Effective mobile hardness testing for airline quality assurance
Safety requirements for materials used in aerospace construction and overhaul are evolving
The safety requirements in the aerospace industry require very strict standards for materials used. This includes the use of advanced composites and metal alloys that are lighter and stronger than traditional materials, as well as extensive testing and certification processes.
In addition, the use of 3D printing is becoming increasingly popular as it allows the production of complex parts with special shapes and geometries that are difficult to achieve with traditional manufacturing methods.
Materials such as carbon fibers, aluminum and titanium alloys form an important pillar in light metal construction for aircraft. They reduce the weight of the aircraft components while ensuring their resilience and durability.
Risks of lightweight components for aircraft construction
In aviation, components are exposed to the most extreme loads. The main risk associated with lightweight aircraft components is, they may not be as strong and durable as traditional materials. This could cause components to fail in flight, which could have catastrophic consequences. Also, lightweight components may be more susceptible to damage from extreme temperatures and high forces.
Lightweight components can be more expensive to manufacture, which could increase the cost of aircraft production. High demands are placed on the production processes here, which minimize rejects even for small component series
How can the risk of component failure be limited by non-destructive testing methods?
To mitigate these risks, it is important that components are thoroughly tested before they are used on an aircraft.
Non-destructive testing (NDT) methods can be used to limit the risk of component failure in aircraft with 100% testing. These methods include visual inspection, radiography, eddy current testing, ultrasonic testing, magnetic particle testing, and non-destructive hardness testing.
These tests can be used to detect faults and defects in materials and components that are not visible to the naked eye and that have arisen, for example, in the manufacturing process.
In addition, non-destructive testing can be used to monitor the condition of components over time. This means that signs of wear that could lead to failures are detected at an early stage.
Common fields of application for mobile hardness measurement in aviation
Portable hardness testers are widely used in aviation to test the hardness of materials used in aircraft components such as the landing gear, engine, and fuselage. For example, landing gear must meet or exceed specified design requirements and safety standards before being approved for use on an aircraft. This ensures the components are strong enough to withstand the rigors of flight. The test is used both in production and later in maintenance. The components to be tested can also vary greatly in size: from the smallest hinge elements to wheel rims or elements of the wings.
The mobile hardness testers can also be used to test the hardness of fasteners such as bolts and screws used to attach components to the aircraft in combination with conductivity testing to check the heat treatment condition on aluminum parts and special high-strength steel alloys to ensure they are suitable for use in aircraft components. Components with a wide variety of elastic properties often have to be measured in quick succession. In addition, it is advantageous if the device settings are already stored in the memory in advance so that they can then be pulled up easily for use. The mobile design also allows flexible and versatile use in goods receipt. This shows that the commitment extends from the manufacture of components to technical maintenance.
Mobile hardness measurement in aviation must fulfill stringent standards
The high standards placed on mobile hardness measurement in aviation include the need for accuracy, repeatability, and reliability that must be maintained over a long period. The operating staff knows the materials and the test task just as well as all the functions of the test device for the best possible calibration and application with verifiable results. The mobile hardness measurement is used to test the hardness of aircraft components that have to meet certain standards in order to be approved for use in aircraft. The test specifications are described in detail in the respective test specifications.
In addition, the mobile hardness measurement must be used in places that are inaccessible for classic applications. In this way, measuring points that are difficult to reach can be managed, or very large components or components that cannot be removed, which are tested in a wide variety of directions. Furthermore, one should be able to measure a wide range of hardness values, from soft to hard materials. The classic measurements in the laboratory are usually carried out on reference parts, the results of which are then used for mobile testing to validate the testing process.
After all, the mobile hardness measurement must be able to be carried out quickly and efficiently so that the components can be checked in good time for the shortest possible maintenance times.
Helpful methods of mobile hardness measurement for aviation
The UCI test method ( Ultrasonic Contact Impedance ) stands out as a method. It electronically evaluates a Vickers hardness test impression during the load within fractions of a second and displays it digitally. Due to the small indentation size and depth, the process is often considered non-destructive.
