Medición rápida de dureza UCI en tornillos y pernos: aplicaciones prácticas.
Aplicaciones prácticas para la medición rápida de dureza UCI en tornillos y pernos
En el siguiente artículo, después de explicar algunos antecedentes sobre la medición de dureza en objetos pequeños como tornillos y pernos, discutiremos su implementación práctica. Esto incluye consejos prácticos y experiencias que facilitan las mediciones en estas geometrías complejas y propensas a errores rápidos.
Información básica sobre el uso de la medición de dureza UCI.
Los medidores móviles de dureza UCI (Ultrasonic Contact Impedance) se han establecido en muchas áreas de la industria metalúrgica como una herramienta importante para la evaluación de calidad de los procesos. Los sistemas de prueba móviles funcionan independientemente de la dirección y con precisión, con diferentes grados de facilidad de uso. La presentación de los resultados, su análisis y gestión son fundamentales para obtener resultados significativos en las pruebas portátiles de dureza.
Las soluciones a las tareas de prueba a menudo no son triviales. Se requiere precaución para excluir las perturbaciones de las propiedades del material o del cable de prueba lo suficiente de los resultados. Aquí, se requiere que el usuario se informe sobre las posibilidades y límites del procedimiento UCI, al igual que con todos los demás métodos de prueba. Los usuarios completamente desprevenidos corren el riesgo de fallar rápidamente. Sin embargo, después de una breve instrucción y con un poco de habilidad manual, nada impide una aplicación exitosa de las sondas de prueba UCI portátiles.
¿Qué se debe tener en cuenta al medir la dureza de los tornillos y pernos?
Además de una buena preparación de la superficie, se deben observar otras condiciones límite. La prueba de dureza UCI determina la dureza Vickers bajo carga, mientras que el diamante Vickers se presiona en el material. La escala de dureza de referencia es el sistema Vickers al cual siempre se ajusta la tecnología UCI. Esto puede ser necesario durante la operación si el módulo de elasticidad del material de prueba difiere significativamente del acero estándar (módulo de elasticidad aproximadamente 210 GPa).
El efecto de la desviación se puede determinar mejor mediante una comparación directa con un sistema de prueba de dureza clásico. A continuación, por ejemplo, al usar el durómetro SONODUR 3, la desviación del módulo de elasticidad se puede compensar fácilmente mediante un ajuste (número CAL). La importancia de estas adaptaciones depende en gran medida de las posibilidades de la tecnología de pruebas clásicas, especialmente cuando se deben medir superficies cilíndricas. También se deben tener en cuenta las diferentes profundidades de penetración en las diversas técnicas de prueba de dureza. Por ejemplo, el método Rockwell C tiene una profundidad de penetración de 100 μm a 50 HRC, que es un factor de 4 veces mayor en comparación con el método Vickers con 513 HV 10 y aproximadamente 27 μm. La experiencia ha demostrado que esto puede provocar diferencias significativas en el valor de dureza en componentes con gradientes de dureza (endurecimiento de superficie).
Así, se deben tener en cuenta:
- La naturaleza de la superficie del material,
- La geometría del componente,
- El procesamiento mecánico del componente,
- La accesibilidad mecánica a la posición de prueba
- Su historial térmico,
Así como, en el caso de piezas pequeñas o delgadas,
- Posibles resonancias del componente.
Dependiendo de la tarea y el arreglo de prueba, puede ser necesario trabajar con sondas motorizadas y fuerzas de prueba muy pequeñas, como SONO 1M 1 N (HV 0.1), para evitar resonancias del componente al usar fuerzas de prueba más altas.
Ejemplos prácticos de mediciones en tornillos y pernos.
A continuación, presentamos mediciones realizadas en diferentes secciones de los componentes de prueba.
