Welche sind die wichtigsten Arten der Materialprüfung
Kennen Sie die wichtigsten Arten der Materialprüfung?
Die zerstörungsfreie Werkstoffprüfung kurz erklärt
Beispielsweise in der Automobilindustrie werden Produktionsprozesse entsprechend kontrolliert, dass sie nur in Extremsituationen das vorgegebene Prozessfenster verlassen. Ob ein Prozess die laut Spezifikation vorgegeben Ziele erreicht, spiegelt sich im Prozessfähigkeitsindex wider. Dieser Index, auch cpk genannt, ist ein Maß dafür, wie wiederholbar und absolut genau der Prozess funktioniert.
Prozesse mit einer schlechten Reproduzierbarkeit oder absoluten Genauigkeit müssen überwacht werden. In einer Serienproduktion ist es zwingend erforderlich rechtzeitig festzustellen, wenn der Prozess sein gegebenes Prozessfenster verlässt, um zu verhindern, dass fehlerhafte Teile produziert werden.
In einem Auto, einem Baukran oder einem Zug gibt es viele sicherheitsrelevante und funktionskritische Komponenten. Deren Funktion ist nur dann gewährleistet, wenn das Material und der Herstellungsprozess exakt eingehalten werden. So kann zum Beispiel eine Anhängerkupplung brechen, wenn der Härteprozess nicht exakt eingehalten wurde und die Anhängerkupplung zu spröde Eigenschaften aufweist. Oder die Laufflächen eines Antriebs können sich zu schnell abnutzen, wenn diese nicht richtig gehärtet wurden.
Bereits der Einsatz des falschen Rohmaterials kann dazu führen, dass sich das Bauteil in der Serienanwendung anders verhält und zu einem schwerwiegendem Fehlverhalten führt.
Immer dann, wenn große Schäden verhindert werden sollen oder Menschenleben in Gefahr sind, ist es notwendig, prozessbegleitende Prüfungen durchzuführen. Nur so kann sichergestellt werden, dass die vorgegebenen Parameter eingehalten werden.
Folgende Materialprüfungen können dabei prozessbegleitend oder im Rahmen eine 100%-Prüfung durchgeführt werden:
- Materialverwechslungsprüfung
- Prüfung von Härteparametern (u.a. Einhärtetiefe und Oberflächenhärte)
- Leitfähigkeitsmessung
- Permeabilitätsmessung
- Prüfung auf Hard- und Soft Spots
- Lunkerprüfung
1. Materialverwechslungsprüfung
Es gibt hunderte verschiedene Metalllegierungen, die sich in ihrer Zusammensetzung und der Art der Herstellung unterscheiden. Viele Hersteller haben ihre Geheimrezepte, die individuell für das jeweilige Endprodukt zusammengestellt werden. Gewisse Schwankungen in den Legierungsbestandteilen sind dabei normal und zulässig - solange diese innerhalb der Spezifikation bleiben. Wie ein Sprichwort sagt: Vertrauen ist gut; Kontrolle ist besser. Je nach Gestaltung der Supply Chain kann man sich nicht auf die Qualität verlassen. Daher muss die Materialzusammensetzung regelmäßig geprüft werden. Dies ist zum Beispiel in der Automobil- oder der Luftfahrtindustrie der Fall und durch entsprechende Normen geregelt. Die Prüfung kann entweder an Stichproben beim Wareneingang stattfinden oder - sofern erforderlich - als 100%-Prüfung direkt in der Produktionslinie. Für die Materialverwechslungsprüfung gibt es verschiedenste Methoden: von der Prüfung mit einem Massenspektrometer im Labor, über eine schnelle Stichprobenmessung des Kohlenstoffgehalts, bis zum magnet-induktiven Verfahren.
