Crack testing: How does an eddy current test instrument work?
Eddy current testing is a non-destructive method for inspecting conductive, i.e. metallic, surfaces for defects such as cracks or inclusions.
For crack testing, the test part is mechanically rotated and scanned by a stationary probe with two cast-in coils. Alternatively, a rotating probe scans the stationary test part. While one coil serves as the transmitter coil, the other is used as the receiver coil. A defined alternating current is applied to the transmitter coil. The alternating current flowing through the coil generates a magnetic field, which in turn induces an eddy current in the conductive test part. Analogous to this technique, the voltage generated by the eddy current can also be measured in reverse with a receiver coil.
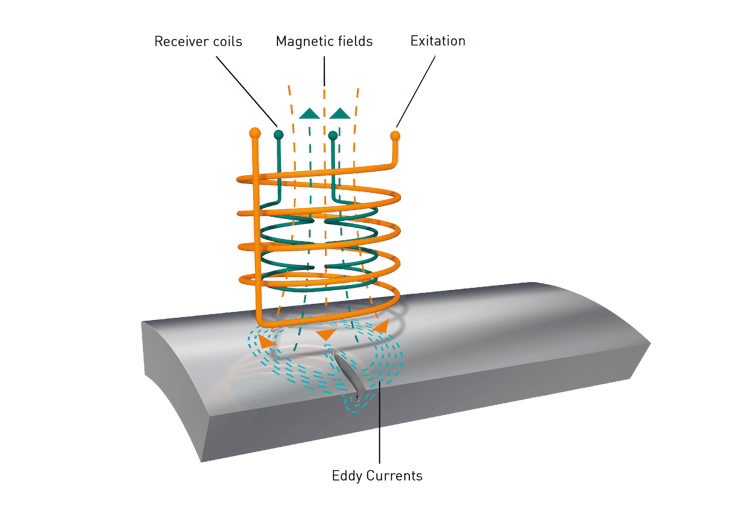
These high-frequency electromagnetic interactions are used for crack testing. An eddy current test instrument compares the transmitted signal with the received signal in order to draw conclusions about the surface of the test object. For example, if there is a crack on the surface of the test part, the eddy currents propagate differently. This leads to a change in phase position and amplitude. It is precisely this change that the test instrument then graphically displays as a so-called eddy current signal.
Learn more about the advantages of eddy current instruments for crack detection.
This method can be used above all to detect cracks or pores close to the surface. The penetration depth of the eddy current is dependent on the
- Electrical conductivity
- Magnetic permeability
- Test frequency
The electrical conductivity and the magnetic permeability are specified by the test object. The test frequency, however, can be actively influenced.
The lower the test frequency, the higher the penetration depth. Therefore, high frequencies are used for the detection of defects close to the surface and low frequencies for deeper defects. As the frequency is reduced, the sensitivity decreases, i.e. the defect resolution becomes much lower for deeper defects. Therefore, there is an optimal test frequency for each test to find the balance between penetration depth and sensitivity.
Important influencing factor for crack testing: the surface quality
Other properties also play an important role. First and foremost, the surface quality of the test object. The eddy current testing is a contact-free type of testing, i.e. the probe does not have to touch the component to be tested, but only has to be positioned reproducibly at a small distance. The finer the surface (e.g. polished), the closer the probe can be moved to achieve a higher defect resolution. With rough surfaces, the probe element can be damaged if the sensor comes too close to the surface of the test part and is touched by unevenness.
Basically, it should be noted that every surface generates a so-called background noise. For reliable and reproducible detection of defects, the generated error signal should be 3x higher than the background noise. This ratio is called Signal-to-Noise Ratio (SNR). For the reasons mentioned above, it is easier to achieve an SNR of 3:1 or higher for thin surfaces.