Mediciones en la cabeza del tornillo
Básicamente, en el caso de las cabezas de los tornillos, la dirección preferida de medición de la sonda es de arriba hacia abajo. Para ello, el tornillo debe sujetarse con la cabeza hacia arriba mediante un tornillo de banco o atornillarse en un soporte adecuado. Especialmente con piezas pequeñas, se esperan vibraciones del componente (resonancias perturbadoras) en el borde exterior de la cabeza, que se pueden minimizar mediante medidas adecuadas (acoplamiento acústico, atornillado o incrustación). Las resonancias ocurren localmente en lugares no predeterminados. Sin embargo, generalmente se pueden detectar muy bien debido a su fuerte dispersión y valores extremos que están muy fuera del rango esperado.
Descripción de la imagen: Tornillos pequeños con cabeza avellanada para medición en la cabeza después del tratamiento térmico. La rosca no es accesible para la medición UCI en este caso. La medición en el vástago no fue solicitada, ya que las pruebas Vickers no son practicables en esa posición.
Descripción de la imagen: Configuración de medición para probar la cabeza del tornillo con la cabeza sujeta en el tornillo de banco con SONO H10L, sonda de versión larga. El criterio esencial es la distribución de las mediciones en la cabeza a corta distancia y la observación de la repetibilidad R. Un valor inferior al 5.0% se puede considerar muy bueno. Cinco mediciones suelen ser suficientes para un resultado significativo.
Antes de comenzar la medición, generalmente se verifica (calibra) la linealidad de la sonda de prueba con cinco mediciones en placas de referencia de dureza. Esto se hace para verificar si la sonda funciona con precisión y si los resultados inesperados pueden estar relacionados solo con la situación de prueba.
Los resultados de medición en todas las cabezas de los tornillos resumidos en una fila muestran un resultado uniforme para los tres tornillos. Cinco puntos de medición cada uno corresponden a un tornillo, con los valores medios para los tornillos 1, 2 y 3 de 455 HV 1 UCI, 452 HV 1 UCI y 444 HV 1 UCI. Todos los resultados de medición se tuvieron en cuenta para el registro.
Mediciones en el vástago.
La dirección de medición preferida es nuevamente de arriba hacia abajo, y la orientación del tornillo debe estar en la dirección de la vista del operador, con una buena iluminación de la posición de medición. Aquí es importante que, al medir a mano, la punta de la sonda se coloque en la dirección de la vista en el vértice de la circunferencia. Esto facilita llevar a cabo la medición allí mismo. Si la posición está desplazada, se introducen pequeñas fuerzas transversales en la barra de resonancia de la sonda de prueba debido al accesorio excéntrico, lo que conduce a un cambio de frecuencia adicional y, por lo tanto, al cálculo de un valor de dureza más bajo. En la práctica, esto significa que, a diferencia de la cabeza del tornillo, el arreglo de medición es más difícil y se deben esperar valores medidos dispersos bajo el valor real. Y esto es aún más cierto cuanto más delgado sea el diámetro.
Medición de un tornillo en el vástago.
Aquí, la observación de la repetibilidad juega un papel importante, al igual que la asignación de los valores mínimos y máximos con respecto al valor medio. Si se observa una clara asimetría en la pantalla de resultados del dispositivo a cierta distancia del valor medio, esto es una señal inequívoca de una medición incorrecta. Por supuesto, esto se aplica en general, pero especialmente para valores medidos mínimos con superficies curvas, ya que un "exceso" es bastante improbable, a menos que se espere la aparición de resonancias aisladas del componente.
Descripción de la imagen: Imagen del dispositivo de medición con el cuadro de resultados
Las mediciones incorrectas obvias se pueden excluir fácilmente de la observación tocando el valor máximo o mínimo en la tabla de resultados del dispositivo. Esto se abre automáticamente y se muestra para luego excluirlo de una mayor consideración.
En el caso de la prueba de tornillos y pernos, los valores atípicos deben declararse como tales para resultados significativos. Los valores excluidos de la consideración forman parte del informe original de la prueba para fines de control adicionales. Si se han iniciado correcciones en la tabla de resultados, se recomienda una serie adicional de mediciones para verificar las medidas, en la medida de lo posible. Los resultados finales (promedios) deben diferir solo ligeramente entre sí.