Massenspektrometer
Das magnet-induktive Verfahren arbeitet mit Wirbelströmen. Zur Prüfung auf die Werkstoffeigenschaften passieren die Prüflinge in der Regel eine Prüfspule, die eine Primär- und Sekundärspule enthält. Dabei werden niederfrequente Wirbelströme in das Material induziert. Die vom Sensor erfasste Prüfspannung resultiert aus den magnetischen und elektrischen Eigenschaften des Prüfteils, wobei der Spannungswert als Messpunkt graphisch dargestellt wird. Die unterschiedlichen Legierungsbestandteile oder Gefügezustände verändern die Empfängerströme und lassen damit Rückschlüsse auf die Materialeigenschaften des Prüfteils zu. Jedes Material hinterlässt sozusagen seinen eigenen eindeutigen “Fingerabdruck”, der sich in Abhängigkeit zur verwendeten Messfrequenz ändert.
Dieser Fingerabdruck wird in das Wirbelstromgerät eingelernt, um ein Material eindeutig zu identifizieren. Wichtig ist, dass die Umgebungsvariablen dabei stabil bleiben. Um Pseudoanzeigen zu minimieren wird meist versucht, die Prüfung mit einer optimierten Frequenz zu lösen. Sollen verschiedene Materialeigenschaften untersucht werden, kann eine Prüfung mit mehreren Grundfrequenzen stattfinden. Alternativ oder zusätzlich zu den Grundfrequenzen können auch die harmonischen Frequenzen ausgewertet werden, um das Material eindeutig zu identifizieren und falsche Materialien auszusortieren. Wichtig ist, dass die Abmessungen des Prüflings identisch zum eingelernten Material sind. Denn unterschiedliche Dimensionen bewirken, dass sich die Magnetfelder der Prüfsonde anders ausbreiten und somit das Signal verändern.
Die magnet-induktive Materialverwechslungsprüfung wird bereits in vielen Produktionslinien erfolgreich eingesetzt. Aber auch außerhalb von Produktionslinien finden sich Anwendungen, beispielsweise zur Unterscheidung von hoch- und minderwertigem Aluminium.
2. Prüfung von Härteparametern
Je nach Material, aus dem ein Bauteil besteht, kommen unterschiedliche Härteverfahren zum Einsatz, wie das Induktionshärten oder das Ofenhärten. Dabei kann es passieren, dass ein Bauteil nach dem Prozess nicht die gewünschte Härte hat, zum Beispiel aufgrund eines falschen Kohlenstoffgehalts oder einer fehlerhaften Legierung.
Beim Induktivhärten muss zudem Strom, der zur Erwärmung des Bauteils benötigt wird, die richtige Größenordnung haben, damit die Oberflächentemperatur des Bauteils stimmt. Eine falsche Oberflächentemperatur kann dazu führen, dass die Gefügeumwandlung inkorrekt abläuft. Optische Kontrollen sind meistens nicht möglich, da die Unterschiede zwischen den Komponenten mit dem bloßen Auge nicht zu sehen sind. Daher werden zerstörungsfreie Prüfmethoden benötigt, die dem Anwender fehlerhafte Prozesse melden. Da vor allem die magnetischen Materialeigenschaften mit der Materialhärte korrelieren, kann mit der magnet-induktiven Prüfung ein spezifischer “Fingerabdruck” des Bauteils aufgenommen werden. Magnetische Eigenschaften von Materialien, die zu Wechselwirkungen beitragen, sind die Magnetische Permeabilität, die Remanenz und Koerzitivfeldstärke. Ein weiterer Einflussfaktor bei der magnet-induktiven Härteprüfung ist die elektrische Leitfähigkeit. Für Materialverwechslungsprüfungen und Härteprüfungen kann dasselbe Verfahren verwendet werden.
3. Leitfähigkeitsmessung mit einem Wirbelstromsystem
In vielen Anwendungen spielt neben dem richtigen Material und dessen Härte die elektrische Leitfähigkeit eine wichtige Rolle. Beispielsweise ist im Flugzeugbau genau spezifiziert, welche Leitfähigkeit die verwendeten Materialien haben dürfen. So will man unter anderem erreichen, dass bei einem Blitzeinschlag die Energie geleitet und abgeführt wird. Die elektrische Leitfähigkeit ist definiert als die Proportionalitätskonstante zwischen der Stromdichte und der elektrischen Feldstärke. Ein typischer Aufbau zur Messung der elektrischen Leitfähigkeit von Metallen ist die Vierpunktmessung. Hierbei wird über eine festgelegte Strecke über zwei Messspitzen ein Strom eingespeist und darüber der Spannungsabfall gemessen.
