What are the most significant properties assessed during materials testing?
What are the most significant properties assessed during materials testing?
A detailed explanation of non-destructive materials testing.
In the automotive industry, for instance, production processes are monitored to ensure that they only leave the specified process window in extreme situations. The process capability index reveals if a process achieves the goals set out in the specification. This index, also called cpk, measures how repeatable and accurate is the process.
Processes introducing less than desirable repeatability and insufficiently maintaining tight tolerance must be monitored. For in-line production, it is critical to determine the integrity of a part, preventing it from continuing to the next manufacturing process. This avoids adding more cost of manufacturing to a part that may not already meet the quality requirements. There are many safety critical and function critical components that make up an automobile, heavy equipment, or train. Their performance can only be guaranteed if the material and manufacturing processes fulfill specific requirements. For example, inadequate hardening techniques can cause gears in an automotive drivetrain to wear prematurely and fail or a trailer coupler to become too fragile and break. Even using the wrong raw material can cause the component to behave differently in the series application and lead to a serious malfunction. Whenever major damage is to be prevented, or human life is at risk, it is necessary to conduct and implement in-process tests. Thereby, the specified parameters can be ensured and maintained. Material tests listed as follows can be performed in parallel with the process, or as part of a 100% inspection:
- Material composition
- Material hardness variations including:
- Case Depth
- Surface hardness (HB, HRC, HV)
- Hard and soft detection
- Conductivity measurement
- Permeability measurement
- Testing for hard and soft spots
- Void inspection.
1. Material composition
There are hundreds of different metal alloys, which differ in their composition and the way they are manufactured. Many producers have their secret recipes, which are individually compiled for each end product, and certain fluctuations in the alloy components are normal and permissible - as long as they remain within the specification.
As the saying goes: Trust is good; verification is better. Depending on the design of the supply chain, you cannot rely on quality. Thus, the material composition must be checked regularly. This applies, for instance, in the automotive and aviation industries and is regulated by the corresponding standards.
The inspection can either take place on samples at incoming goods or - if necessary - as a 100% inspection directly in the production line. There are various methods for material mix testing: either you test with a mass spectrometer in the laboratory to sample the carbon content randomly, or rely on a magnetic-inductive inspection.
Mass spectrometer
The magnetic-inductive method works with eddy currents. Test components usually pass through a test coil containing a primary and secondary coil as a means to examine their material properties. Accordingly, low-frequency eddy currents are introduced into the material induced. The test voltage registered by the sensor results from the magnetic and electrical properties of the test part, whereby the voltage value is graphically displayed as a measuring point. The different alloy components or structural states change the receiver currents and thus allow conclusions to be drawn about the material properties of the test part. Each material leaves its own unique "fingerprint,” so to speak, which changes depending on the measurement frequency used.
This fingerprint is taught into the eddy current testing instrument to uniquely identify a material. It is important to make sure that the environmental variables remain stable. As a means to minimize pseudo indications, it is usually attempted to solve the test with an optimized frequency. If manufacturers need to examine different material properties, they can examine them with several fundamental rates. As an alternative, or in addition to the basic frequencies, the harmonic ones can also be evaluated in order to identify the material and sort out flawed components.
The dimensions of the test components must be identical to the taught-in material. This is since different dimensions cause the magnetic fields of the test probe to propagate differently and thus change the signal. Many production lines are using the magnetic-inductive material identification testing successfully. However, applications can also be found outside the production lines, for example to differentiate between high-grade and low-grade aluminum.
2. Material hardness variations
Depending on the material from which it makes a component, different hardening processes are used, among these, induction hardening or furnace hardening. It can happen that a piece does not have the desired hardness after the hardening procedure; this can be caused by an incorrect carbon content or a defective alloy.
In induction hardening, the current required to heat the component also has to be of the right magnitude. Therewith, ensuring that the surface temperature of the component is correct. The imprecise surface temperature can lead to incorrect microstructure transformation. Optical controls are usually not possible since the differences between the components cannot be seen with the naked eye. Therefore, non-destructive testing methods are needed to report faulty processes to the user.
Since magnetic material properties correlate with material hardness, magnetic-inductive testing can be used to record a specific "fingerprint" on the component. Magnetic properties of materials that contribute to interactions are magnetic permeability, remanence, and coercivity. Another influencing factor in magnetic-inductive hardness testing is electrical conductivity. The same method can be used for material mix tests and hardness tests.
