Come funziona un test applicativo nel controllo non distruttivo dei componenti?
Questo blog post descrive come vengono eseguiti i test applicativi sui componenti utilizzando metodi di controllo non distruttivi. L'attenzione si concentra sull'individuazione di problemi di qualità come cricche e difetti di durezza. L'articolo fornisce una panoramica della metodologia del processo di prova a correnti parassite e sottolinea l'importanza della selezione dei sensori, delle frequenze di prova e dei test microstrutturali. Infine, vengono discussi i rapporti applicativi.
Nel processo di produzione dei componenti metallici possono verificarsi problemi di qualità come cricche o difetti di durezza. Individuarli in tempo ed eliminare i componenti difettosi è importante per garantire che il prodotto finale sia privo di difetti.
Questi difetti del materiale possono essere rilevati con il metodo non distruttivo dei test a correnti parassite. Utilizzando interazioni elettromagnetiche ad alta o bassa frequenza, è possibile rilevare e valutare manualmente o automaticamente, a seconda dei requisiti, difetti quali cricche, pori o differenze strutturali. Per individuare i difetti, il metodo a correnti indotte si basa sul confronto con difetti di riferimento. Pertanto, in uno studio di fattibilità durante le prove di applicazione nel nostro laboratorio applicativo, il risultato ottimale viene determinato sulla base dei campioni forniti dal cliente, sia per quanto riguarda l'attrezzatura tecnica che i parametri di impostazione corretti. A questo scopo, FOERSTER dispone di uno speciale team di ingegneri che a stretto contatto con sviluppatori che hanno una profonda conoscenza delle applicazioni. I risultati vengono resi disponibili in un rapporto dettagliato e discussi personalmente su richiesta.
Le frequenze di test, i parametri di impostazione, le soglie di errore e le configurazioni dei sensori vengono determinate nei test applicativi. Tra le altre cose, le proprietà del materiale, la finitura superficiale e le caratteristiche dei difetti ricoprono un ruolo fondamentale nella riuscita del test.
Nella produzione odierna, un adeguato controllo della qualità è essenziale. Il metodo del test a correnti parassite può fornire informazioni preziose sulla qualità dei vostri componenti. Rilevando precocemente cricche o difetti di durezza, il produttore può intervenire tempestivamente nel processo di produzione, effettuare ottimizzazioni e modificare i processi di lavorazione per ottenere alla fine prodotti di alta qualità.
Casi d'uso che possono essere analizzati nel laboratorio applicativo.
Durante il collaudo dei componenti, spesso entrano in gioco due test importanti. L'ispezione dei difetti superficiali e l'ispezione della microstruttura. Per un test affidabile, è necessario selezionare i parametri di impostazione ottimali e i sensori giusti. Con l'aiuto di vari esempi, vorremmo illustrare la procedura necessaria nel laboratorio applicativo:
Scenario 1: Ispezione di difetti superficiali come crepe
Velocità di rotazione: il metodo a correnti parassite è adatto a componenti a simmetria di rotazione, poiché la rotazione viene utilizzata per rilevare difetti come le cricche. Per questo motivo, nei test applicativi presso il nostro laboratorio, i componenti da esaminare vengono bloccati in un tornio. In questo modo si determina la velocità superficiale ottimale, che facilita il rilevamento dei difetti superficiali. Analizzando attentamente le reazioni del campo magnetico durante la rotazione, è possibile determinare con precisione la posizione esatta e la gravità delle cricche. Trasferito in produzione, ciò consente di adottare rapidamente misure correttive in caso di difetti di qualità.
Selezione del sensore: Un'altra importante ruolo nell'ispezione è ricoperto dal sensore. A seconda del componente e dell'applicazione, FOERSTER offre una vasta scelta di sensori differenti. Per questo motivo, negli studi di fattibilità vengono utilizzati molteplici sensori, selezionati in base a fattori quali la conduttività del materiale, le proprietà della superficie e le dimensioni e la posizione delle aree da ispezionare. A seconda dell'applicazione, si utilizzano ad esempio sensori angolati, sonde a foro o anche sonde flessibili, sempre con l'obiettivo di rilevare in modo affidabile i difetti superficiali richiesti.