Die Messmethode ist sehr genau und rückführbar auf genormte Messgrößen. Allerdings lässt sich diese Messmethode nur schwer in einer Produktionsumgebung umsetzen, da jedes zu prüfende Bauteil kontaktiert werden muss. Dreck, Öle oder Oberflächenunterschiede können den Kontakt der Messspitzen mit dem Prüfteil und damit die Messung selbst erheblich beeinflussen. Daher hat sich seit Jahren eine weitere Methode auf dem Markt etabliert: die Leitfähigkeitsmessung mit Wirbelstrom. Im Gegensatz zur Riss- und Gefügeprüfung mit Wirbelstrom findet bei der Messung der elektrischen Leitfähigkeit keine vergleichende Prüfung statt, sondern eine reine Messung. Das heißt, die Sonden können auf einen nationalen Standard hin kalibriert werden. Die elektrische Leitfähigkeit bewirkt die Ausbildung von Wirbelströmen im Material, welche eine Wechselwirkung mit dem in der Sonde erzeugten Primärfeldes eingehen. Diese Wechselwirkung wird in der Messhardware erfasst und ausgewertet. Setzt man diese Wechselwirkung in einen Bezug zur Leitfähigkeit eines Vergleichskörpers, kann man aufgrund der Information über die Wechselwirkung der Wirbelströme eine Verbindung zur Leitfähigkeit herstellen. Zu beachten ist allerdings, dass die Feldstärke des eingekoppelten Magnetfeldes vom Abstand der Prüfsonde zum Werkstück abhängig ist. Verändert sich der Abstand während der Messung oder ist der Abstand im Vergleich zur Kalibrierung auf einen Standard unterschiedlich, können Messfehler entstehen. Um diese Messfehler zu reduzieren, wird das Amplitudensignal zur Kompensation des Abstandseffektes verwendet.
Üblicherweise findet die Messung an Stichproben statt, weshalb bevorzugt mobile Messgeräte verwendet werden. Natürlich ist es auch möglich, die Messmethode in einer Serienprüfung mit einem Linienmessgerät einzusetzen. Weiter ist eine ganzflächige Überprüfung von Platten oder Stangen auf eine Fluktuation der Leitfähigkeit realisierbar.
4. Messung der Materialpermeabilität
Die magnetische Permeabilität ist ein Maß für die Durchlässigkeit von Materie für magnetische Felder (analog der elektrischen Leitfähigkeit zu elektrischen Feldern). So weisen beispielsweise ferritische oder martensitische Stähle eine gute magnetische Permeabilität auf, während bei austenitischen Stählen das Gegenteil der Fall ist. Da die Funktionalität und der Wirkungsgrad zum Beispiel von Elektromotoren stark von der magnetischen Permeabilität beeinflusst wird, wird die Messung und der Nachweis dieser Materialeigenschaft zunehmend wichtiger. Denn manche Komponenten für Elektroantriebe müssen aus Werkstoffen bestehen, die leicht magnetisierbar sind, damit das elektromagnetische System schnell und mit möglichst geringem Energieaufwand arbeiten kann.
Es gibt aber auch Anwendungen, bei denen die Materialien keine oder nur eine sehr geringe Permeabilität aufweisen dürfen. Zum Beispiel sind zum Einbau in einen Magnet-Resonanz-Tomographen (MRT) nur amagnetische Komponenten geeignet, damit diese das entstehende Magnetfeld nicht beeinflussen. Aus demselben Grund dürfen auch Implantate nur aus amagnetischen Materialien bestehen, falls ein Patient ein MRT benötigt. Um die Permeabilität eines Materials zu messen gibt es zwei Möglichkeiten:
- AC Permeabilitätsmessung, d.h. die Messung der magnetischen Permeabilität bei Wechselfeldern.
- DC Permeabilitätsmessung, d.h. die Messung der magnetischen Permeabilität durch eine sukzessive Erhöhung des magnetischen Flusses.
