6 metodi importanti per la verifica delle cricche nei controlli non distruttivi
Negli ultimi anni il controlli non distruttivo sui materiali si è affermato nel monitoraggio dei processi grazie alle sue elevate prestazioni. Allo stesso tempo, in molti settori industriali non è più sufficiente testare solo le dimensioni geometriche di un componente. Ciò è dovuto al fatto che si richiede sempre più spesso di testare i componenti in parallelo al funzionamento continuo. Sono quindi necessarie procedure molto più approfonditi per dimostrare le proprietà corrispondenti durante la vita utile.
Perché sono necessari i test non distruttivi sui materiali?
Sono molte le applicazioni critiche per la sicurezza o i danni economici più gravi che si verificano quando i componenti si guastano o non soddisfano i requisiti fondamentali. Se, ad esempio, una montagna russa si rompe durante il funzionamento, le vite umane sono immediatamente in pericolo. Se le condutture di un edificio si guastano, possono verificarsi ingenti danni all'acqua con conseguenti elevati costi di ristrutturazione.
Di conseguenza, sono stati definiti degli standard nel settore automobilistico e in molte altre industrie. Questi garantiscono un'ispezione continua e approfondita dei componenti rilevanti per la sicurezza durante il processo di produzione e prima dell'installazione.
Che tipo di difetti si possono trovare nei componenti?
Il catalogo dei difetti dei clienti è vario. Ad esempio, fattori d'influenza decisivi sono l'area di applicazione del componente, il materiale di cui è fatto e le sue dimensioni. I tipi di difetti più comuni che si riscontrano in un'ispezione superficiale sono:
- Crepe
- Cavità
- Ammaccature
- Bruciatura da macinazione
- Punti difficili
- Macchie morbide
- Inclusioni magnetiche (Remanenze)
I difetti classici dei componenti sono le cricche individuate sulla superficie del materiale. In questo caso si ricorre solitamente ai test a correnti indotte. Questo perché anche le cricche più piccole, che inizialmente non rappresentano un problema, possono ingrandirsi e allargarsi sotto carico permanente. Nel peggiore dei casi, ciò può portare alla rottura del componente. Pensate a una crepa in un disco del freno: è possibile che dopo un certo periodo di funzionamento il disco del freno si rompa gravemente durante la decelerazione. Nel traffico stradale, un componente così difettoso può portare rapidamente a situazioni di pericolo di vita.
Per questo motivo, i clienti si aspettano che anche i difetti più piccoli, con una profondità di pochi micrometri, vengano trovati e visualizzati in modo affidabile durante il processo di ispezione. Per verificarlo, ad esempio, può essere utilizzato lo strumento di controllo STATOGRAPH di FOERSTER. La dimensione del difetto che può essere localizzato con lo STATOGRAPH dipende dal componente e dal suo materiale, nonché dalla frequenza di prova e dalla sonda utilizzata. Con un design ottimale è possibile individuare anche cricche con una profondità di soli 30 µm.
Vuoi ottenere l'eBook gratuito? Clicca qui!
Quali sono i metodi disponibili per il rilevamento delle cricche nei componenti fusi?
Esistono diversi metodi per il test dei componenti. Si distingue tra due approcci classici:
- Test distruttivi
- Controlli non distruttivi
A lungo i componenti di lotti successivamente rivenduti e installati sono stati testati solo in modo casuale e distruttivo. All'aumentare della necessità di test, aumenta il costo degli scarti causati dal test. Di conseguenza, un test completo è metodologicamente impossibile.
Per fronteggiare questo problema si è sviluppato il campo dei controlli non distruttivi. Sono disponibili diversi metodi a seconda dell'attività di controllo:
- Ispezione visiva (VT)
- Test di penetrazione con colorante (PT)
- Test a correnti indotte (ET)
- Test termografici (TT)
- Test delle particelle magnetiche (MT)
- Test a ultrasuoni (UT)
A seconda dell'applicazione, vengono utilizzati diversi metodi di prova. I fattori che influiscono in modo determinante sono il materiale di prova, le dimensioni, il modello di difetto e l'attività di prova, nonché il tempo di ciclo richiesto e il budget disponibile.
