¿De qué sirve el mejor equipo de pruebas si no sabes qué probar?
Esto suena extraño al principio, pero muchos clientes sienten de esta manera. Ellos ya han decidido por sí mismos que las pruebas de corrientes inducida son el sistema preferido para su aplicación específica. Las razones son que las pruebas de corrientes inducida ofrecen una alta confiabilidad combinada con un ciclo de tiempo rápido y costos bajos en comparación con otros métodos de prueba. Además, las especificaciones de defectos o las posibles imperfecciones naturales que se pueden encontrar son conocidas.
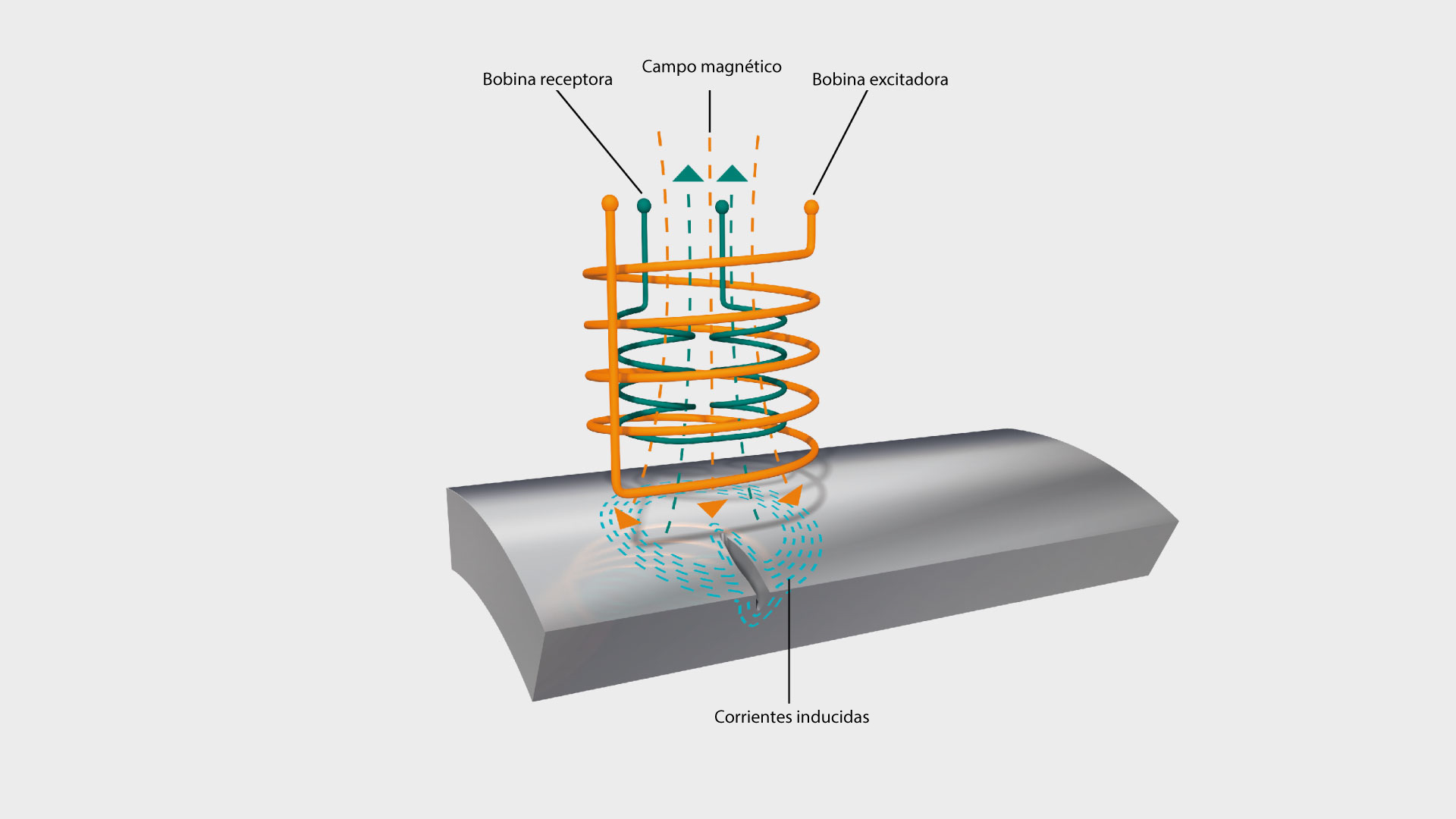
Figura 1: Pruebas de corrientes inducidas
¿Cómo funciona el método de corrientes inducidas?