The great strength of the UCI measurement compared to the optical Vickers measurement on workpieces is the full material contact when determining the Vickers hardness. Measuring the diagonal lengths with the optical method is becoming more and more difficult, especially with smaller measuring indentations (low measuring force, high hardness).
The UCI hardness measurement can be adjusted very precisely to the measurement task relative to the classic Vickers hardness measurement. It becomes the "extended arm" of the classic laboratory measurement technology in production or the maintenance area. A device adjustment to materials with a different modulus of elasticity (copper, aluminum, chromium, etc.) is easily possible via a comparison measurement with a classic hardness measuring machine (HV, HRC, HB).
Where can such UCI solutions for mobile hardness measurement be found?
With the SONODUR 3, FOERSTER offers a mobile UCI hardness tester that meets the diverse requirements of flexible use with a high degree of accuracy, repeatability, and reliability at the same time. The device can be used with the widest range of probes with the standard test forces of 10 N, 30 N, 49 N, and 98 N (hand-held measuring probes) and 1 N, 3 N, and 8.6 N (motor measuring probes). Classic manual measuring probes are available with different probe tip designs to reach deeper measuring points such as in boreholes or in the tooth base of a gear wheel. Even with high levels of hardness, motorized probes provide maximum reproducibility of the measured values thanks to their uniform application of force and simple use with special probe feet on a level and curved surface. Using a steel support tube, the tooth flanks on gears can also be reliably measured with small test forces. Tripod probes round off the solutions with their play-free guidance of hand-held measuring probes, which allows minimization of operator dependency due to their guided operation.
Share this
You May Also Like
These Related Stories
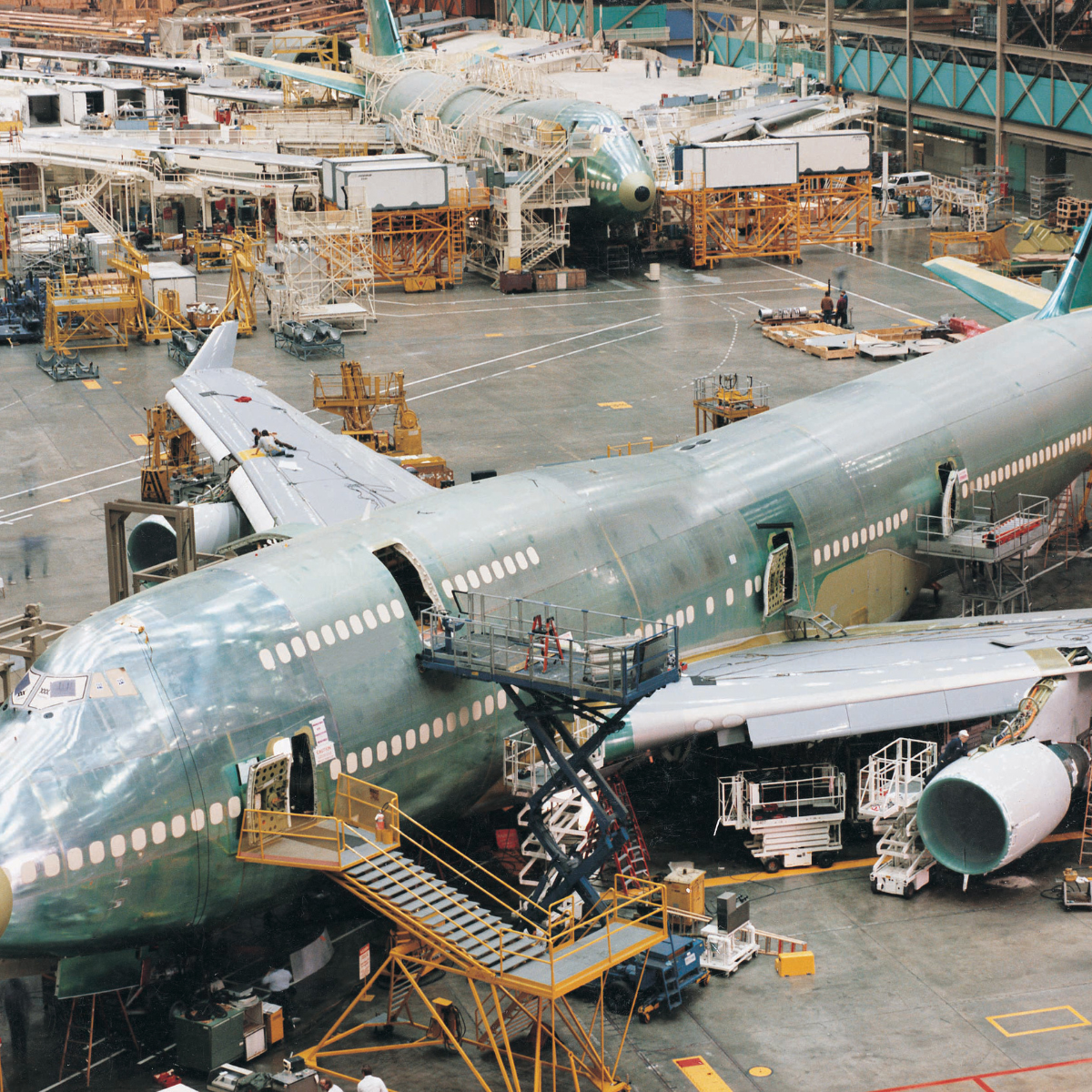
Solving Real-World Inspection Problems with Mobile NDT Solutions
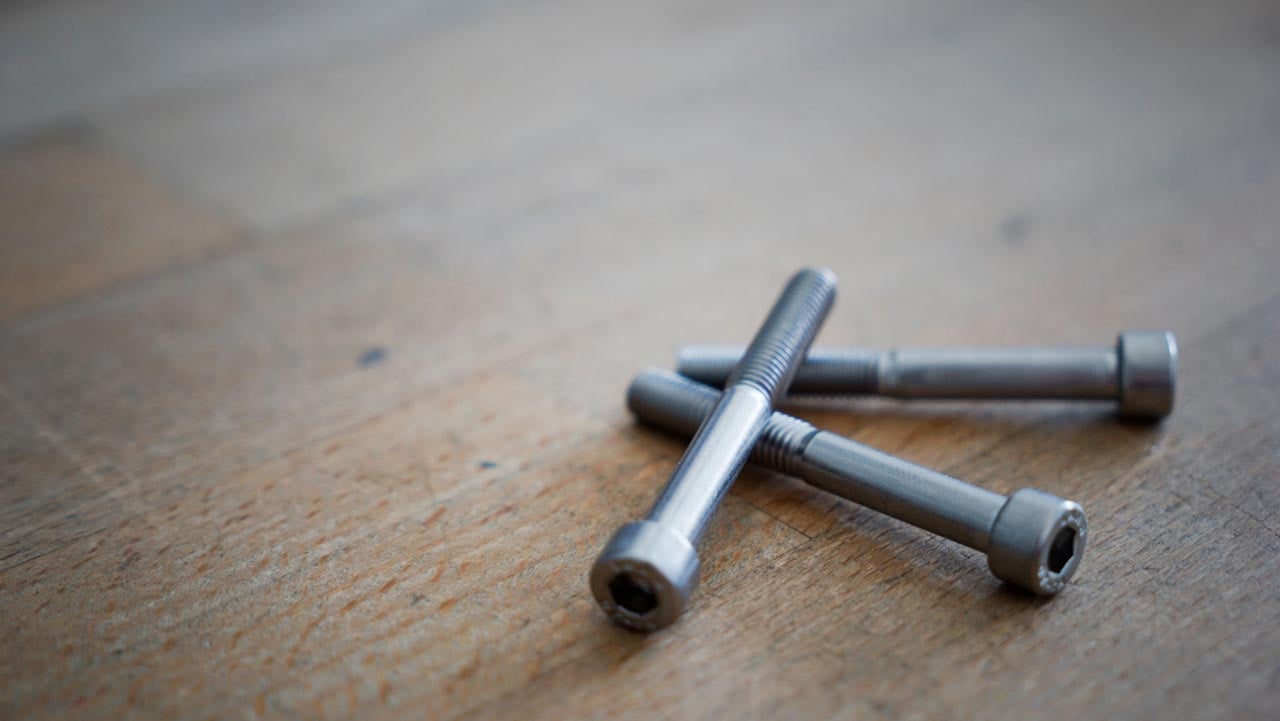
Fast UCI hardness measurement on screws and bolts: practical applications
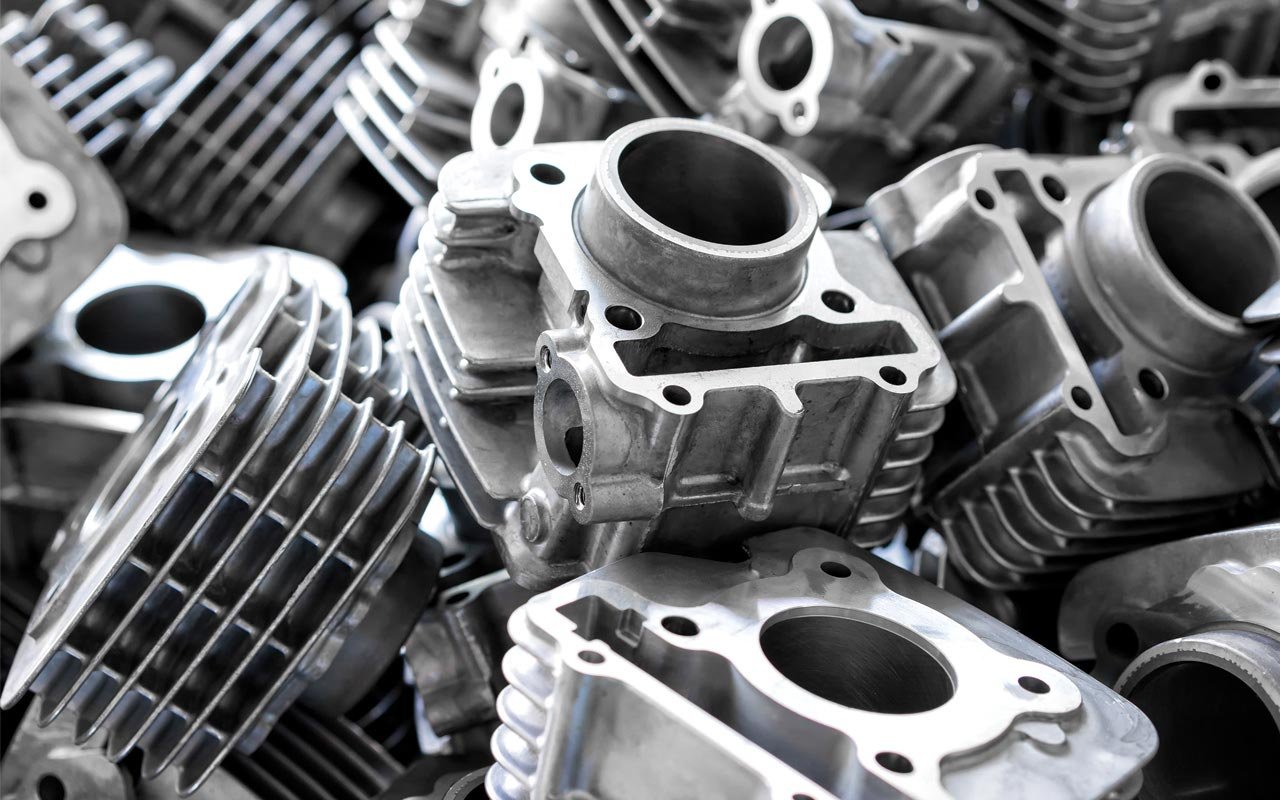