Measuring conductivity in aircraft components to address temperature-related structural issues
Due to exposure to extreme temperatures, especially near turbines or during sudden lightning strikes, the material composition can deteriorate. This exposure can result in changes to the material's properties, such as its electrical conductivity. The SIGMATEST device helps measure the conductivity in specific locations or parts, allowing for the identification and replacement of deteriorated components.
Challenges in aviation: Extreme temperatures and structural integrity
In the dynamic world of aviation, ensuring that aircraft are not only efficient but also safe is essential. However, this safety is often threatened by a persistent challenge: extreme temperatures. Particularly near turbines or during sudden lightning strikes, temperatures can often exceed tolerable limits. These extreme heat conditions can have devastating effects on the structural integrity of aircraft, especially on the aluminum components that form the mainstay of the aircraft structure.
The consequences are serious: prolonged exposure to extreme temperatures can cause aluminum to lose its structural strength, endangering the safety of the aircraft. Therefore, addressing these temperature fluctuations is an urgent challenge to ensure the safety of passengers and crew.
Only through a robust and resilient structure can aircraft withstand the rigors of flight operations and ensure the protection of their occupants. It is of utmost importance to address the problem of extreme temperatures and their impact on structural safety with an appropriate approach.
Material properties and their changes at high temperatures
When considering the effects of extreme temperatures on the structural safety of aircraft, it is essential to understand the changes in material properties that can occur at high temperatures. Heat can induce various physical changes in materials, including a significant change in their electrical conductivity. These changes not only indicate the thermal stress to which the material has been exposed but can also serve as precursors to structural damage that could compromise the aircraft's safety.
To effectively assess the structural integrity of aircraft and ensure that they can withstand the rigors of flight operations, strict test specifications are crucial. These specifications are defined by aircraft manufacturers and include precise test points distributed along the aircraft structure, as well as predefined electrical conductivity values that serve as references.
