What is eddy current testing?
Eddy current testing is a non-destructive test method for electrically conductive materials. The physical properties of electrically conductive materials are used to generate a current flow in the material, the so-called eddy current.
The first thing to do is to induce an eddy current in the material. To do this, an alternating magnetic field is generated with an excitation coil. By applying an alternating current to the excitation coil, it excites the material. The eddy currents in the material in turn cause their own changing magnetic field. This magnetic field is in turn received with a measuring coil. This also creates an alternating current, which differs from the alternating exciter current in terms of the voltage amplitude and the phase position. Differences in the material become visible, such as impurities in the material (inclusions, different material composition) or damage (cracks, pores) to the material.
As a result, a distinction can be made between three different test methods in the eddy current testing:
1. Crack testing |
2. Coating thickness measurement |
3. Examination of the microstructural properties of a material |
1. Crack testing:
The crack testing can be carried out statically or dynamically.
With dynamic crack testing, either the sensor, in which the exciter and measuring coil are installed or the part to be tested are set in constant rotation. The sensor then scans the surface of the test part to be inspected. If the surface has no inclusions or damage, the eddy currents flow evenly in the material. However, as soon as inclusion or crack appears on the surface of the test part, the electrical resistance changes and the eddy current becomes smaller or has to "swerve". This changes the density of the eddy current so that this change is detected and evaluated by the measuring coil. This test takes place, for example, in the automotive industry in the form of automated testing in the production of safety-relevant and function-critical components.
In static crack testing, the sensor is moved manually over the surface of the test part. This type of inspection is used, among other things, during maintenance inspections of various safety-relevant components in the aviation industry.
Fig.1: Eddy Current Principle
In conclusion, it can be said that crack testing using eddy currents is a good way to find open defects on surfaces, such as cracks or pores.
Checklist for eddy current crack testing:
- Is the material electrically conductive?
- Are there any error specifications?
- Is there a definition of the test area?
- Is there a rotational symmetry?
2. Coating thickness measurement:
Coating thickness measurement is another field of eddy current testing. An iron core is used around which the excitation coil and measuring coil are wound. A low-frequency alternating current typically flows through the excitation coil (magnetic-inductive measuring method). When the iron core with the two coils approaches a magnetizable object, iron, the iron strengthens the alternating magnetic field. The measuring coil registers this gain as a voltage. How high this voltage difference turns out depends on the distance between the pole and the iron part. In the case of coated parts, this distance corresponds to the coating thickness of the part to be tested.
Furthermore, two effects are distinguished in the coating thickness measurement:
- Magnetic-induction effect: When the field coil is excited with a very low test frequency, the magnetic permeability of the ferromagnetic base material is used to measure the thickness of non-ferromagnetic coatings such as copper or zinc.
- Eddy current effect: When the field coil is excited with a high test frequency, the electrical conductivity of the electrically conductive base materials is used to measure the thickness of non-electrically conductive coatings such as paint, varnish, anodizing, etc. The thickness of the electrically conductive base material is then measured.
3. Examination of the microstructural properties of the material:
In the course of the testing for microstructural properties, a further distinction is made between hardness testing and material mix testing.
During hardness testing, for example, the microstructure of the material changes as a result of heat treatment. This in turn changes the conductivity or permeability of the material. The part to be tested is guided through a coil. There are two windings in this, the excitation winding and the measurement winding. Just as in crack testing, an alternating current is applied to the excitation winding. It creates an alternating magnetic field, which induces an eddy current in the material to be tested. The eddy current generates its own alternating magnetic field. This in turn is converted into an alternating current by the measuring winding. By changing the voltage amplitude and the phase position, the evaluation can be performed.
During the material mix testing, a distinction is made between different materials because different materials have different conductivities or permeabilities. These differences can be detected by the sensors. Therefore, the different materials such as free-cutting steel 9S20, case-hardened steel C15, quenched and tempered steel, structural steel St37, etc. — can be separated from each other.
MAGNETOSCOP 1.070: For Magnetic Field and Permeability Measurement.
Checklist for the microstructure testing:
- Is the material electrically conductive?
- Are there differences between conductivity or permeability?
- Is there a definition of the test area (e.g. partially hardened parts)?
Contact our experts and discuss your measuring tasks. We are glad to help you!
