Eddy current testing of red-hot forged parts
In the production of forgings, the metals steel, iron and their alloy are formed in a press at a temperature above the Curie temperature (950-1050 °C). They are then specifically cooled from the forging heat in air (BY process) and thus do not require any further additional tempering.
Due to the mold cooling, the forged parts may partially come into contact with water during removal.
Why do black magnetic spots need to be detected?
This partial cooling must be detected, since these spots can lead to a very hard microstructure and in some cases to distortion of the part geometry during the subsequent controlled air cooling. The subsequent machining of the parts can thus cause severe tool wear and correspondingly high costs.
Subsequent normalization of the parts by means of an additional heat treatment is not possible for economic and material-related reasons.
How can the partial cooling be detected with eddy current?
Above the Curie temperature, the forging material is in a paramagnetic state. Due to the partial cooling, this range is clearly below the Curie point and the material regains its magnetic property.
These magnetic properties of the forging can be determined with the non-destructive, magnetic induction testing method using eddy current. In this process, low-frequency eddy currents are induced in the material via a sensor. The test voltage detected by the sensor results from the magnetic and electrical properties of the test part, with the voltage value being graphically displayed as a measuring point.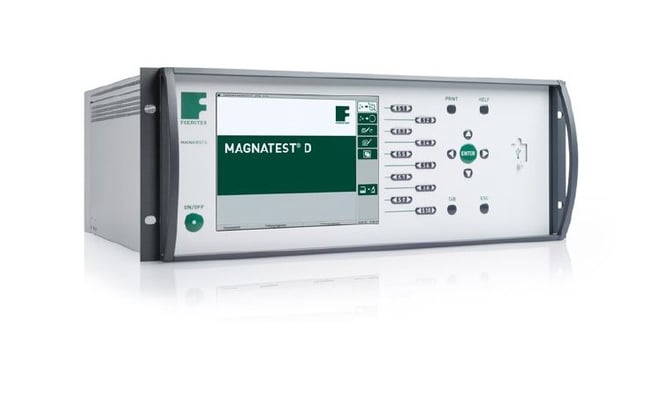
The MAGNATEST D testing system from FOERSTER is used to test the red-hot forged parts in the press. In the process, the parts fall through the water-cooled special coil. Parts that regain magnetic properties due to partial cooling in this area trigger a magnetic inductive pulse in the coil, which leads to reliable sorting of the parts with the testing system. In this way, defective parts are detected at an early stage and damage in the subsequent production process is avoided.