Distance compensation and other important parameters for optimal crack testing
However, not only the surface condition influences the distance of the probe to the component, but also the symmetrical rotation is a decisive factor. With an improper rotation, it can happen that the distance is not always constant over a 360° rotation, but varies. This is compensated by the so-called distance compensation. Here, an additional distance channel permanently measures the signal strength and can thus draw conclusions about the distance of the probe to the test part. This information is incorporated into the crack signal by an algorithm to generate identical amplitudes for identical cracks, regardless of the distance of the probe to the test object.
However, with modern eddy current testing instruments such as the STATOGRAPH CM / CM+ from FOERSTER, it is not only possible to set the frequency and the distance compensation, but also the parameters:
- Sensitivity
- Bandpass (highpass / lowpass)
- Phase position
With the sensitivity (test sensitivity), the amplitude of the error signal can be increased manually in order to bring an error signal safely above the threshold value. The threshold value defines when a recorded eddy current signal is too high and the component is declared not OK. The sensitivity is set and checked using artificial or natural reference errors prior to testing. By means of suitable interfaces, e.g. PROFINET, this value can be transferred to a PLC, which in turn sorts the components into good and bad parts. Other interfaces, such as digital inputs and outputs, also tell the tester when to start a test (external trigger) or how long to test.
With the bandpass, interfering secondary frequencies can be filtered out so that false indications in the error signal and thus pseudo rejection will not occur.
The phase position works in a similar way. Here, signals can be rotated in their phase position in order to evaluate only the relevant error signal by means of threshold and to neglect other irrelevant signals.
It is always important that an eddy current testing instrument check against reference errors. This means that an adjustment takes place. Depending on whether the previously defined threshold value is exceeded during this adjustment, the test parts are grouped into OK and not OK. With high-quality instruments such as the STATOGRAPH CM / CM+ from FOERSTER, various threshold values and evaluation methods can be selected. For example, a message can be generated at an early stage if the components develop a tendency towards the NOK threshold. With the help of this information, conclusions can be drawn about the entire manufacturing process at an early stage and interventions can be made - completely in line with Industry 4.0.
FOERSTER has extensively developed the STATOGRAPH to make testing even simpler and more intuitive.
Share this
You May Also Like
These Related Stories
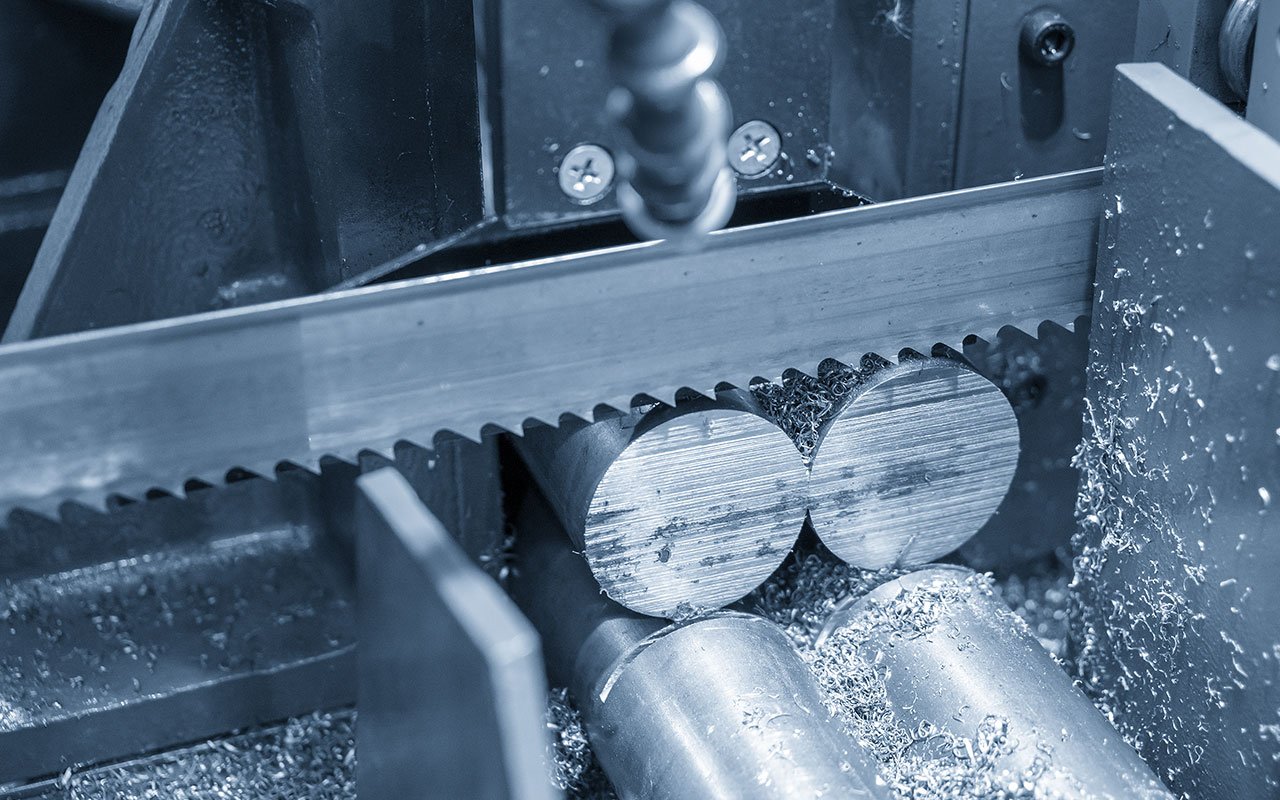
The smartest method to improve crack testing on saw bands
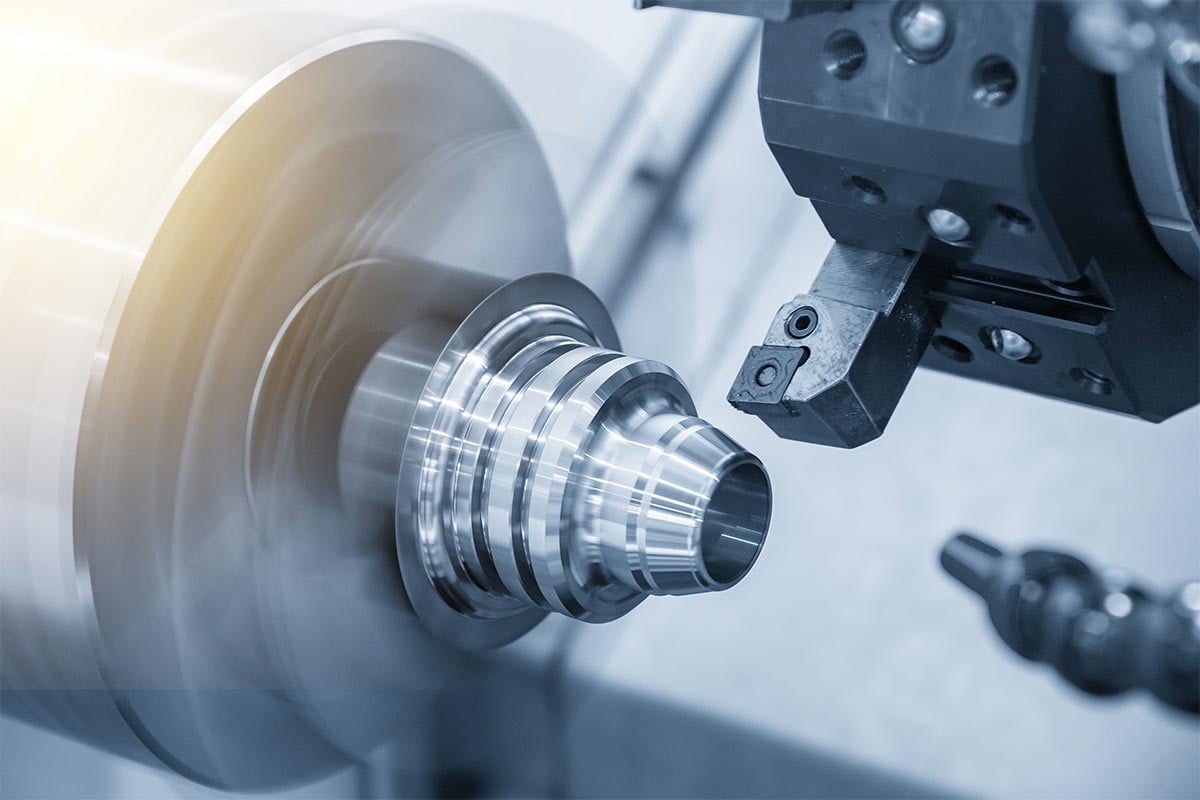
Crack testing: How do I set my filters and frequencies correctly?
