Schnelle UCI-Härtemessung an Schrauben und Bolzen: Anwendungsfälle aus der Praxis
Praktische Anwendungen für schnelle UCI-Härtemessung an Schrauben und Bolzen
Im folgenden Beitrag werden zunächst einige Hintergründe zur Härtemessung an kleinen Objekten wie Schrauben und Bolzen erläutert. Anschließend gehen wir auf die praktische Umsetzung der Härtemessung ein. Dies beinhaltet Praxistipps und -erfahrungen, mit denen Messungen an komplexen und schnell fehleranfälligen Geometrien erleichtert werden.
Grundsätzliches zum Einsatz der UCI-Härtemessung
Mobile UCI (Ultrasonic Contact Impedance) Härtemessgeräte haben sich in vielen Bereichen der metallverarbeitenden Industrie etabliert. Sie sind ein wichtiges Werkzeug zur Qualitätsbeurteilung von Prozessen. Die mobilen Prüfsysteme arbeiten richtungsunabhängig und präzise bei unterschiedlich guter Bedienerfreundlichkeit. Wegweisend für die Erzielung von signifikanten Prüfergebnissen ist die Darstellung der Ergebnisse, deren Analyse und Verwaltung.
Das Lösen der Prüfaufgaben ist häufig nicht trivial. Es ist Vorsicht geboten, damit Störungen über die Materialbeschaffenheit bzw. die Versuchsführung aus den Ergebnissen gut genug ausgeblendet werden können. Hier muss sich der Anwender über die Möglichkeiten und Grenzen des UCI-Verfahrens informieren. Unvorbereitete Benutzer riskieren schnell zu scheitern. Nach kurzer Einweisung und etwas handwerklichem Geschick steht einer erfolgreichen Anwendung der handgeführten UCI-Prüfsonden nichts mehr im Wege.
Was ist bei der Härtemessung an Schrauben und Bolzen zu beachten?
Neben einer guten Oberflächenvorbereitung muss man weitere Randbedingungen beachten. Die UCI-Härteprüfung bestimmt die Vickers-Härte unter Last während der Vickers-Diamant ins Material gedrückt wird. Die Referenz-Härteskala ist dabei das Vickers System auf das die UCI-Technik immer eingestellt wird. Dies kann im Betrieb notwendig werden, wenn der E-Modul des Prüfmaterials sich deutlich von Standard-Stahl (E-Modul ca. 210 GPa) unterscheidet.
Die Wirkung der Abweichung lässt sich am besten durch einen direkten Vergleich mit einem klassischen Härteprüfsystem ermitteln. Im Anschluss kann, zum Beispiel beim Einsatz des SONODUR 3 Härtemessgerätes, einfach über eine Justierung (CAL-Zahl) die E-Modulabweichung kompensiert werden. Die Aussagefähigkeit dieser Anpassungen hängt stark von den Möglichkeiten der klassischen Prüftechnik ab. Dies gilt besonders, wenn zylindrische Oberflächen gemessen werden. Dabei müssen auch die unterschiedlichen Eindringtiefen bei den verschiedenen Härte-Prüftechniken berücksichtigt werden. So hat beispielsweise Rockwell C bei 50 HRC eine Eindringtiefe von 100 µm, was gegenüber der Vickers-Methode z.B. mit 513 HV 10 und ca. 27 µm eine um Faktor 4 höhere Eindringtiefe ausmacht. Dies kann erfahrungsgemäß zu deutlichen Unterschieden im Härtewert auf Bauteilen mit Härtegradienten führen (Oberflächenhärtung).
Somit sind die
- Beschaffenheit der Oberfläche
- Bauteilgeometrie
- Mechanische Verarbeitung des Bauteils
- Mechanische Zugänglichkeit zur Prüfposition
- Thermische Vorgeschichte
Zu beachten. Ebenso wie, bei kleinen bzw. dünnen Teilen,
- mögliche Bauteil-Resonanzen.
