Optimizing Copper Conductivity Testing: Temperature Correction Techniques
Conductivity is the ability of a material to conduct electric current, and assessing the electrical properties of materials like copper is essential. Because of its conductive nature, copper is used widely in industries such as electronics and construction. Testing for conductivity can aid in material identification, quality control, heat treatment verification, fatigue monitoring. However, temperature variations can significantly impact measurement accuracy. This blog explores the importance of conductivity testing, the role of temperature in these measurements, and practical temperature correction techniques to ensure reliable results in the real world.
Why is accurate conductivity testing important for copper?
Put simply, conductivity is vital to every stage of copper production. From verification of the raw material, to inspecting the finished alloy to make sure it will work as intended. Ideally, this test would be conducted in a non-destructive manner, such as eddy current. Accurate conductivity testing ensures that electrical components and systems perform reliably, which is crucial in applications ranging from small electronic devices to large-scale power grids. Beyond quality and safety considerations, there is a financial cost to improper testing. An unaccounted for 10-degree temperature difference between the probe and the material can lead to scrapping thousands of pounds of good material, or a customer receiving something that never should have left the dock.
What can cause inaccurate readings?
A conductivity meter, such as the SIGMATEST, is calibrated in a temperature-controlled room using a wide spectrum of reference materials. In an ideal situation outside of a lab, standards would be allowed to rest on the material you are testing until they are the same temperature. This can prove difficult in an industrial setting. A technician may need to test hot billets that have been off the line for minutes, or they might have to test a batch that was left on the floor overnight in January. There is no way to bring the probe and standard to those temperatures in a timely manner, even with the use of an external temperature probe.
Solutions for accurate conductivity testing
Beyond standardizing testing conditions as best you can, we are left with good old-fashioned arithmetic. Copper's resistance changes predictably with temperature, typically around 0.00393 per degree Celsius. By applying this coefficient, one can adjust conductivity measurements to account for temperature variations, ensuring more accurate results. There's a bit more mathematical complexity involved in this process, but the necessary formulas are conveniently integrated into the internal temperature compensation feature of the SIGMATEST 2.070.
To ensure accuracy and improve ease of operation, the integration of temperature sensors is recommended. An external temperature probe was historically used in applications where the test sample would not have severely fluctuating temperatures. The Smart Probe on the SIGMATEST 2.070 can handle ordinary temperature fluctuation that can be expected from the weather and eliminates the need for an external probe. Based on the real example from earlier, technicians have to deal with much more than the weather. You may have to test material that shows wide temperature variations in quick succession.
This has led to some interesting workarounds. In an attempt at standardization, one facility utilized an oven that would heat all of the test samples to the same temperature before testing. Another facility used an operator to take 6 unique measurements on a single test piece, and feeding those six pieces of data to a second operator who would enter it into a computer. From there multiple calculations were utilized, the outputs were averaged and provided manually back to the first operator. These methods can be time and resource intensive. Based in part on stories like this, the SIGMATEST 2.070 has been designed to help easily find a problem before it ruins your day.
The SIGMATEST 2.070 compensates for temperature related electrical conductivity variations. A default temperature coefficient is installed in each instrument. In addition, the user can define a specific temperature coefficient to optimize the results for specific applications. The user defined option truly is the magic bullet when the temperature of the test piece differs from the probe temperature.
For situations such as this you can quickly create, edit, or load different test profiles. These will be stored on the device for future use. This allows you to set a user defined temperature in seconds. In practice, a calibrated infrared thermometer is used quickly take the temperature of the test area. By pressing a few buttons, you can seamlessly incorporate the temperature into your test profile. From here you can test as you normally would and let the device take care of the rest.
