength with a uniform designation on the screw head or on the screw shaft. "M8.8" here denotes M = hex head bolt metric dimension, 8 x 100 = 800 MPa tensile strength and 8 x 8 x 100 = 640 MPa yield strength or "M12.9" would say 12 x 100 = 1200 MPa and 12 x 9 x 100 = 1080 MPa. These are two of the minimum requirements that have to be met and can be found in so-called screw fibers.
Since the tensile strength correlates positively with the hardness of the material (≥HV 10) and empirical conversion rules exist, e.g. according to EN ISO 18265, the hardness test is also repeatedly used for quality assessment for practical reasons. This is particularly important when a larger number of screws, bolts, etc. have to be inspected and/or the geometric dimensions are opposed to a tensile test. Although the classic Vickers, Brinell and Rockwell hardness test is more flexible, it usually requires complex surface processing or the bolt must be cut up and frequently embedded for the testing process. Attempts are being made to circumvent this additional work by using mobile hardness testing methods such as the UCI method (Ultrasonic Contact Impedance). However, there is no general statement on applicability here either. Due to the high variability in the characteristics of screws and bolts, tests on samples are highly recommended in advance. The situation becomes particularly volatile if, despite all precautionary measures, safety-relevant bolts are already installed in the vehicle or on the construction site, for example, and subsequent removal is very difficult. This is also where hardness measurement with UCI comes into play for confusion testing, as the measurement can simply be carried out directly on the installed part in any direction quickly and safely.
Click here to get more information about the UCI hardness testing method.
Hardness testing of fasteners & bolts: How is it done?
- What are the present solutions?
- Where do these approaches fall short?
- What are the challenges in hardness testing of screws and fasteners?
- What are limiting factors?
Questions upon questions we will answer:
Screws and bolts are manufactured optimized for the application. This includes surface coatings against corrosion or for optimum sliding properties and even local hardness or strength properties through thermal treatment. Thus, at predetermined points such as bolt head, shaft and end, the core hardness and surface hardness must be tested with defined test forces between HV 0.3 and HV 10. Accordingly, the hardness testing methods must be adjusted to these tasks. Before measuring the material, surface coatings must be removed. Measurements on the shaft are difficult for Vickers hardness testing because the surface usually must be ground flat to properly capture the diagonals of the indentation. The test location on the screw must be easily accessible, which often requires disassembly of the screw due to the complex setup of a testing machine. Finally, the screw must then also be correctly aligned (embedded and polished) in the case of a conical body, because otherwise, depending on the pitch, the optics cannot be focused well enough to evaluate the test indentation.
What are the hardness testing methods?
Depending on the requirements, various test methods are available. The most common are the following:
- Martens (universal hardness)
- Vickers (HV)
- Rockwell (HR)
- Brinell
- Knoop
- Shore
- Barcol
- Buchholz
One step ahead in testing fasteners & screws with UCI measuring technology?
Why or when and where is the UCI method better suited for hardness testing of bolts and fasteners?
The essence of UCI hardness testing is the measurement of the acoustic impedance of a body via the frequency shift of a rod vibrating in resonance with Vickers diamonds. The hardness of the material is determined from the frequency shift Δf at a certain predefined test force. Here, the Vickers hardness scale forms the reference for each material. The UCI devices are adjusted to materials with a modulus of elasticity of approx. 210 GPa and can be precisely set to the new task by means of a comparative measurement with a Vickers hardness testing device. This is needed only once because the setting data can be retrieved from the memory again in a reproducible manner.
SONODUR 3 and UCI measuring probes
Thus, screw testing with UCI is very easy and fast through one-time comparison with the Vickers scale. Since the UCI probes are pin-shaped with thin test tips (Φ 2.5 mm or especially Φ 1.7 mm), they are suited for hardness testing at hard-to-reach positions.
Nevertheless, the boundary conditions from the application of the UCI method must be observed at this point. The surface must be clean or polished, but not necessarily bright. In addition, the measurement location must be accessible for the probe tip. The component must be solid and decoupled from possible component resonances. Resonances can usually be recognized very well by strongly scattering and excessively high or much too low measured values, which are far outside the expected range.
Shafts can still be measured up to Φ 3 mm without special precautions according to standard DIN 50159-1. With test forces between HV 0.1 UCI (motor measuring probes) and HV 10 UCI (hand-held measuring probes), screws can be measured as a whole or also embedded, both manually and in a stand. Due to the rapidity of UCI measurement combined with its high precision, a large number of measurements are possible compared to classical methods. As a result, entire measurement series can provide a detailed picture of the treatment result achieved by scanning the shaft.