1. Test delle cricche con ispezione visiva (VT)
Durante le procedure di ispezione visiva, le caratteristiche qualitative legate alla superficie, come le deviazioni di forma, i difetti o le condizioni superficiali di un componente, vengono osservate e valutate a occhio nudo o con l'ausilio di strumenti ottici (ad esempio lenti di ingrandimento, microscopi o endoscopi). Prima di tutti gli altri metodi di controllo distruttivi e non distruttivi, l'ispezione visiva viene inizialmente eseguita in un test completo e viene utilizzata per varie forme di prodotto secondo le istruzioni di test specificate.
La procedura di test è implementata come ispezione visiva diretta e indiretta nell'ambito del monitoraggio della produzione, dell'ispezione e dell'indagine sui danni di componenti, sistemi o altri oggetti di prova. I risultati del test dipendono fortemente dall'esperienza e dalla valutazione soggettiva del collaudatore. Pertanto, è difficile ottenere una comparabilità.
2. Test delle fessure con penetrazione di colorante (PT)
Il test di penetrazione del colorante è un altro metodo di prova non distruttivo per le superfici dei materiali. La base di questo processo è l'azione capillare. Il processo di penetrazione viene utilizzato come prova visiva di difetti superficiali come crepe o pori.
Il processo è utilizzato principalmente per i metalli. Se idoneo, il test di penetrazione del colore può anche evidenziare difetti nelle materie plastiche e nelle ceramiche. Come per l'ispezione visiva, il test di penetrazione del colore è un metodo soggettivo che dipende dall'esperienza dell'ispettore.
3. Test delle cricche con strumenti a correnti parassite (ET)
Per l'ispezione superficiale di materiali conduttori, il metodo delle correnti parassite (in inglese "eddy current testing", abbreviato ECT) si è affermato come tecnologia dominante. I sistemi di test a correnti parassite sono costituiti da uno strumento di test, da una sonda corrispondente e, se necessario, da moduli software aggiuntivi. La sonda di prova contiene una bobina di campo (bobina primaria) e una bobina differenziale (bobina secondaria). La sonda di prova è collegata allo strumento di prova, ad esempio uno STATOGRAPH CM per il test delle cricche.
La bobina di campo viene azionata con un campo alternato e induce un campo secondario nella bobina differenziale, il cui segnale cambia di ampiezza e fase quando si verificano cambiamenti di superficie. Questa variazione del segnale viene registrata dallo strumento di prova con una velocità di trasmissione dati molto elevata. Le informazioni vengono successivamente comunicate all'impianto di produzione permettendo di riconoscere ed eliminare un pezzo difettoso.
A seconda del modello di errore e del materiale dell'oggetto in prova, è necessario selezionare la configurazione corretta per lo strumento di prova e la sonda di prova. Esistono vari modi per regolare i parametri del test in modo che reagiscano nel modo più ottimale possibile a specifici modelli di errore. Allo stesso tempo, questo favorisce la possibilità di individuare più difficilmente gli errori irrilevanti. Anche i programmi software a valle possono aiutare a valutare i dati del test. Gli stessi dati vengono valutati con diversi metodi di filtraggio e quindi ottimizzati per diversi modelli di errore.
STATOVISION è un esempio di software in grado di migliorare la qualità del segnale. Dopo l'acquisizione dei dati grezzi, il software utilizza metodi di filtraggio digitale. Ciò è particolarmente necessario se i requisiti per la dimensione dell'errore da individuare sono molto elevati. Le profondità di errore tipiche che si prevede di rilevare con il metodo eddy current vanno da 30 μm a 1 mm.
I prerequisiti per il test a correnti parassite per la ricerca di difetti superficiali sono, da un lato, componenti generalmente conduttivi, dall'altro, la simmetria rotazionale degli oggetti di prova. La simmetria rotazionale è necessaria per eseguire il test nel modo più efficiente possibile. Il componente viene ruotato per il test e la sonda ne scansiona la superficie in parallelo. Se non c'è simmetria, può essere necessario utilizzare un altro metodo di prova.