Je nach Aufgabe und Prüfanordnung kann es notwendig sein, mit Motorsonden und sehr kleinen Prüfkräften wie SONO 1M 1 N (HV 0,1) zu arbeiten, um sonst auftretende Bauteilresonanzen bei höheren Prüfkräften zu vermeiden.
Praxisbeispiele zu Messungen an Schrauben und Bolzen
Im Folgenden stellen wir Ihnen durchgeführte Messungen an unterschiedlichen Abschnitten der Bauteile vor.
Messungen am Schraubenkopf
Grundsätzlich ist bei Schraubenköpfen die bevorzugte Messrichtung der Messsonde von oben nach unten. Dazu muss die Schraube mit dem Schraubenkopf nach oben fixiert sein. Dies kann über einen Schraubstock oder eine passende Halterung geschehen. Besonders bei kleinen Teilen ist am Außenrand des Kopfes mit auftretenden Bauteilschwingungen (störenden Resonanzen) zu rechnen. Dies kann durch entsprechende Maßnahmen (akustisches Ankoppeln, Einschrauben bzw. Einbetten) minimiert werden. Resonanzen treten lokal auf an nicht vorbestimmbaren Stellen. Sie lassen sich aber in der Regel sehr gut über stark streuende und überhöhte Messwerte erkennen, die weit außerhalb des Erwartungsbereichs liegen.
Bildbeschreibung: Kleine Senkkopfschrauben zur Messung auf dem Schraubenkopf nach Wärmebehandlung. Das Gewinde ist für die UCI-Messung in diesem Fall nicht zugänglich. Die Messung am Schaft war nicht gefragt, da Vickersprüfungen dort nicht praktikabel sind.
Bildbeschreibung: Messanordnung zur Prüfung des Schraubenkopfes bei im Schraubstock eingespanntem Kopf mit SONO H10L, Langversion. Das wesentliche Kriterium ist die Verteilung der Messungen auf dem Kopf im engen Abstand und Beobachtung der Wiederholpräzision R. Ein Wert unter 5,0 % kann als sehr guter Wert betrachtet werden. Fünf Messungen sind häufig ausreichend für ein signifikantes Ergebnis.
Vor Beginn der Messung wird üblicherweise die Linearität der Prüfsonde mit jeweils fünf Messungen an Härtevergleichsplatten überprüft (kalibriert). Dies geschieht, damit die Sonde exakt arbeitet und unerwartete Ergebnisse nur etwas mit der Prüfsituation zu tun haben können.
Mittelwert aus 5 Messungen | 284,5 | HV 1 UCI | 615,7 | HV 1 UCI |
Härtevergleichsplatte | 289 | HV 1 | 602,0 | HV 1 |
Abweichung | -4,5 | HP | 13,7 | HP |
Abweichung in % | -1,6 | % | 2,3 | % |
Grenzabweichung nach Norm Din 50159-1 |
±5 |
% |
±6 |
% |
Messergebnisse an allen Schraubenköpfen in einer Reihe zusammengefasst zeigen ein einheitliches Ergebnis für alle drei Schrauben. Jeweils fünf Messpunkte stehen für eine Schraube mit den Mittelwerten für Schraube 1, 2 und 3 von 455 HV 1 UCI, 452 HV 1 UCI und 444 HV 1 UCI. Für die Protokollierung wurden alle Messergebnisse berücksichtigt.
Messungen am Schaft
Bevorzugte Messrichtung ist wieder von oben nach unten. Die Orientierung der Schraube sollte in Richtung zum Blick des Bedieners sein, mit guter Beleuchtung der Messposition. Hier ist es wichtig, dass man bei Messungen von Hand die Sondenspitze in Blickrichtung auf den Scheitelpunkt des Umfangs setzt. Dies erleichtert die Messung genau dort auszuführen. Liegt man daneben, werden durch das exzentrische Aufsetzen kleine Querkräfte im Resonanzstab der Prüfspitze eingebracht, die zu einer zusätzlichen Frequenzverschiebung führen und damit zur Berechnung eines abgesenkten Härtewertes. Das bedeutet in der Praxis, dass anders als am Schraubenkopf, die Messanordnung schwieriger ist und man eher mit Messwertstreuungen nach unten rechnen muss. Dies umso mehr je dünner der Durchmesser wird.