Mediciones en la base de la rosca.
El tornillo debe ser lo suficientemente grande como para que el diamante se pueda fijar dentro de la rosca. Aquí debe tenerse en cuenta que el diamante no toque la pared y las mediciones se realicen exactamente en la base de la rosca; de lo contrario, pueden ocurrir nuevamente fuerzas transversales. Estas tareas de medición no son muy comunes debido a su complejidad y aplicabilidad limitada.
Descripción de la imagen: Ejemplo de medición en la ranura de sujeción de una punta de broca. Aquí SONO H10L, versión larga.
Mediciones en tornillos de acero dulce.
Como configuración de prueba, se llevaron a cabo mediciones comparativas en varios tornillos experimentales de acero estructural (bruñidos o recubiertos de estaño), con Rockwell C como escala de referencia. El cliente había establecido un punto de medición HRC en cada caso. Se debe tener en cuenta que se permite una tolerancia de ±1 HRC en las placas de referencia de dureza. Realmente se deben realizar tres mediciones de calibración (EN ISO 6706). Las mediciones se tomaron con HV 10 UCI (sonda manual SONO H100) en la cabeza y el vástago. Los tornillos se sujetaron en un tornillo de banco o se colocaron sobre una base de prisma (mediciones en el vástago).
Las mejores condiciones estarían presentes si los tornillos se aprietan en una fijación. Las mediciones UCI se distribuyeron cerca de las impresiones de prueba Rockwell. No se excluyeron lecturas de UCI. En el caso de los tornillos recubiertos, las impresiones de Rockwell se colocaron en las superficies laterales. Las superficies bruñidas no fueron mecanizadas.
Los resultados UCI han confirmado las mediciones HRC, siendo las mediciones de los tornillos recubiertos en general ligeramente más altas y los valores medidos son mayores que con los tornillos bruñidos. Las razones podrían buscarse en el procesamiento térmico mediante el proceso de recubrimiento.
Resultados con la sonda SONO H100 en HRC UCI.
En base a los criterios para tornillos de seguridad, es más probable que los tornillos bruñidos se asignen a la clase 10.9 con un rango de tolerancia de 32-39 HRC según la hoja de datos. En contraste, los tornillos recubiertos se encuentran en la clase 12.9 con 39-44 HRC.
Ejemplo de un protocolo de medición.
1 | 38,4 | HRC | 376 | HP |
2 | 37,8 | HRC | 371 | HP |
3 | 37,3 | HRC | 366 | HP |
4 | 38,6 | HRC | 378 | HP |
5 | 37,5 | HRC | 368 | HP |
6 | 38,3 | HRC | 376 | HP |
7 | 38,7 | HRC | 379 | HP |
8 | 39,7 | HRC | 389 | HP |
9 | 38,5 | HRC | 377 | HP |
10 | 39,4 | HRC | 386 | HP |
11 | 38,7 | HRC | 379 | HP |
Mediciones con sondas motorizadas en un perno de acero.
Si hay suficiente espacio para dispositivos auxiliares como pies de sonda de prisma, se recomienda la medición con una sonda de medición motorizada y una base de prisma en superficies cilíndricas o recubrimientos delgados. El diámetro se puede ajustar con un tornillo estriado. Debido a la auto alineación a través del prisma, se pueden obtener resultados confiables incluso con fuerzas de prueba muy pequeñas, como con la sonda de medición motorizada SONO M3 de 3 N.
