¿Cuáles son las propiedades más significativas evaluadas durante las pruebas de materiales?
Una explicación detallada de las pruebas no destructivas de materiales.
Explicación detallada de los ensayos no destructivos de materiales.
En la industria automotriz, por ejemplo, se monitorean los procesos de producción para asegurarse de que solo salgan de la ventana de proceso especificada en situaciones extremas. El índice de capacidad del proceso revela si un proceso alcanza los objetivos establecidos en la especificación. Este índice, también llamado cpk, mide qué tan repetible y preciso es el proceso.
Los procesos que introducen una repetibilidad menos deseable y que mantienen tolerancias insuficientemente ajustadas deben ser monitoreados. Para la producción en línea, es fundamental determinar la integridad de una pieza, evitando que continúe al siguiente proceso de fabricación. Esto evita agregar más costos de fabricación a una pieza que puede que no cumpla con los requisitos de calidad. Existen muchos componentes críticos para la seguridad y el funcionamiento en un automóvil, equipo pesado o tren. Su rendimiento solo puede garantizarse si el material y los procesos de fabricación cumplen con requisitos específicos. Por ejemplo, técnicas de endurecimiento inadecuadas pueden hacer que los engranajes en la transmisión automotriz se desgasten prematuramente y fallen, o que un acoplador de remolque se vuelva demasiado frágil y se rompa. Incluso el uso del material incorrecto puede hacer que el componente se comporte de manera diferente en la aplicación en serie y conduzca a un mal funcionamiento grave. Siempre que se deba evitar un daño importante o cuando esté en riesgo la vida humana, es necesario llevar a cabo e implementar pruebas en proceso. De esta manera, se pueden garantizar y mantener los parámetros especificados. Las pruebas de materiales enumeradas a continuación se pueden realizar en paralelo con el proceso, o como parte de una inspección del 100%:
- Composición del material
- Variaciones en la dureza del material, incluidas:
Profundidad del caso
Dureza superficial (HB, HRC, HV)
Detección de materiales duros y blandos - Medición de la conductividad
- Medición de permeabilidad
- Pruebas de manchas duras y blandas
- Inspección de cavidades.
1. Composición del material
Existen cientos de aleaciones metálicas diferentes, que difieren en su composición y la forma en que se fabrican. Muchos productores tienen sus recetas secretas, que se compilan individualmente para cada producto final, y ciertas fluctuaciones en los componentes de la aleación son normales y permitidas, siempre que se mantengan dentro de la especificación.
Como dice el dicho: la confianza es buena; la verificación es mejor. Dependiendo del diseño de la cadena de suministro, no se puede confiar en la calidad. Por lo tanto, la composición del material debe verificarse regularmente. Esto se aplica, por ejemplo, en las industrias automotriz y de aviación y está regulado por las normas correspondientes.
La inspección puede llevarse a cabo en muestras en mercancías entrantes o, si es necesario, como una inspección del 100% directamente en la línea de producción. Hay varios métodos para las pruebas de mezcla de materiales: ya sea que se realice una prueba con un espectrómetro de masas en el laboratorio para muestrear el contenido de carbono al azar, o que se confíe en una inspección magnético-inductiva.
Espectrómetro de masas
El método magnético-inductivo funciona con corrientes inducidas. Los componentes de prueba generalmente pasan por una bobina de prueba que contiene una bobina primaria y una secundaria como medio para examinar sus propiedades materiales. En consecuencia, se inducen corrientes inducidas de baja frecuencia en el material. La tensión de prueba registrada por el sensor resulta de las propiedades magnéticas y eléctricas de la pieza de prueba, y el valor de tensión se muestra gráficamente como un punto de medición. Los diferentes componentes o estados estructurales de la aleación cambian las corrientes recibidas y permiten sacar conclusiones sobre las propiedades materiales de la pieza de prueba. Cada material deja su propia "huella digital", por así decirlo, que cambia según la frecuencia de medición utilizada.