Schraube am Schaft messen
Hier spielt die Beobachtung der Wiederholpräzision eine wichtige Rolle, ebenso wie die Zuordnung der Minimum- und Maximumwerte relativ zum Mittelwert. Wird in der Ergebnisdarstellung des Gerätes eine deutliche Asymmetrie im Abstand zum Mittelwert beobachtet, ist dies ein untrügliches Zeichen für eine Fehlmessung. Dies gilt natürlich generell, jedoch hier bei gekrümmten Oberflächen besonders für Minimum-Messwerte, da ein „Übermessen“ recht unwahrscheinlich ist, außer man muss mit dem Auftreten von vereinzelten Bauteilresonanzen rechnen.
Bild vom SONODUR 3 mit dem Ergebnis-Tableau
Offenkundige Fehlmessungen lassen sich einfach aus der Betrachtung ausschließen, indem man in der Ergebnistabelle des Gerätes den Maximum- bzw. Minimum-Wert berührt. Dieser wird automatisch aufgesucht und angezeigt, um aus der Betrachtung ausgeschlossen werden zu können.
Im Falle der Schrauben- und Bolzenprüfung sind für signifikante Ergebnisse Ausreißer in jedem Fall als solche zu deklarieren. Von der Betrachtung ausgeschlossene Werte sind Teil des originalen Prüfprotokolls für zusätzliche Kontrollzwecke. Wurden Korrekturen in der Ergebnistabelle veranlasst, empfiehlt sich eine weitere Messreihe zur Verifikation der Maßnahmen. Dabei sollten sich die Endergebnisse (Mittelwerte) nur unwesentlich voneinander unterscheiden.
Messungen im Gewindegrund
Die Schraube muss groß genug sein, damit der Diamant innerhalb des Gewindegangs angesetzt werden kann. Hier ist zu beachten, dass der Diamant die Wandung nicht berührt und die Messungen genau im Gewindegrund erfolgen, da sonst Querkräfte auftreten können. Diese Messaufgaben sind aufgrund der Komplexität und eingeschränkten Anwendbarkeit nicht sehr verbreitet.
Beispiel für die Messung in der Spannut an einer Bohrerspitze. Hier SONO H10L, Langversion.
Messungen an Baustahl-Schrauben
Als Versuchsaufbau wurden mehrere experimentelle Baustahlschrauben (brüniert bzw. Zinn-beschichtet) Vergleichsmessungen unterzogen, wobei Rockwell C als Referenz-Skala vorlag. Der Kunde hatte jeweils einen HRC-Messpunkt gesetzt. Dabei muss man berücksichtigen, dass auf Härtevergleichsplatten eine Toleranz von ±1 HRC zulässig ist. Es sollen eigentlich drei Kalibriermessungen vorgenommen werden (EN ISO 6706). Die Messungen wurden mit HV 10 UCI (SONO H100 Handmess-Sonde) an Kopf und Schaft aufgenommen. Die Schrauben wurden dabei in einem Schraubstock gehalten bzw. auf eine Prismen-Unterlage (Messungen am Schaft) aufgelegt.
Beste Bedingungen würden vorliegen, wenn die Schauben in eine Befestigung eingeschraubt werden. Die UCI-Messungen wurden in der Nähe der Rockwell-Prüfeindrücke verteilt. Dabei wurden keine UCI-Messwerte ausgeblendet. Bei den beschichteten Schrauben waren die Rockwell-Eindrücke in die geschliffenen Oberflächen gesetzt. Die brünierten Oberflächen waren nicht bearbeitet.
Die UCI-Ergebnisse haben die HRC-Messungen bestätigt, wobei die Messungen an den beschichteten Schrauben generell etwas erhöht und die Messwertstreuungen größer als bei den brünierten Schrauben sind. Gründe könnten in der thermischen Bearbeitung durch den Beschichtungsprozess liegen.
