6 métodos importantes para la detección de grietas mediante Ensayos No Destructivos
En los últimos años, los ensayos no destructivos de materiales se han consolidado en la monitorización de procesos. Debido a su eficaz rendimiento, este procedimiento de inspección se ha hecho crucial para el control exhaustivo de los procesos. Al mismo tiempo, en muchas industrias ya no basta solo con comprobar únicamente la dimensión geométrica de un componente. Esto es debido a que cada vez se incrementan las exigencias puestas en el control de los componentes en paralelo con el funcionamiento continuo. Por tanto, es esencial realizar controles mucho más exhaustivos para demostrar las propiedades correspondientes.
¿Por qué son necesarios los ensayos no destructivos de materiales?
Hay muchas aplicaciones críticas para la seguridad o con importantes consecuencias económicas en las que los componentes pueden fallar o no cumplir con sus requisitos. Si, por ejemplo, una montaña rusa se rompe durante su funcionamiento, se ponen inmediatamente en riesgo las vidas humanas. Si fallan las tuberías de un edificio, se puede producir considerables daños debido al agua, con los correspondientes elevados costes de renovación.
Por ello, se definen normas en el sector del automóvil y en muchas otras industrias se definen normas. Estas garantizan una inspección continua y en profundidad de los componentes relevantes para la seguridad durante el proceso de fabricación y antes de su instalación.
¿Qué tipo de defectos pueden encontrarse en los componentes?
El catálogo de defectos de los clientes es diverso. Por ejemplo, los factores de influencia decisivos son: el área de aplicación del componente y el material del que está hecho y sus dimensiones. Los tipos de defectos más comunes que se pueden encontrar en una inspección de superficies son:
- Grietas.
- Cavidades.
- Abolladuras.
- Quemaduras por esmerilado.
- Puntos duros.
- Puntos blandos.
- Inclusiones magnéticas (remanencias.)
Los defectos clásicos de los componentes son las grietas detectadas en la superficie del material. En este caso, se suele utilizar el ensayo de Corrientes Inducidas. Esto se debe a que incluso las grietas más pequeñas, que inicialmente no planteaban problemas, pueden agrandarse y ensancharse bajo una carga permanente. En el peor de los casos, esto puede provocar el fallo del componente. Piense en una grieta en un disco de freno: existe la posibilidad de que, tras un cierto periodo de funcionamiento, el disco de freno se rompa gravemente al frenar. Un componente defectuoso de este tipo puede llevar rápidamente a situaciones que pongan en peligro la vida.
Por esta razón, los clientes esperan que incluso los defectos más pequeños con una profundidad de solo unas micras sean encontrados y mostrados de forma fiable durante el proceso de inspección. El equipo de control STATOGRAPH de FOERSTER, por ejemplo, suele emplearse para comprobarlo. El tamaño del defecto que aún puede ser resuelto con el STATOGRAPH depende del componente y su material, así como de la frecuencia de ensayo y la sonda utilizada. Con el diseño óptimo pueden encontrarse grietas incluso con una profundidad de sólo 30 µm.
¿Desea obtener el eBook gratuito? ¡Haga click aquí!
¿Qué métodos existen para la detección de grietas en componentes de fundición?
Existen varios métodos para el ensayo de componentes. Se distinguen dos enfoques clásicos:
- Ensayos destructivos.
- Ensayos no destructivos.
Los componentes procedentes de lotes que posteriormente se revenden y se instalan solo pueden someterse a pruebas de forma aleatoria y destructiva. A medida que aumenta la necesidad de realizar pruebas, se incrementa el coste del achatarramiento provocado por la prueba. En consecuencia, un control al completo es metodológicamente imposible.
En este sentido, se ha desarrollado el campo de los ensayos no destructivos. Sobre esta base, existen diferentes métodos en función de la tarea de ensayo:
- Inspección visual (IV)
- Pruebas por líquidos penetrantes (LP)
- Ensayos por corrientes Inducidas (CI)
- Ensayos termográficos (ET)
- Pruebas de partículas magnéticas (PPM)
- Pruebas ultrasónicas (PU)
En función de la aplicación, se utilizan distintos métodos de ensayo. Los factores esenciales que influyen son: el material de ensayo, el tamaño, el patrón de defectos y la tarea de ensayo, así como el tiempo de ciclo necesario y el presupuesto disponible.