Share this
You May Also Like
These Related Stories
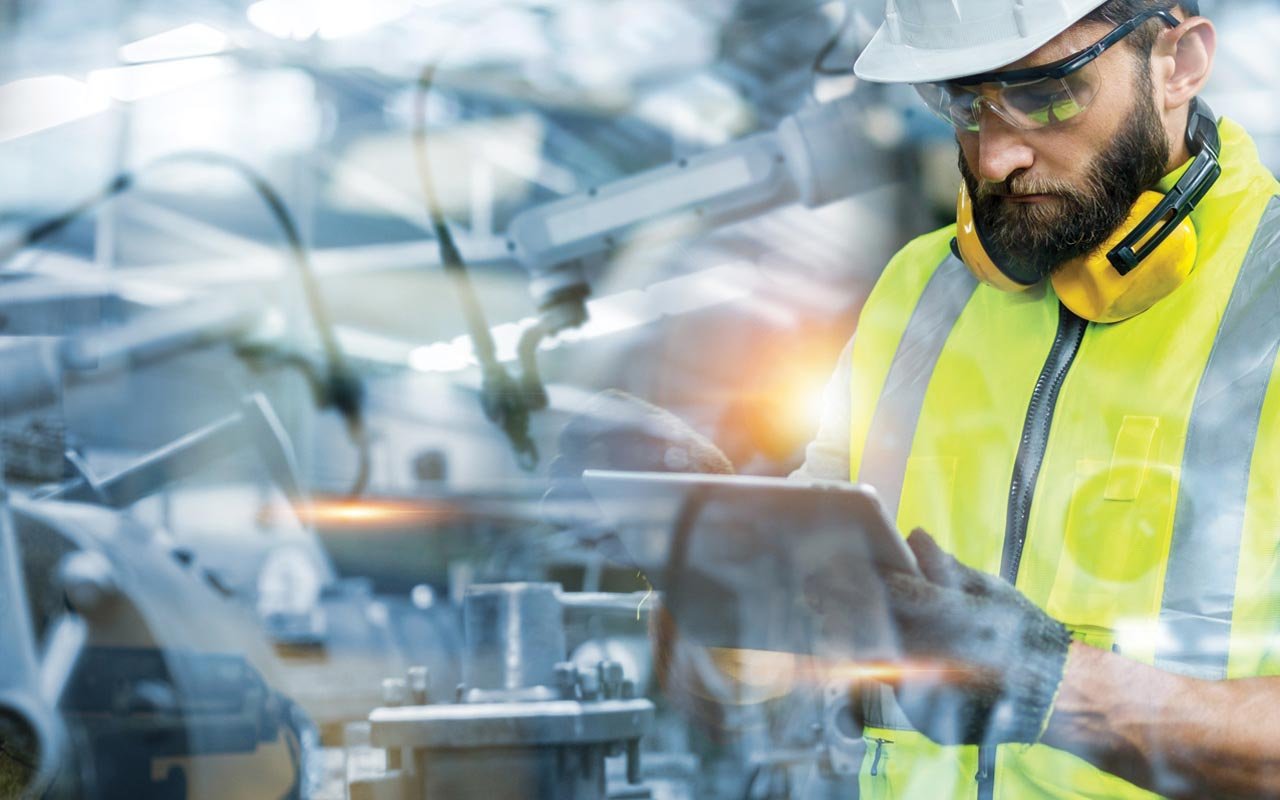
Crack testing: How does an eddy current test instrument work?