Die Permeabilität ist definiert als die Steigung der Kennlinie in einer B/H Messkurve. Voraussetzung ist ein geschlossener Magnetkreis wie er zum Beispiel bei einer Ringproben DC oder Epsteinrahmen AC Messungen vorliegen. Die Permeabilität bzw. die B/H Messkurve kann so durch Einsatz einer Primärspule (misst H-Feld) und Sekundärspule (misst B-Feld) aufgenommen werden. Die Beziehung zwischen dem eingeprägten Strom und der gemessenen Induktionsspannung als Integral stellt die B/H Kennlinie dar und deren Steigung die magnetische Permeabilität.
Mit der Primärspule wird dazu ein definiertes Feld mit einem eingeprägten Strom erzeugt. Das vom Strom induzierte Magnetfeld H generiert im Prüfteil einen magnetischen Fluss. Parallel zur Primärspule ist die Sekundärspule angeordnet. Der magnetische Fluss bewirkt im Prüfteil eine Induktionsspannung.
Die große Herausforderung dieser Messmethode besteht darin, die Beziehung zwischen B/H möglichst entsprechend der vorliegenden Bauteilgeometrie zu realisieren, um verschiedene Formen von Prüfstücken zu messen. Dafür ist es notwendig ein Modell zu entwickeln, welches man von einem Normstück auf die Geometrie des Prüfstückes anwenden kann. In der Regel wird in der Industrie eine DC Messung durchgeführt, die AC Messung ist allerdings interessant für Anwendungen, deren Arbeitsfrequenzen sich in einem höheren kHz Bereich befinden.
5. Prüfung von Hardspots, Softspots und Lunker
Sogenannte Hardspots oder Softspots sind lokale Gefügeunterschiede (Inhomogenitäten), die aufgrund des Fertigungsprozesses entstehen. Sie machen sich durch unterschiedliche Härten, Leitfähigkeit oder Materialkompositionen bemerkbar. Zum Auffinden dieser Inhomogenitäten kommen dieselben Methoden wie bei der Materialverwechslungs- oder der Härteprüfung zum Einsatz. Während dort das Ergebnis über das gesamte Bauteil gemittelt wird, ist es in diesem Fall notwendig, das Bauteil genau zu scannen. Der Aufbau zur Prüfung auf Hardspots ist daher analog zur klassischen Rissprüfung mit Wirbelstrom. Auch die Lunkerbildung beschränkt sich auf einen sehr lokalen Bereich. Zur Auffindung wird typischerweise die Ultraschallprüfung genutzt. Auch dafür ist es notwendig, den Ultraschallkopf entlang des Prüfstückes zu bewegen oder analog das Prüfstück entlang des Ultraschallkopfes. Die Methodik dazu wird im Bereich der Rissprüfmethoden erklärt.
Wie kann eine typische Materialprüfung aussehen?
Für Prüfaufgaben im Bereich der Material- und Härteprüfung hat FOERSTER ein spezielles Prüfgerät entwickelt. Das MAGNATEST D ist insbesondere für Serienanwendungen geeignet. Die Hardware des Prüfgerätes ist so ausgelegt, dass mehrere Bauteile innerhalb kürzester Zeit geprüft werden können, d.h. es können hohe Taktraten realisiert werden. Für diesen Prüfaufbau benötigt es eine Prüfspule, ein Prüfgerät und die Bauteilzuführung. Die Bauteilzuführung kann sowohl manuell als auch automatisch erfolgen. Die Art der Bauteilzuführung sowie die Höhe des Automatisierungsgrad beeinflussen die Anschaffungskosten eines Prüfsystems.
In der Regel ist das MAGNATEST D so konfiguriert, dass es automatisch erkennt, wenn ein Prüfling in die Spule eingeführt wird. Mit der Bauteilerkennung startet dann die eigentliche Prüfung sowie die anschließende Gut- / Schlecht-Sortierung. Die Prüfergebnisse werden als I/O-Signal und als direkte Information auf dem Bildschirm zurückgeliefert. Die Prüfung findet entweder mit einer Durchlaufspule statt, die der Prüfling durchläuft, oder mit feststehenden Tastsonden, an die der Prüfling manuell oder automatisch herangeführt wird. Das MAGNATEST D kann natürlich auch direkt in die Produktion integriert werden. So kann idealerweise direkt nach dem Veredelungsprozess überprüft werden, ob dieser korrekt verlief. Im Falle eines fehlerhaften Prozesses und daraus folgenden Produktionsausschusses können durch die zeitnahe Rückmeldung rechtzeitig Gegenmaßnahmen ergriffen werden.