3. Conductivity measurement with an eddy current system
Besides the right material and its hardness, electrical conductivity also plays a significant role. In aircraft construction, for instance, the conductivity of the materials is strictly specified in many applications. One of the aims is to ensure that the energy is conducted and dissipated in the event of a lightning strike. Electrical conductivity is defined as the constant of proportionality between the current density and the strength of the electric field. A typical setup for measuring the electrical conductivity of metals is the four-point measurement. Here, a current is fed in over a defined distance via two measuring tips and the voltage drop is measured above this.
This measuring method is very accurate and traceable to standardized measurement quantities. However, it is difficult to implement it in a production environment, since every component to be tested must be contacted. Dirt, oils or surface differences can significantly affect the contact of the test probes with the test part and thus the measurement itself. Therefore, another method has been established on the market for years: conductivity measurement with eddy current. In contrast to crack and microstructure testing with eddy current, the measurement of electrical conductivity is not a comparative test, but a pure measurement. This means that the probes can be calibrated to a national standard. The electrical conductivity causes eddy currents to develop in the material, which interact with the primary field generated in the probe. This interaction is recorded and evaluated in the measurement hardware. If this interaction is set in relation to the conductivity of a reference body, a connection to the conductivity can be established based on the information about the interaction of the eddy currents. It should be noted, however, that the field strength of the coupled magnetic field depends on the distance between the test probe and the workpiece. If the distance changes during the measurement or if the distance is different compared to calibration to a standard, measurement errors can occur.
To reduce these measuring errors, the amplitude signal is used to compensate for the distance effect. (For information: For the measurement of the electrical conductivity the phase signal is primarily evaluated, the amplitude signal is used to compensate for distance effects). The measurement is usually carried out on random samples, which is why mobile measuring devices are preferred. Likewise, it is also possible to use the measuring method in a series test with a line measuring instrument. Furthermore, a full-surface inspection of plates or rods for a fluctuation in conductivity can be performed.
4. Measurement of material permeability
The magnetic permeability is a measure of the permeability of matter to magnetic fields (analogous to the electrical conductivity in electric fields). For instance, ferritic or martensitic steels have good magnetic permeability. In contrast, the opposite is true for austenitic steels. In the case of electric motors, the functionality and efficiency are strongly influenced by magnetic permeability; as a result, the measurement and verification of this material property are becoming increasingly important. Reason for this is that some components for electric drives have to be made of materials that are easily magnetizable so that the electromagnetic system can operate quickly and with as little energy as possible.
Electromagnetic Component Inductor
However, there are also applications in which the materials must have no or only very low permeability. For instance, only amagnetic components are suitable for installation in a magnetic resonance tomography (MRI) so that they do not influence the magnetic field that is generated. For the same reason, implants may only consist of amagnetic materials if a patient requires an MRI.
There are two ways to measure the permeability of a material:
- AC permeability measurement, i.e. the measurement of magnetic permeability in alternating fields.
- DC permeability measurement, i.e. measuring the magnetic permeability by successively increasing the magnetic flux.
The permeability is defined as the slope of the characteristic curve in a B/H measurement curve. A closed magnetic circuit such as the one used for a ring sample DC or Epstein frame AC measurement is a prerequisite.
The permeability or the B/H measurement curve can be registered by using a primary coil (measures H field) and a secondary coil (measures B field). The relationship between the impressed current and the measured induction voltage as an integral represents the B/H characteristic curve, and its slope represents the magnetic permeability. A defined field with an impressed current is generated with the primary coil. The magnetic field H induced by the current produces a magnetic flux in the test part.
The secondary coil is arranged parallel to the primary coil. The magnetic flux causes an induction voltage in the test part. Particularly challenging is to realize the relationship between B/H as close as possible to the existing component geometry in order to measure different shapes of test pieces with this method. To achieve this developing a model that can be applied from a standard piece to the geometry of the test piece becomes crucial. DC measurement is commonly used in industrial environments, but AC measurement is interesting for applications where the working frequencies are in a higher kHz range.