Esta huella digital se incorpora al instrumento de prueba de corrientes inducidas para identificar de manera única un material. Es importante asegurarse de que las variables ambientales se mantengan estables. Para minimizar las indicaciones falsas, generalmente se intenta resolver la prueba con una frecuencia optimizada. Si los fabricantes necesitan examinar diferentes propiedades del material, pueden examinarlos con varias frecuencias fundamentales. Como alternativa, o además de las frecuencias básicas, también se pueden evaluar las frecuencias armónicas para identificar el material y eliminar componentes defectuosos.
Las dimensiones de los componentes de prueba deben ser idénticas al material enseñado. Esto se debe a que diferentes dimensiones hacen que los campos magnéticos de la sonda de prueba se propaguen de manera diferente y, por lo tanto, cambien la señal. Muchas líneas de producción están utilizando con éxito la identificación magnético-inductiva de materiales. Sin embargo, también se pueden encontrar aplicaciones fuera de las líneas de producción, por ejemplo, para diferenciar entre aluminio de alta calidad y de baja calidad.
2. Variaciones en la dureza del material
Dependiendo del material del que se fabrique un componente, se utilizan diferentes procesos de endurecimiento, como el endurecimiento por inducción o el endurecimiento en horno. Puede suceder que una pieza no tenga la dureza deseada después del procedimiento de endurecimiento; esto puede deberse a un contenido de carbono incorrecto o una aleación defectuosa.
En el endurecimiento por inducción, la corriente necesaria para calentar el componente también debe tener la magnitud adecuada. Con ello, se asegura que la temperatura superficial del componente sea correcta. La temperatura superficial imprecisa puede llevar a una transformación incorrecta de la microestructura. Por lo general, los controles ópticos no son posibles, ya que las diferencias entre los componentes no pueden verse a simple vista. Por lo tanto, se necesitan métodos de prueba no destructivos para informar al usuario sobre procesos defectuosos.
Dado que las propiedades magnéticas de los materiales se correlacionan con la dureza del material, la prueba magnético-inductiva se puede utilizar para registrar una "huella digital" específica en el componente. Las propiedades magnéticas de los materiales que contribuyen a las interacciones son la permeabilidad magnética, la remanencia y la coercitividad. Otro factor influyente en las pruebas magnético-inductivas de dureza es la conductividad eléctrica. El mismo método se puede utilizar para pruebas de mezcla de materiales y pruebas de dureza.
3. Medición de conductividad con un sistema de corriente inducidas
Además del material adecuado y su dureza, la conductividad eléctrica también juega un papel importante. En la construcción de aeronaves, por ejemplo, la conductividad de los materiales está estrictamente especificada en muchas aplicaciones. Uno de los objetivos es asegurar que la energía se conduzca y disipe en caso de un impacto de rayo. La conductividad eléctrica se define como la constante de proporcionalidad entre la densidad de corriente y la intensidad del campo eléctrico. Una configuración típica para medir la conductividad eléctrica de los metales es la medición de cuatro puntos. Aquí, se alimenta una corriente a lo largo de una distancia definida a través de dos puntas de medición y se mide la caída de voltaje por encima de esta.
Este método de medición es muy preciso y rastreable a cantidades de medición estandarizadas. Sin embargo, es difícil implementarlo en un entorno de producción, ya que cada componente a ser probado debe ser contactado. La suciedad, los aceites o las diferencias en la superficie pueden afectar significativamente el contacto de las puntas de prueba con la pieza de prueba y, por lo tanto, la medición en sí misma. Por lo tanto, otro método se ha establecido en el mercado durante años: medición de conductividad con corriente inducidas. A diferencia de las pruebas comparativas de detección de grietas y microestructuras con corrientes inducidas, la medición de la conductividad eléctrica no es una prueba comparativa, sino una medición pura. Esto significa que las puntas de prueba se pueden calibrar con un estándar nacional. La conductividad eléctrica hace que se desarrollen corrientes inducidas en el material, que interactúan con el campo primario generado en la sonda. Esta interacción se registra y evalúa en el hardware de medición. Si esta interacción se relaciona con la conductividad de un cuerpo de referencia, se puede establecer una conexión con la conductividad en función de la información sobre la interacción de las corrientes inducidas. Sin embargo, hay que tener en cuenta que la intensidad del campo del campo magnético acoplado depende de la distancia entre la sonda de prueba y la pieza de trabajo. Si la distancia cambia durante la medición o si la distancia es diferente en comparación con la calibración a un estándar, pueden ocurrir errores de medición.