1. Control de grietas con inspección visual (IV)
Durante los procedimientos de inspección visual, las características de calidad relacionadas con la superficie, tales como las desviaciones de forma, los defectos o el estado de la superficie de un componente, se observan y evalúan a simple vista o mediante aparatos ópticos (por ejemplo, lupas, microscopios o endoscopios). Antes de todos los demás métodos de ensayo destructivos y no destructivos, la inspección visual se lleva a cabo inicialmente en un ensayo completo y se utiliza para diversas formas de productos de acuerdo con las instrucciones de ensayo especificadas.
El procedimiento de control se aplica como inspección visual directa e indirecta en el ámbito de la supervisión de la producción, la inspección y la investigación de daños de componentes, sistemas u otros objetos de prueba. Los resultados de las pruebas dependen en gran medida de la experiencia y la evaluación subjetiva de la persona que las realiza. Por lo tanto, la comparabilidad es difícil de lograr.
2. Control de grietas con líquidos penetrantes (PLP)
El ensayo mediante líquidos penetrantes es otro método de ensayo no destructivo para superficies de materiales. La base de este proceso es la acción capilar. El proceso de penetración se utiliza como prueba visual de defectos superficiales como grietas o poros.
El proceso se utiliza principalmente en metales. Si es adecuado, el ensayo mediante líquidos penetrantes también puede mostrar defectos en plásticos y cerámicas. Al igual que la inspección visual, la inspección mediante líquidos penetrantes es un método subjetivo que depende de la experiencia del inspector.
3. Ensayo de grietas con instrumentos de corrientes inducidas (CI)
Para la inspección de superficies de piezas conductoras, el método de corrientes inducidas (en inglés: "eddy current testing", abreviado ECT) se ha establecido como la tecnología dominante. Los sistemas de ensayo por corrientes inducidas constan de un instrumento de ensayo con su correspondiente sonda y, en caso necesario, módulos de software adicionales. La sonda de ensayo contiene una bobina de campo (bobina primaria) y una bobina diferencial (bobina secundaria). La sonda de ensayo se conecta al instrumento de ensayo, por ejemplo, un STATOGRAPH CM para pruebas de grietas.
La bobina de campo funciona con un campo alterno e induce un campo secundario en la bobina diferencial, que modifica la amplitud y la fase de la señal cuando se producen cambios en la superficie. Esta variación de la señal es registrada por el instrumento de ensayo con una velocidad de refresco de datos muy alta. Esta información se comunica posteriormente a la planta de producción. Como resultado, se puede reconocer y clasificar una pieza defectuosa.
En función del patrón de fallo y del material del objeto de ensayo, debe seleccionarse la configuración correcta para el instrumento y la sonda de ensayo. Existen varias formas de ajustar los parámetros de la prueba para que reaccionen de la mejor forma posible a patrones de defectosespecíficos. Al mismo tiempo, esto favorece que los defectos irrelevantes se puedan detectar de forma más deficiente. Los programas de software posteriores también pueden ayudar a evaluar los datos de la prueba. Los mismos datos se evalúan con distintos métodos de filtrado y se optimizan así para múltiples patrones de defectos.
STATOVISION es un ejemplo de este tipo de software capaz de mejorar la calidad de la señal. Tras la adquisición de los datos en bruto, el software utiliza métodos de filtrado digital. Esto es especialmente necesario si los requisitos en cuanto al tamaño del defecto que debe detectarse son muy elevados. Las profundidades de defecto típicas que se espera detectar con el método de corrientes inducidas oscilan entre 30 µm y 1 mm.
Los prerrequisitos para el ensayo por corrientes inducidas de defectos superficiales son, por un lado, componentes generalmente conductores y, por otro, la simetría rotacional de los objetos de ensayo. La simetría rotacional es necesaria para realizar la prueba de la forma más eficiente posible. El componente se gira para la prueba y la sonda explora su superficie en paralelo. Si no hay simetría, puede ser necesario utilizar otro método de ensayo.