Parametri di test e ottimizzazione: Una volta selezionata la velocità di rotazione corretta e individuato il sensore appropriato, i parametri di prova devono essere impostati e ottimizzati correttamente sul dispositivo. Ciò include la selezione della corrente di eccitazione corretta, la determinazione delle frequenze di prova e, se necessario, l'impostazione dei filtri passa-alto e passa-basso appropriati. Inoltre, vengono definite le soglie di guasto e altri parametri vengono adattati all'applicazione, cioè alle proprietà specifiche del materiale e alle caratteristiche del guasto.
In base a questo studio di fattibilità, viene elaborato e discusso con il cliente il set-up ottimale per il processo di test in linea o offline. Per saperne di più, consultate la sezione "Rapporto di applicazione e comunicazione con il cliente".
Scenario 2: test di microstruttura per determinare le proprietà del materiale
Miscelazione di materiali: Nonostante l'estrema cautela, nel processo di produzione possono verificarsi miscele di materiali. Questi possono causare notevoli danni economici agli utensili della linea di produzione e persino danni conseguenti agli utenti. Per evitare questo inconveniente, si può ricorrere ai test di microstruttura a induzione magnetica. Poiché la curva di isteresi è fortemente influenzata da parametri tecnologici quali la durezza, i costituenti della lega e la microstruttura, le proprietà magnetiche del materiale possono essere utilizzate per determinare questi parametri in modo particolarmente efficace, consentendo di eliminare i componenti i cui parametri non sono corretti. Nel laboratorio applicativo, i valori delle caratteristiche magnetiche vengono determinati sulla base di pezzi di riferimento e vengono formati dei limiti di selezione, in modo che i componenti possano essere testati nel processo di produzione automatizzato e quindi selezionati automaticamente.
Selezione del sensore: Per le prove di microstruttura e durezza automatizzate è disponibile un'ampia gamma di sensori che consentono di eseguire test ottimali. Ad esempio, esistono sensori speciali per il controllo della durezza dei bordi dei componenti lavorati. I sensori vengono sempre selezionati in base alla geometria e alla posizione del pezzo per fornire risultati precisi.
Valutazione armonica ad alte prestazioni: è risaputo che le condizioni di laboratorio non possano essere mantenute nel processo di produzione. La valutazione armonica ad alte prestazioni viene utilizzata per compensare, ad esempio, le influenze della temperatura e del lotto, l'alimentazione eccentrica dei componenti e le tolleranze dei componenti. In questo caso, la curva di magnetizzazione viene scomposta in onda fondamentale e armoniche (multipli dell'onda fondamentale) mediante una trasformazione di Fourier. Lo spettro di frequenza comprende tutte le frequenze dispari, cioè f1 (fondamentale), f3, f5, f7, ecc. Valutando le armoniche, si possono ottenere ulteriori informazioni sulle proprietà del materiale in esame. In questo modo si riduce al minimo l'influenza di fattori esterni sui risultati del test.
Rapporto di applicazione e comunicazione con i clienti
Al termine delle prove applicative e degli studi di fattibilità, l'ingegnere applicativo prepara una relazione completa che documenta le procedure di prova, i risultati e le raccomandazioni. Questo rapporto fornisce informazioni dettagliate sulla qualità dei pezzi lavorati, nonché raccomandazioni su come il controllo qualità automatizzato potrebbe funzionare nel processo. Sulla base di questo rapporto, è possibile sviluppare, in collaborazione con i nostri reparti di vendita e di progettazione, una soluzione di ispezione appropriata per il vostro processo. Le possibilità spaziano da celle o linee di prova automatizzate direttamente nel vostro processo produttivo a linee di prova offline o a soluzioni per il controllo di campioni casuali. Insieme a voi, determineremo la soluzione ottimale per controllare e valutare oggettivamente la qualità dei vostri componenti. Naturalmente, tutti i risultati dei test vengono registrati in protocolli di prova automatici, in modo che possiate dimostrarne la qualità.
Prove di applicazione: l'inizio della nostra collaborazione
Avete problemi di qualità nella vostra produzione e desiderate risolvere il problema? Il primo passo è rappresentato dai nostri approfonditi test applicativi e studi di fattibilità, in cui rendiamo visibili i vostri problemi e sviluppiamo insieme a voi una soluzione per valutare la qualità dei vostri componenti in modo automatico e oggettivo.
