Freight wagon wheels endure constant mechanical and thermal stress, making them vulnerable to surface cracks, rolling contact fatigue, and thermal-induced damage. Traditional methods like Magnetic Particle Inspection (MPI) have been reliable but time-consuming, involving multiple handling steps that interrupt workflows.
Eddy Current Testing (ECT)—especially when integrated directly into the wheel reprofiling machine—provides a faster, more efficient, and non-destructive testing (NDT) solution.
This blog highlights how FOERSTER’s TCM system with ECARRAY technology transforms railway maintenance through automated, real-time wheel defect detection.
The Challenge: Surface Cracks in Freight Wagon Wheels
Freight wheels operate under harsh conditions. Over time, this leads to wear, material fatigue, and ultimately safety risks.
Common Defect Mechanisms:
-
Rolling Contact Fatigue: Microcracks from cyclic stress evolve into surface spalling.
-
Thermal Stress: Frequent braking leads to rapid heating/cooling, triggering structural changes and cracks.
-
Mechanical Wear: Continuous friction degrades material, increasing the risk of flaws.
Early flaw detection is essential not just for safety, but also for cost-effective, long-lasting wheel use.
The Solution: Eddy Current Testing for Surface Crack Detection
ECT uses electromagnetic induction to detect surface and near-surface flaws in conductive materials. It is:
How It Works:
A probe generates alternating current, producing a magnetic field. When placed near a conductive material (like a steel wheel), it induces eddy currents. Defects interrupt these currents, which the system captures and analyzes.
In Practice: Why Eddy Current Testing outperforms Traditional Methods
ECT Advantages in Freight Rail Maintenance
-
Inline integration: Directly embedded into the reprofiling machine, eliminating manual handling
-
Real-time analysis: Immediate defect feedback, no inspection delay
-
No consumables: No developer, film, or magnetic particles needed
-
Preserves material: Precise flaw depth info prevents unnecessary wheel grinding
Case Study: FOERSTER’s TCM with ECARRAY in Real-World Use
A validation study with W.S. Werkstoff Service GmbH demonstrated outstanding ECT performance on simulated wheelset defects.
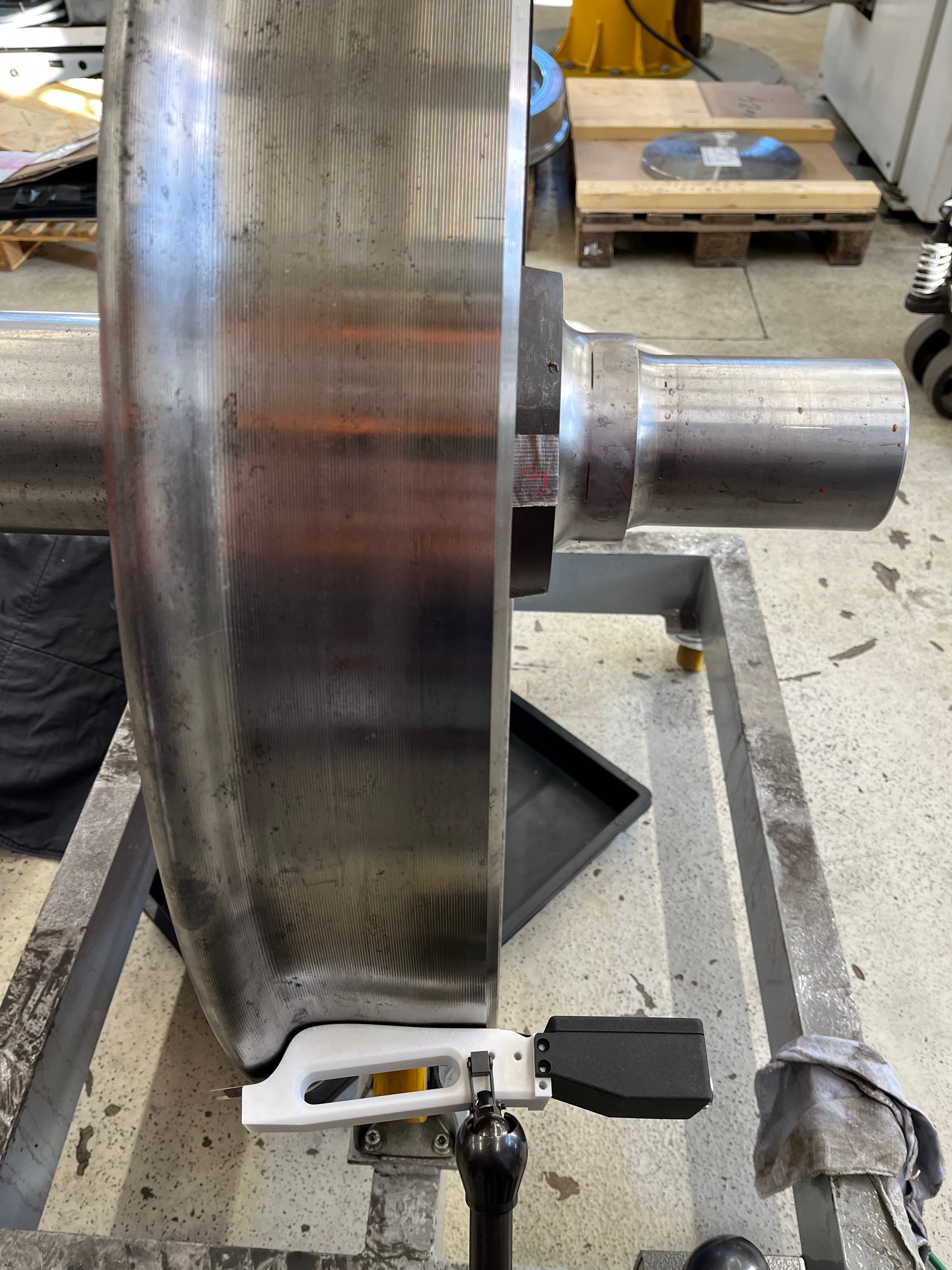
Setup:
-
Master test wheel with artificial grooves (10 mm × 1.0 mm and others)
-
FOERSTER’s TCM system with ECARRAY technology
-
Customized 64-element array probe for full-surface coverage
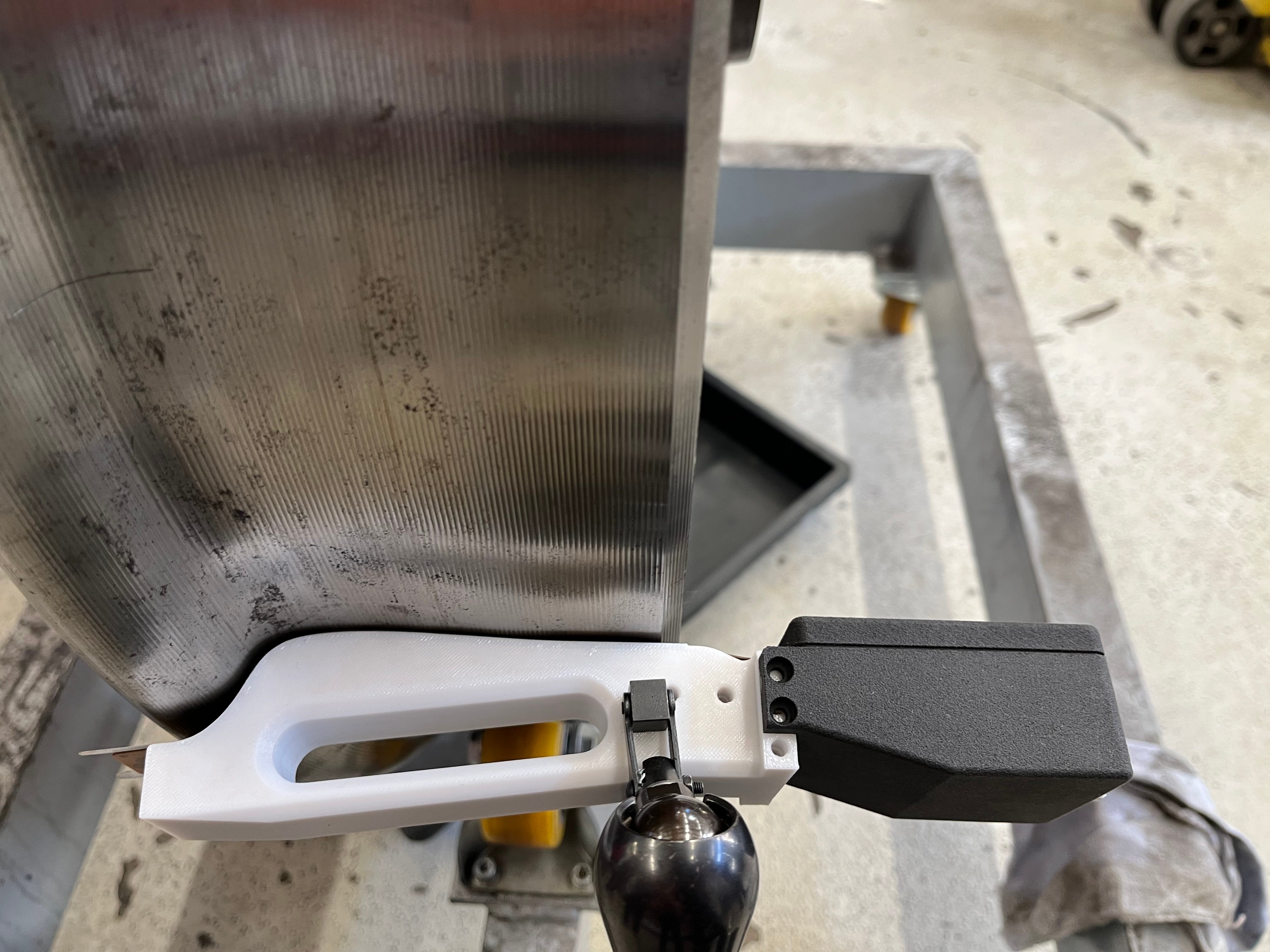
Key Probe Features:
-
Tailored contour matching the wheel profile
