The most common mistakes in crack testing - and their solution!
Wherever safety-relevant and function-critical components are used, crack testing is essential. It can detect material defects at an early stage and prevent worse.
There are various methods available for non-destructive crack testing. The most common methods are:
- Visual inspection
- Dye penetrant inspection
- Thermographic testing
- Magnetic particle inspection (fluxing)
- Ultrasonic testing
- Eddy current testing
Each of these methods has its advantages and disadvantages. Depending on the test task, each of these non-destructive testing methods has its reason for existence.
Click here to know more about these six important methods in non-destructive crack testing.
What are the mistakes in crack testing?
Whichever method is used, the following important information must be known for successful crack testing.
1. The selection of testing method 2. Defect specification 3. Stable process 4. The positioning of the test part 5. Magnetization |
1. The selection of testing method
It is important that the defect to be detected is matched to an appropriate test method. For example, eddy current testing has a clear advantage for surface-open material cracks, while ultrasonic testing is preferred for volumetric defects.
2. Defect specification
For reproducible crack testing, it is important that you know the defect specification. Where no natural cracks are present, artificial cracks can be introduced into the test part according to the customer's specifications, for example by eroding. In addition, it is of great importance that the defect specification can be reliably detected. The surface properties and geometric conditions play an important role here.
Thus, the rule of thumb applies to eddy current testing:
The smallest detectable crack size is at least three times the surface roughness. For example, defect depths of 0.05 mm can be detected in a polished shock absorber rod, whereas in forged wheel hubs the detectability of the crack depth is 1-2 mm.
Likewise, a good surface cover is necessary for reliable defect detection in eddy current testing. The defects should be hit during a scan of the surface with a rotating probe at least at two, better at three revolutions. This should be considered depending on the defect size, track width, feed rate, and rotational speed.
A wheel hub with bearing
3. Stable process
In dynamic crack testing, such as automated eddy current testing, concentricity plays a decisive role. The better it is, the more stable and process-reliable a defect can be detected. Therefore, it is important to pay attention to high precision right from the start when designing the system. To a certain extent, component tolerances and machine inaccuracies in eddy current crack testing can be compensated for by distance compensation.
4. The positioning of the test part
Another important point in the system design is the topic of positioning. Precise and reproducible positioning is essential for meaningful (eddy current) testing.
If great importance is attached to these two points - stable production process and correct positioning - right from the start, many problems will not even occur in the subsequent testing process.
5. Magnetization
Local magnetization can lead to problems not only in subsequent processes but also during crack testing itself. For example, a magnetic spot can generate increased noise or even a crack-like signal during the inspection. This not only affects the signal-to-noise ratio, which is important for reliable testing but also increases the risk of pseudo-rejects.
This can be prevented by demagnetization. For this purpose, FOERSTER offers the powerful ZMAG demagnetization unit.
FOERSTER is glad to support you with our technical advice, feasibility studies, and tips on system design. Through joint coordination, a large number of problems can be avoided in advance. Thus, nothing stands in the way of crack testing with process reliability.
FOERSTER's product solution for powerful demagnetization
The ZMAG CM demagnetization helps you ensure that these local magnetizations do not generate any interference signals during the crack testing. The pulse method used enables high penetration depth to demagnetize the components effectively and promptly. With ZMAG CM you now receive all solutions at once.
We are the right contact partner for you when it comes to defect specifications. If required, we can also produce artificial defects for you. These can be eroded, measured, and recorded at FOERSTER and thus serve as a basis for a feasibility study.