Extensive testing has been conducted in our laboratory, demonstrating tangible success in copper foundries and real-world applications
Share this
You May Also Like
These Related Stories
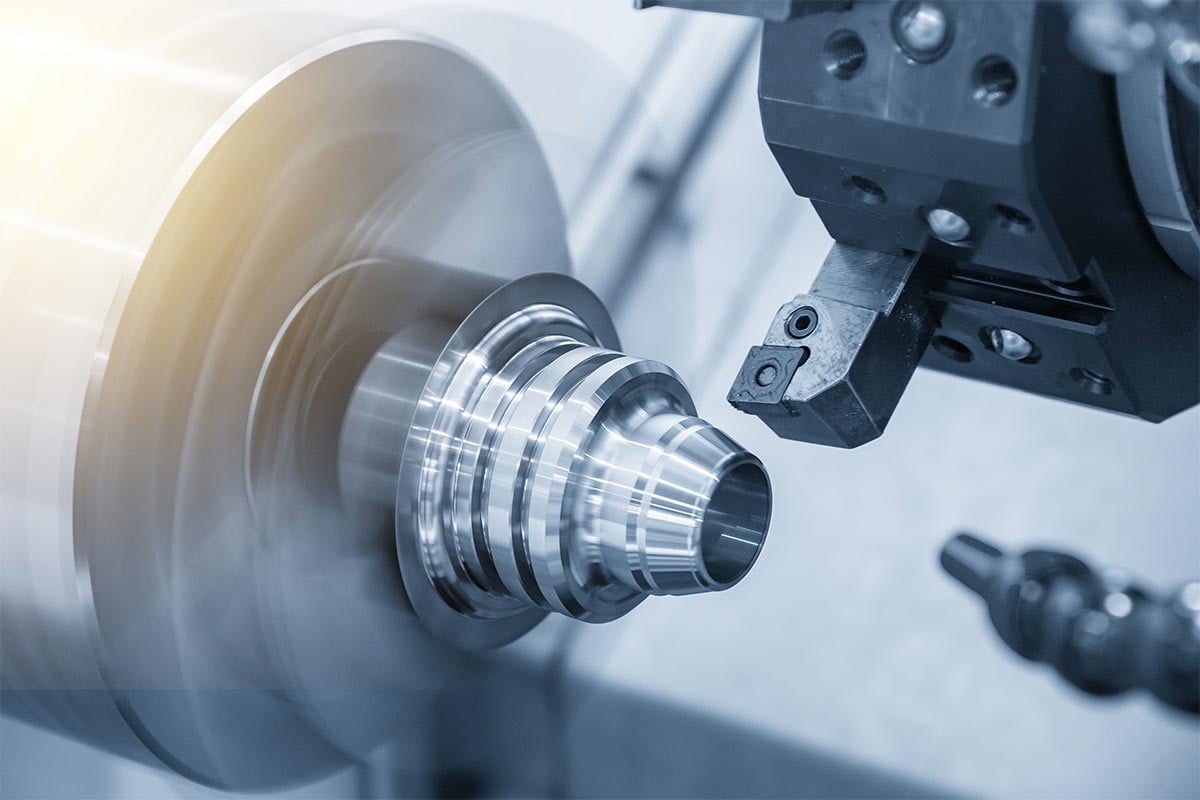