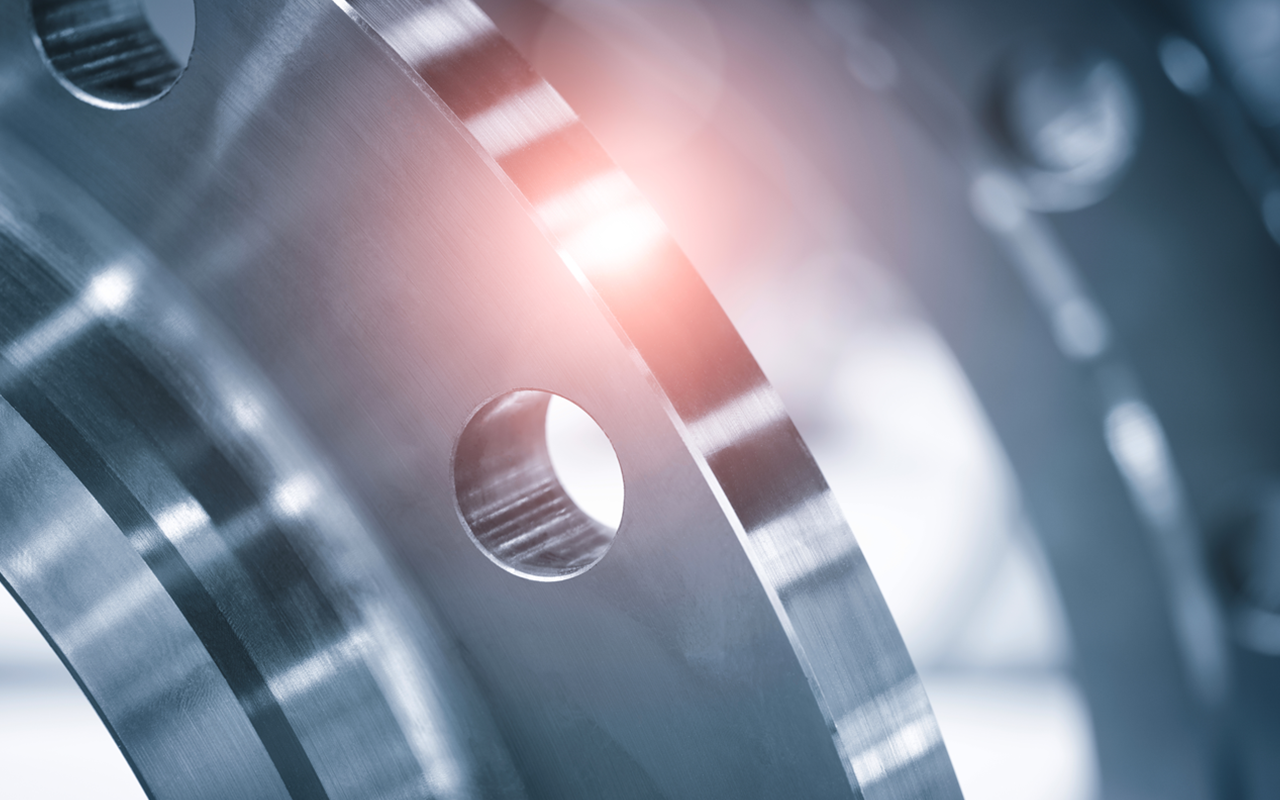