Ergebnisse mit Sonde SONO H100 in HRC UCI
Brünierte Schrauben | 1 | 2 | 3 | 4 |
36 HRC | 37,0 | 38,4 | ||
37 HRC | 37,2 | 38,4 | 38,5 | |
38 HRC | 38,9 | 399,4 | 38,5 | |
Härtebereich: 37-39 HRC | ||||
Beschichtete Schrauben | 1 | 2 | 3 | 4 |
36 HRC | 40,7 | 41,5 | ||
37 HRC | 40,0 | |||
38 HRC | 42,1 | 42,2 | 41,6 | |
Härtebereich: 37-39 HRC |
Legt man die Kriterien für Sicherheitsschrauben zugrunde, sind die brünierten Schrauben eher der Klasse 10.9 mit dem Toleranzbereich 32 – 39 HRC laut Datenblatt zuzuordnen. Dagegen liegen die beschichteten Schrauben in Klasse 12.9 mit 39 – 44 HRC.
Beispiel eines Messprotokolls
File |
\My Documents\Basic\Screw-38-Head-2_01 |
Date |
15. June 2022 |
Start of Meas. |
10:43 |
Probe/Test Force |
Sono100/100N |
Dwell Time |
0 sec |
Orientation |
0° |
Material |
Steel |
Norm; HV->HRC |
THIS IS 18265. |
Adj. Number |
0 |
Limits |
Off |
Number |
11 |
Mean |
38,5 HRC |
Std. Deviation |
0,7 HRC; 1,9% |
Maximum |
39,7 HRC |
Minimum |
37,3 HRC |
R |
2,4 HRC; 6,3% |
Remarks |
Zweite Seite am Kopf gemessen, da die Auflage des Kopfes uneben war auf der Seite des HRC-Eindrucks. Die Schraube wurde nicht fixiert, sondern nur aufgelegt. |
1 |
38,4 |
HRC |
376 |
HP |
2 |
37,8 |
HRC |
371 |
HP |
3 |
37,3 |
HRC |
366 |
HP |
4 |
38,6 |
HRC |
378 |
HP |
5 |
37,5 |
HRC |
368 |
HP |
6 |
38,3 |
HRC |
376 |
HP |
7 |
38,7 |
HRC |
379 |
HP |
8 |
39,7 |
HRC |
389 |
HP |
9 |
38,5 |
HRC |
377 |
HP |
10 |
39,4 |
HRC |
386 |
HP |
11 |
38,7 |
HRC |
379 |
HP |
Messungen mit Motorsonden an einem Stahlbolzen
Ist ausreichend Raum für Hilfsmittel wie Prismen-Sondenfüße vorhanden, bietet sich auf zylindrischen Oberflächen bzw. dünnen Beschichtungen die Messung mit einer Motorsonde und Prismen-Sondenfuß an. Mit einer Rändelschraube lässt sich der Durchmesser einstellen. Durch die Selbstzentrierung über das Prisma sind sichere Ergebnisse auch bei sehr kleinen Prüfkräften erzielbar, wie hier mit der 3N-Motorsonde SONO M3.
Bei diesem Beispiel handelt es sich um einen Stahlbolzen mit 6 mm Durchmesser. Die Oberfläche des austenitischen Stahls (hier 1.4571) ist kolsterisiert (Aufkohlung durch Diffusion bei niedriger Temperatur von ca. 300 °C). Die Oberflächenhärte wurde mit ca. 1100 HV 0,3 UCI gemessen, wobei man eine Einhärtetiefe von ca. 20 µm (EHT bei 550 HV) annehmen kann. Versuche mit etwas höherer Prüfkraft haben ca. 600 HV UCI (Handprüfsonde SONO H10, HV 1 UCI) ergeben, aufgrund der sehr dünnen Aufhärtungsschicht. Die Oberflächenhärte am Kopf war identisch zu den Ergebnissen am Schaft.