Crack testing: How do I set my filters and frequencies correctly?
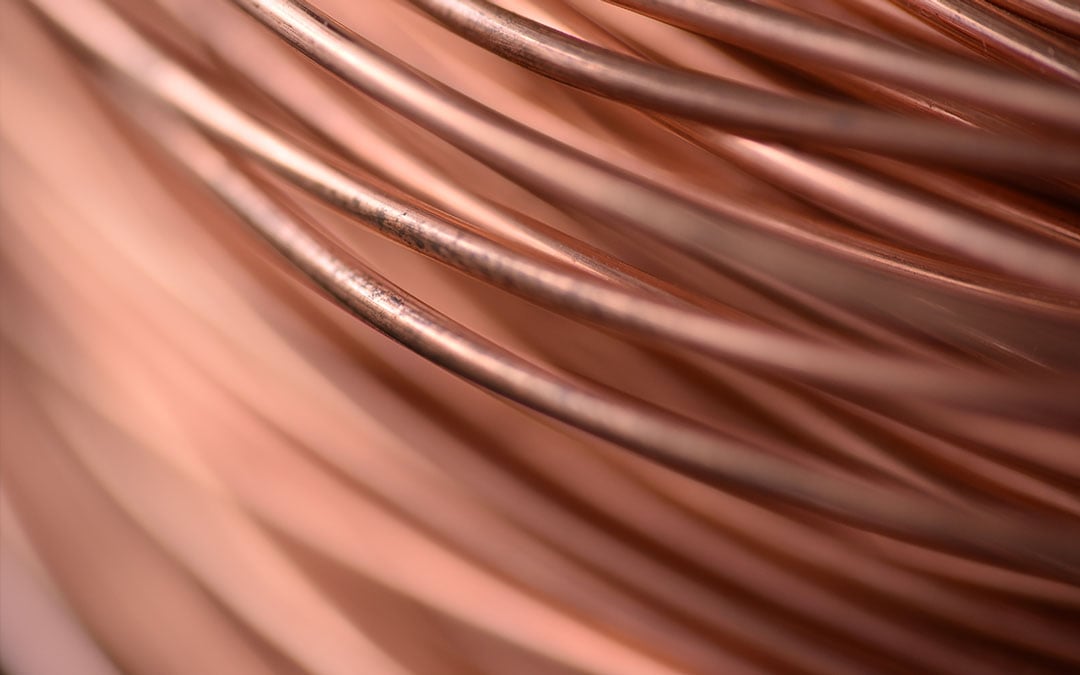
Conductivity measurement of metallic materials
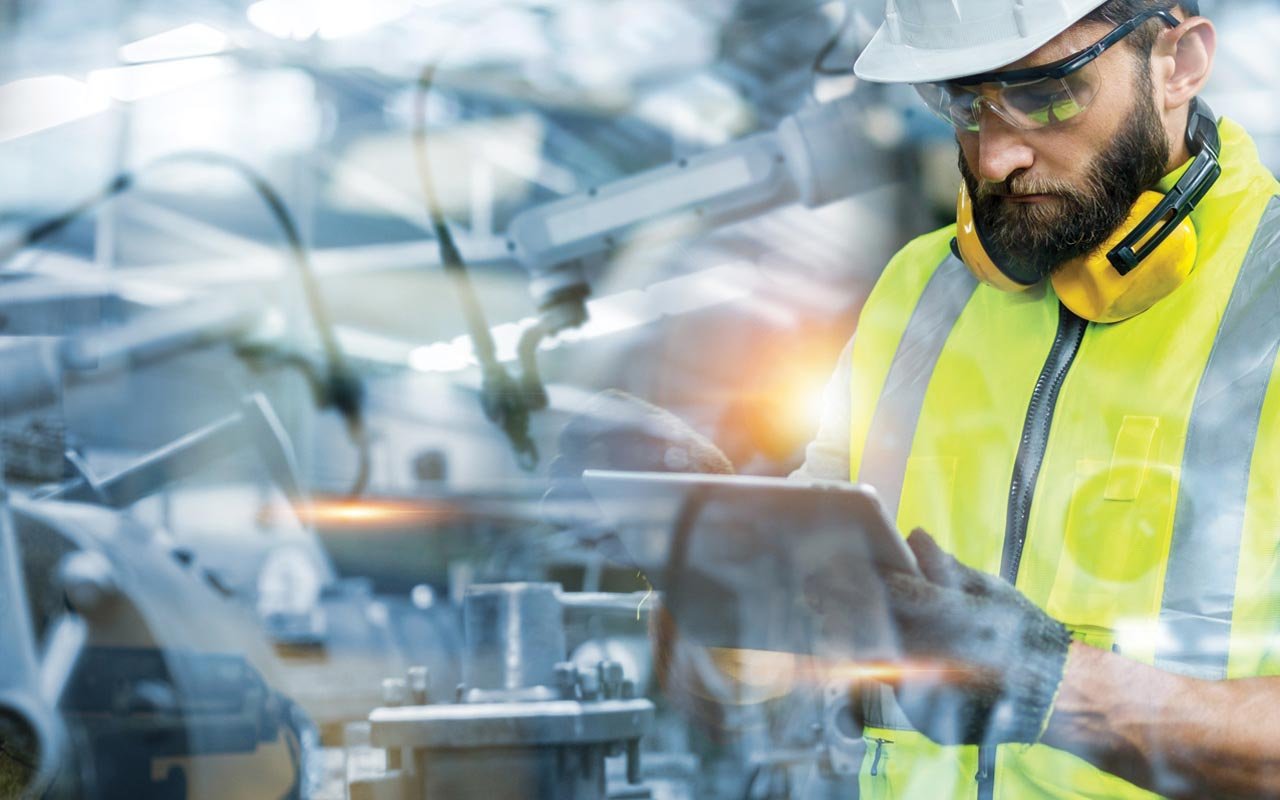