Este ejemplo es un perno de acero con un diámetro de 6 mm. La superficie del acero austenítico (en este caso, 1.4571) está colsterizada (carbonizada por difusión a una baja temperatura de aproximadamente 300 °C). La dureza superficial se midió con aproximadamente 1100 HV 0.3 UCI, lo que sugiere una profundidad de endurecimiento de aproximadamente 20 μm (profundidad de endurecimiento a 550 HV). Las pruebas con fuerzas de prueba ligeramente mayores han dado aproximadamente 600 HV UCI (sonda de prueba manual SONO H10, HV 1 UCI), debido a la capa de endurecimiento muy delgada. La dureza superficial en la cabeza fue idéntica a los resultados en el vástago.
Los resultados en comparación:
Resumen: Múltiples soluciones para la medición móvil de dureza en tornillos y pernos con el SONODUR 3
SONODUR 3 ofrece múltiples soluciones para una amplia variedad de aplicaciones para el control de procesos en producción y mantenimiento. Con la gama de productos actualmente más amplia, desde microdureza (1 N, HV 0.1 UCI) hasta macrodureza (100 N, HV 10 UCI), se pueden medir de manera confiable una amplia variedad de geometrías, tamaños de componentes y texturas. En comparación con los métodos clásicos, las mediciones se pueden realizar rápidamente, en lugares de difícil acceso y complicados en cualquier dirección. Debido al gran número de mediciones, los resultados de medición sospechosos también se pueden evaluar rápidamente en el dispositivo y, en última instancia, se pueden lograr resultados significativos.