A suitable tool for hardness testing of screws and fasteners
SONODUR 3: Portable hardness testing for maximum flexibility and reliable results
Among the UCI hardness testers, the SONODUR 3 is predestined for difficult testing tasks. It currently has the widest range of probes and accessories in the market. Using the touch screen, extensive series of measurements can be quickly searched for faulty measurements and evaluated - all you have to do is tap "extreme values". SONODUR 3 will locate the suspicious measured value. In addition, both the test management (conversion tables, CAL adjustment function and penetration time) and the documentation possibilities (data formats CSV, .txt, HTML, wireless, USB, photo) form a strong argument for the use of SONODUR 3.
Discover the advantages of SONODUR 3!
Share this
You May Also Like
These Related Stories
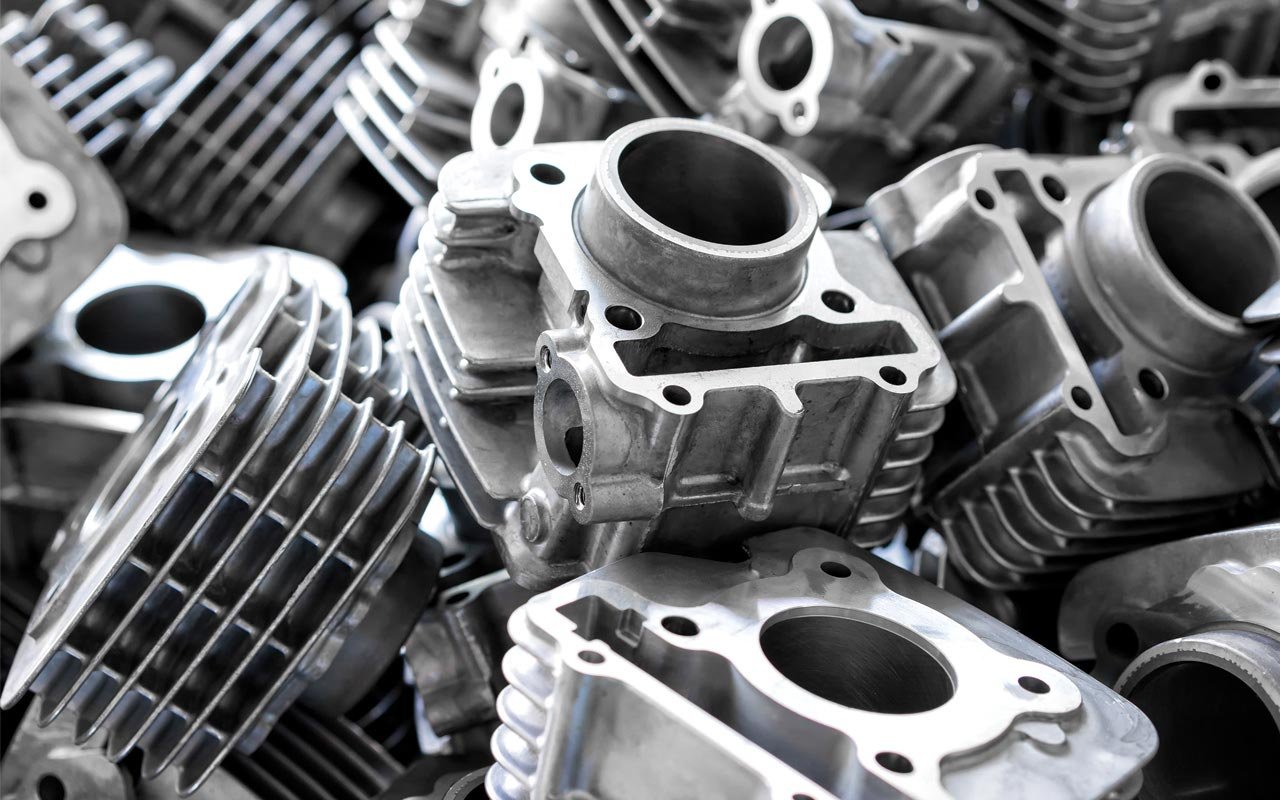
Mobile Vickers hardness testing with UCI to reduce the workload of test personnel
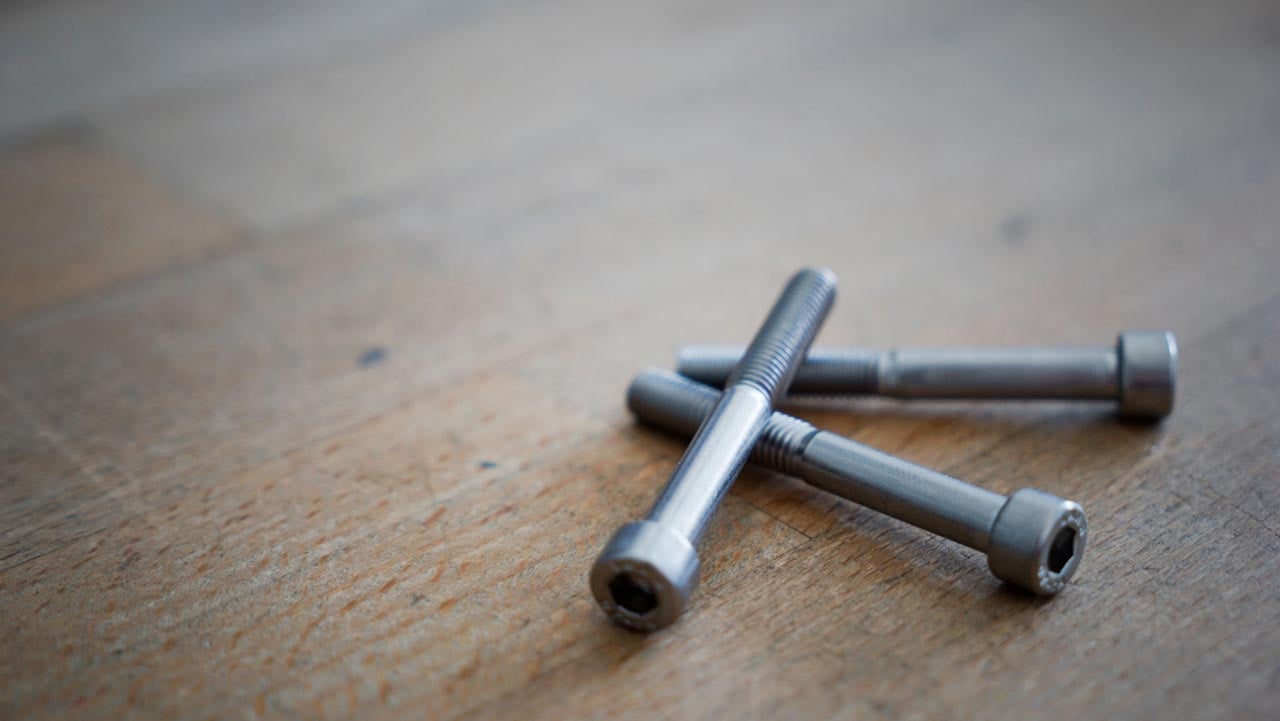
Fast UCI hardness measurement on screws and bolts: practical applications
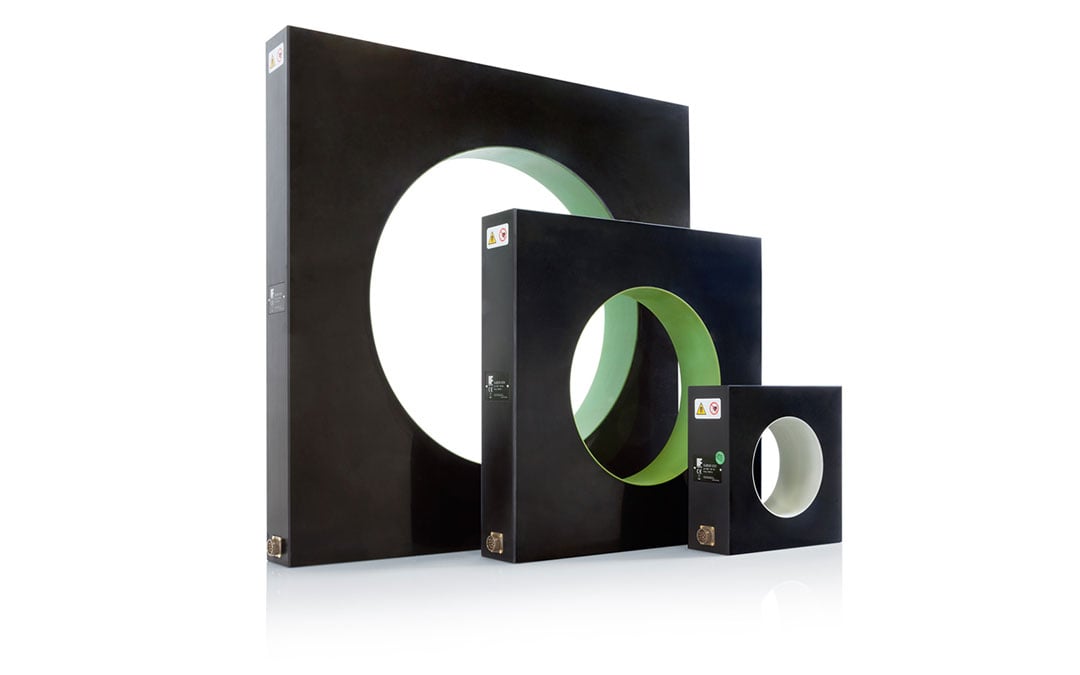