Why Final-Stage Component Testing is Your Best Quality Assurance Tool
In today’s manufacturing world, final-stage quality assurance isn’t just a checkpoint—it’s a competitive edge. Whether you are producing drive system components for the automotive industry or fabricating life-critical medical devices, delivering defect-free parts at the end of the process is essential. That is where component testing plays a key role.
Why Non-Destructive Testing of Finished Components Matters
Material testing early in the production process is standard practice, but by the time a component reaches its finished form, new risks emerge. Defects introduced during forming, machining, or assembly can compromise performance, safety, and compliance. If missed, they can lead to recalls, warranty claims, or worse—product failure in the field.
The automotive, aerospace, medical devices, and industrial tooling industries must rely on high-precision non-destructive testing (NDT) throughout the production process, especially at the final stage. It is the last line of defense before a part goes out the door and the best way to ensure your product—and your brand—holds up under pressure.
When Simplicity Falls Short
Some inspection systems are marketed as “simple” to use, often relying on a single “good part” for calibration. While this can make setup feel approachable for non-technical operators, it introduces risk. If that one part isn’t truly representative, the whole inspection process can fall short.
We take a different view. Simplicity matters—but not at the expense of reliability. Our systems are designed to be user-friendly without cutting corners, backed by hands-on training and support to make sure every setup is done right.
How Our Component Testing Solutions Deliver Value
The FOERSTER Component Testing (CT) team delivers precision testing systems built for real-world manufacturing and lab environments. Our systems are trusted by engineers, operators, and quality managers because they offer flexibility, repeatability, and long-term reliability.
Here is how we stand out:
- U.S.-Based Service and Support: All installation, training, and ongoing service support happen right here in the U.S. by our expert U.S. team. This means faster turnaround times, making sure you have what you need when you need it.
