Los errores más comunes en las pruebas de fisuras... ¡y su solución!
Siempre que se utilicen componentes relevantes para la seguridad críticos para el funcionamiento, la comprobación de grietas es esencial. Puede detectar defectos de material en una fase temprana y evitar que empeoren.
Hay varios métodos disponibles para la comprobación no destructiva de grietas. Los métodos más comunes son:
- Inspección visual.
- Inspección por líquidos penetrantes.
- Inspección termográfica.
- Inspección por partículas magnéticas (fundente).
- Pruebas ultrasónicas.
- Pruebas por corrientes parásitas.
Cada uno de estos métodos tiene sus ventajas e inconvenientes. En función de la tarea de ensayo, cada uno de estos métodos de ensayo no destructivos tiene su razón de ser.
¿Cuáles son los errores en las pruebas de grietas?
Sea cual sea el método utilizado, para que la prueba de grietas tenga éxito es necesario conocer la siguiente información:
1. La selección del método de ensayo. 2. La especificación de los defectos. 3. Proceso estable. 4. La colocación de la pieza de ensayo. 5. Magnetización. |
1. La selección del método de ensayo
Es importante que el defecto a detectar se corresponda con un método de ensayo adecuado. Por ejemplo, las pruebas de corrientes de Foucault tienen una clara ventaja para las grietas superficiales del material, mientras que las pruebas ultrasónicas son preferibles para los defectos volumétricos.
2. Especificación del defecto
Para que los ensayos de grietas sean reproducibles, es importante conocer la especificación del defecto. Si no hay grietas naturales, se pueden introducir grietas artificiales en la pieza de ensayo de acuerdo con las especificaciones del cliente, por ejemplo, mediante erosión. Además, es muy importante que la especificación del defecto pueda detectarse de forma fiable. Las propiedades de la superficie y las condiciones geométricas desempeñan aquí un papel importante.
Así pues, la regla empírica se aplica a las pruebas de corrientes de Foucault:
El tamaño más pequeño de grieta detectable es al menos tres veces la rugosidad de la superficie. Por ejemplo, en un vástago de amortiguador pulido pueden detectarse profundidades de defecto de 0,05 mm, mientras que en los cubos de rueda forjados la detectabilidad de la profundidad de la grieta es de 1-2 mm.
Del mismo modo, es necesario un buen recubrimiento de la superficie para una detección fiable de los defectos en los ensayos por corrientes de Foucault. Los defectos deben ser escaneados durante una exploración de la superficie con una sonda giratoria al menos a dos revoluciones o mejor a tres revoluciones. Esto debe considerarse en función del tamaño del defecto, la anchura de la pista, la velocidad de avance y la velocidad de rotación.
Un cubo de rueda con rodamiento.
3. Proceso estable
En los ensayos dinámicos de grietas, como los ensayos automatizados por corrientes inducidas, la concentricidad desempeña un papel decisivo. Cuanto mejor sea, más estable y fiable será el proceso de detección de un defecto.
Por lo tanto, es importante prestar atención a la alta precisión desde el principio al diseñar el sistema. Hasta cierto punto, las tolerancias de los componentes y las imprecisiones de la máquina en los ensayos de fisuras por corrientes de Foucault pueden compensarse mediante la compensación de distancia.
4. El posicionamiento de la pieza de ensayo
Otro punto importante en el diseño del sistema es el tema del posicionamiento. Un posicionamiento preciso y reproducible es esencial para que el ensayo (por corrientes de Foucault) tenga sentido.
Si se concede gran importancia a estos dos puntos -proceso de producción estable y posicionamiento correcto- desde el principio, muchos problemas ni siquiera se producirán en el proceso de ensayo posterior.
5. Magnetización
La magnetización local puede provocar problemas no sólo en los procesos posteriores, sino también durante el propio ensayo de grietas. Por ejemplo, un punto magnético puede generar un aumento del ruido o incluso una señal similar a una grieta durante la inspección. Esto no sólo afecta a la relación señal/ruido, que es importante para realizar pruebas fiables, sino que también aumenta el riesgo de pseudo rechazos.