4. Pruebas de grietas con equipo termográfico (PT)
La prueba por corrientes inducidas es siempre un método ventajoso cuando se trata de materiales conductores y con simetría de rotación. Además, estos componentes deben tener superficies lo más lisas posible para poder ser exploradas con una sonda. Si no se cumplen estas condiciones, se utilizan métodos de ensayo complementarios. La detección de grietas mediante termografía está aumentando constantemente en las aplicaciones industriales. El control de grietas mediante termografía suelen realizarse empleando el método de impulsos o el método de bloqueo. El componente se calienta localmente en pulsos cortos con una fuente de energía (por ejemplo, por inducción, ópticamente a través de lámparas o láser). La superficie se registra con una cámara termográfica. Las grietas y otras diferencias locales de la superficie reaccionan de forma diferente al calor aplicado. Una grieta almacena da menos calor y destaca claramente de su entorno en la imagen termográfica.
Las distintas fuentes de calor también muestran efectos diferentes. Si, por ejemplo, se excita un componente conductor con un inductor, se genera más calor en las puntas de una grieta que en otros puntos de la pieza de ensayo. Las corrientes inducidas se condensan aquí y la concentración de calor es mayor. Las imágenes grabadas con la cámara termográfica se introducen en un software de procesamiento de datos. Para la evaluación de las imágenes se utilizan algoritmos de procesamiento especiales. Varias imágenes tomadas sucesivamente muestran, entre otras cosas, el flujo de calor a lo largo del tiempo y proporcionan más información. La principal ventaja del método termográfico para la detección de grietas es que los componentes pueden tener un alto grado de libertad en su tamaño y geometría. Además, esta técnica se puede aplicar a los componentes no conductores. En estos casos, suele ser necesario un método óptico para la entrada de energía.
Además, el método es relativamente estable frente a las influencias ambientales. Sin embargo, la superficie sometida a ensayo debe estar libre de contaminación siempre que sea posible. La modificación de las propiedades de la superficie pueden dar lugar a flujos de calor diferentes, que pueden aparecer como pseudefectos en la evaluación. Hoy en día es relativamente fácil automatizar los procesos con manipulación de componentes. También se dispone ya de buenas cámaras termográficas, por lo que este proceso se está estableciendo lentamente en las líneas de producción. La tecnología tiene potencial para sustituir a la inspección por partículas magnéticas, que sigue siendo muy dominante hoy en día.
5. Control de grietas con equipos de inspección por partículas magnéticas (PPM)
Probablemente es el método más antiguo para detectar grietas en los materiales es el ensayo con partículas magnéticas. Según este método, los componentes ferromagnéticos se magnetizan y se rocían con polvo magnético. Los defectos en la pieza de prueba reaccionan de forma diferente a la magnetización. En ese punto, el campo magnético aparece con más fuerza en la superficie. En consecuencia, el polvo magnético puede adherirse mejor. Al añadir material fluorescente al polvo magnético, las imperfecciones "brillan" de forma diferente en determinadas condiciones de iluminación. La principal desventaja de este procedimiento es que la clasificación en buena o mala de la pieza de prueba se realiza sobre la base de la evaluación subjetiva del operaodor del ensayo. Sólo la experiencia del inspector determina si una grieta se valora como grande o pequeña, o si el alcance de un defecto es de una magnitud que puede valorarse como mala. Además, la limpieza de los componentes tras la prueba requiere un gran esfuerzo ya que el polvo magnético se adhiere a las piezas de prueba. La automatización de los sistemas de ensayo con partículas magnéticas puede resultar bastante compleja. Por tanto, el procedimiento de prueba solo será útil si el número de piezas de prueba no es demasiado grande.
