Pressure vessels hold gases or liquids at a pressure higher than atmospheric one. They are found in fire extinguishers as well as in avalanche airbags. In order to save weight, the wall thickness of pressure vessels is becoming smaller and smaller and thus more susceptible to cracking. Since a crack in the material can cause the container to burst and have catastrophic consequences, the pressure vessels are subject to the highest safety and quality requirements. FOERSTER supports quality control with non-destructive eddy current testing systems. These inspect the pressure vessels directly in the production process for surface defects such as cracks.
Fig. 1: Pressure vessel
The STATOGRAPH CM+ testing system is used in conjunction with a high-resolution eddy current probe for crack testing of the pressure vessels. Surface defects such as cracks disturb the uniform propagation of eddy currents in the material. These irregularities are detected by the probe and displayed as a signal. In addition, the surface can be displayed as a scan image by using the STATOVISION software.
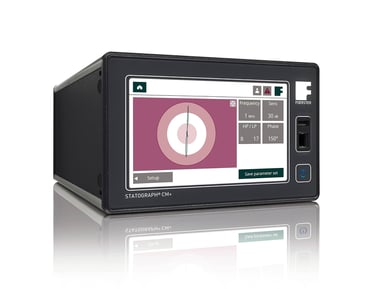
.jpg?width=408&height=288&name=Blog9(1).jpg)
Figure 1: STATOGRAPH CM+ & STATOVISION
To inspect the pressure vessel, it is clamped in a lathe and set in rotation. The eddy current probe is fixed and scans the rotating vessel. This allows the smallest cracks of 0.2 mm in length and 0.1 mm in depth to be reliably detected on the cylindrical surface with a signal-to-noise ratio of 4:1. For continuous quality assurance, the results can be documented and evaluated.
Fig. 3: Eddy current signal
Fig. 4: Surface scan with STATOVISION
For crack testing of pressure vessels, we recommend the STATOGRAPH CM+ testing system with a high-resolution eddy current probe. This ensures an automated and standardized inspection of the cylindrical surface of the pressure vessels. For further information, please visit our website at: foerstergroup.com