-
2.2 mm sensor pitch for high resolution
-
Flexible mount for consistent surface contact
-
Full coverage of running surfaces and transition zones
Results:
-
Accurate flaw detection including <1.0 mm cracks
-
Defect visualization via ECARRAY’s impedance display
-
Stable signal quality even over multiple wheel rotations
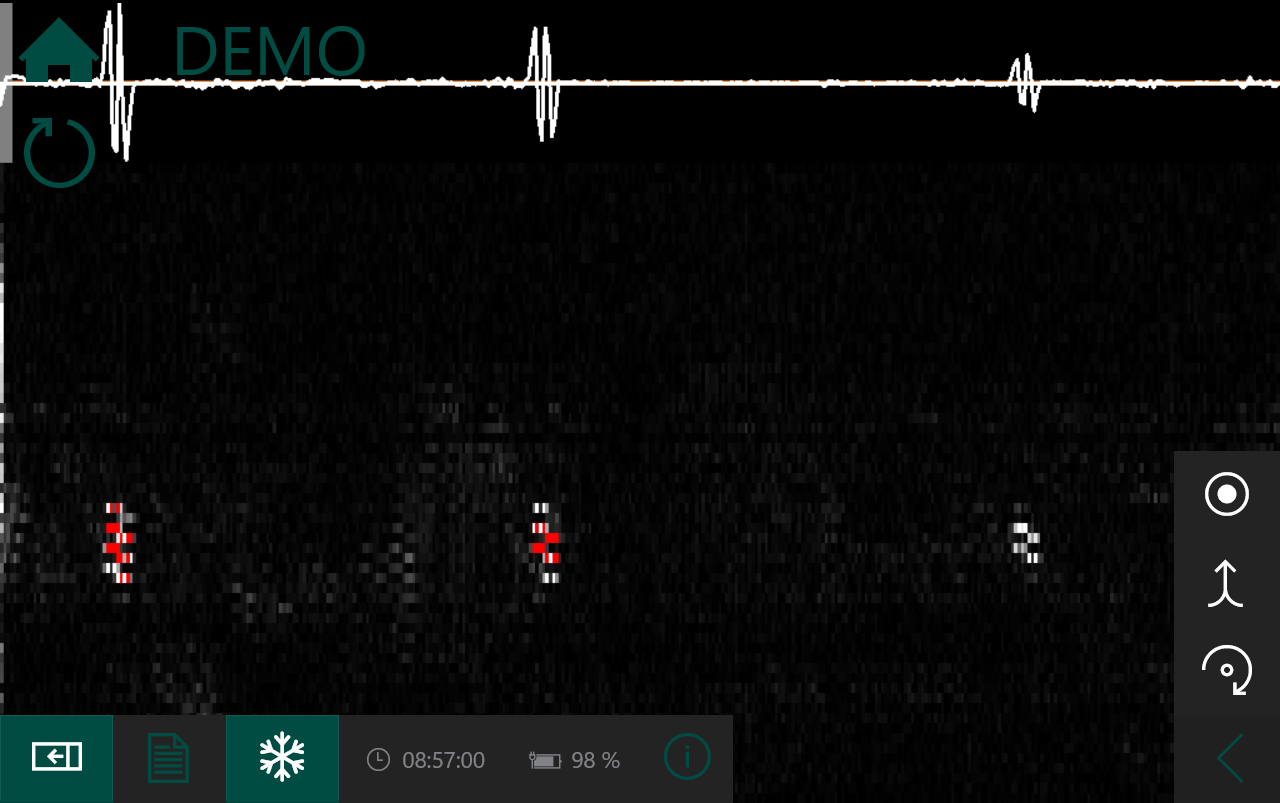
Benefits for Maintenance Teams
Less Handling Effort – No wheel disassembly or remounting
Faster Turnaround – Real-time inspection during reprofiling
Zero Consumables – Environmentally friendly, lower cost
Longer Wheel Life – Optimized defect detection avoids unnecessary material removal
TCM by FOERSTER – Eddy Current Testing for Rail Safety
.jpg?width=1592&height=1428&name=DSC04497_bearb%20(3).jpg)
FOERSTER’s TCM system with ECARRAY delivers a fully integrated, high-performance Eddy Current Testing solution for freight wheel inspections.
- Flaw detection down to 0.5 mm depth
- Inline operation—no workflow interruptions
- Objective, digital results in real time
- Proven performance under real-world conditions
Ready to Upgrade Your Wheel Inspections?
Optimize your railway maintenance with FOERSTER’s leading non-destructive Eddy Current technology.
Contact our experts today to discuss your specific application needs or schedule a demo.