There are several ways to manufacture parts: forging, casting, cutting and powder metallurgy. In powder metallurgy, powder is compressed and sintered in a mold to produce parts. This method can be used to mass-produce parts with complex shapes and high precision requirements, and it is also more cost effective than other manufacturing methods because the production process can be shortened. This is why it is used for mechanical components and wear-resistant parts for automobiles. However, the quality, particle size, homogeneity, and mixture of different materials of the powder, as well as the temperature control during sintering and heat treatment, greatly affect the mechanical performance of the material.
If one of these mass-produced parts is defective and integrated into the final product, such as an automobile, it could cause serious problems. Therefore, magneto-inductive test instruments are used to control the quality of the parts produced. These instruments can immediately determine the quality of the parts by simply placing them in an encircling coil. The encircling coil contains an excitation coil as well as a receiver coil. When an electric current of a specific frequency is induced by the excitation coil into the material, a magnetic field is generated.
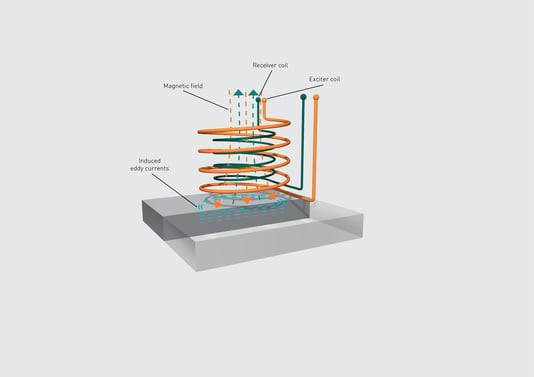
Fig.1: Operating principle of magneto-inductive testing
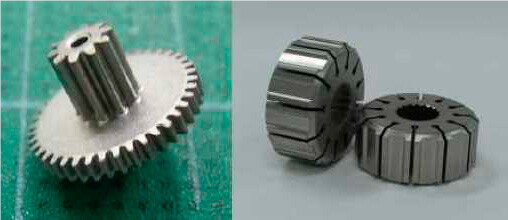
Fig. 2: Examples for sintered metallurgical parts
When a part is passed through the coil, eddy currents are induced. If the specified quality is not met due to material mix-up, incorrect sintering or heat treatment, etc., the eddy currents shift. This change received by the receiver coil, and the part is being rejected.
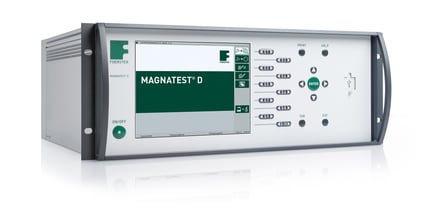
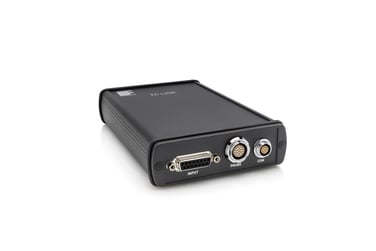
Fig. 3: MAGNATEST D, MAGNATEST TCL and encircling coils
For highest performance of the magneto-inductive testing, we recommend the MAGNATEST test instrument from FOERSTER in combination with an encircling coil. For further information please visit our homepage: foerstergroup.com