Share this
You May Also Like
These Related Stories
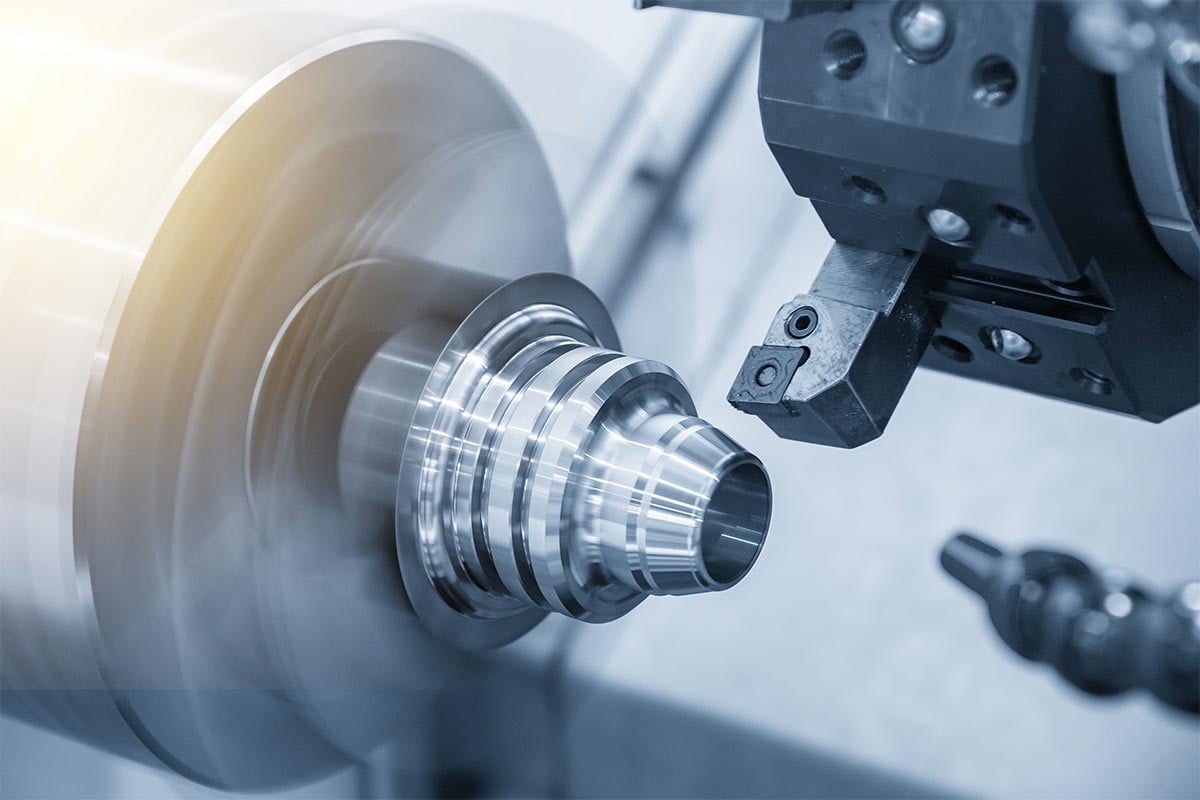
Crack testing: How do I set my filters and frequencies correctly?
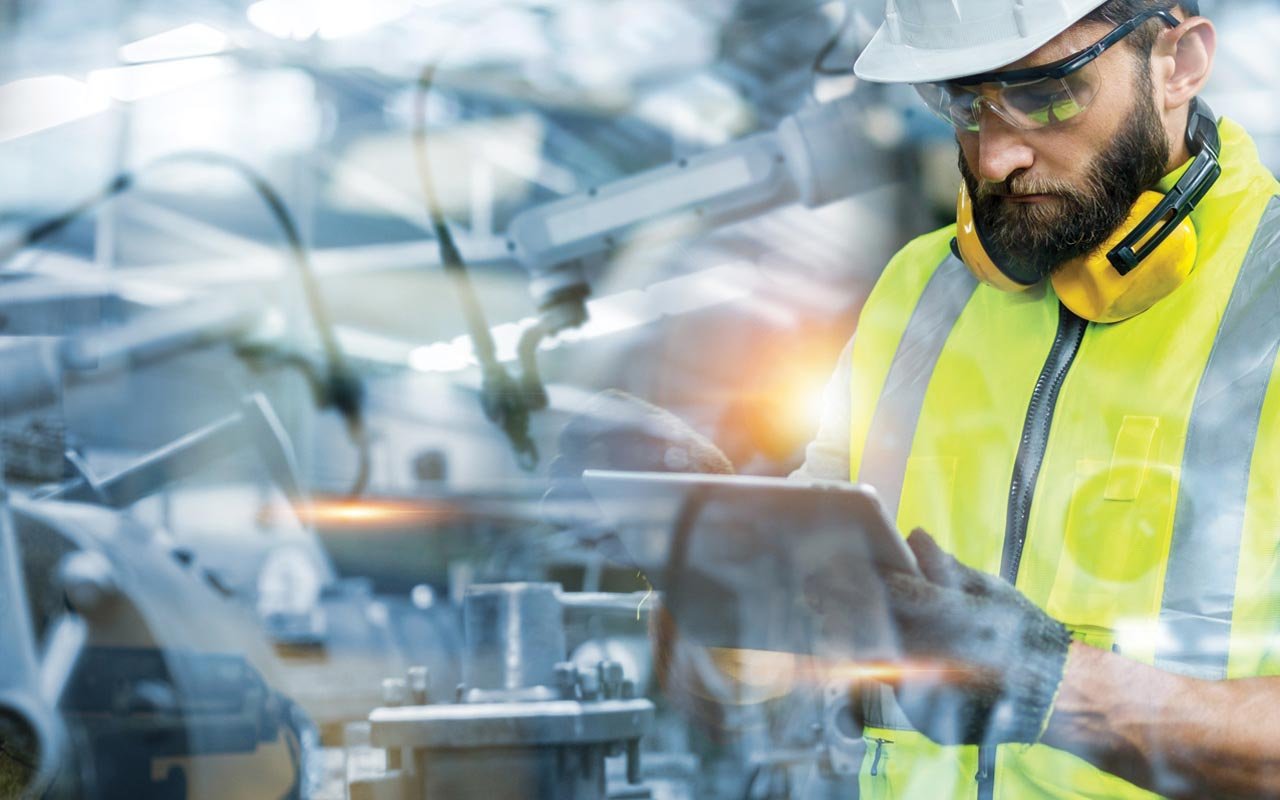
Crack testing: How does an eddy current test instrument work?