Esto puede evitarse mediante la desmagnetización. Para ello, FOERSTER ofrece la potente unidad de desmagnetización ZMAG.
FOERSTER se complace en apoyarle con nuestro asesoramiento técnico, estudios de viabilidad y consejos sobre el diseño de sistemas. Gracias a la coordinación conjunta, es posible evitar de antemano un gran número de problemas. Así, nada se interpone en el camino de las pruebas de fisuración con fiabilidad de proceso.
Solución de producto FOERSTER para una desmagnetización potente:
La desmagnetización ZMAG CM le ayuda a garantizar que estas magnetizaciones locales no generen ninguna señal de interferencia durante el ensayo de grietas. El método de impulsos utilizado permite una gran profundidad de penetración para desmagnetizar los componentes de forma eficaz y rápida. Con ZMAG CM obtendrá todas las soluciones a la vez.
Somos el interlocutor adecuado para usted cuando se trata de especificaciones de defectos. Si lo desea, también podemos producir defectos artificiales para usted. Estos pueden erosionarse, medirse y registrarse en FOERSTER y servir así de base para un estudio de viabilidad.
Share this
You May Also Like
These Related Stories
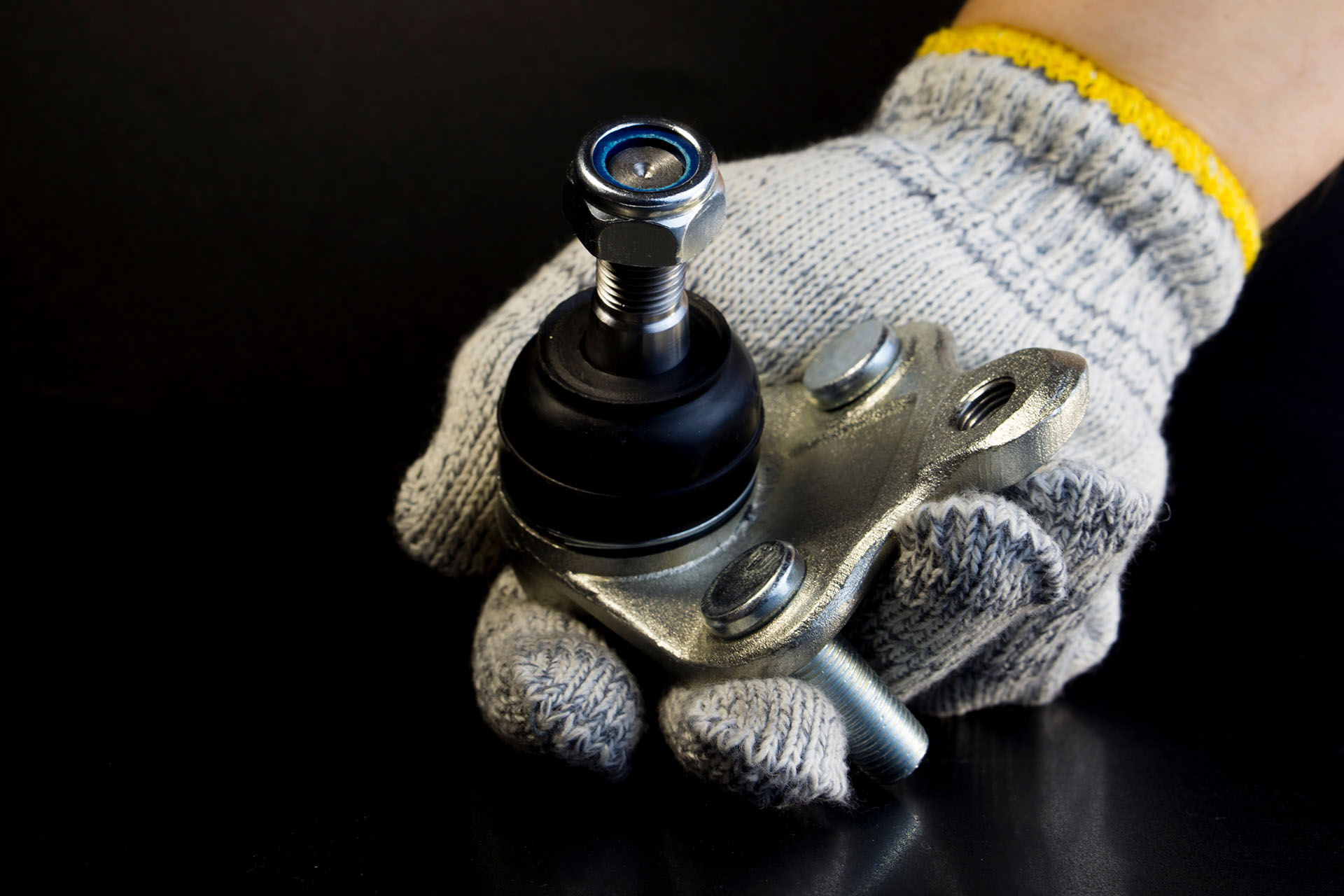
Pruebas automatizadas de grietas en esferas de rótulas
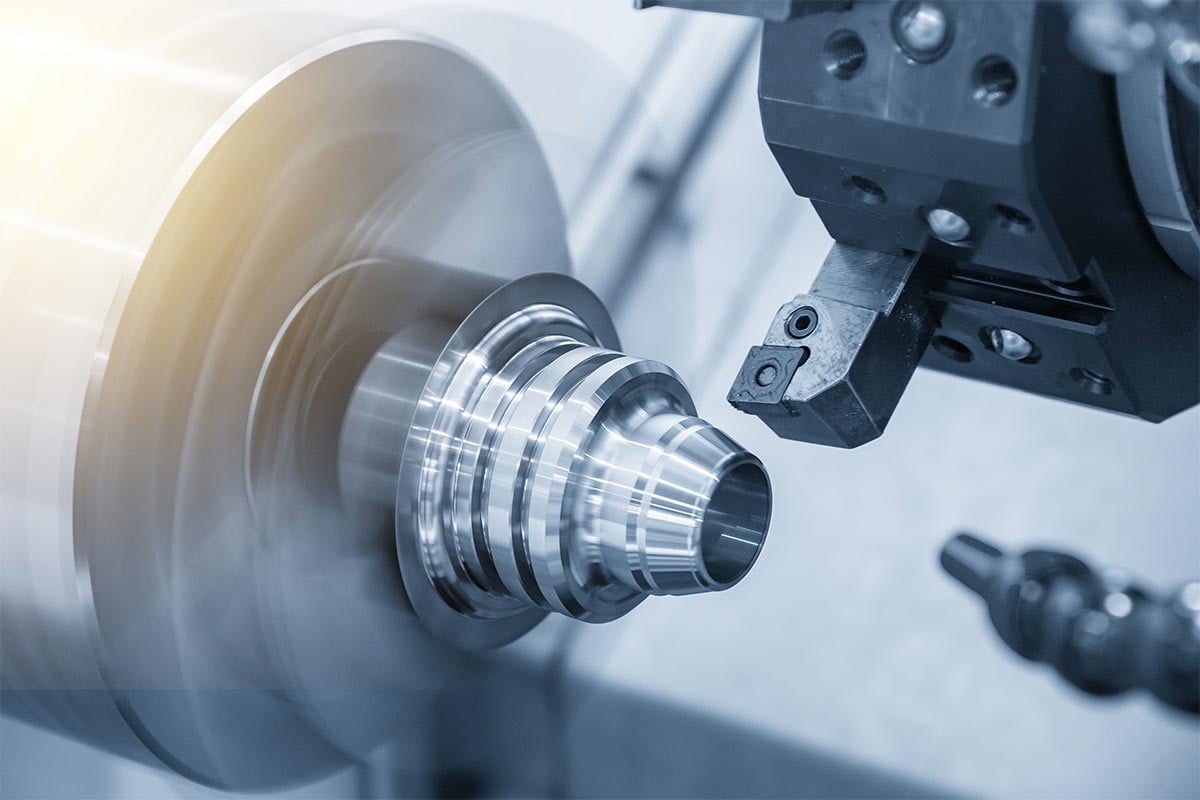
Pruebas de grietas: ¿Cómo configuro correctamente mis filtros y frecuencias?