4. Prova di fessurazione con apparecchiatura termografica (TT)
Le prove a correnti parassite sono sempre un metodo vantaggioso quando si tratta di materiali conduttivi e a simmetria di rotazione. Inoltre, questi componenti devono avere superfici il più possibile lisce per poter essere scansionati con una sonda. Se queste condizioni non sono soddisfatte, si ricorre a metodi di prova complementari. Il rilevamento delle cricche mediante termografia è in costante aumento nelle applicazioni industriali. Il test termografico delle cricche viene solitamente eseguito utilizzando il metodo termografico a impulsi o il metodo termografico Lock-In. In questo caso, il componente viene riscaldato localmente in brevi impulsi con una fonte di energia (ad esempio, per induzione, otticamente tramite lampade o laser). La superficie viene registrata con una termocamera. Le cricche e altre differenze locali sulla superficie reagiscono in modo diverso al calore applicato. Una crepa accumula meno calore e si distingue chiaramente dall'ambiente circostante nell'immagine termografica.
Anche le diverse fonti di calore mostrano effetti diversi. Se, ad esempio, un componente conduttivo viene eccitato con un induttore, si genera più calore all'estremità di una cricca che in altri punti del pezzo in prova. Le correnti parassite si sono condensate qui e l'apporto di calore è maggiore. Le immagini registrate con la termocamera confluiscono in un software di elaborazione dati e vengono valutate tramite speciali algoritmi di elaborazione. Diverse immagini scattate in successione mostrano, tra l'altro, il flusso di calore nel tempo e forniscono ulteriori informazioni. Il principale vantaggio del metodo termografico per il rilevamento delle cricche è che i componenti possono avere un elevato grado di libertà nelle dimensioni e nella geometria. Inoltre, la tecnica può essere applicata a componenti non conduttivi. In questi casi, per l'immissione di energia è solitamente necessario un metodo ottico.
Sebbene il metodo è relativamente stabile rispetto alle influenze ambientali, presenta il difetto di richiedere una priva di contaminazione: la variazione delle proprietà della superficie può portare a flussi di calore diversi, che possono apparire come pseudo difetti nella valutazione. Oggi è possibile realizzare con relativa facilità processi automatizzati con manipolazione dei componenti. Sono ora disponibili anche buone termocamere e quindi questo processo si sta lentamente affermando nelle linee di produzione. Questa tecnologia ha il potenziale per sostituire l'ispezione delle particelle magnetiche, che oggi è ancora molto dominante.
5. Test delle cricche con apparecchiatura per il controllo delle particelle magnetiche (MT)
Probabilmente il metodo più antico per individuare le cricche nei materiali è il test delle particelle magnetiche. Secondo questo metodo, i componenti ferromagnetici vengono magnetizzati e spruzzati con polvere magnetica. I difetti nel pezzo in esame reagiscono in modo diverso alla magnetizzazione. Di conseguenza, la polvere magnetica può aderire meglio. Aggiungendo materiale fluorescente alla polvere magnetica, le imperfezioni "brillano" in modo diverso in determinate condizioni di luce. Lo svantaggio principale di questa procedura è che la selezione buona o cattiva del pezzo in prova avviene sulla base della valutazione soggettiva del tecnico di prova. L'esperienza dell'ispettore determina da sola se una cricca viene valutata come grande o piccola, o se l'entità di un errore è di entità tale da poter essere valutata come cattiva. Inoltre, la pulizia dei componenti dopo il test richiede un grande sforzo, poiché la polvere magnetica si attacca alle parti in esame. L'automazione dei sistemi per il test delle particelle magnetiche può essere piuttosto complessa. La procedura di test è quindi utile solo se il numero di elementi da testare non è troppo elevato.
6. Test delle cricche con strumenti a ultrasuoni (UT)
Il test a correnti indotte è il metodo preferito per le cricche aperte in superficie nei componenti conduttivi. Tuttavia, il metodo raggiunge i suoi limiti nel caso di cricche o anomalie del materiale che si trovano all'interno del provino. Questo perché la profondità di penetrazione di questo metodo dipende dalla frequenza utilizzata. Se questa è nell'intervallo dei kHz, la profondità di penetrazione si riduce relativamente rapidamente a pochi millimetri. Pertanto, un altro metodo di prova consolidato è la verifica delle cricche con dispositivi a ultrasuoni. Il metodo a ultrasuoni è adatto a testare i componenti fino alla loro profondità. Con questo metodo, qualsiasi tipo di materiale può essere completamente "radiografato". A tale scopo, una testa di misura con un trasmettitore e un ricevitore a ultrasuoni viene posizionata sul pezzo da testare. Gli ultrasuoni generati nella testa di misura vengono trasportati nella parte in esame attraverso un mezzo di accoppiamento, di solito un tipo di acqua. Un buon accoppiamento è importante per un test efficace.
