What good is the best testing equipment if you don't know what to test?
This sounds strange at first, but many customers feel this way. They have already decided for themselves that eddy current testing is the preferred system for their specific application. The reasons are that eddy current testing offers high reliability combined with a fast cycle time and low costs compared to other testing methods. Furthermore, the defect specifications or the potential natural flaws to be found are known.
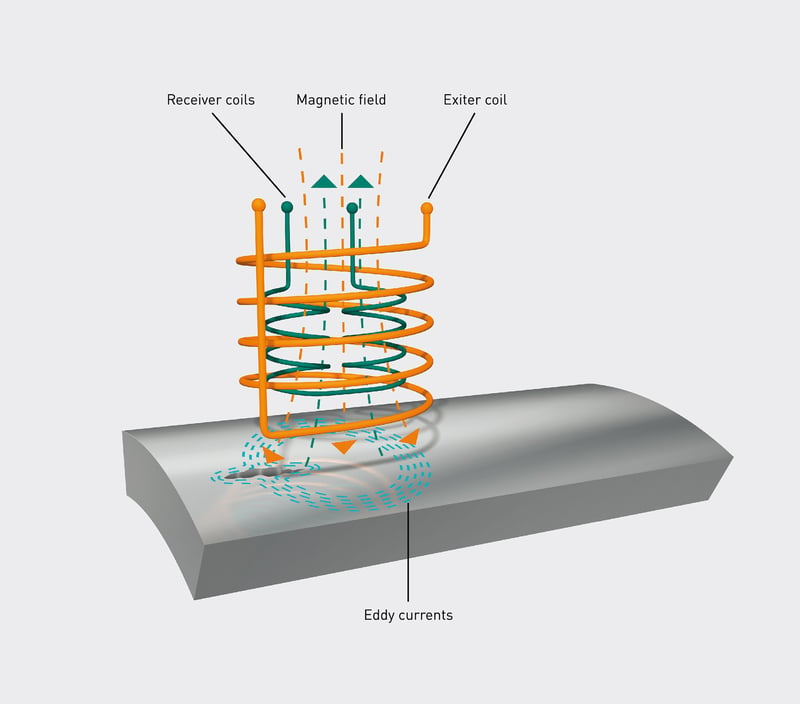
Figure 1: Eddy current testing
How does the eddy current method work?
Depending on the material and surface condition of the metal component to be tested, cracks of 100 µm depth and sometimes even less can be detected. For this purpose , a probe with cast-in primary and secondary windings is moved over the component without contact and differences between the transmitted and received signals are evaluated. These differences are caused by the fact that the eddy current propagates differently in the case of surface defects. This results in a change in phase and amplitude with respect to the output signal, which is significantly different from the background noise. This ratio between the background signal and the flaw signal is also called the "signal-to-noise ratio" or SNR for short. If the flaw signal exceeds a certain, individually defined threshold, a command to reject the component can be sent to PLC. Suitable procedures are then used to reject the faulty part so that it is not available for the further production process. This prevents subsequent failures of the product.
Accordingly, eddy current testing is a comparative method. It detects defects that have previously been defined by a reference defect and the setting of a certain threshold for sorting out. These reference defects are essential both for the basic setting of the test instrument and for regular checks in the production process. For this purpose, a master with a reference defect can be deliberately introduced into the test system at regular intervals to verify that the sorting of OK and NOK parts functions without errors.
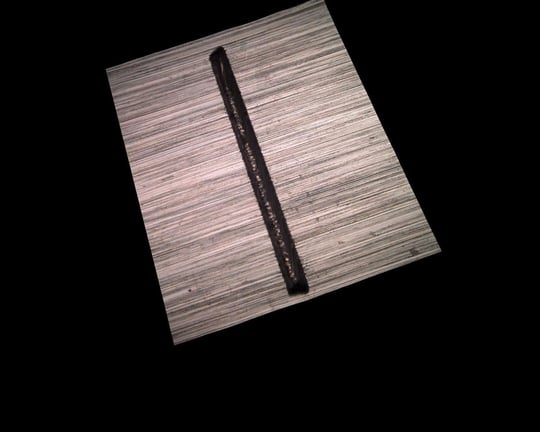
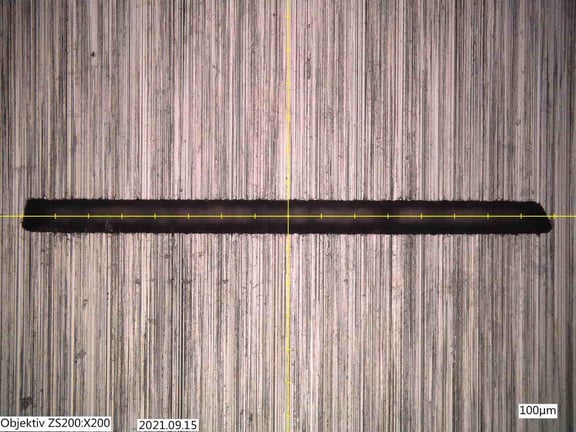
Figure 2: Artificial defects
Artificial test defects - use, advantages and production
For the reasons mentioned above, the natural flaws mentioned at the beginning are usually replaced by an artificial, reproducible error, that is modeled on the natural flaw. This has the great advantage that the defect can be introduced exactly with the desired dimensions and copied as often as needed. Natural flaws in comparison, although theoretically known, cannot be created at the push of a button, let alone reproduced. For this reason, it is always advisable to resort to artificial defects with very small tolerances.
Such defects can be created by FOERSTER's in-house specialists in any number. Multiple defects, e.g. with different depths or orientations per part are also possible. Simply let us know your requirements for your calibration parts and we will prepare a professional quotation for the desired defects on this part. Based on this quotation you can send us your components and get back your calibration parts with eroded defects and corresponding certificates in the given delivery time. Or we can go one step further and perform application tests at our premises upon request. Thereby we verify with which probes, settings, process capability and cycle time these defects can be detected reproducibly. In this way, you can achieve the best result for your inspection tasks and reliably sort out defective parts as well as avoid pseudo defects. This means avoiding unnecessarily sorted out good parts and checking the process at any time with corresponding masters or calibrated parts.