6. Control de grietas con instrumentos ultrasónicos (PS)
El ensayo por corrientes inducidas es el método preferido para las grietas abiertas en la superficie de los componentes conductores. Sin embargo, el método alcanza sus límites en el caso de grietas o anomalías del material que se encuentran en el interior de una pieza. Esto se debe a que la profundidad de penetración de este método depende de la frecuencia utilizada. Si ésta se encuentra en el rango de los kHz, la profundidad de penetración se reduce relativamente rápido a tan sólo unos milímetros. Por lo tanto, otro método de ensayo establecido es el ensayo de grietas con dispositivos ultrasónicos. El método ultrasónico es adecuado para controlar componentes en toda su profundidad. Con este método se puede "radiografiar" completamente cualquier tipo de material. Para ello, se coloca en la pieza de ensayo un cabezal de medición con un emisor y un receptor de ultrasonidos, un palpador ultrasónico. Los ultrasonidos generados en el paloador se transportan a la pieza de ensayo a través de un medio de acoplamiento, normalmente un tipo de agua. Un buen acoplamiento es importante para que el control sea eficaz.
Los ultrasonidos penetran en la pieza de ensayo y se crean ecos de las ondas ultrasónicas por reflexión en la pared posterior. Los defectos, como grietas o inclusiones, provocan una reflexión adicional de los ultrasonidos. Estos se registran en el palpeador. El tipo y el tamaño de las reflexiones permiten sacar conclusiones sobre el lugar de la muestra en el que se encuentra la anomalía detectada. La fabricación de palpeadores de ultrasonidos es muy compleja. Además, se requieren sistemas cerrados debido al medio de acoplamiento. Además, el medio de acoplamiento debe estar lo más libre posible de impurezas y formación de burbujas, ya que éstas perturban la trayectoria de la onda ultrasónica y actúan como un defecto del material.