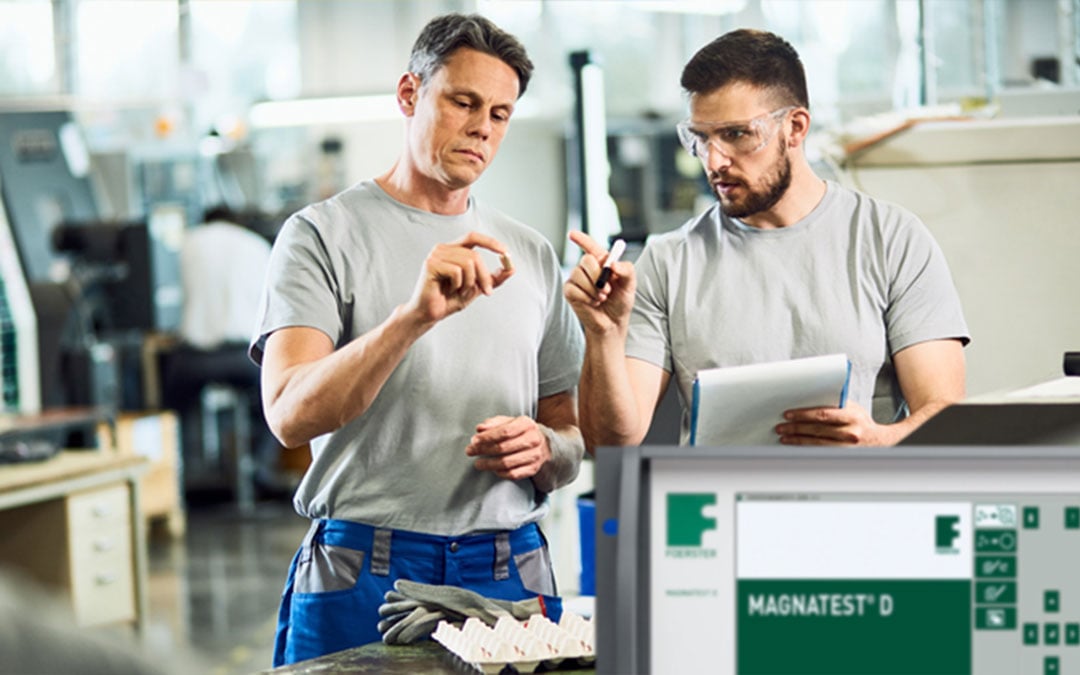
Hardness testing – The 7 largest challenges with eddy current systems
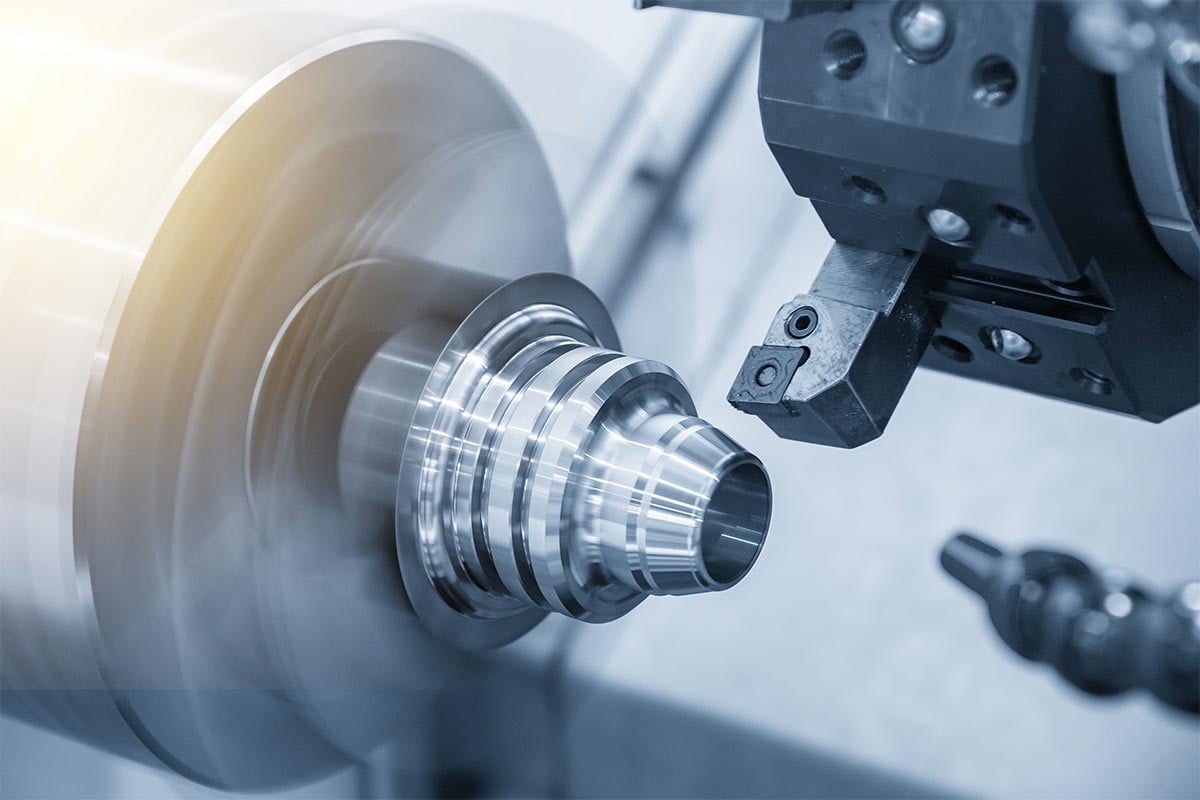