Dependiendo del material y la condición de la superficie del componente de metal a ser probado, se pueden detectar grietas de 100 µm de profundidad, e incluso menos. Para ello, se mueve una sonda con bobinados primarios y secundarios incrustados sobre el componente sin contacto y se evalúan las diferencias entre las señales transmitidas y recibidas. Estas diferencias son causadas por el hecho de que la corriente inducida se propaga de manera diferente en el caso de defectos superficiales. Esto resulta en un cambio en la fase y la amplitud con respecto a la señal de salida, que es significativamente diferente del ruido de fondo. Esta relación entre la señal de fondo y la señal de defecto también se llama "relación señal-ruido" o SNR en breve. Si la señal de defecto supera un umbral específico definido individualmente, se puede enviar una orden para rechazar el componente al PLC. Se utilizan procedimientos adecuados para rechazar la parte defectuosa de manera que no esté disponible para el proceso de producción posterior. Esto evita fallos posteriores del producto.
Por lo tanto, las pruebas de corrientes inducidas son un método comparativo. Detecta defectos que previamente han sido definidos por un defecto de referencia y la configuración de un cierto umbral para su eliminación. Estos defectos de referencia son esenciales tanto para la configuración básica del instrumento de prueba como para las comprobaciones regulares en el proceso de producción. Para ello, un patrón con un defecto de referencia puede ser introducido deliberadamente en el sistema de prueba a intervalos regulares para verificar que la clasificación de piezas OK y NOK funcione sin errores.
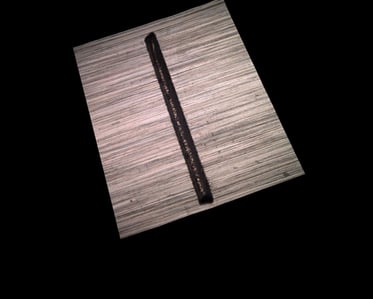
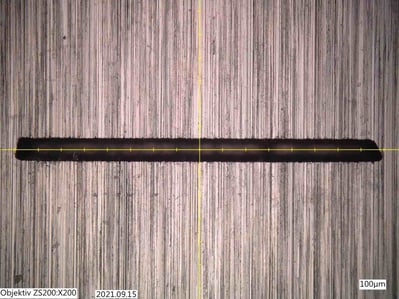
Figura 2: Defectos artificiales
Defectos de prueba artificiales: uso, ventajas y producción
Por las razones mencionadas anteriormente, las imperfecciones naturales mencionadas al principio suelen ser reemplazadas por un error artificial y reproducible, que está modelado en la imperfección natural. Esto tiene la gran ventaja de que el defecto puede ser introducido exactamente con las dimensiones deseadas y copiado tantas veces como sea necesario. Las imperfecciones naturales, en comparación, aunque teóricamente conocidas, no se pueden crear con solo apretar un botón, y mucho menos reproducirlas. Por esta razón, siempre es recomendable recurrir a defectos artificiales con tolerancias muy pequeñas.
Tales defectos pueden ser creados por los especialistas internos de FOERSTER en cualquier cantidad. También son posibles múltiples defectos, por ejemplo, con diferentes profundidades u orientaciones por pieza. Simplemente avísanos tus requerimientos para tus piezas de calibración y te prepararemos un presupuesto profesional para los defectos deseados en esta pieza. Basado en este presupuesto, puedes enviarnos tus componentes y recibirás tus piezas de calibración con defectos erosionados y certificados correspondientes en el plazo de entrega indicado. O podemos ir un paso más allá y realizar pruebas de aplicación en nuestras instalaciones bajo pedido. De esta manera, verificamos con qué sondas, configuraciones, capacidad de proceso y ciclo de tiempo estos defectos pueden ser detectados de manera reproducible. De esta forma, puedes obtener el mejor resultado para tus tareas de inspección y clasificar de manera confiable las partes defectuosas y evitar pseudodefectos. Esto significa evitar que las partes buenas sean innecesariamente desechadas y verificar el proceso en cualquier momento con maestros o partes calibradas correspondientes.