By systematically checking the electrical conductivity at these predefined test points, maintenance teams can identify potential structural issues early and take appropriate measures to ensure the safety of the aircraft. If the measured conductivity is outside the defined tolerance limits, immediate actions such as repair or replacement are required to restore and ensure the structural integrity of the aircraft.
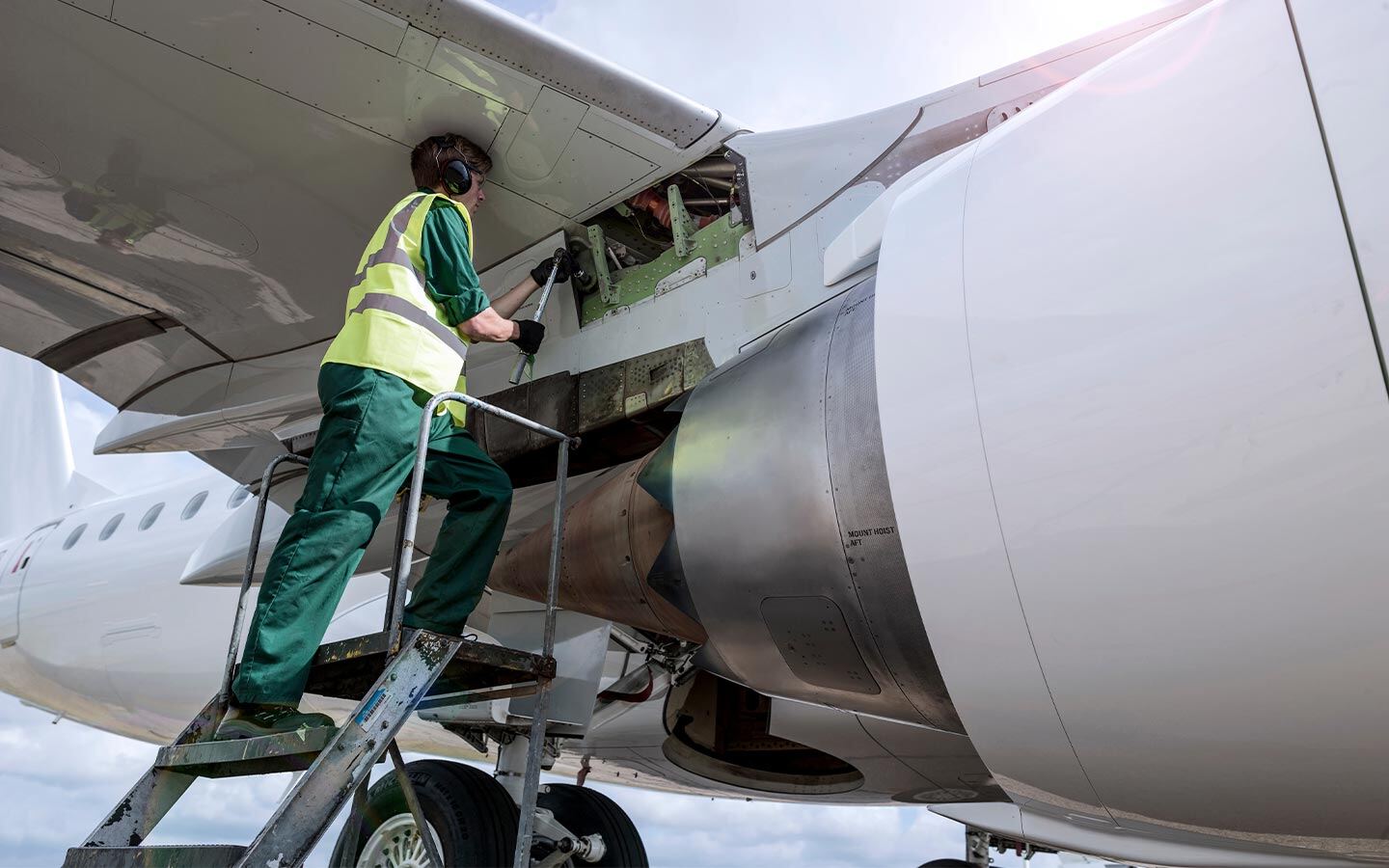
Solution Approach: SIGMATEST 2.070 for Precise Conductivity Measurements
An instrument that has proven extremely useful for precisely measuring the electrical conductivity of aircraft components is the SIGMATEST 2.070. With its user-friendly handling, this state-of-the-art conductivity testing device allows operators to check the predefined test points quickly and efficiently for their electrical conductivity. The versatility of the SIGMATEST 2.070 is also evident in its various probes with different probe heads. These have diameters of 5 mm, 8 mm, or 14 mm, allowing even hard-to-reach test points to be easily accessed and tested.
Addressing problems caused by extreme temperatures requires a holistic approach that considers various aspects of aircraft design and maintenance. By using advanced technologies, adhering to strict test protocols, and implementing proactive maintenance strategies, the aerospace industry can significantly improve the safety and reliability of aircraft operations. Such a comprehensive approach helps identify and mitigate potential risks early while maintaining the efficiency and cost-effectiveness of aircraft operations.
Thanks to years of close collaboration with leading companies in the aerospace industry, FOERSTER has extensive expertise and broad know-how in dealing with temperature-related structural issues in aircraft. Our commitment to the highest standards and innovative solutions has established us as a trusted partner in this field. We are ready to answer any questions and use our knowledge and experience to contribute to the safety and efficiency of air travel.
Conclusion
In summary, protecting airplanes from the effects of extreme temperatures is crucial for maintaining the safety of air travel. High temperatures can weaken airplane components, especially those made of aluminum, and alter their electrical conductivity. By following strict testing protocols, using advanced tools like the SIGMATEST 2.070 for accurate conductivity measurements, and being proactive with maintenance, we can mitigate the risks associated with extreme temperatures.