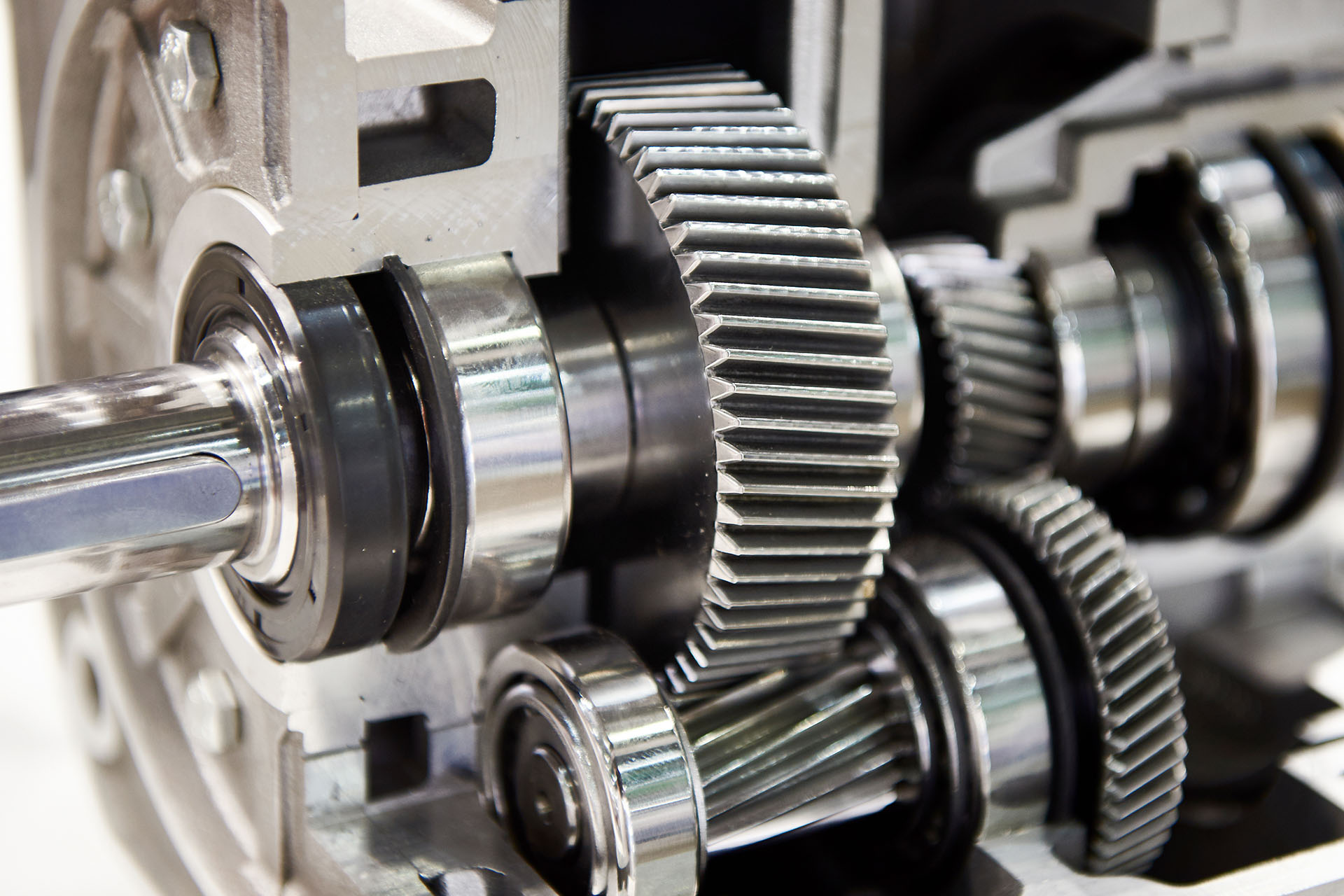