Gli ultrasuoni penetrano nel pezzo in esame e le onde vengono riflesse sulla parete posteriore e dai difetti come crepe o inclusioni. Questi echi vengono registrati nell'unità di ricerca. Il tipo e la dimensione delle riflessioni consentono di trarre conclusioni sulla posizione dell'anomalia riscontrata nel campione. La produzione di unità di ricerca a ultrasuoni è molto complessa. Inoltre, sono necessari sistemi chiusi a causa del mezzo di accoppiamento. Inoltre, il mezzo di accoppiamento deve essere il più possibile privo di impurità e formazione di bolle, poiché queste disturbano il percorso del suono ultrasonico e agiscono come un difetto del materiale.
Quale crepa - quale processo?
Didascalie
- A = Il più adatto
- B = Più o meno adatto all'uso
- C = Non così buono
- D = Per niente adatto
Conclusioni
Tutti i metodi non distruttivi per il controllo delle cricche qui illustrati sono giustificati. Il metodo di prova appropriato viene definito in base al tipo di errore e al materiale utilizzato. È anche possibile utilizzare una combinazione di diversi metodi di prova, che possono essere integrati in un'unica linea di prova.
Share this
You May Also Like
These Related Stories
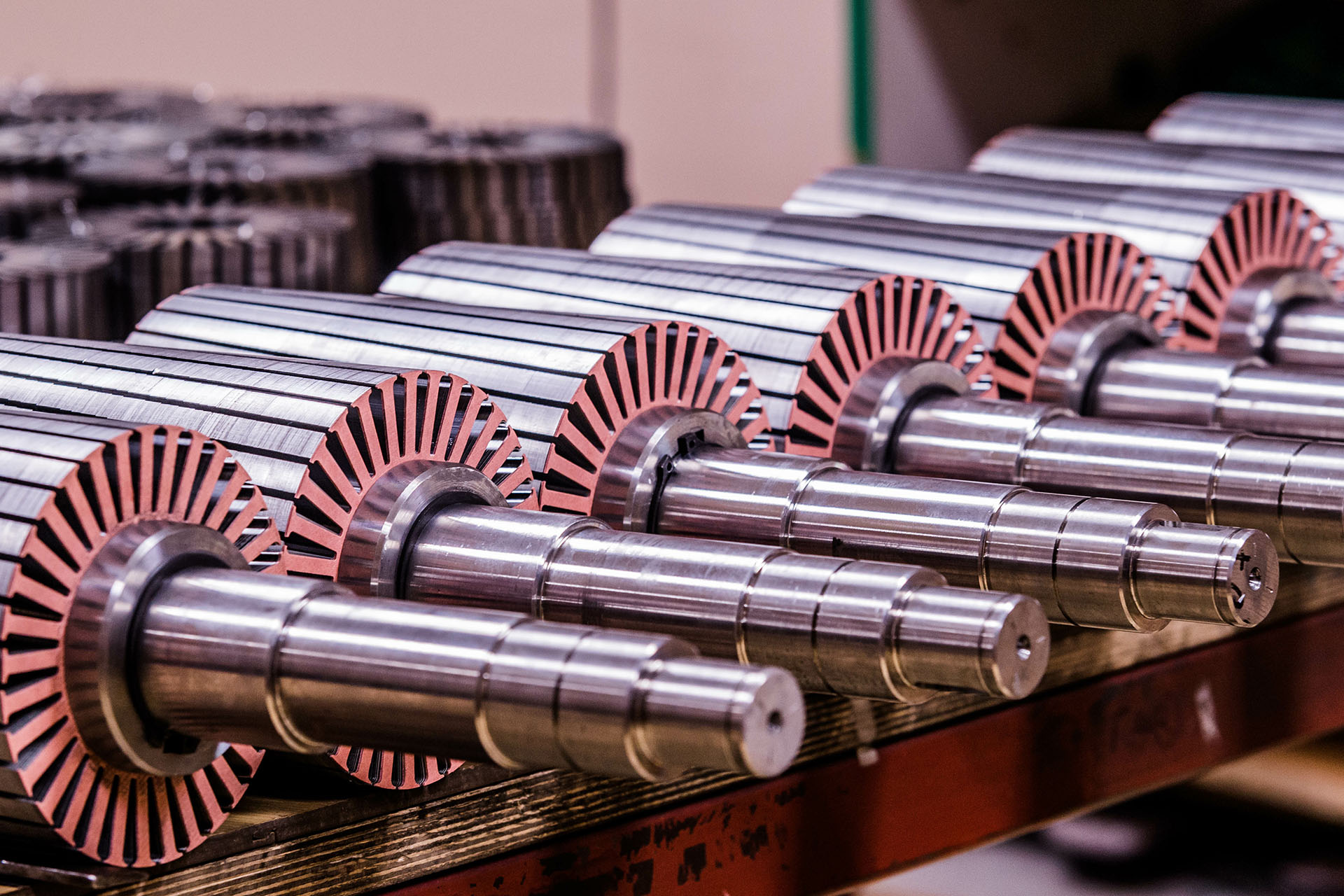
Test della microstruttura e delle cricche sugli alberi del rotore mediante correnti parassite
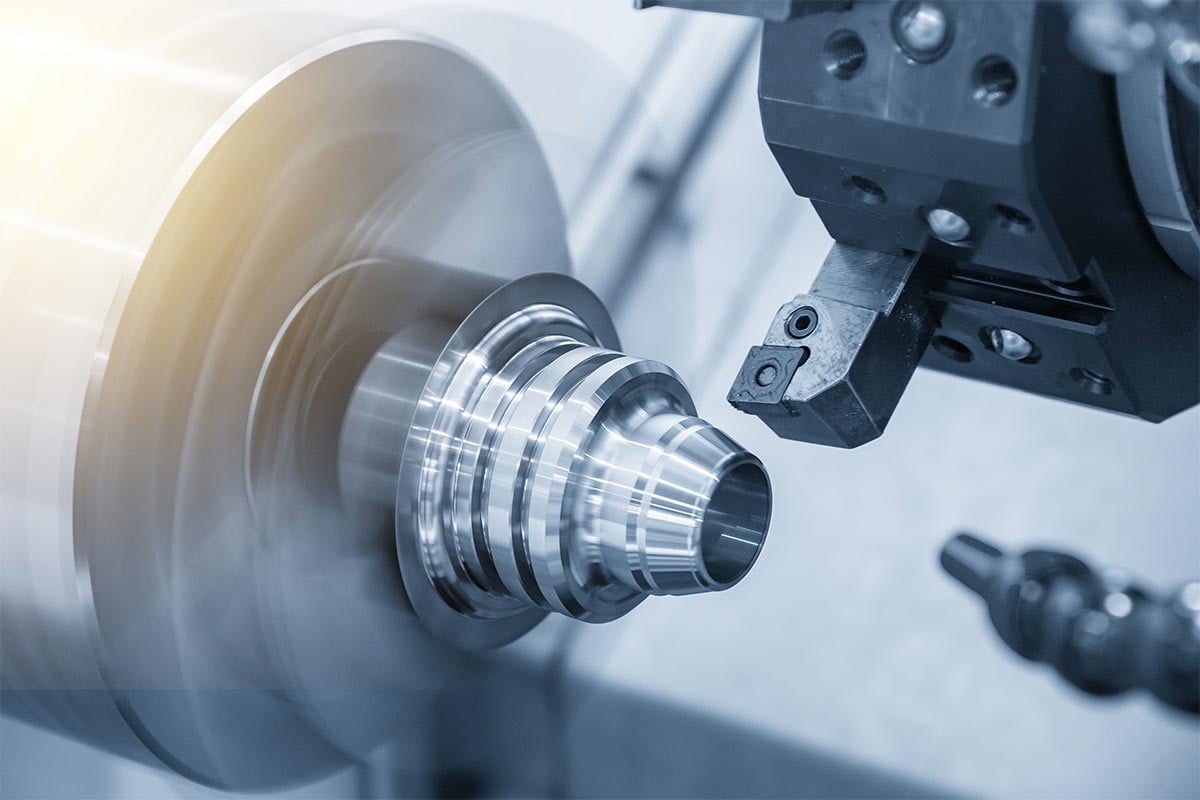
Test delle crepe: Come si impostano correttamente i filtri e le frequenze?