It's essential to take a comprehensive approach and use intelligent methods to detect and address problems before they become dangerous. By working together, embracing innovation, and striving for the highest standards, we can make air travel even safer for everyone. FOERSTER is here to assist with our expertise and tools. Let's continue to collaborate to ensure flying remains as safe and smooth as possible.
Share this
You May Also Like
These Related Stories
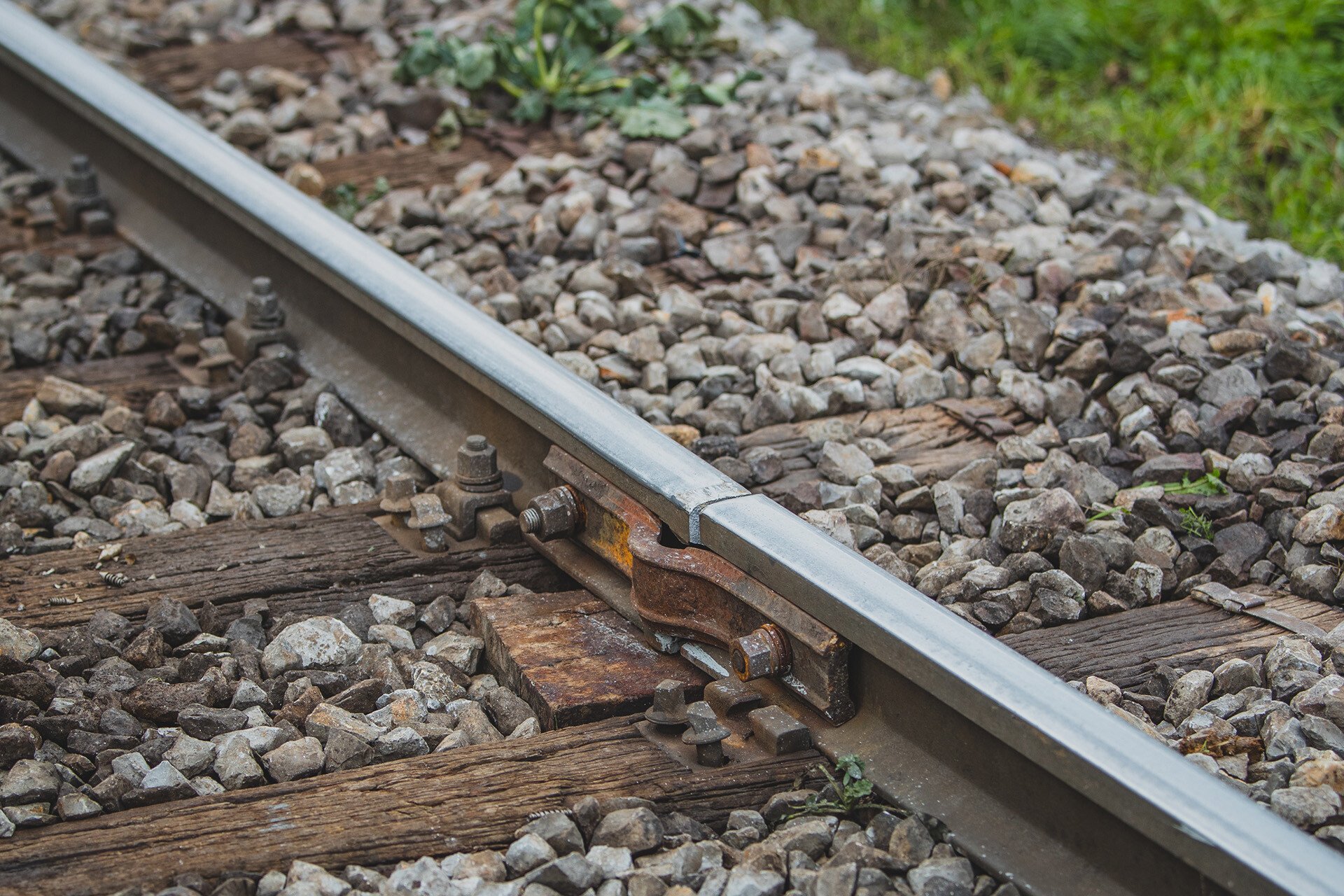
Portable Precision for Reliable Crack Detection
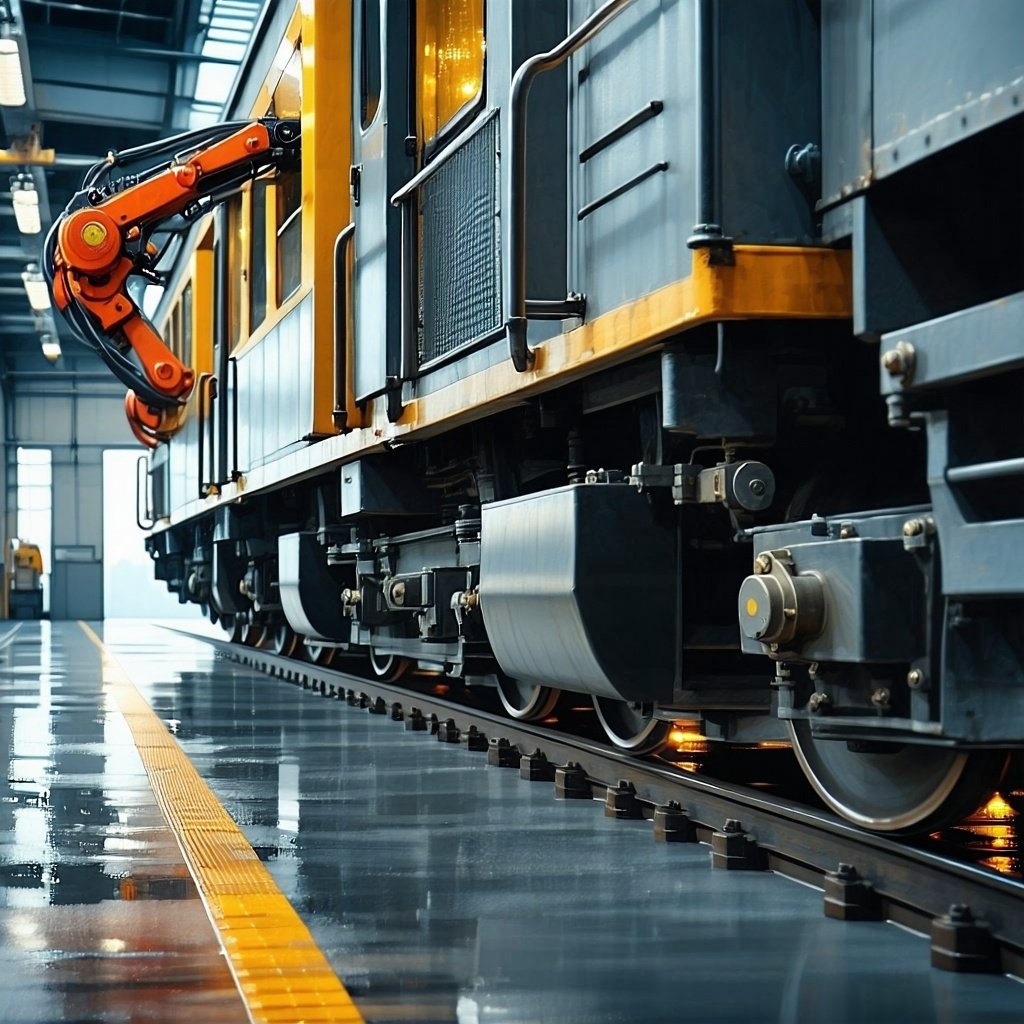
Advanced Eddy Current Testing for Freight Wagon Wheels
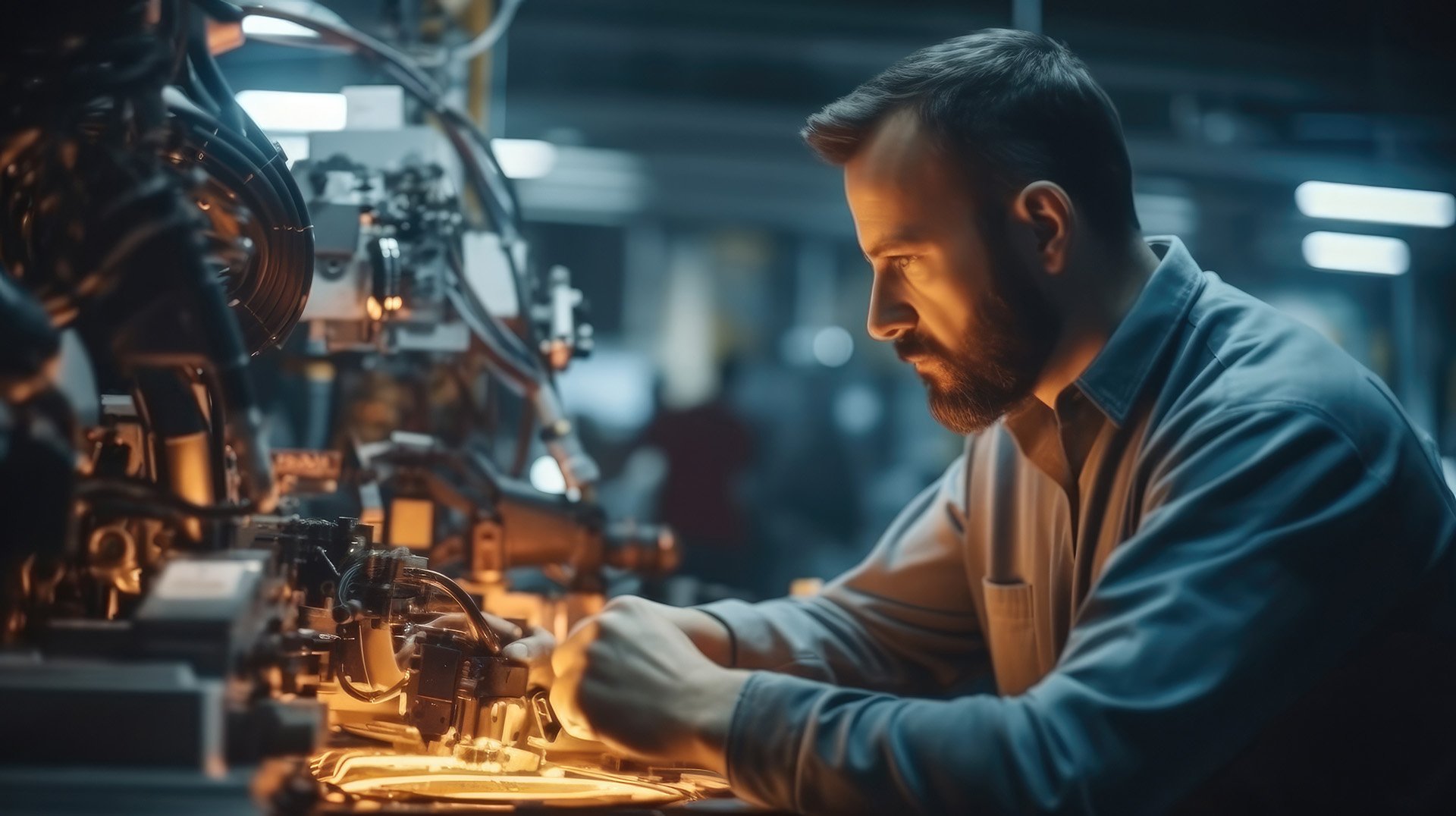