Die Ergebnisse im Vergleich:
Messreihen |
SONO H10 |
SONO H10 |
SONO M3 |
Kopf SONO M3 |
Anzahl Messungen |
27 |
37 |
34 |
10 |
Mittelwert |
624 HV |
622 HV |
1078 HV |
1042 HV |
Sigma |
26 HV; 4.4% |
27 HV; 4.6% |
68 HV; 6.3% |
38 HV; 3.7% |
Maximum |
670 HV |
705 HV |
1200 HV |
1115 HV |
Minimum |
541 HV |
555 HV |
940 HV |
994 HV |
R |
129 HV; 17.6% |
150 HV; 15.4% |
261 HV; 24.2% |
122 HV; 11.7% |
Zusammenfassung: Vielfache Lösungsmöglichkeiten der mobilen Härtemessung an Schrauben und Bolzen mit dem SONODUR 3
SONODUR 3 bietet viele Lösungsmöglichkeiten für eine hohe Vielfalt an Anwendungen zur Prozesskontrolle in Produktion und Wartung. Mit dem derzeit weitesten Produktprogramm von Mikrohärte (1 N, HV 0,1 UCI) bis zur Makrohärte (100 N, HV 10 UCI) können verschiedenste Geometrien, Bauteilgrößen und Texturen sicher gemessen werden. Die Messungen sind im Vergleich zu klassischen Methoden sehr schnell, an schwer zugänglichen und komplizierten Stellen in jeder Richtung auszuführen. Durch die Vielzahl an Messungen lassen sich auch im Gerät verdächtige Messergebnisse schnell bewerten und signifikante Ergebnisse erzielen.
Am Beispiel von Schrauben und Bolzen wurden Vergleichsmessungen erfolgreich mit klassischen Härteprüfverfahren angestellt. Dies legt eine Verwendung von SONODUR 3 in der Produktion