I test approfonditi sono necessari per mettere a punto un sistema di prova su misura per la vostra applicazione. Solo una perfetta interazione tra i parametri di prova, la giusta attrezzatura che tenga conto delle proprietà del materiale e dei difetti e le condizioni di processo, permette di costruire un sistema di prova affidabile e sensibile. I nostri test applicativi forniscono già preziose conoscenze sul vostro processo produttivo. Questo ci permette di individuare i processi produttivi difettosi e di avviare miglioramenti del processo.
Rapporti completi sulle applicazioni e una comunicazione efficace sono fondamentali per condividere risultati, raccomandazioni e soluzioni. Per questo motivo, ci impegniamo a trovare una soluzione di test ottimale per ogni specifica applicazione in un confronto aperto con i nostri clienti.
Le nostre apparecchiature di prova hanno già dato prova di sé per decenni e rendono visibile la qualità in molti settori. Tra questi, i sistemi di prova STATOGRAPH CM/CM+ 6.470 per il rilevamento di cricche, pori e altri difetti superficiali, nonché i sistemi MAGNATEST TCL e MAGNATEST D per le prove di durezza e microstruttura.
Se anche voi volete saperne di più, prenotate oggi stesso un appuntamento con il nostro laboratorio applicativo per contribuire ad elevare la qualità dei vostri prodotti.
Share this
You May Also Like
These Related Stories
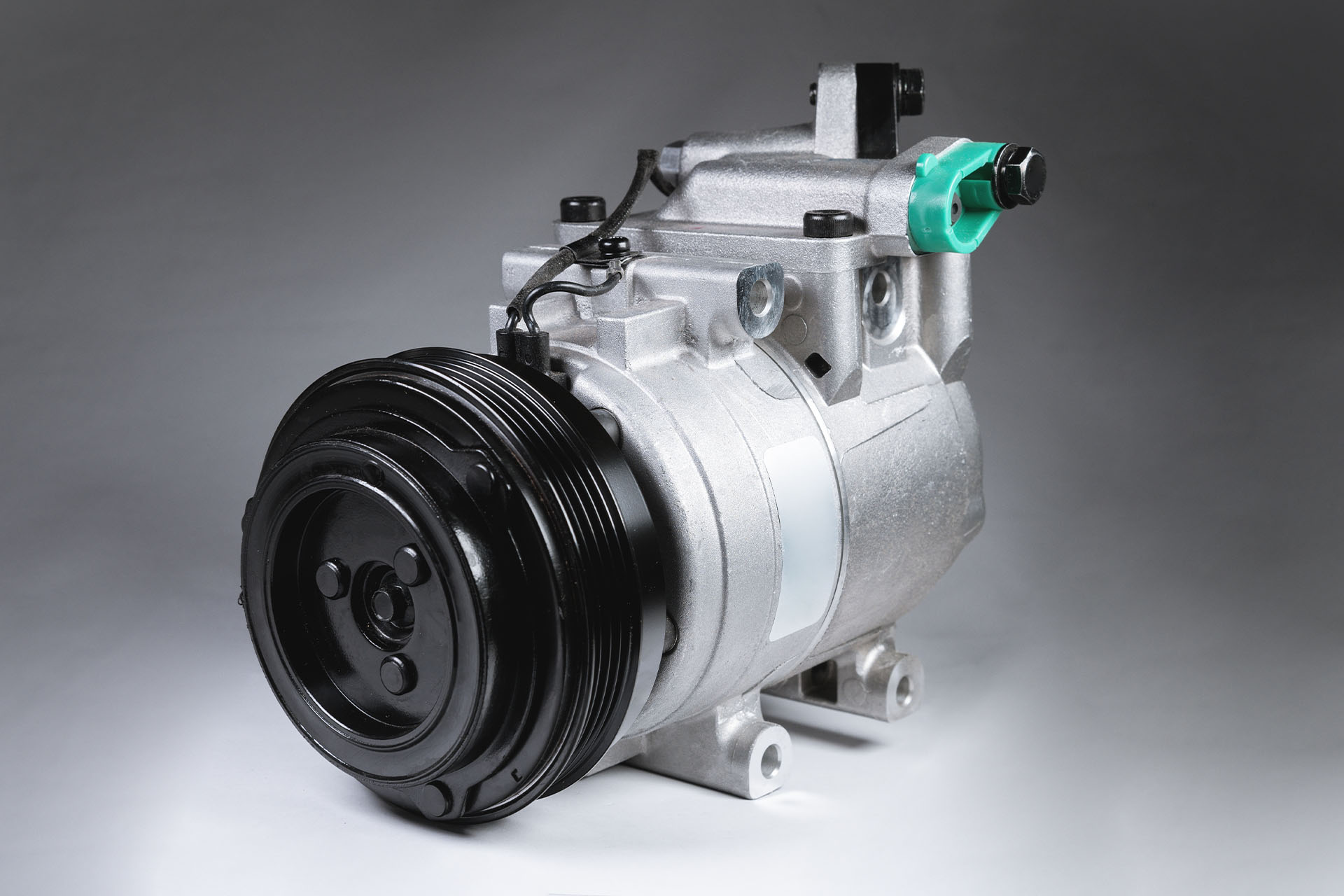
Ispezione del piatto oscillante fuso del compressore del condizionatore d'aria dell'automobile
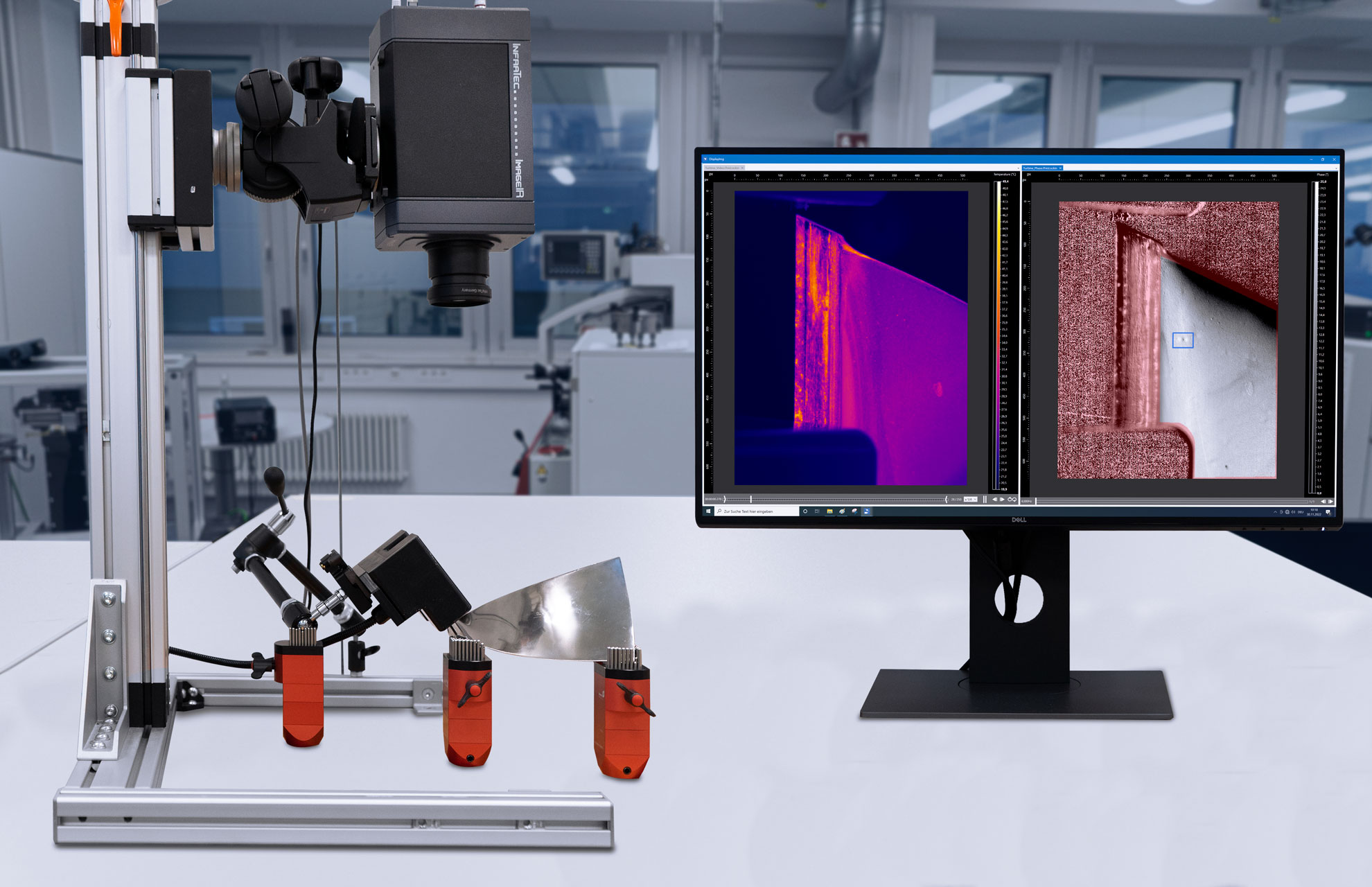
Termografia a induzione per il collaudo dei componenti - Una nuova soluzione per l'ispezione automatizzata di superfici complesse
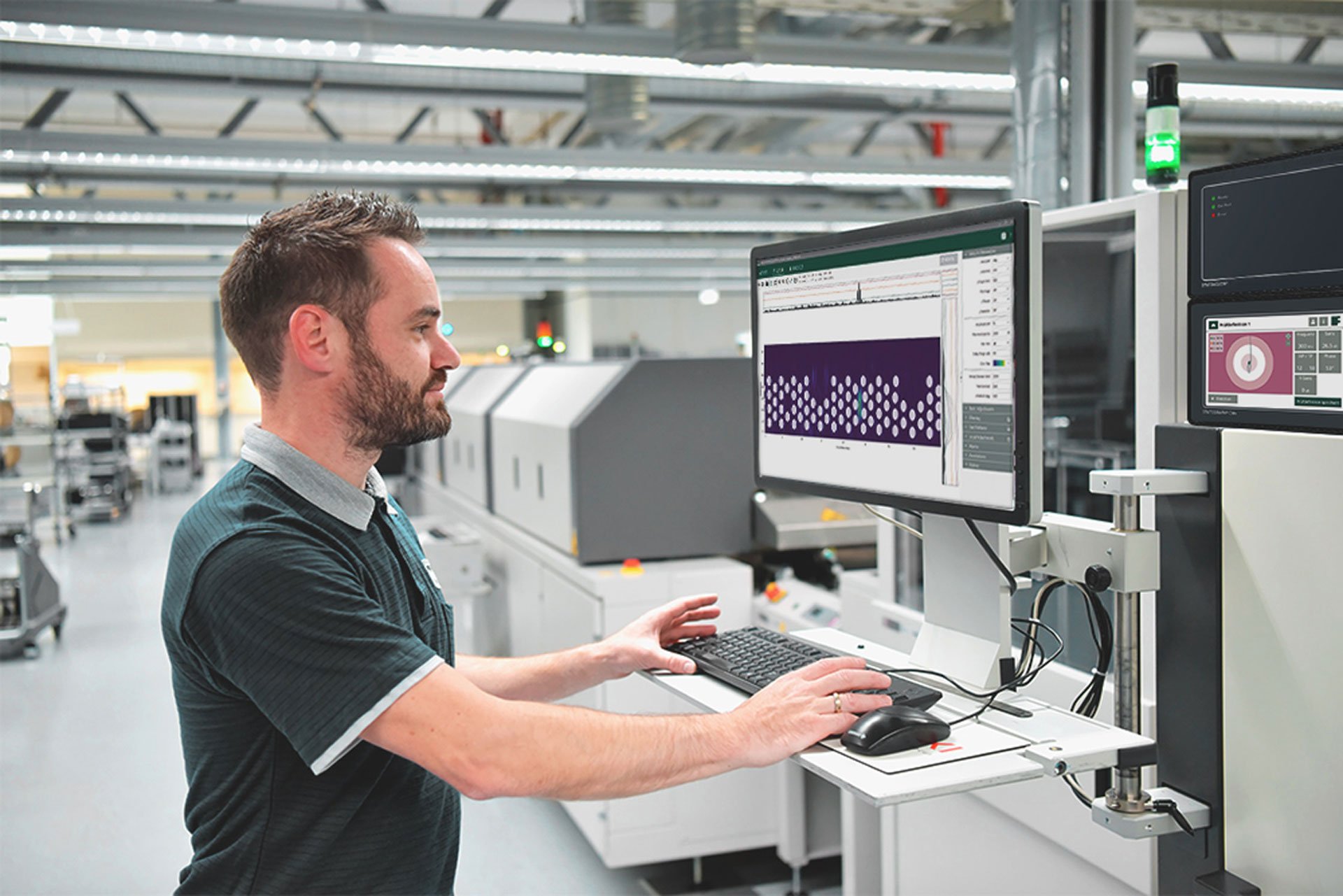