Para reducir estos errores de medición, la señal de amplitud se utiliza para compensar el efecto de la distancia. (Para información: para la medición de la conductividad eléctrica, la señal de fase se evalúa principalmente, la señal de amplitud se utiliza para compensar los efectos de la distancia). La medición generalmente se realiza en muestras aleatorias, por lo que se prefieren los dispositivos de medición móviles. Del mismo modo, también es posible utilizar el método de medición en una prueba en serie con un instrumento de medición en línea. Además, se puede realizar una inspección de superficie completa de placas o barras para detectar fluctuaciones en la conductividad.
4. Medición de permeabilidad de materiales
La permeabilidad magnética es una medida de la permeabilidad de la materia a los campos magnéticos (análogo a la conductividad eléctrica en campos eléctricos). Por ejemplo, los aceros ferríticos o martensíticos tienen buena permeabilidad magnética. En contraste, ocurre lo contrario en los aceros austeníticos. En el caso de los motores eléctricos, la funcionalidad y la eficiencia están fuertemente influenciadas por la permeabilidad magnética; como resultado, la medición y verificación de esta propiedad del material se están volviendo cada vez más importantes. La razón de esto es que algunos componentes para accionamientos eléctricos deben estar hechos de materiales que sean fácilmente magnetizables para que el sistema electromagnético pueda operar rápidamente y con la menor energía posible.
Componente electromagnético Inductor
Sin embargo, también hay aplicaciones en las que los materiales no deben tener permeabilidad o solo deben tener una permeabilidad muy baja. Por ejemplo, solo los componentes no magnéticos son adecuados para su instalación en una tomografía por resonancia magnética (MRI) para que no influyan en el campo magnético que se genera. Por la misma razón, los implantes solo pueden estar compuestos de materiales no magnéticos si un paciente requiere una resonancia magnética.
Existen dos formas de medir la permeabilidad de un material:
-
- Medición de permeabilidad en corriente alterna (AC), es decir, la medición de la permeabilidad magnética en campos alternos.
- Medición de permeabilidad en corriente continua (CC), es decir, medir la permeabilidad magnética aumentando sucesivamente el flujo magnético.
5. Pruebas de manchas duras, blandas y cavidades
Las llamadas manchas duras o blandas son diferencias locales en la microestructura (no homogeneidades) que surgen debido al proceso de fabricación. Se hacen notar mediante diferentes durezas, conductividad o composiciones de materiales. Se utilizan los mismos métodos para encontrar estas no homogeneidades que en las pruebas de mezcla de materiales o pruebas de dureza. Mientras que el resultado se promedia en todo el componente en esos casos, para probar las manchas es necesario escanear el componente de manera precisa. La configuración para probar manchas duras es, por lo tanto, análoga, a diferencia de la prueba clásica de detección de grietas con corriente inducidas. La formación de porosidades también se limita a un área muy local. La detección ultrasónica se utiliza típicamente para su detección. En este caso, es necesario mover la cabeza ultrasónica a lo largo de la pieza de prueba o, de manera análoga, la pieza de prueba junto con la cabeza ultrasónica. La metodología para esto se explica en la sección sobre métodos de detección de grietas.
¿Cómo puede ser una prueba de material típica?
FOERSTER ha desarrollado un dispositivo particular para tareas de pruebas en el campo de pruebas de materiales y dureza. El MAGNATEST D es particularmente adecuado para aplicaciones en serie. El hardware del dispositivo de prueba está diseñado de tal manera que varios componentes pueden ser probados en un tiempo muy corto, es decir, se pueden lograr altas tasas de ciclo. Esta configuración de prueba requiere una bobina de prueba, un dispositivo de prueba y la alimentación del componente. La alimentación del componente puede realizarse manual o automáticamente. El tipo de alimentación del componente y el nivel de automatización influyen en los costos de adquisición de un sistema de prueba.