¿Qué grieta?-¿Qué proceso?
Leyendas
- A = El más adecuado
- B = Más o menos adecuado
- C = No muy adecuado
- D = No adecuado
Conclusión
Todos los métodos no destructivos para el ensayo de grietas aquí expuestos están justificados. El método de ensayo adecuado se define en función del tipo de defecto y del material utilizado. También es posible utilizar una combinación de diferentes métodos de ensayo que pueden integrarse juntos en una línea de ensayo.
Share this
You May Also Like
These Related Stories
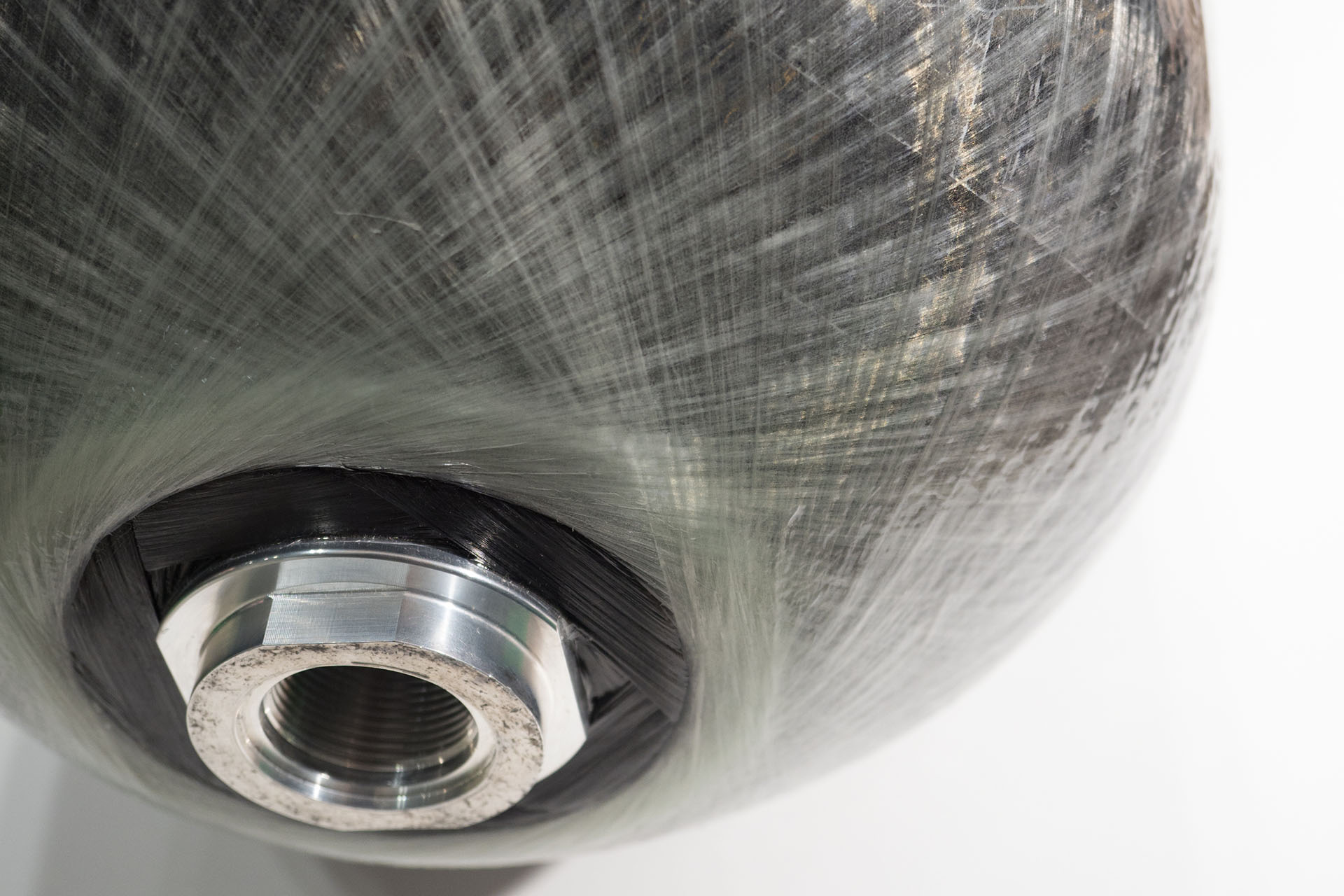
Detección automatizada de grietas por corrientes inducidas en recipientes a presión
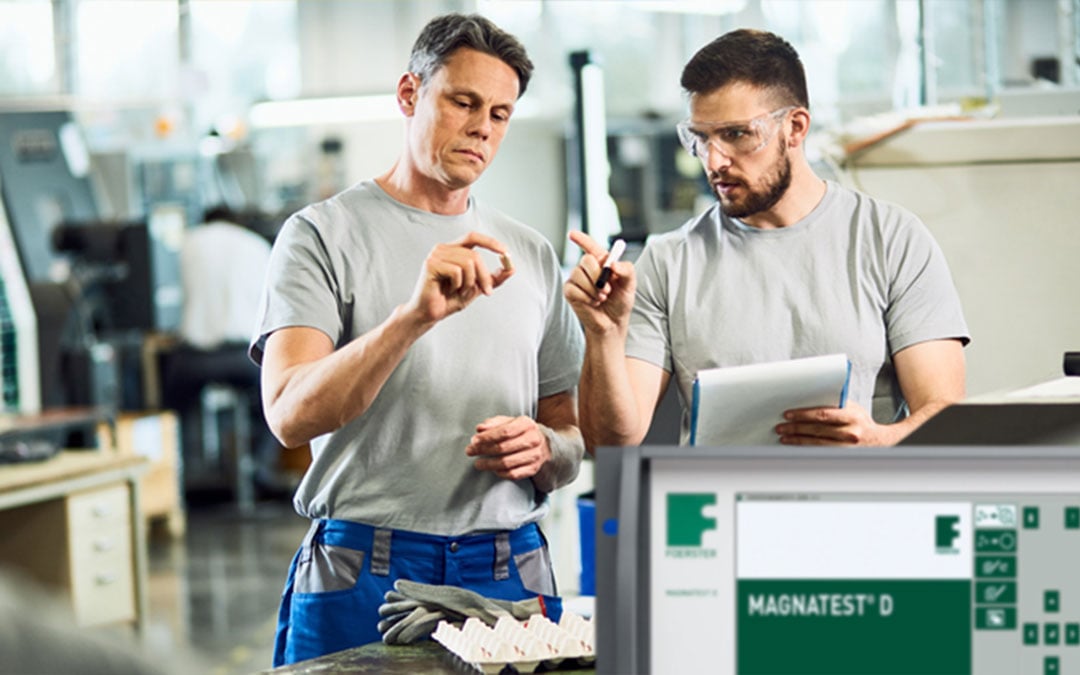
Pruebas de dureza: los 7 mayores desafíos con sistemas de corrientes inducidas
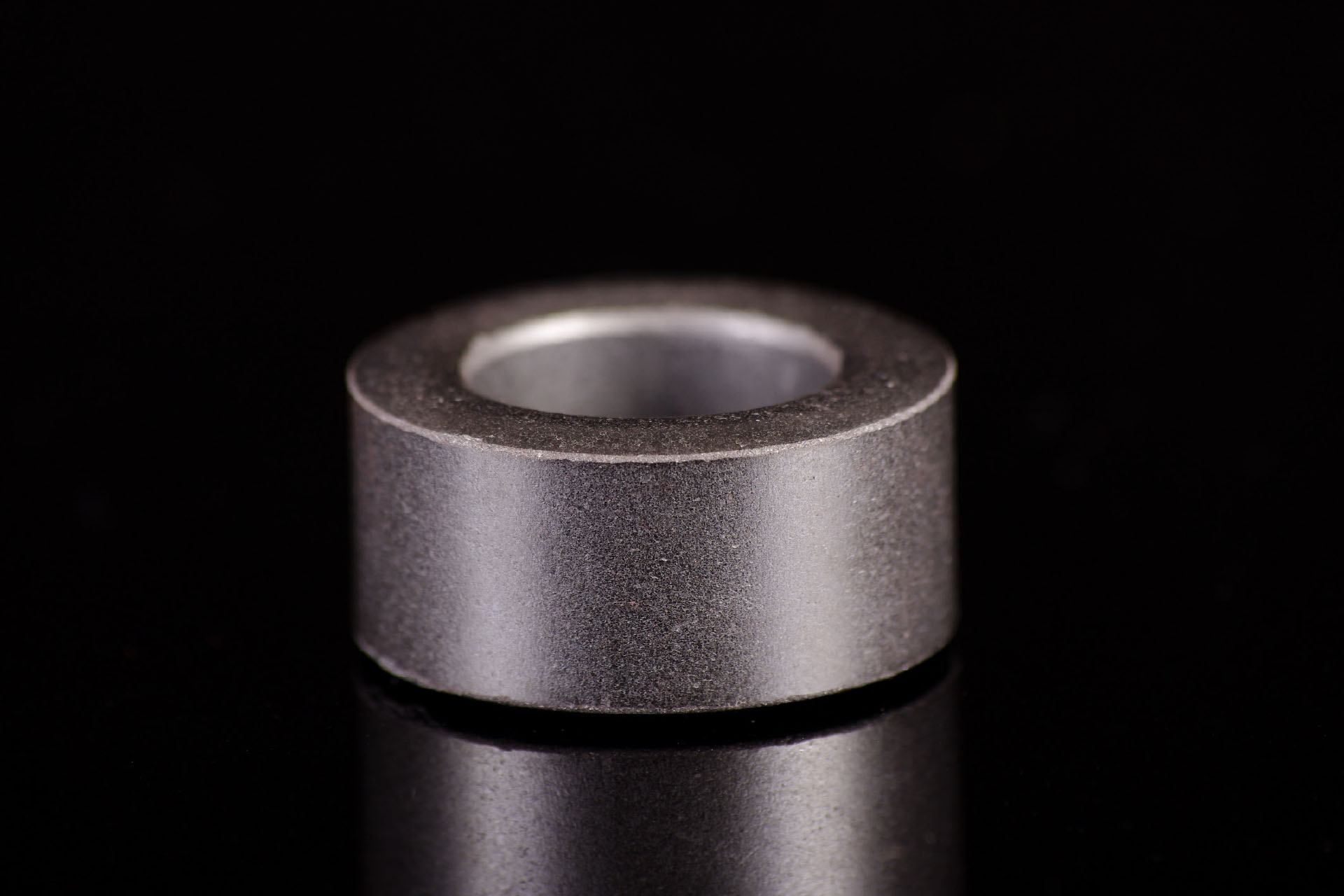