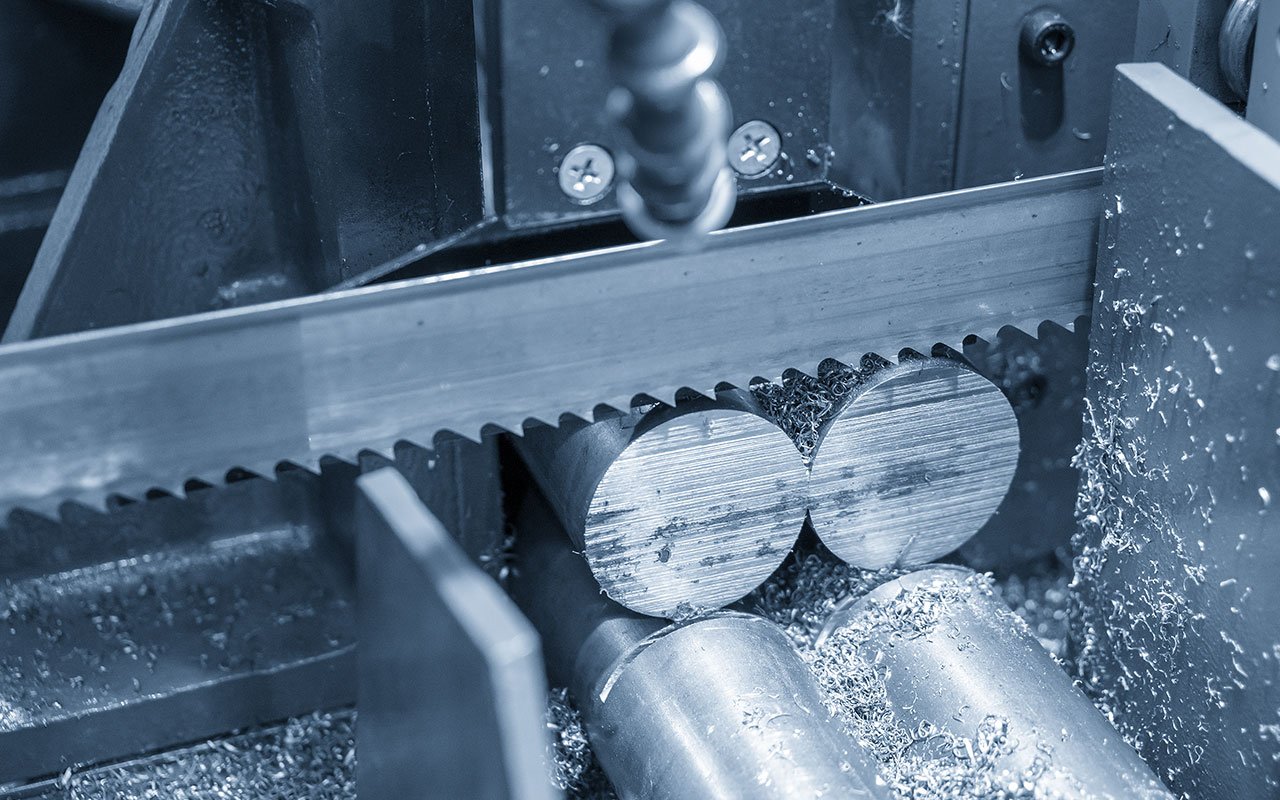