nahe. Bei der Versuchsführung und Auswertung von Ergebnissen müssen, wie bei anderen Mess- und Prüfverfahren, Randbedingungen berücksichtigt werden, um negative Beeinflussungen zu minimieren. SONODUR 3 ist im Zusammenspiel mit der klassischen Härteprüfung und der breiten Auswahl an Sondengeometrien wie ein „Prüflabor vor Ort“.
Share this
Vielleicht gefällt Ihnen auch
Verwandte Artikel
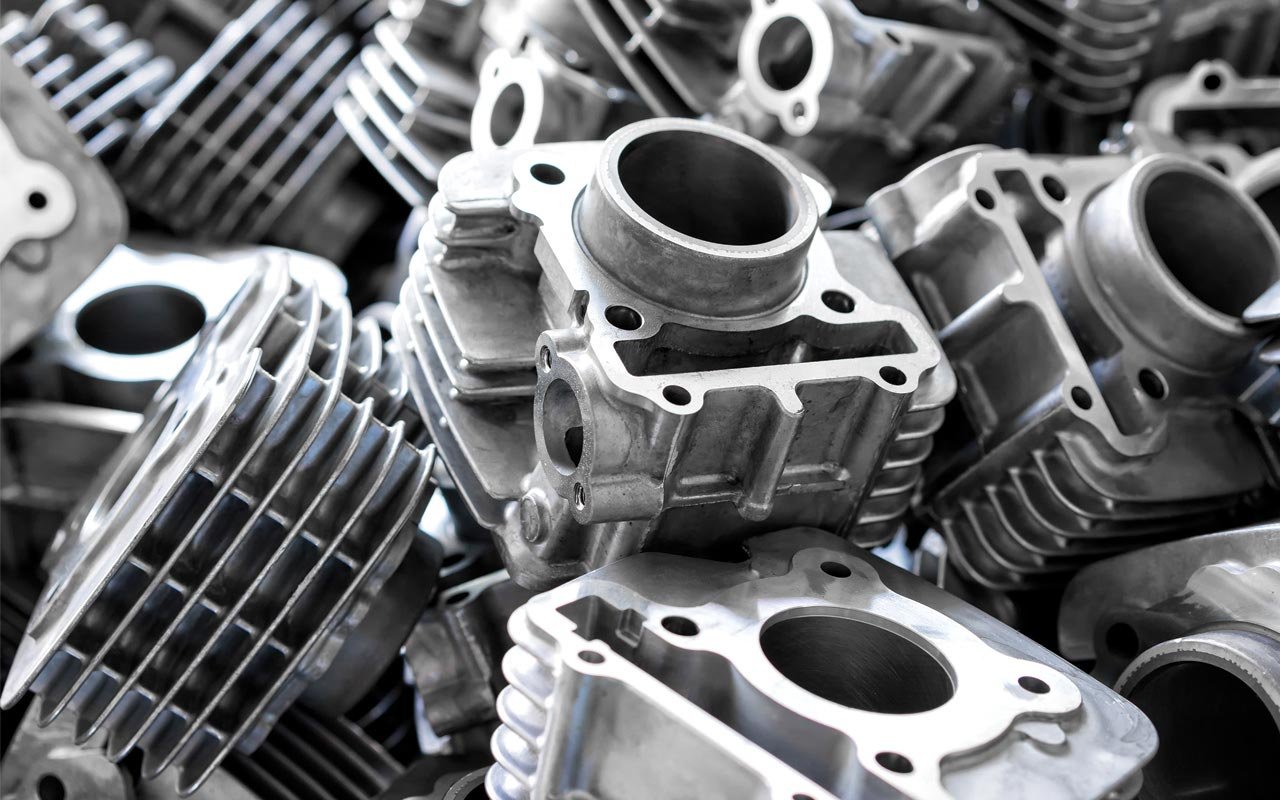
Mobile Vickers-Härtemessung mit UCI zur Entlastung des Prüfpersonals
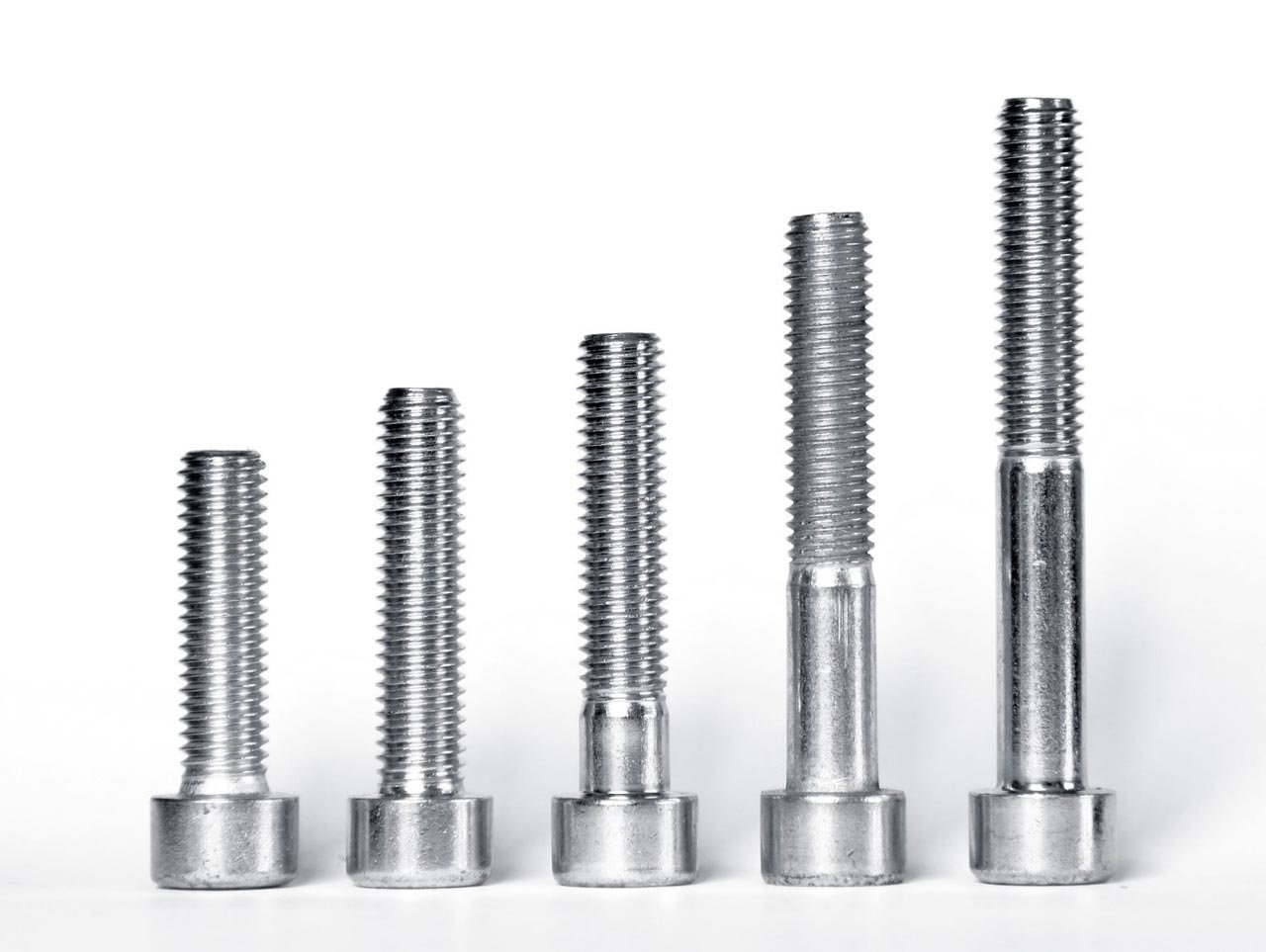
Härteprüfung - Verbindungsmittel & Schrauben, damit sie halten, was sie versprechen
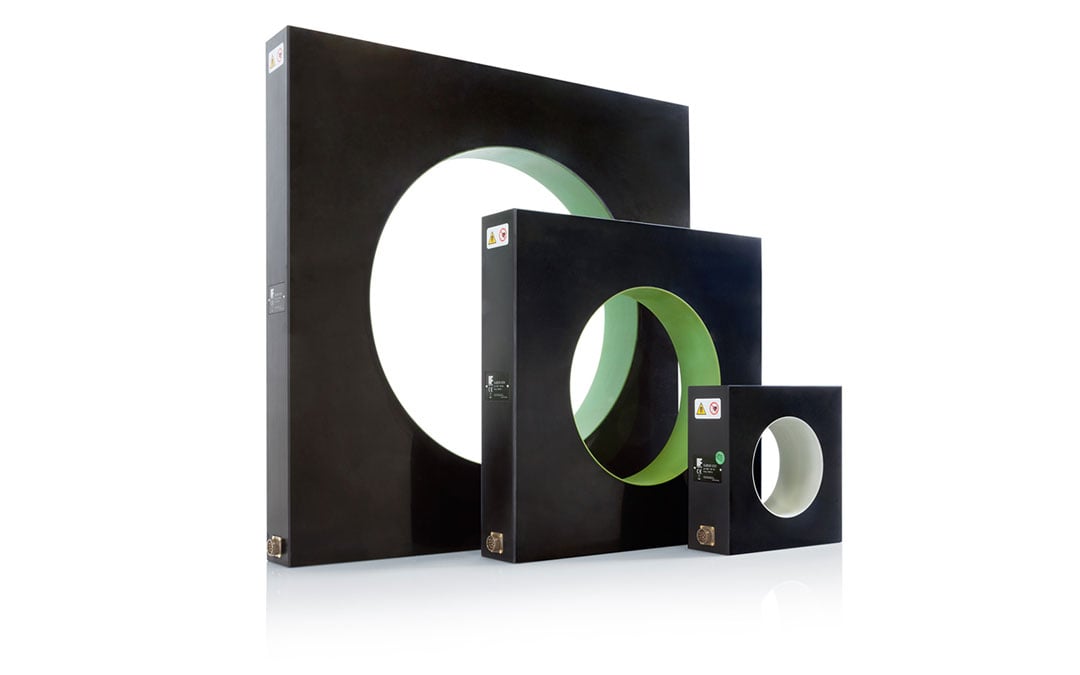