5. Testing of hard spots, soft spots, and cavities
So-called hard spots or soft spots are local differences in the microstructure (inhomogeneities) that arise due to the manufacturing process. They become noticeable through different hardnesses, conductivity, or material compositions. The same methods are used to find these inhomogeneities as in material mix or hardness testing. While the result is averaged over the entire component in those cases, to test the spots it is necessary to scan the component precisely. The setup for testing hard spots is therefore analogous, contrary to the classical crack testing with eddy current. The formation of blowholes is also limited to a very local area. Ultrasonic testing is typically used for detection. In this case, it is necessary to move the ultrasonic head along the test piece or, analogously, the test piece along with the ultrasonic head. The methodology for this is explained in the section on crack detection methods.
What can a typical material test look like?
FOERSTER has developed a particular device for testing tasks in the field of material and hardness testing. The MAGNATEST D is particularly suitable for series applications. The hardware of the testing device is designed in such a way that several components can be tested within a very short time, i.e. high cycle rates can be achieved. This test setup requires a test coil, a test device and the component feed. The component feeding can be done manually or automatically. The type of component feed and the level of automation influence the acquisition costs of a test system.
As a rule, the MAGNATEST D is specially configured to automatically detect when a test object is inserted into the coil. On this note, the component recognition triggers the beginning of the actual test and the subsequent good/bad sorting. The test results are returned as an I/O signal and direct information on the screen. The test takes place either with a feed-through coil, which the test object passes through, or with fixed probes, to which the test object is manually or automatically fed. Besides this, the MAGNATEST D can also be integrated directly into production. On top of that, it can be checked directly after the finishing process to ensure that it was carried out correctly. In the event of a faulty process and the resulting waste of production, timely feedback allows countermeasures to be taken in a timely manner.