Usando el ejemplo de tornillos y pernos, se realizaron con éxito mediciones comparativas utilizando métodos de prueba de dureza clásicos, lo que sugiere el uso de SONODUR 3 en producción. Al igual que con otros métodos de medición y prueba, se deben tener en cuenta las condiciones límite en la prueba y evaluación de resultados para minimizar las influencias negativas. En combinación con pruebas de dureza clásicas y la amplia selección de geometrías de sonda, SONODUR 3 es como un "laboratorio de pruebas in situ".
Share this
You May Also Like
These Related Stories
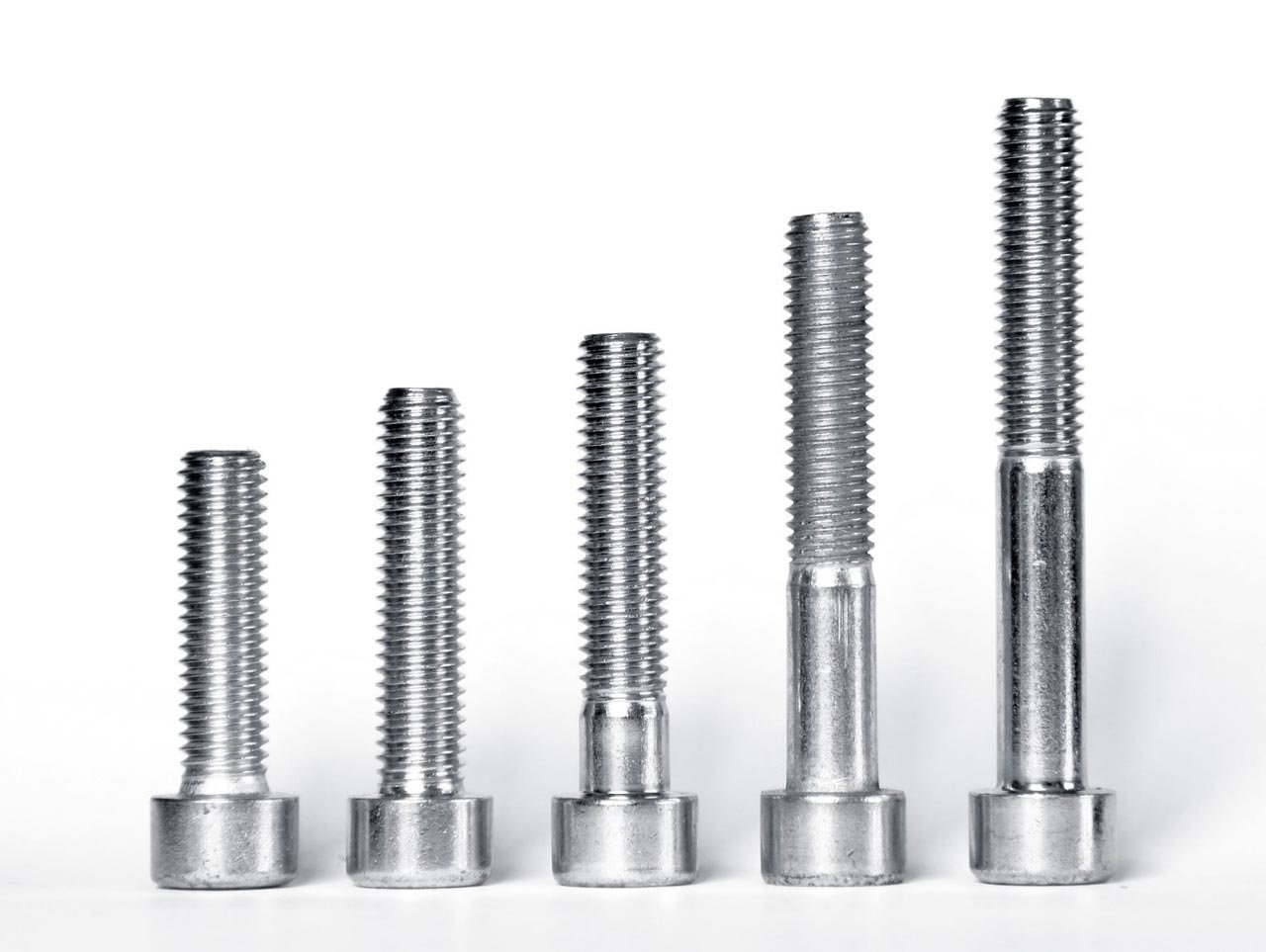
Pruebas de dureza: para que las fijaciones y los tornillos cumplan lo que prometen
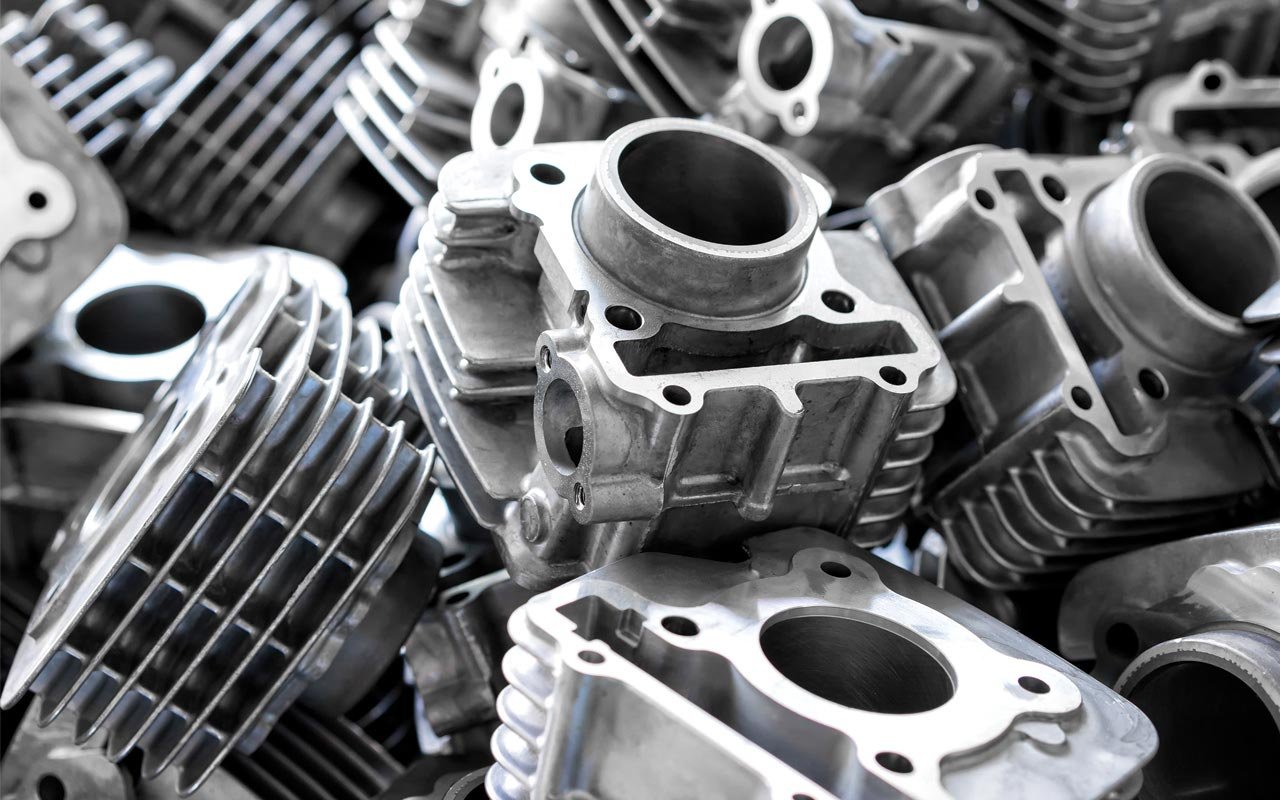
Ensayos de dureza Vickers móviles con ICU para reducir la carga de trabajo del personal de ensayos
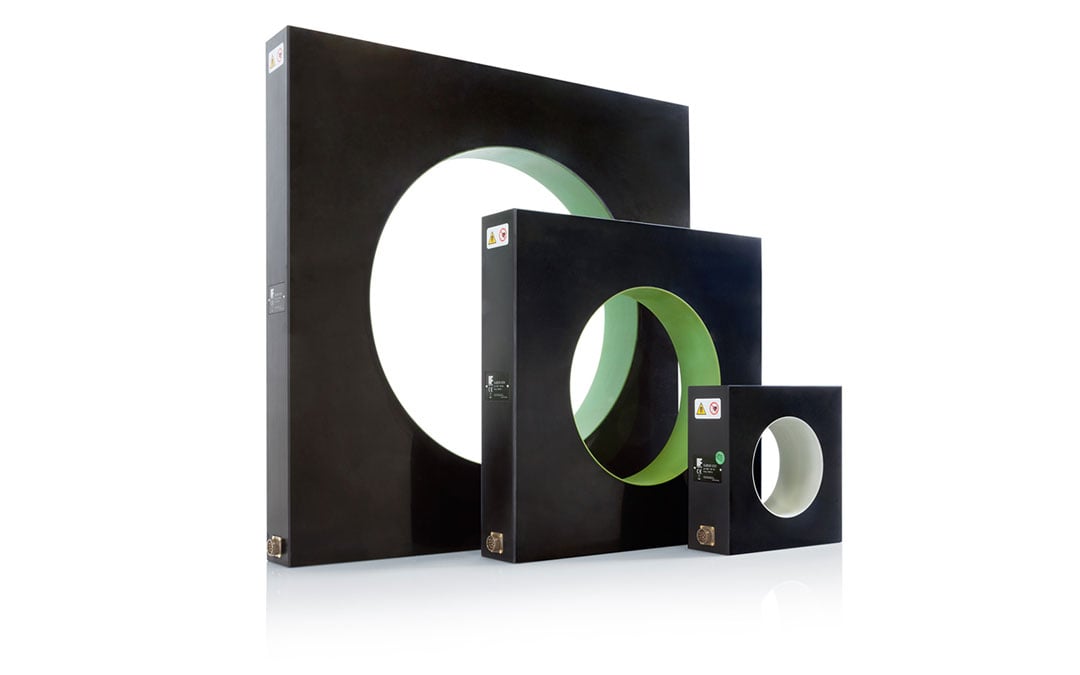