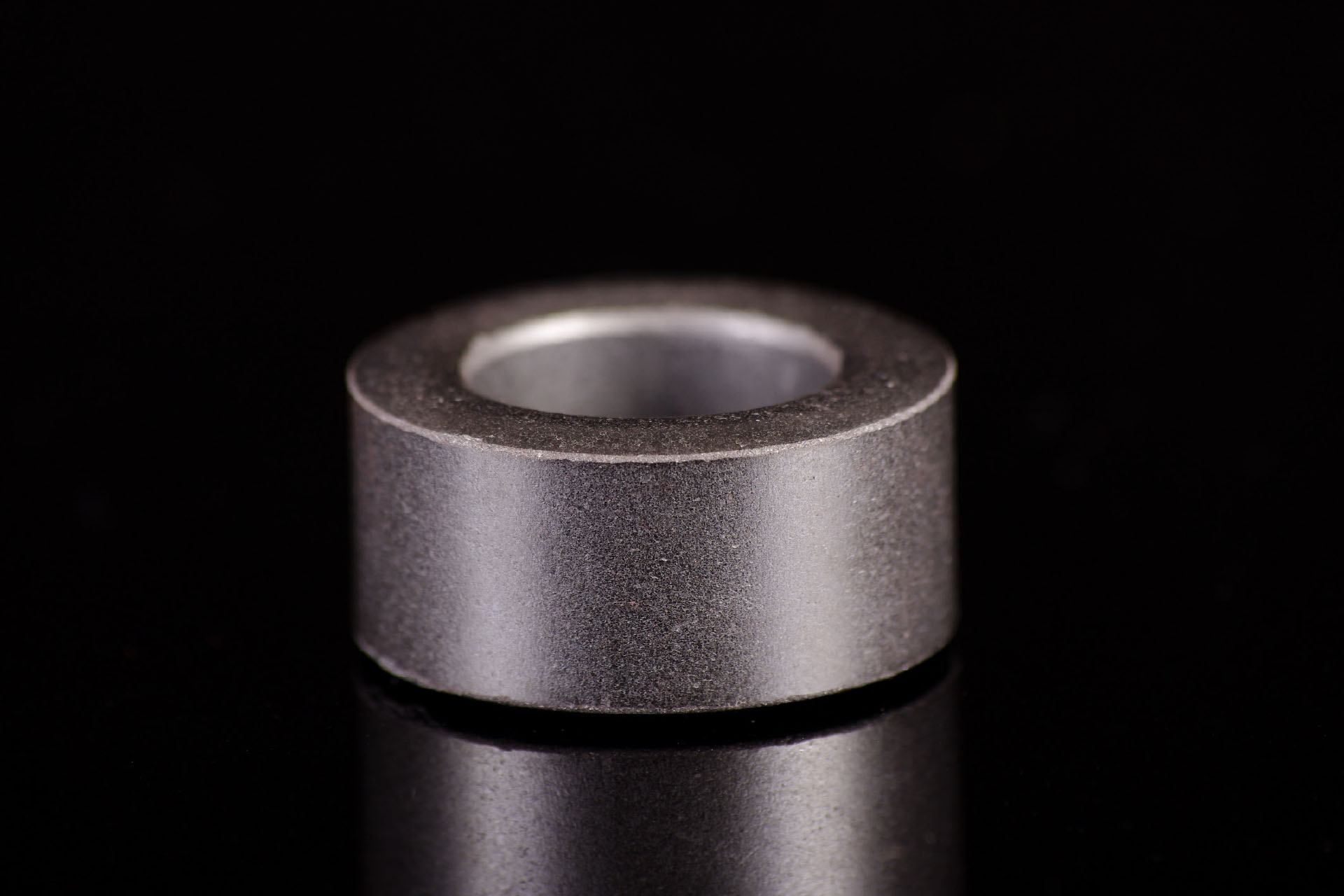