Regression analysis in hardness testing
The measured values during non-destructive hardness testing with an eddy current instrument are dimensionless values that contain a statement about the real and imaginary part of the signals in the secondary measuring coil. By means of a correlation analysis, i.e., a regression of a physical measuring method of the absolute hardness with the dimensionless values of eddy current testing, these values can be parameterized, meaning that the testing instrument can be used for measuring during the series process. How this regression analysis looks like and how it can be implemented is addressed in another section.
Share this
You May Also Like
These Related Stories
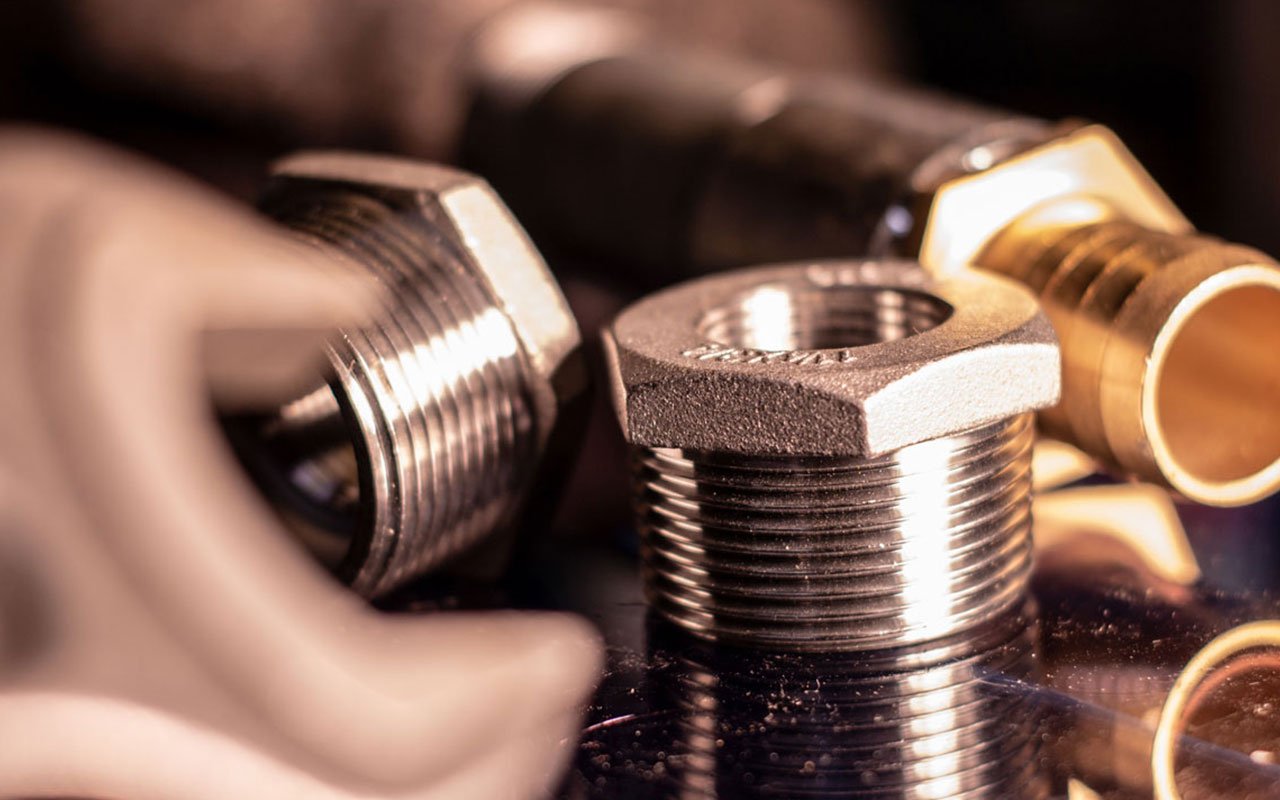
Electrical conductivity measurement with eddy current - 6 factors you should pay attention to
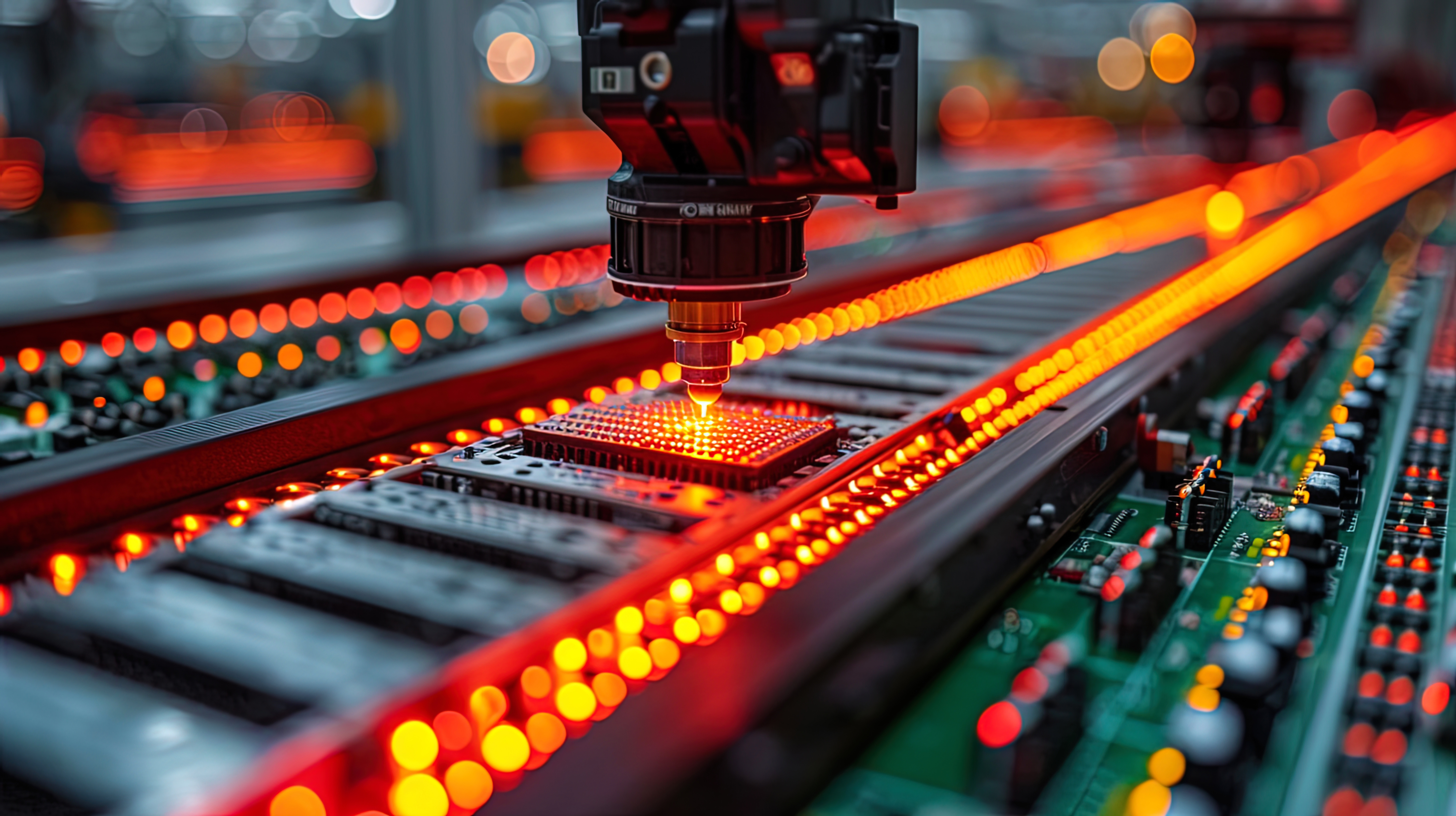
Decoding Coercivity & Magnetic Saturation Testing: Industry Significance
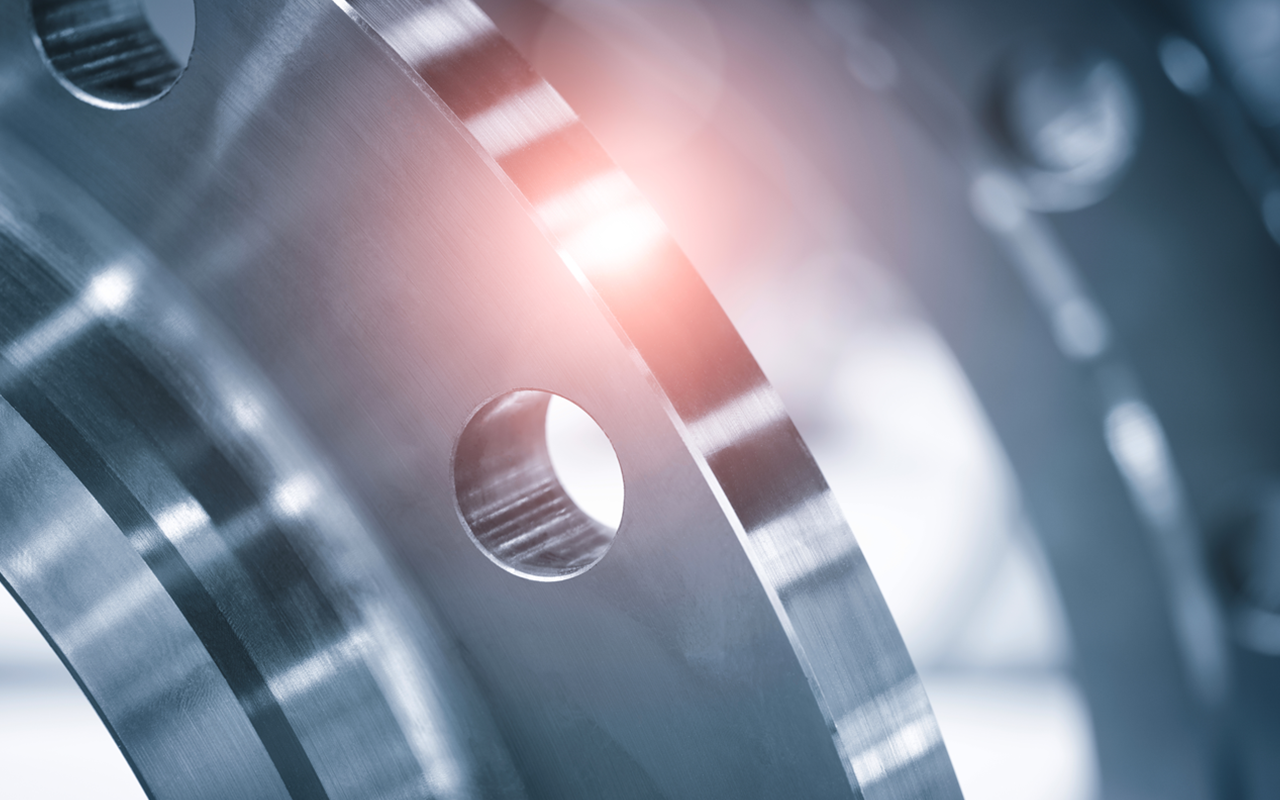