Por lo general, el MAGNATEST D está configurado especialmente para detectar automáticamente cuándo se inserta un objeto de prueba en la bobina. Con esta detección, se activa el inicio de la prueba real y la posterior clasificación de buena/mala. Los resultados de la prueba se devuelven como una señal de entrada/salida y como información directa en la pantalla. La prueba se realiza ya sea con una bobina de paso, por la cual pasa el objeto de prueba, o con sondas fijas, a las cuales se alimenta el objeto de prueba manual o automáticamente. Además de esto, el MAGNATEST D también puede integrarse directamente en la producción. Además, se puede verificar directamente después del proceso de acabado para asegurarse de que se realizó correctamente. En caso de un proceso defectuoso y el consiguiente desperdicio de producción, la retroalimentación oportuna permite tomar contramedidas a tiempo.
Análisis de regresión en pruebas de dureza
Los valores medidos durante la prueba de dureza no destructiva con un instrumento de corriente inducidas son valores adimensionales que contienen una declaración sobre la parte real e imaginaria de las señales en la bobina de medición secundaria. Mediante un análisis de correlación, es decir, una regresión de un método de medición física de la dureza absoluta con los valores adimensionales de las pruebas de corriente inducidas, estos valores se pueden parametrizar, lo que significa que el instrumento de prueba se puede utilizar para medir durante el proceso en serie. Cómo se ve este análisis de regresión y cómo se puede implementar se aborda en otra sección.
Share this
You May Also Like
These Related Stories
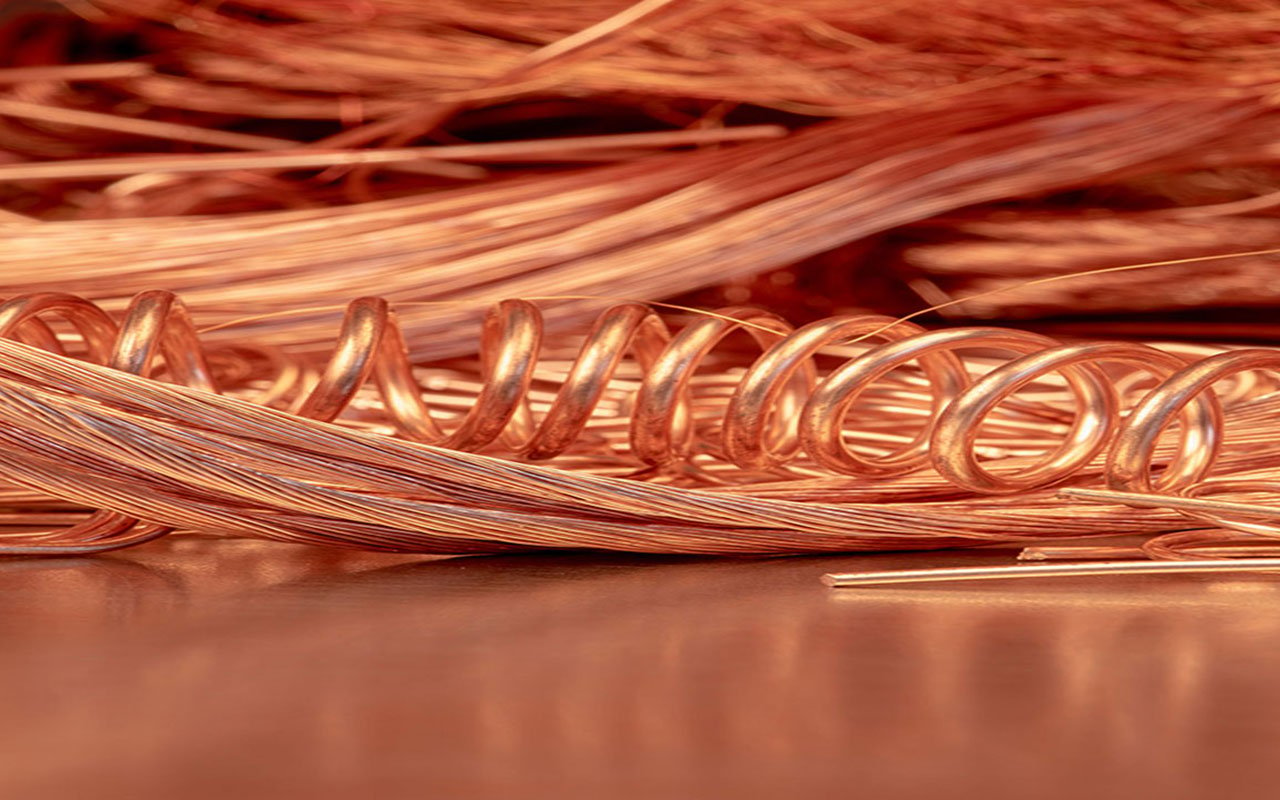
Las propiedades magnéticas de materiales y componentes
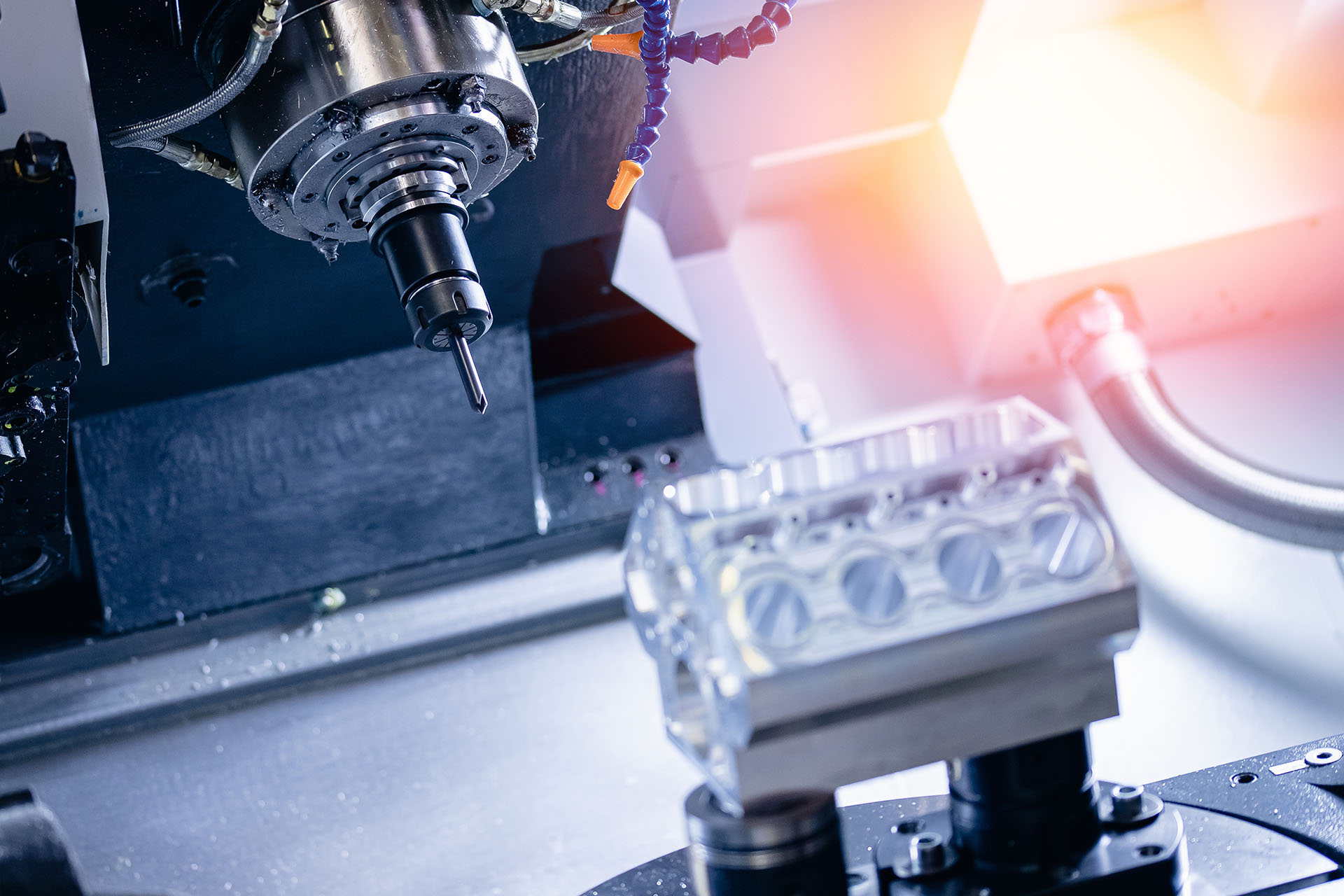
Pruebas automatizadas de cilindros con el método de corrientes inducidas
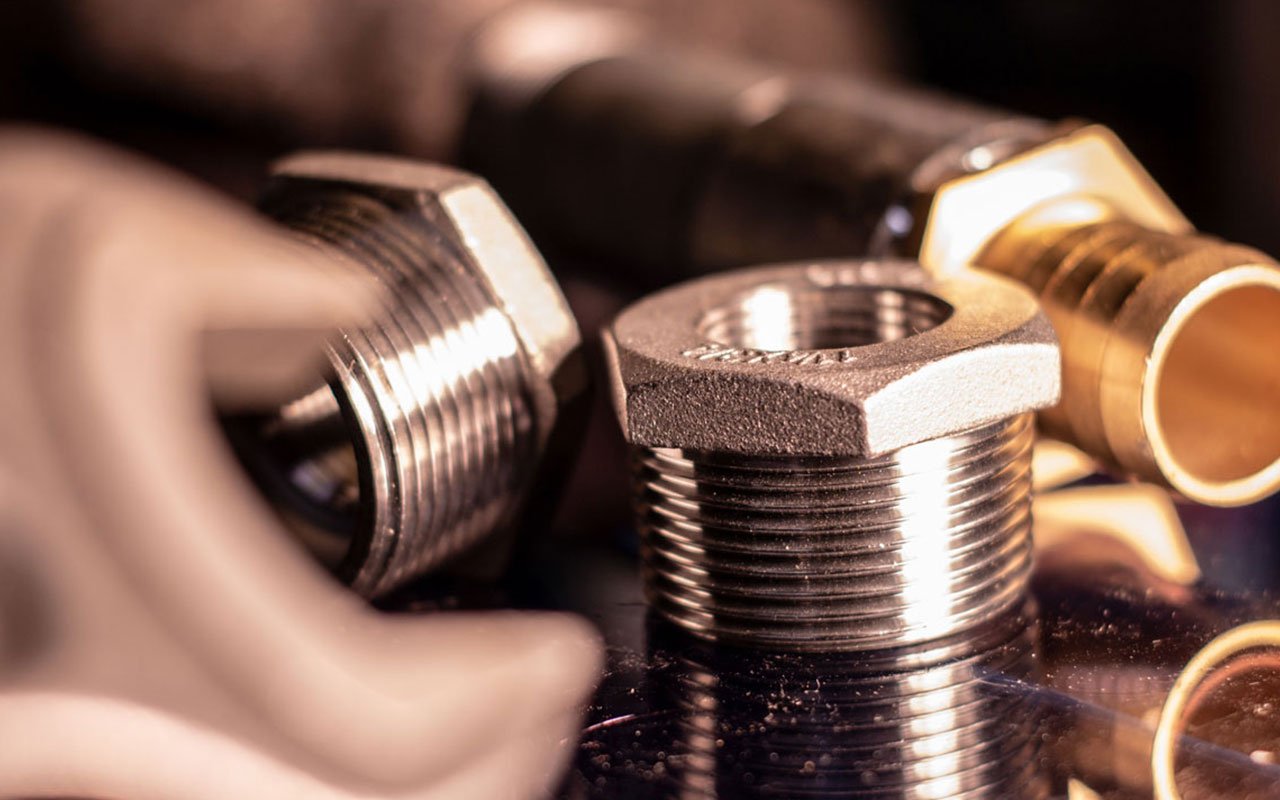