- Application Testing and Turnkey System Integration: Our Ohio facility builds custom turnkey component testing systems and conducts real-world application studies. You can bring your parts, see our systems in action, and make informed decisions with confidence.
- Complete NDT Solutions: While we’re known for eddy current inspection, our automated systems also incorporate dimensional gauging, vision systems, and other NDT techniques to meet a wide range of quality control needs.
- 100% Inspection Capability: Unlike sample-based inspection, our systems support inline 100% inspection, which is essential for traceability, compliance, and end-use performance assurance. There is no cycle time requirement that our team cannot handle.
- Making Subjective Tests Objective: Let’s face it, humans make mistakes. The days of relying on subjective human judgments to determine if a component is within specification no longer suffice for safety-critical components. Our automated solutions take these pass/fail decisions out of the hands of your operators.
Next Steps for Quality and Engineering Teams
- Evaluate Your Current Workflow: Are your inspection processes aligned with today’s quality and compliance demands? If not, we can help you identify areas of improvement.
- Leverage Operator and Engineer Feedback: NDT technicians and engineers can highlight pain points that impact productivity. We take that feedback and incorporate it into our solutions.
- Visit Our Salem Facility: See firsthand how our systems work with your actual part. It’s the most reliable way to validate fit and function before you invest in our products.
Partner with Experts Who Understand Critical Component Inspection
When the stakes are high and the tolerances are tight, you need more than a generic inspection system. You need a team that understands your application, your quality standards, and your pressure to deliver. Our Component Team delivers on this promise every day and has been doing so for 75+ years.
Share this
You May Also Like
These Related Stories
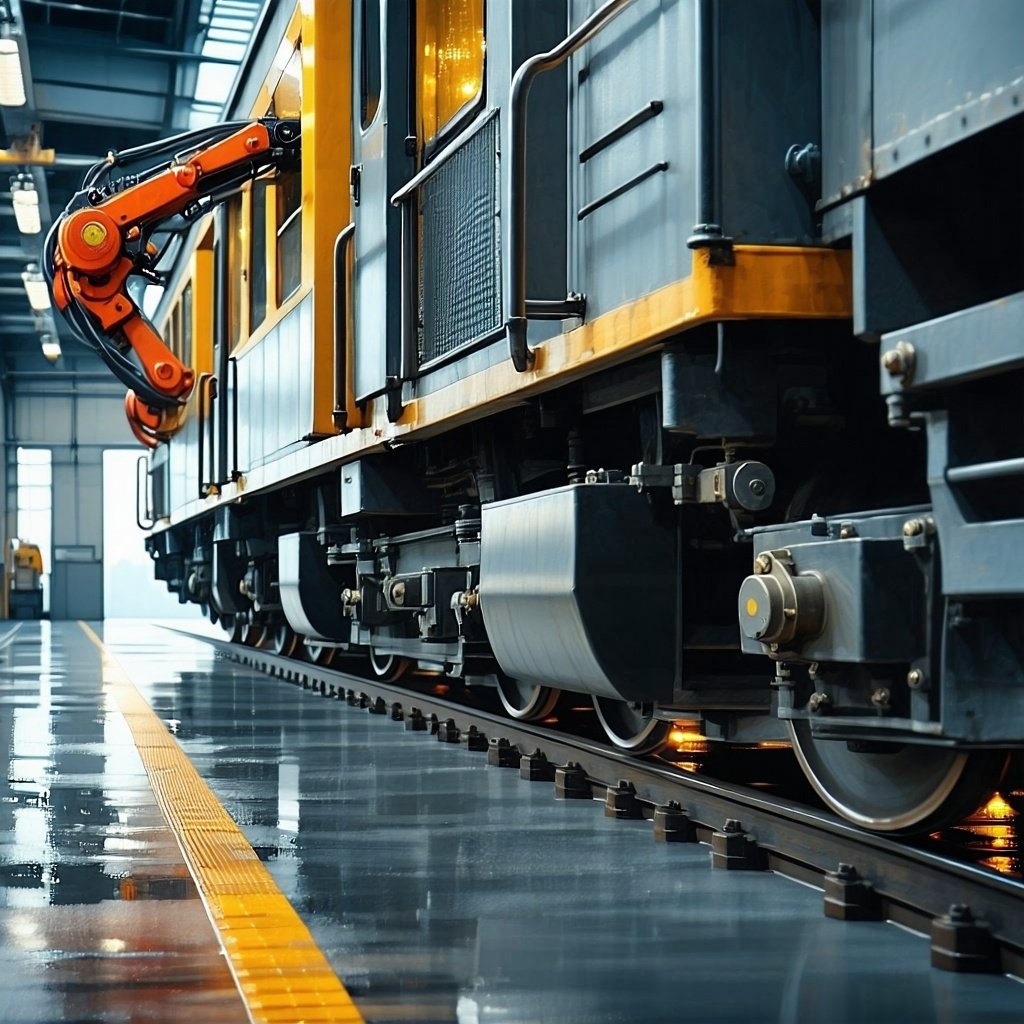
Advanced Eddy Current Testing for Freight Wagon Wheels
.png)
Future-Ready Inspection: How FOERSTER Powers Smarter, Safer NDT Solutions
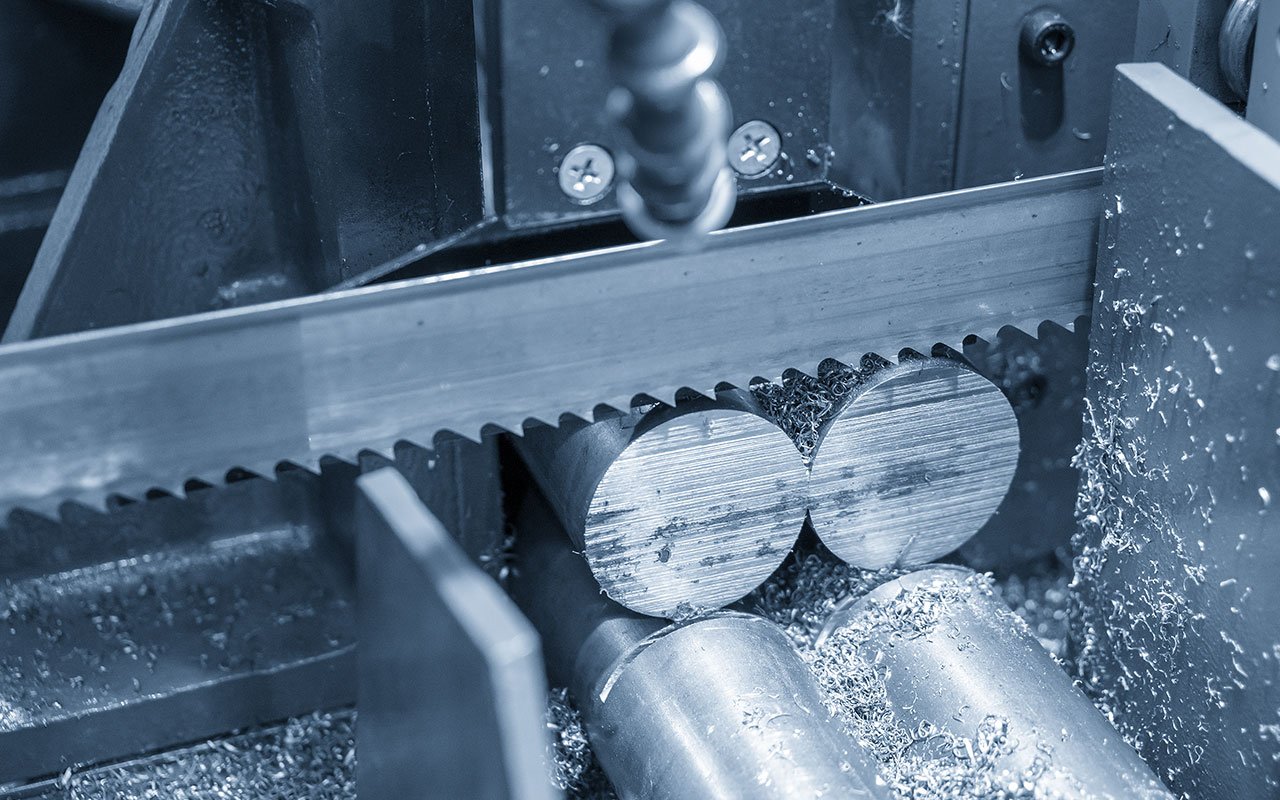