Regressionsanalyse in der Härteprüfung
Die Messwerte bei der zerstörungsfreien Härteprüfung mit einem Wirbelstromgerät sind dimensionslose Werte, die eine Aussage über den Real- und Imaginärteil der Signale in der Sekundärmessspule beinhalten. Durch eine Korrelationsanalyse, d.h. eine Regression von einem physikalischen Messverfahren der absoluten Härte mit den dimensionslosen Werten der Wirbelstromprüfung, können diese parametriert werden, was dazu führt, dass man das Prüfgerät im Serienprozess als Messgerät einsetzen kann. Wie diese Regressionsanalyse aussieht und umgesetzt werden kann wird in einem anderen Themenkomplex behandelt.
Share this
Vielleicht gefällt Ihnen auch
Verwandte Artikel
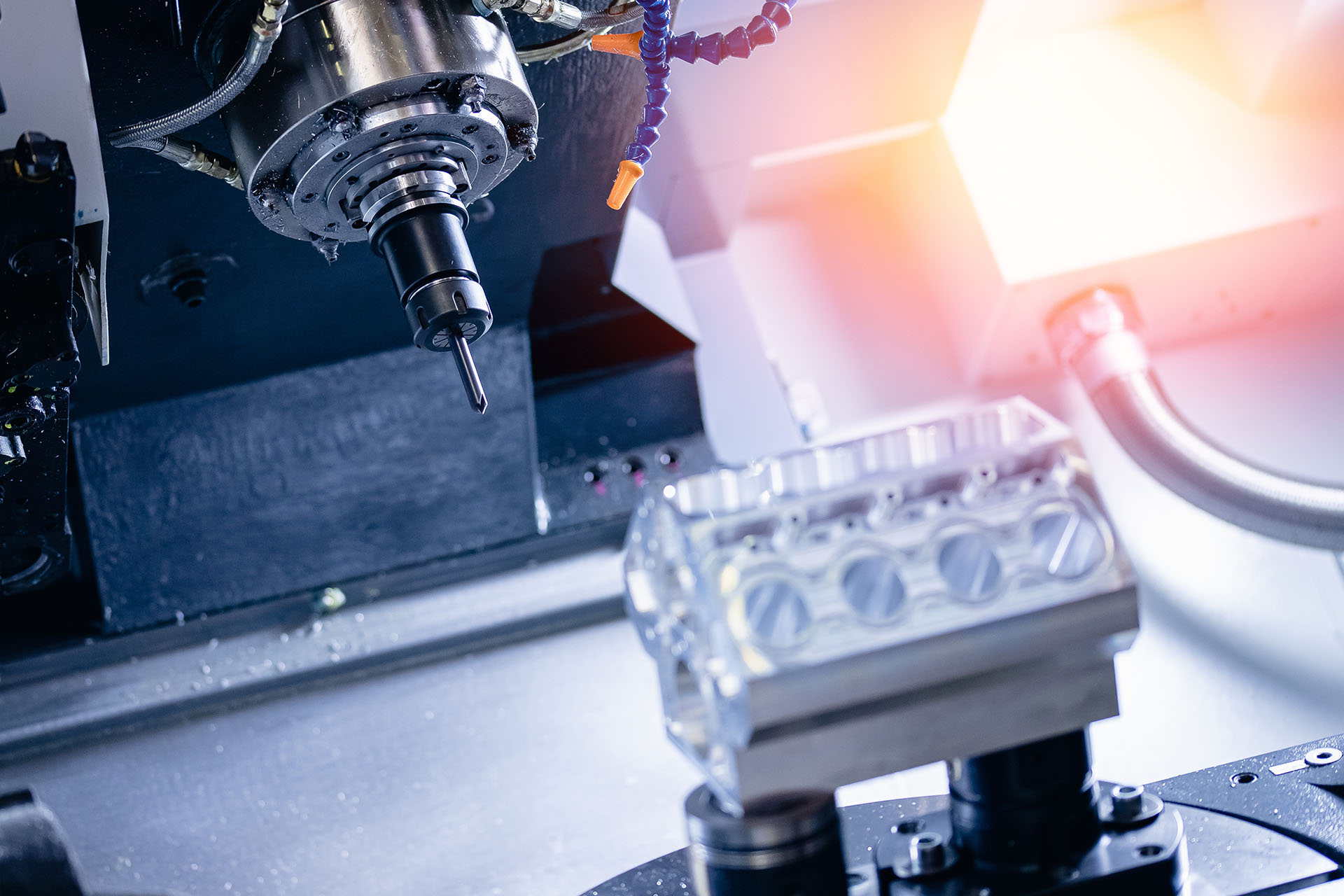
Automatisierte Prüfung von Zylinderlaufbuchsen mittels Wirbelstrom
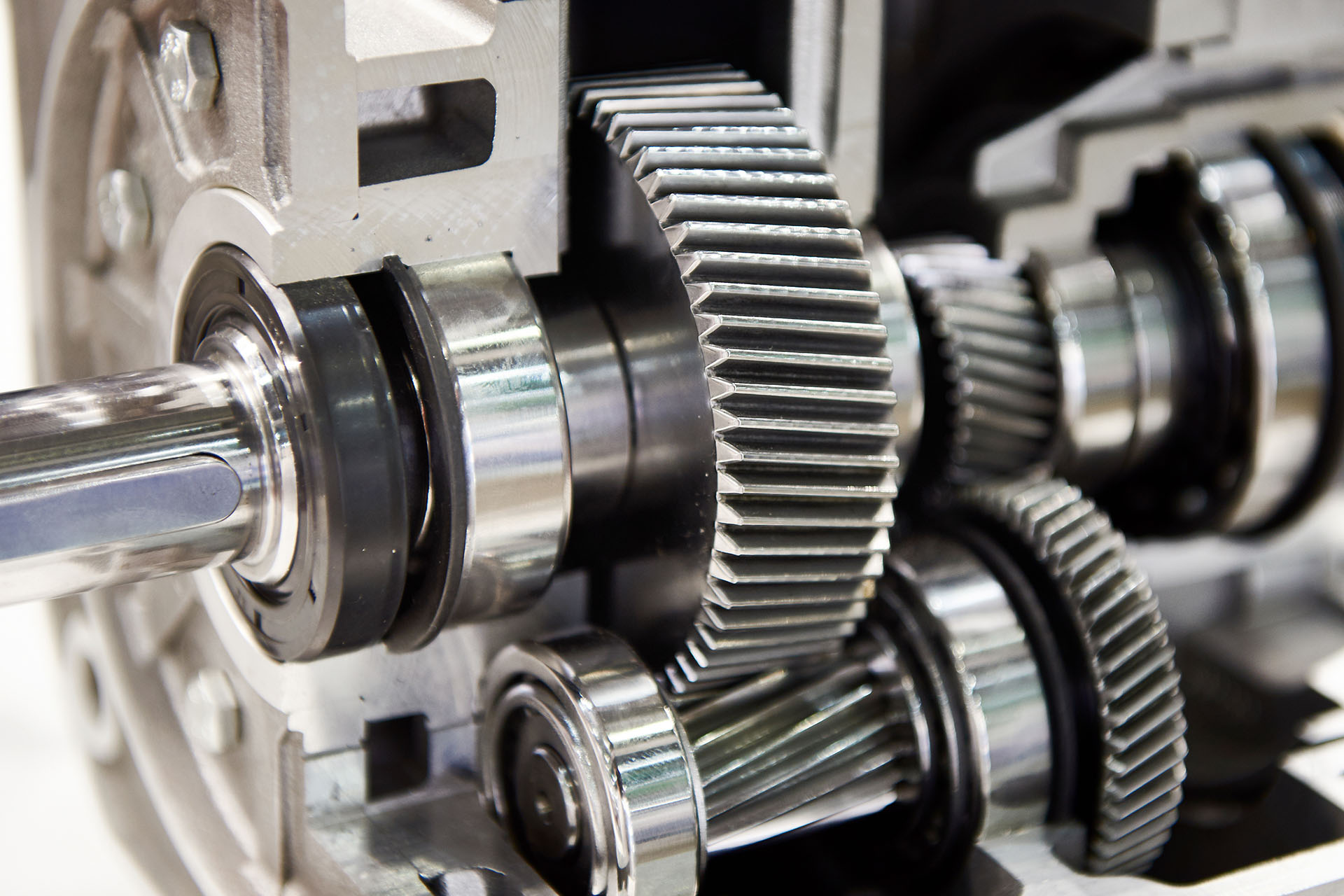
Automatisierte 100% Riss- und Wärmebehandlungsprüfung von Getriebewellen
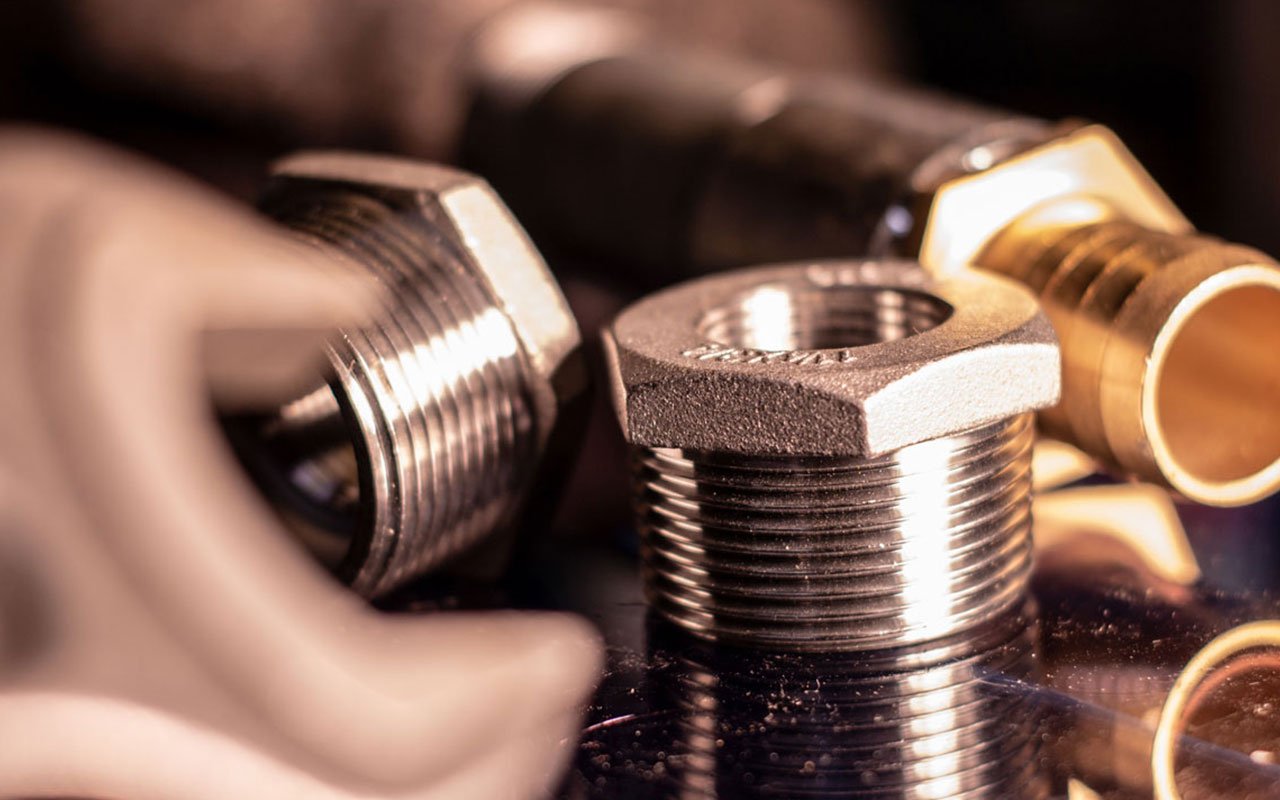